Introduction to IPC PCB Standards
In the world of electronics manufacturing, printed circuit boards (PCBs) play a crucial role in connecting and supporting electronic components. To ensure the quality, reliability, and consistency of PCBs, the electronics industry relies on a set of standards known as IPC PCB standards. These standards, developed by the Association Connecting Electronics Industries (IPC), provide guidelines and specifications for the design, fabrication, assembly, and testing of PCBs.
What is IPC?
IPC, formerly known as the Institute for Printed Circuits, is a global trade association dedicated to the electronics manufacturing industry. Founded in 1957, IPC has been instrumental in developing and maintaining standards for PCBs, electronic assemblies, and related processes. With members from various sectors, including designers, manufacturers, suppliers, and end-users, IPC aims to promote the growth and success of the electronics industry through standardization, education, and advocacy.
The Importance of IPC PCB Standards
IPC PCB standards serve several critical purposes in the electronics industry:
-
Quality Assurance: By adhering to IPC standards, manufacturers can ensure that their PCBs meet the necessary quality requirements, reducing the risk of defects, failures, and customer dissatisfaction.
-
Consistency: IPC standards provide a common language and set of specifications for PCB manufacturers worldwide, ensuring that PCBs produced by different companies are compatible and interchangeable.
-
Cost Reduction: Standardization helps to streamline the manufacturing process, reduce errors, and minimize waste, ultimately leading to cost savings for both manufacturers and customers.
-
Reliability: IPC standards address various aspects of PCB manufacturing, including materials, processes, and testing, which contribute to the overall reliability and durability of the final product.
-
Innovation: By establishing a solid foundation for PCB manufacturing, IPC standards foster innovation and the development of new technologies in the electronics industry.
Key IPC PCB Standards
IPC has developed a comprehensive set of standards covering different aspects of PCB manufacturing. Some of the most widely used IPC PCB standards include:
IPC-2221: Generic Standard on Printed Board Design
IPC-2221 is a general standard that provides guidelines for the design of PCBs. It covers various aspects of PCB design, such as:
- Board layout and routing
- Material selection
- Hole and pad sizes
- Electrical clearances
- Thermal management
This standard serves as a foundation for other, more specific IPC standards related to PCB design and manufacturing.
IPC-6012: Qualification and Performance Specification for Rigid Printed Boards
IPC-6012 is a performance specification standard that defines the requirements for rigid PCBs. It covers aspects such as:
- Material properties
- Dimensional tolerances
- Conductor thickness and width
- Hole and via requirements
- Surface finishes
- Electrical testing
This standard ensures that rigid PCBs meet the necessary quality and reliability criteria for various applications.
IPC-A-600: Acceptability of Printed Boards
IPC-A-600 is a visual acceptance standard for PCBs. It provides a comprehensive set of visual criteria for evaluating the quality of PCBs, including:
- Solderability
- Laminate defects
- Conductor defects
- Marking and labeling
- Cleanliness
This standard helps manufacturers and customers assess the visual quality of PCBs and identify potential issues before assembly.
IPC-7711/7721: Rework, Modification and Repair of Electronic Assemblies
IPC-7711/7721 is a standard that provides guidelines for the rework, modification, and repair of electronic assemblies, including PCBs. It covers topics such as:
- Soldering and desoldering techniques
- Component replacement
- Conductor repair
- Laminate repair
- Cleaning and inspection
This standard ensures that rework and repair processes are performed in a controlled and consistent manner, minimizing the risk of damage to the PCB or electronic components.
Benefits of Implementing IPC PCB Standards
Implementing IPC PCB standards offers numerous benefits for manufacturers, designers, and end-users:
1. Enhanced Product Quality
By following IPC standards, manufacturers can produce PCBs with consistent quality, reducing the occurrence of defects and failures. This leads to improved product performance, reliability, and customer satisfaction.
2. Increased Efficiency and Productivity
IPC standards provide clear guidelines and specifications for PCB manufacturing processes, allowing for streamlined operations and reduced errors. This increased efficiency translates to faster production times and higher productivity.
3. Reduced Costs
Standardization helps to minimize waste, rework, and scrap, leading to cost savings in materials and labor. Additionally, the improved quality and reliability of PCBs produced according to IPC standards can reduce warranty claims and customer returns, further reducing overall costs.
4. Improved Communication and Collaboration
IPC standards provide a common language for designers, manufacturers, and customers, facilitating effective communication and collaboration. This helps to ensure that all parties involved in the PCB manufacturing process are on the same page, reducing misunderstandings and delays.
5. Access to Global Markets
By adhering to internationally recognized IPC standards, manufacturers can more easily access global markets and compete on a level playing field. Customers worldwide can have confidence in the quality and reliability of PCBs produced to IPC standards, increasing the potential for international business opportunities.
