Introduction to Kapton PCB
Kapton, a polyimide film developed by DuPont, has revolutionized the printed circuit board (PCB) industry due to its exceptional properties. Kapton PCBs are widely used in various applications that require high performance, reliability, and durability. In this comprehensive guide, we will explore the world of Kapton PCBs, their manufacturing process, advantages, applications, and frequently asked questions.
What is Kapton?
Kapton is a polyimide film that possesses a unique combination of properties, making it an ideal material for various industrial applications. It exhibits excellent thermal stability, maintaining its mechanical and electrical properties over a wide temperature range. Kapton also has high dielectric strength, low dielectric constant, and good chemical resistance.
Properties of Kapton
Property | Value |
---|---|
Dielectric Strength | 7700 V/mil (303 kV/mm) |
Dielectric Constant | 3.4 (at 1 kHz) |
Tensile Strength | 30,000 psi (207 MPa) |
Thermal Conductivity | 0.12 W/m·K |
Temperature Resistance | -269°C to 400°C (-452°F to 752°F) |
Kapton PCB Manufacturing Process
Substrate Preparation
The Kapton PCB manufacturing process begins with the preparation of the Kapton substrate. The Kapton film is cleaned and treated to enhance its adhesion properties. The substrate is then laminated with copper foil on one or both sides, depending on the PCB design requirements.
Circuit Design and Patterning
The desired circuit pattern is designed using specialized PCB design software. The design is then transferred onto the copper-laminated Kapton substrate using photolithography. A photoresist layer is applied to the copper surface and exposed to UV light through a photomask containing the circuit pattern. The exposed areas of the photoresist are developed, revealing the copper layer beneath.
Etching and Plating
The exposed copper is etched away using a chemical solution, leaving behind the desired circuit pattern. The remaining photoresist is then stripped off. If required, additional copper plating can be performed to increase the thickness of the copper traces.
Solder Mask Application
A solder mask layer is applied to the PCB surface, covering the copper traces while leaving the pads and other designated areas exposed. The solder mask protects the copper from oxidation and prevents solder bridging during the assembly process.
Surface Finish
To enhance solderability and protect the exposed copper pads, a surface finish is applied. Common surface finishes for Kapton PCBs include electroless nickel immersion gold (ENIG), immersion tin, and immersion silver.
Cutting and Drilling
The manufactured Kapton PCB panel is cut into individual boards using a precision cutting machine. Holes for through-hole components and mounting are drilled using a computer-controlled drilling machine.
Advantages of Kapton PCBs
High Temperature Resistance
Kapton PCBs can withstand extreme temperatures ranging from -269°C to 400°C (-452°F to 752°F), making them suitable for applications in harsh environments, such as aerospace, automotive, and industrial electronics.
Excellent Dielectric Properties
With a high dielectric strength of 7700 V/mil (303 kV/mm) and a low dielectric constant of 3.4 (at 1 kHz), Kapton PCBs provide excellent insulation and signal integrity, minimizing crosstalk and signal loss.
Lightweight and Flexible
Kapton PCBs are lightweight and flexible, allowing for compact and conformable designs. This makes them ideal for applications where space is limited or where the PCB needs to conform to a specific shape.
Chemical and Radiation Resistance
Kapton PCBs exhibit excellent chemical resistance, withstanding exposure to various solvents, oils, and acids. They also have high radiation resistance, making them suitable for use in radiation-prone environments, such as space applications.
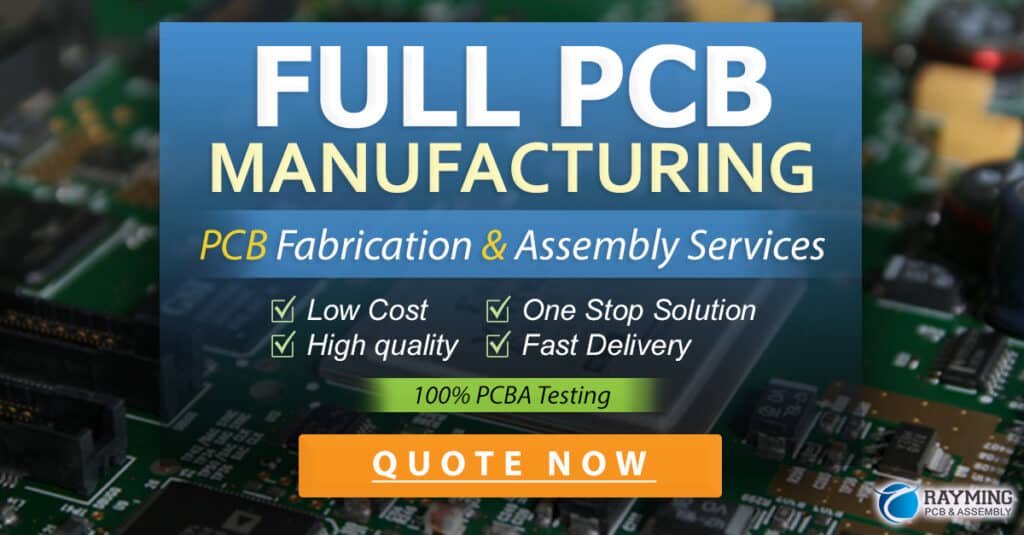
Applications of Kapton PCBs
Aerospace and Defense
Kapton PCBs are extensively used in aerospace and defense applications due to their ability to withstand extreme temperatures, vibrations, and radiation. They are used in satellite systems, avionics, and military equipment.
Automotive Electronics
In the automotive industry, Kapton PCBs are used in high-temperature applications such as engine control units, exhaust gas sensors, and brake systems. They provide reliable performance in harsh under-hood environments.
Industrial Electronics
Kapton PCBs find applications in various industrial electronics, including power electronics, motor drives, and process control systems. They can withstand the high temperatures and harsh conditions often encountered in industrial settings.
Medical Devices
The biocompatibility and chemical resistance of Kapton make it suitable for use in medical devices. Kapton PCBs are used in implantable devices, surgical instruments, and medical imaging equipment.
Frequently Asked Questions (FAQ)
1. What is the maximum operating temperature of Kapton PCBs?
Kapton PCBs can withstand temperatures ranging from -269°C to 400°C (-452°F to 752°F), making them suitable for high-temperature applications.
2. Are Kapton PCBs flexible?
Yes, Kapton PCBs are flexible and can conform to various shapes, making them ideal for applications where flexibility is required.
3. Can Kapton PCBs be used in vacuum environments?
Yes, Kapton PCBs have low outgassing properties and can be used in vacuum environments, such as space applications.
4. How does the cost of Kapton PCBs compare to traditional PCBs?
Kapton PCBs are generally more expensive than traditional FR-4 PCBs due to the higher material cost and specialized manufacturing process. However, their superior performance and durability justify the added cost in demanding applications.
5. Can Kapton PCBs be soldered using standard soldering techniques?
Yes, Kapton PCBs can be soldered using standard soldering techniques, such as reflow soldering and hand soldering. However, care must be taken to avoid excessive heat exposure, which can damage the Kapton substrate.
Conclusion
Kapton PCBs offer a unique combination of properties that make them ideal for demanding applications in various industries. Their high temperature resistance, excellent dielectric properties, lightweight and flexible nature, and chemical and radiation resistance set them apart from traditional PCBs. By understanding the manufacturing process, advantages, and applications of Kapton PCBs, engineers and designers can leverage their capabilities to create high-performance electronic systems that can withstand extreme conditions. As technology continues to advance, Kapton PCBs will undoubtedly play a crucial role in enabling innovative solutions across diverse sectors.
No responses yet