What are IPC Standards?
IPC, which stands for the Institute of Printed Circuits, is a global trade association that develops standards for the electronics industry. IPC standards cover nearly every aspect of printed circuit board (PCB) design and manufacturing, as well as electronics assembly and quality control.
IPC standards are widely recognized and adopted by electronics manufacturers worldwide. They ensure consistency, reliability, and interoperability of electronic products and assemblies. Adhering to IPC standards helps companies produce high-quality products efficiently and cost-effectively.
Why are IPC Standards Important?
IPC standards play a crucial role in the electronics industry for several reasons:
-
Quality Assurance: IPC standards establish best practices and guidelines for PCB design, manufacturing, and assembly. Following these standards helps ensure that the end product meets the desired quality level and performs as intended.
-
Consistency: By adhering to IPC standards, manufacturers can maintain consistency across different production runs and facilities. This consistency is essential for products that require high reliability, such as those used in aerospace, medical, and military applications.
-
Cost Savings: Implementing IPC standards can help reduce costs associated with defects, rework, and warranty claims. By following best practices and using standardized processes, manufacturers can minimize errors and improve efficiency.
-
Improved Communication: IPC standards provide a common language for designers, manufacturers, and customers to communicate effectively. Using standardized terminology and specifications helps avoid misunderstandings and ensures that all parties have the same expectations.
-
Regulatory Compliance: Many industries have specific regulatory requirements that must be met. IPC standards often incorporate these requirements, making it easier for manufacturers to comply with regulations and avoid penalties.
Types of IPC Standards
IPC standards cover a wide range of topics related to PCB design, manufacturing, and assembly. Some of the most commonly used IPC standards include:
IPC-A-610: Acceptability of Electronic Assemblies
IPC-A-610 is the most widely used standard for the inspection of electronic assemblies. It provides acceptance criteria for PCBs, components, and solder joints. The standard defines three classes of products based on their intended use and the level of reliability required:
Class | Description | Example Applications |
---|---|---|
1 | General Electronic Products | Consumer electronics, toys, and low-end appliances |
2 | Dedicated Service Electronic Products | Computers, communications equipment, and industrial controls |
3 | High Performance Electronic Products | Aerospace, medical, and military equipment |
IPC-6012: Qualification and Performance Specification for Rigid Printed Boards
IPC-6012 sets the requirements for the qualification and performance of rigid PCBs. It covers various aspects of PCB fabrication, including:
- Material selection
- Conductor width and spacing
- Hole size and placement
- Solder mask and silkscreen
- Electrical testing
The standard also defines three performance classes based on the intended end-use of the PCB:
Class | Description | Example Applications |
---|---|---|
1 | General Purpose | Consumer electronics and non-critical applications |
2 | Dedicated Service | Industrial controls, automotive, and telecommunications |
3 | High Reliability | Aerospace, medical, and military applications |
IPC J-STD-001: Requirements for Soldered Electrical and Electronic Assemblies
IPC J-STD-001 is a joint standard developed by IPC and the Electronic Industries Alliance (EIA). It defines the requirements for producing high-quality soldered interconnections on electronic assemblies. The standard covers:
- Soldering processes
- Workmanship
- Inspection criteria
- Rework and repair
Like IPC-A-610, J-STD-001 also defines three classes of products based on their intended use and reliability requirements.
IPC-2221: Generic Standard on Printed Board Design
IPC-2221 provides guidelines for the design of PCBs, including:
- Board layout
- Material selection
- Conductor sizing and spacing
- Hole sizing and placement
- Thermal management
The standard aims to help designers create PCBs that are manufacturable, reliable, and cost-effective.
