What are IPC Standards?
IPC standards are a set of guidelines and specifications developed by the Association Connecting Electronics Industries (IPC) to ensure high-quality, reliable, and consistent manufacturing of electronic products. These standards cover various aspects of the electronics industry, including design, fabrication, assembly, and testing of printed circuit boards (PCBs), electronic components, and assemblies.
Key Areas Covered by IPC Standards
- PCB Design and Fabrication
- Electronic Component Packaging
- Soldering and Assembly Processes
- Quality and Reliability Testing
- Environmental Compliance
The Importance of IPC Standards
IPC standards play a crucial role in the electronics industry by:
- Ensuring consistency and reliability in manufacturing processes
- Facilitating communication between designers, manufacturers, and customers
- Reducing costs and time-to-market by streamlining processes
- Promoting environmental sustainability and compliance with regulations
Benefits of Implementing IPC Standards
Benefit | Description |
---|---|
Improved Product Quality | Consistent manufacturing processes lead to higher quality products with fewer defects |
Enhanced Reliability | Standardized testing and quality control ensure reliable performance of electronic products |
Increased Efficiency | Streamlined processes reduce manufacturing time and costs |
Better Communication | Clear guidelines facilitate effective communication between stakeholders |
Environmental Sustainability | IPC standards promote the use of eco-friendly materials and practices |
Key IPC Standards
IPC-A-610: Acceptability of Electronic Assemblies
IPC-A-610 is a widely recognized standard that provides acceptance criteria for the manufacture of electronic assemblies. It covers various aspects, such as soldering, component placement, and mechanical assembly.
IPC-A-610 Classes
Class | Description |
---|---|
1 | General Electronic Products (Consumer products, some industrial and military) |
2 | Dedicated Service Electronic Products (Industrial, medical, automotive, military) |
3 | High-Performance Electronic Products (Aerospace, military, medical implants) |
IPC-6012: Qualification and Performance Specification for Rigid Printed Boards
IPC-6012 defines the requirements for the qualification and performance of rigid printed circuit boards. It covers aspects such as material selection, dimensional tolerances, and electrical properties.
IPC J-STD-001: Requirements for Soldered Electrical and Electronic Assemblies
IPC J-STD-001 provides guidelines for the manufacture of soldered electrical and electronic assemblies. It covers soldering processes, materials, and inspection criteria.
IPC-A-600: Acceptability of Printed Boards
IPC-A-600 defines the acceptance criteria for printed circuit boards, including visual and dimensional requirements, as well as structural integrity and reliability.
IPC-7711/7721: Rework, Modification and Repair of Electronic Assemblies
IPC-7711/7721 provides procedures for the rework, modification, and repair of electronic assemblies, ensuring that these processes do not compromise the quality and reliability of the products.
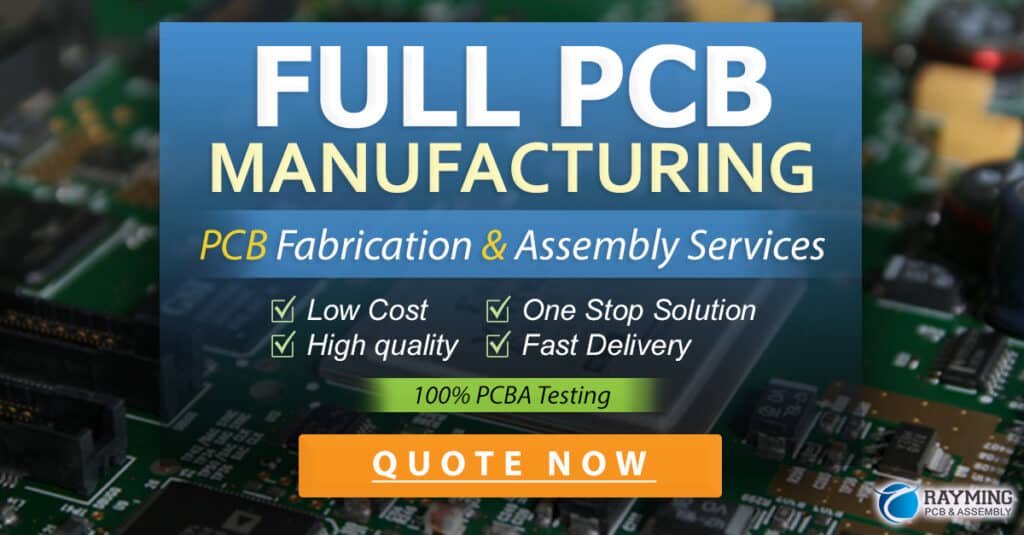
Implementing IPC Standards in Your Organization
To successfully implement IPC standards in your organization, follow these steps:
- Identify the relevant IPC standards for your products and processes
- Train your staff on the requirements and guidelines of the selected standards
- Develop and document standard operating procedures (SOPs) aligned with IPC standards
- Regularly audit your processes to ensure compliance with the standards
- Continuously improve your processes based on the audit results and updates to the standards
Training and Certification
IPC offers various training and certification programs to help organizations and individuals acquire the knowledge and skills necessary to implement and adhere to IPC standards effectively. Some of the popular certification programs include:
- IPC-A-610 Certified IPC Specialist (CIS)
- IPC J-STD-001 Certified IPC Specialist (CIS)
- IPC-A-600 Certified IPC Specialist (CIS)
- IPC-7711/7721 Certified IPC Specialist (CIS)
The Future of IPC Standards
As the electronics industry continues to evolve, IPC standards must adapt to address emerging technologies and challenges. Some of the areas where IPC is focusing its efforts include:
- Advanced packaging technologies, such as 3D integration and system-in-package (SiP)
- Additive manufacturing (3D printing) for electronics
- Automotive and aerospace electronics reliability
- Environmental sustainability and circular economy practices
Frequently Asked Questions (FAQ)
1. Are IPC standards mandatory?
While IPC standards are not mandatory, they are widely adopted and recognized as best practices in the electronics industry. Many companies require their suppliers to adhere to specific IPC standards to ensure the quality and reliability of their products.
2. How often are IPC standards updated?
IPC standards are regularly reviewed and updated to keep pace with technological advancements and industry needs. The frequency of updates varies depending on the standard and the rate of change in the relevant technology.
3. Can IPC standards be customized for specific company requirements?
Yes, companies can develop their own internal standards based on IPC guidelines, taking into account their specific products, processes, and quality requirements. However, it is essential to ensure that these customized standards meet or exceed the minimum requirements set by IPC.
4. How can I access IPC standards?
IPC standards can be purchased directly from the IPC website (www.ipc.org) or through authorized distributors. Some standards may also be available through subscription services or as part of training and certification programs.
5. What are the consequences of not following IPC standards?
Not following IPC standards can lead to various issues, such as:
- Inconsistent product quality and reliability
- Increased manufacturing costs and time-to-market
- Communication breakdowns between stakeholders
- Difficulty in securing contracts with customers who require IPC compliance
- Potential legal and financial liabilities related to product failures or recalls
In conclusion, IPC standards play a vital role in ensuring the quality, reliability, and consistency of electronic products. By adopting and adhering to these standards, organizations can improve their manufacturing processes, reduce costs, and enhance customer satisfaction. As the electronics industry continues to evolve, staying up-to-date with the latest IPC standards and best practices will be essential for success in the competitive global market.
No responses yet