Introduction to SMT and BGA Components
Surface-mount technology (SMT) is a method for producing electronic circuits in which the components are mounted directly onto the surface of printed circuit boards (PCBs). SMT has largely replaced the through-hole technology construction method of fitting components with wire leads into holes in the circuit board. Components used in surface mount technology are referred to as surface-mount devices or SMDs.
Ball Grid Array (BGA) is a surface-mount package with solder balls on the bottom. The solder balls are used to conduct electrical signals from the integrated circuit to the printed circuit board (PCB) it is mounted on. BGA packages are ideal for high-density connections and offer several advantages, including:
- Reduced lead inductance
- Smaller package footprint compared to wire-bond packages
- Better thermal and electrical performance
- Lower profile
- Higher connection densities
However, BGA packages also present challenges in terms of inspection, soldering, and rework due to their design with balls hidden underneath.
Key Steps in SMT Assembly Process for BGA Components
The SMT assembly process for BGA components involves several key steps:
1. Solder Paste Printing
Solder paste, a mixture of tiny solder balls and flux, is applied to the PCB pads where the BGA will be placed. The most common method is stencil printing, which uses a laser-cut stencil to apply solder paste only to the desired areas.
Factors influencing solder paste printing quality:
– Stencil thickness and aperture size
– Solder paste viscosity and composition
– Print speed, pressure, and separation speed
– Squeegee hardness and angle
– PCB and stencil cleaning
Common solder paste printing defects include:
– Insufficient or excessive solder
– Solder bridging or solder beading
– Poor aperture fill or solder paste slumping
– Stencil smearing or scooping
2. BGA Placement
The BGA component is precisely placed onto the PCB using a pick-and-place machine. The machine uses computer vision to align the component and place it accurately on the solder paste deposits.
Factors influencing BGA placement accuracy:
– Component size, weight, and center of gravity
– Nozzle type and vacuum pressure
– Placement force and speed
– PCB support and clamping
– Fiducial recognition and offset correction
Common BGA placement defects include:
– Misalignment or rotated component
– Lifted leads or missing balls
– Excessive or insufficient placement force
– Tombstoning (one end lifted)
3. Reflow Soldering
The PCB with the placed BGA goes through a reflow oven, which melts the solder paste and permanently attaches the component to the board. The reflow profile is carefully controlled to achieve optimal solder joint quality.
Factors influencing reflow soldering quality:
– Reflow profile (preheating, soaking, reflow, cooling)
– Peak temperature and time above liquidus
– Temperature ramp rate and uniformity
– Nitrogen or air atmosphere
– PCB and component thermal mass
Common reflow soldering defects for BGAs:
– Solder joint voids or incomplete coalescence
– Solder balling or solder beading
– Component shifting or misalignment
– PCB or component warpage
4. Inspection and Testing
After reflow, the assembled PCB undergoes inspection and testing to verify the solder joint quality and electrical functionality of the BGA component.
Inspection methods for BGA solder joints:
– X-ray imaging (2D or 3D)
– Endoscopic inspection
– Boundary scan testing
– Electrical testing (ICT, flying probe, functional test)
Common BGA solder joint defects:
– Head-in-pillow (incomplete ball collapse)
– Open or cracked solder joints
– Solder bridging or shorts
– Voids exceeding acceptable levels
5. Rework and Repair
If defects are found during inspection, the BGA component may need to be reworked or replaced. This involves removing the defective component, cleaning the site, and soldering a new component.