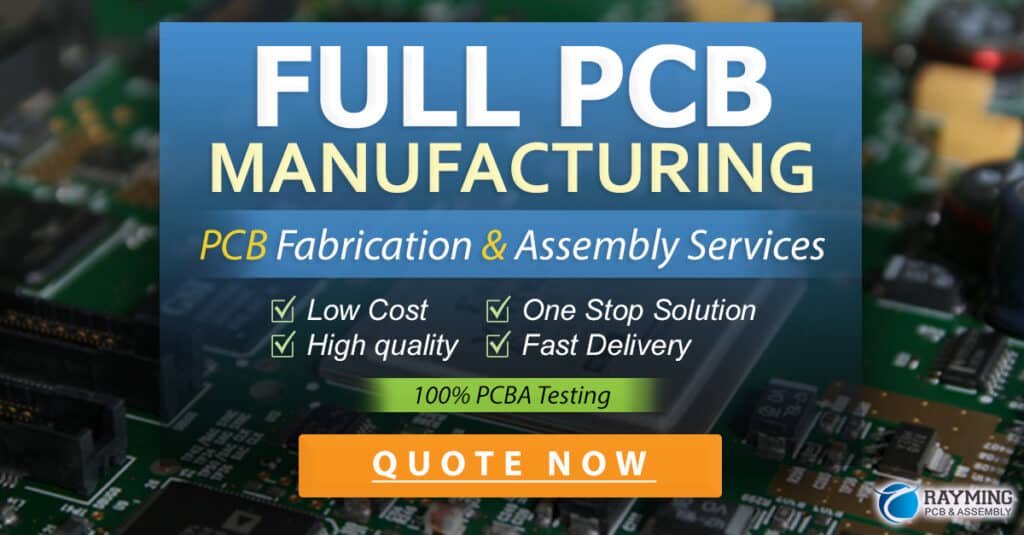
Implementing IPC Standards
To effectively implement IPC standards in your organization, consider the following steps:
-
Identify Relevant Standards: Determine which IPC standards apply to your products and processes. Consider the intended end-use, reliability requirements, and regulatory obligations.
-
Train Personnel: Provide training to your staff on the relevant IPC standards. Ensure that designers, engineers, and production personnel understand the requirements and best practices outlined in the standards.
-
Integrate Standards into Processes: Incorporate IPC standards into your design, manufacturing, and quality control processes. Develop standard operating procedures (SOPs) that align with the requirements of the relevant standards.
-
Audit and Monitor Compliance: Regularly audit your processes and products to ensure compliance with IPC standards. Use checklists and inspection criteria provided in the standards to verify conformance.
-
Continuous Improvement: Continuously monitor and improve your processes based on the results of audits and customer feedback. Stay up-to-date with the latest revisions of IPC standards and adapt your practices accordingly.
Frequently Asked Questions (FAQ)
1. Are IPC standards mandatory?
IPC standards are voluntary, but they are widely adopted by the electronics industry. Many customers and regulatory bodies require compliance with specific IPC standards as a condition of doing business.
2. How often are IPC standards updated?
IPC standards are regularly reviewed and updated to keep pace with advances in technology and changes in industry practices. The frequency of updates varies depending on the standard and the pace of change in the relevant technology.
3. Can I get certified to IPC standards?
Yes, IPC offers certification programs for individuals and companies. These programs demonstrate proficiency in specific IPC standards and best practices. Certified individuals and companies are recognized for their commitment to quality and reliability.
4. What happens if I don’t follow IPC standards?
Not following IPC standards can result in various issues, such as:
- Reduced product quality and reliability
- Increased defects and rework
- Higher production costs
- Difficulty in obtaining customer approval or regulatory compliance
5. Where can I purchase IPC standards?
IPC standards can be purchased directly from the IPC website (www.ipc.org) or through authorized distributors. Many standards are available in both printed and digital formats.
Conclusion
IPC standards are essential for ensuring the quality, reliability, and consistency of electronic products and assemblies. By adopting and adhering to these standards, manufacturers can improve their processes, reduce costs, and meet customer and regulatory requirements. Implementing IPC standards requires a commitment to training, process integration, and continuous improvement. With the proper understanding and application of IPC standards, your organization can produce high-quality electronics that meet the demands of today’s competitive market.
No responses yet