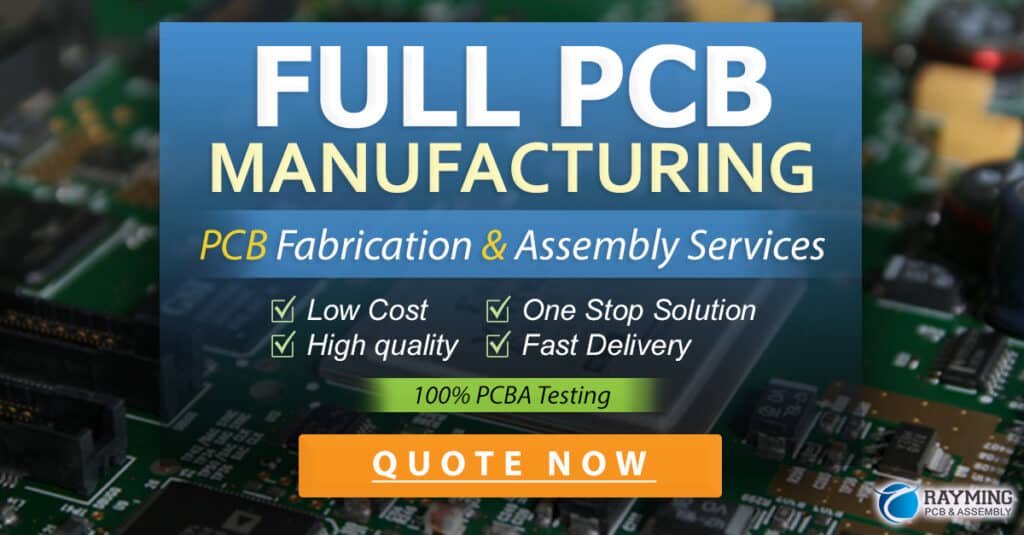
Challenges in Implementing IPC PCB Standards
While the benefits of implementing IPC PCB standards are significant, there are also some challenges that manufacturers may face:
1. Initial Investment
Implementing IPC standards may require an initial investment in equipment, training, and process changes. Manufacturers must carefully consider the costs and benefits of adopting IPC standards and develop a strategic plan for implementation.
2. Training and Education
To effectively implement IPC standards, manufacturers must ensure that their employees are properly trained and educated. This may involve investing in training programs, workshops, and certification courses to build the necessary skills and knowledge.
3. Continuous Improvement
IPC standards are regularly updated to keep pace with advances in technology and industry best practices. Manufacturers must stay informed about the latest developments in IPC standards and be prepared to adapt their processes and procedures accordingly.
4. Supply Chain Management
Implementing IPC standards may require changes in the supply chain, as manufacturers must ensure that their suppliers and partners also adhere to the same standards. This may involve working closely with suppliers to align processes and quality requirements.
FAQ
1. Are IPC PCB standards mandatory?
While IPC PCB standards are not legally mandatory, they are widely recognized and adopted by the electronics industry. Many customers and regulatory bodies require or strongly recommend adherence to IPC standards as a measure of quality and reliability.
2. How can manufacturers ensure compliance with IPC PCB standards?
Manufacturers can ensure compliance with IPC standards by:
- Providing training and education for their employees
- Implementing quality control processes and procedures
- Regularly auditing their processes and products
- Seeking certification from IPC or third-party auditors
3. What happens if a manufacturer does not follow IPC PCB standards?
Manufacturers who do not follow IPC standards may face several consequences, such as:
- Reduced product quality and reliability
- Increased customer complaints and returns
- Difficulty accessing certain markets or customers
- Potential legal or regulatory issues
4. Can IPC PCB standards be tailored to specific products or applications?
While IPC standards provide a comprehensive set of guidelines, they can be tailored to specific products or applications through the use of performance classes and additional requirements. Manufacturers should work closely with their customers to determine the appropriate level of adherence to IPC standards for each project.
5. How often are IPC PCB standards updated?
IPC regularly reviews and updates its standards to keep pace with changes in technology and industry best practices. The frequency of updates varies depending on the specific standard and the rate of technological advancement in the relevant area. Manufacturers should stay informed about the latest revisions and updates to ensure ongoing compliance.
Conclusion
IPC PCB standards play a vital role in ensuring the quality, reliability, and consistency of printed circuit boards in the electronics industry. By providing comprehensive guidelines and specifications for PCB design, fabrication, assembly, and testing, IPC standards help manufacturers to produce high-quality products, reduce costs, and improve efficiency. While implementing IPC standards may present some challenges, the benefits – including enhanced product quality, increased productivity, and access to global markets – make it a worthwhile investment for PCB manufacturers. As technology continues to advance, the importance of IPC PCB standards in the electronics industry will only continue to grow, driving innovation and success in the years to come.
IPC Standard | Description |
---|---|
IPC-2221 | Generic Standard on Printed Board Design |
IPC-6012 | Qualification and Performance Specification for Rigid Printed Boards |
IPC-A-600 | Acceptability of Printed Boards |
IPC-7711/7721 | Rework, Modification and Repair of Electronic Assemblies |
Table 1: Key IPC PCB Standards
By embracing IPC PCB standards, manufacturers can position themselves for success in the highly competitive and rapidly evolving electronics industry. Through commitment to quality, collaboration, and continuous improvement, PCB manufacturers can meet the demands of customers worldwide and contribute to the advancement of electronic products and technologies.
No responses yet