BGA Rework process:
1. Pre-bake PCB and component to remove moisture
2. Remove component using hot air or infrared heating
3. Clean pads and remove old solder
4. Print solder paste on pads using mini-stencil
5. Place new component and reflow solder
6. Clean flux residue and inspect solder joints
Challenges in BGA rework:
– Thermal stress on PCB and adjacent components
– Difficulty in cleaning and preparing pads
– Precise alignment of replacement component
– Achieving acceptable solder joint quality
– Potential damage to PCB or new component
Best Practices for SMT Assembly of BGA Components
To achieve high yield and reliability in SMT assembly of BGA components, consider the following best practices:
1. Design for Manufacturing (DFM)
- Follow BGA land pattern and solder mask guidelines
- Provide adequate PCB support and copper balancing
- Minimize PCB and component warpage
- Allow for inspection and rework access
- Use thermally-enhanced BGA substrates if needed
2. Material Selection and Control
- Select compatible solder paste and flux for BGA
- Control solder paste viscosity and particle size
- Use fresh and properly stored materials
- Verify paste and flux activity before use
- Clean and maintain stencils and nozzles regularly
3. Process Control and Monitoring
- Optimize and monitor solder paste printing parameters
- Verify BGA placement accuracy and repeatability
- Develop and control reflow profile for each product
- Monitor reflow oven performance and temperature uniformity
- Implement SPC for key process parameters
4. Inspection and Quality Assurance
- Perform 100% solder paste inspection after printing
- Verify BGA placement with AOI before reflow
- Conduct X-ray inspection for hidden solder joints
- Perform electrical testing to verify functionality
- Use cross-sections or endoscopy for failure analysis
5. Training and Documentation
- Train operators on BGA assembly best practices
- Provide work instructions for each process step
- Document material and process specifications
- Maintain traceability for materials and processes
- Conduct regular audits and continuous improvement
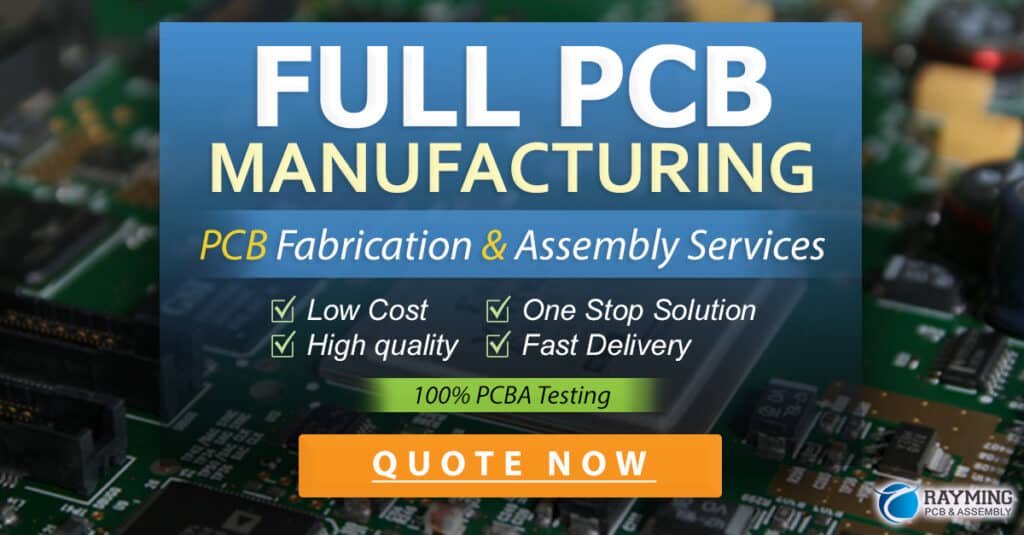
Common Challenges and Solutions in SMT-BGA Assembly
Despite following best practices, various challenges can arise in SMT assembly of BGA components. Here are some common issues and their solutions:
Challenge | Possible Causes | Solutions |
---|---|---|
Head-in-pillow defect | – Oxidized or contaminated solder balls – Insufficient fluxing or wetting – Poor reflow profile |
– Use fresh components and solder paste – Increase flux activity or clean pads – Optimize reflow profile and atmosphere |
Solder joint voids | – Entrapped flux vapors – Moisture in PCB or component – Insufficient solder volume |
– Optimize reflow profile and use vacuum oven – Bake PCB and component before assembly – Increase solder paste deposit or stencil thickness |
BGA misalignment | – Inaccurate solder paste printing – Placement machine setup or nozzle issues – Uneven PCB or component surfaces |
– Optimize stencil design and printing parameters – Calibrate placement machine and maintain nozzles – Use support pins or carriers for even surfaces |
PCB or component warpage | – Mismatch in thermal expansion coefficients – Excessive reflow temperature or time – Inadequate PCB support or clamping |
– Use compatible materials and thermal-matching – Optimize reflow profile and minimize time above liquidus – Provide proper support and clamping during reflow |
Solder beading or bridging | – Excessive solder paste volume – Component placement pressure too high – Insufficient solder mask between pads |
– Reduce stencil thickness or aperture size – Optimize placement pressure and speed – Increase solder mask width or use NSMD pads |
Inspection Techniques for BGA Solder Joints
Inspecting BGA solder joints is challenging due to their hidden nature under the component. Several techniques are used, each with their advantages and limitations:
X-ray Imaging
X-ray is the most common method for BGA solder joint inspection. It allows viewing the solder balls and any defects or voids.
- 2D X-ray provides a top view image, good for checking bridges, voids, and missing balls
- 3D X-ray (CT) provides cross-sectional slices, better for detecting cracks, head-in-pillow, and measuring void volume
- Automated X-ray inspection (AXI) uses image analysis to detect and classify defects
Advantages:
– Non-destructive testing
– Can inspect hidden solder joints
– Enables void measurement and failure analysis
Limitations:
– Equipment cost and complexity
– Limited resolution compared to microscopy
– Difficulty detecting some non-volumetric defects
Endoscopic Inspection
Endoscopy involves inserting a micro-camera probe between the PCB and BGA to view the solder joints at the periphery.
Advantages:
– Relatively low cost and simple setup
– Provides direct optical viewing of solder joints
– Can detect solder joint shape and wetting defects
Limitations:
– Limited to peripheral balls only
– Probe access requires sufficient clearance
– Risk of damaging solder joints or components
Boundary Scan Testing
Boundary scan is an electrical test method that uses a special test circuit built into the BGA component to test the connectivity and logic functions.
Advantages:
– Tests both structural and functional defects
– Programmable test coverage
– Can test inaccessible or hidden connections
Limitations:
– Requires boundary scan compatible components
– Limited to digital logic and interconnects
– Cannot detect some mechanical or process defects
Electrical Testing
Various electrical tests can be used to verify BGA solder joint quality and functionality:
- In-circuit test (ICT) probes test pads and measures resistance
- Flying probe test uses moving probes to access test pads
- Functional test applies power and signals to verify operation
Advantages:
– Verifies actual electrical performance
– Can detect solder joint defects and component faults
– Enables system-level testing and diagnosis
Limitations:
– Requires test pad access and fixturing
– Limited to electrically testable faults
– Cannot directly pinpoint the defect location
Frequently Asked Questions (FAQ)
1. What is the difference between a solder paste and flux?
Solder paste is a mixture of tiny solder particles suspended in a thick flux medium. It is used to form the solder joints during reflow. Flux is a chemical agent that removes oxides, prevents re-oxidation, and promotes wetting of the solder to the pads and leads. Flux can be a separate liquid or part of solder paste.
2. Can solder joint voids be eliminated completely?
While it is desirable to minimize voids, eliminating them completely is not practical. Some level of voids is acceptable as long as they do not exceed the size and quantity limits set by industry standards such as IPC-610. Typical void levels are below 25% of the solder joint volume for BGAs. Voids can be reduced by optimizing the reflow profile, using vacuum ovens, and proper material storage and handling.
3. How do you control the reflow profile for BGA components?
The reflow profile for BGAs is typically developed using guidelines from the solder paste and component suppliers, as well as industry standards. Key factors to control are the preheating rate, soak time and temperature, reflow peak temperature and time above liquidus, and cooling rate. The profile is programmed into the reflow oven controller and monitored using thermocouples or profilers attached to the PCB. Regular oven maintenance and calibration are also important for consistent reflow profiles.
4. What is the purpose of underfill for BGA components?
Underfill is an epoxy material that is dispensed under the BGA after soldering to fill the gap between the component and PCB. Its main purposes are to redistribute the thermal and mechanical stresses on the solder joints, and to provide environmental protection. Underfill is especially important for large or thermally mismatched BGAs, and for high-reliability applications subjected to shock, vibration, or thermal cycling.
5. How do you perform failure analysis on BGA solder joints?
When a BGA solder joint fails, various techniques can be used to analyze the failure mode and cause:
- Visual and X-ray inspection to locate the failure site
- Cross-sectioning to examine the solder joint structure and interfaces
- Scanning electron microscopy (SEM) for high magnification imaging
- Energy-dispersive X-ray spectroscopy (EDX) for chemical analysis
- Dye penetrant testing to reveal cracks or delamination
The failure analysis results are used to determine the root cause, such as manufacturing defects, design issues, or environmental factors, and to implement corrective actions to prevent future failures.
Conclusion
SMT assembly of BGA components requires careful process control and monitoring to achieve high yield and reliability. Key steps include solder paste printing, component placement, reflow soldering, inspection, and rework. Best practices involve design for manufacturing, material selection and control, process optimization, and quality assurance.
Common challenges such as head-in-pillow defects, solder joint voids, misalignment, warpage, and solder beading can be prevented or solved by understanding their causes and implementing appropriate mitigation techniques.
Inspecting BGA solder joints requires specialized techniques such as X-ray imaging, endoscopy, boundary scan testing, and electrical testing. Each method has its strengths and limitations in terms of coverage, resolution, and defect detection.
By following industry guidelines, supplier recommendations, and continuous improvement practices, manufacturers can successfully assemble BGA components using SMT processes and achieve the desired quality and performance goals.
No responses yet