What is IoT in Electronic Manufacturing?
IoT in electronic manufacturing refers to the integration of internet-connected sensors, devices, and systems into the production process. This allows for real-time monitoring, control, and optimization of various aspects of manufacturing, such as:
- Machine performance and maintenance
- Inventory and supply chain management
- Quality control and defect detection
- Energy consumption and efficiency
- Worker safety and productivity
By collecting and analyzing data from these connected devices, manufacturers can gain valuable insights into their operations and make data-driven decisions to improve efficiency, reduce costs, and enhance product quality.
Benefits of IoT in Electronic Manufacturing
The adoption of IoT in electronic manufacturing brings numerous benefits, including:
-
Increased Efficiency and Productivity: IoT enables real-time monitoring and control of production processes, allowing manufacturers to identify and address bottlenecks, optimize resource allocation, and minimize downtime. This leads to increased efficiency and productivity.
-
Reduced Costs: By optimizing processes, reducing waste, and preventing equipment failures, IoT helps manufacturers lower their operating costs. Additionally, predictive maintenance enabled by IoT can extend the lifespan of machines and reduce maintenance costs.
-
Improved Quality: IoT-enabled quality control systems can detect defects and anomalies in real-time, allowing for quick corrective actions. This helps manufacturers maintain high product quality and reduce the risk of costly recalls.
-
Enhanced Supply Chain Visibility: IoT provides real-time visibility into the entire supply chain, from raw materials to finished products. This allows manufacturers to optimize inventory levels, reduce lead times, and respond quickly to changes in demand.
-
Greater Customization: IoT enables manufacturers to collect data on customer preferences and behavior, allowing for greater customization of products and services. This can lead to increased customer satisfaction and loyalty.
Applications of IoT in Electronic Manufacturing
IoT has numerous applications in electronic manufacturing, including:
Predictive Maintenance
Predictive maintenance is one of the most significant applications of IoT in electronic manufacturing. By monitoring the performance and health of machines in real-time, manufacturers can detect potential issues before they cause downtime or quality problems. This allows for proactive maintenance, reducing unplanned downtime and extending the lifespan of equipment.
For example, sensors can monitor the vibration, temperature, and other parameters of a machine, and alert maintenance teams when anomalies are detected. This allows for timely interventions, such as lubricating, adjusting, or replacing components, before a failure occurs.
Quality Control
IoT-enabled quality control systems can significantly improve the accuracy and efficiency of defect detection in electronic manufacturing. By integrating sensors and vision systems into the production line, manufacturers can monitor product quality in real-time and identify defects as they occur.
For instance, machine vision systems can inspect printed circuit boards (PCBs) for missing components, solder defects, or incorrect placements. If a defect is detected, the system can alert operators or automatically remove the defective product from the line.
Inventory and Supply Chain Management
IoT can greatly enhance inventory and supply chain management in electronic manufacturing. By tracking the location and status of raw materials, work-in-progress, and finished products, manufacturers can optimize inventory levels, reduce stockouts, and improve delivery times.
For example, RFID tags can be attached to components and products, allowing for real-time tracking throughout the supply chain. This can help manufacturers identify bottlenecks, monitor supplier performance, and respond quickly to changes in demand.
Energy Management
Electronic manufacturing is an energy-intensive industry, and IoT can help manufacturers optimize their energy consumption and reduce costs. By monitoring energy usage at the machine, process, and facility levels, manufacturers can identify opportunities for efficiency improvements.
For instance, sensors can monitor the power consumption of machines and alert operators when they are running inefficiently. Manufacturers can also use IoT-enabled building management systems to optimize heating, ventilation, and air conditioning (HVAC) and lighting systems based on occupancy and production schedules.
Worker Safety and Productivity
IoT can also enhance worker safety and productivity in electronic manufacturing. By monitoring the location and movements of workers, manufacturers can ensure compliance with safety protocols and optimize workflow.
For example, wearable devices can alert workers when they enter hazardous areas or when they are exposed to excessive noise, heat, or other environmental factors. IoT-enabled systems can also track worker productivity and provide real-time feedback to help improve efficiency.
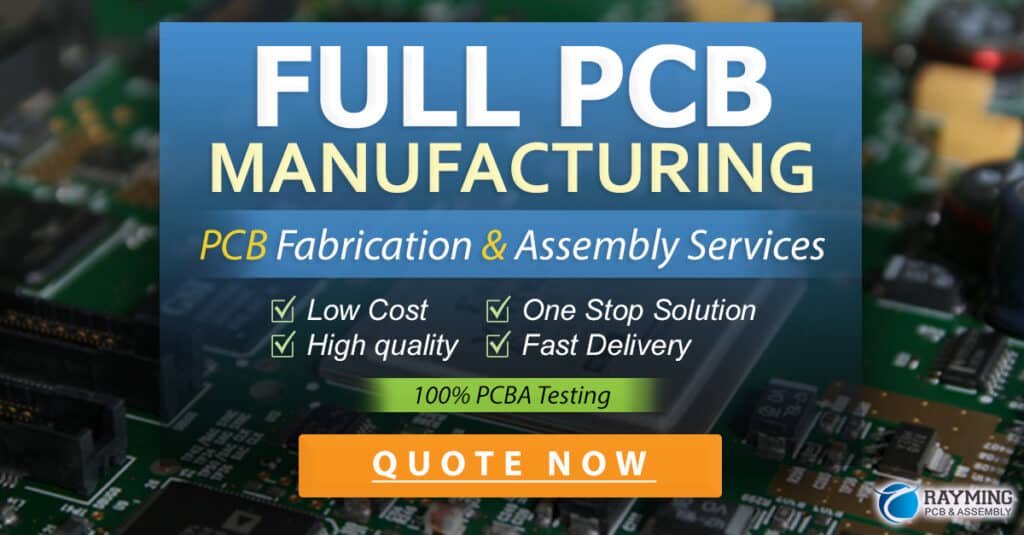
Challenges and Considerations
While IoT offers numerous benefits to electronic manufacturing, there are also challenges and considerations that manufacturers must address. These include:
Data Security and Privacy
IoT generates vast amounts of data, and ensuring the security and privacy of this data is critical. Manufacturers must implement robust cybersecurity measures to protect against data breaches, unauthorized access, and other threats.
Integration with Legacy Systems
Many electronic manufacturing facilities have legacy systems and equipment that may not be compatible with IoT technologies. Integrating these systems can be complex and costly, requiring significant investments in hardware, software, and training.
Skilled Workforce
Implementing and maintaining IoT systems requires a skilled workforce with expertise in areas such as data analytics, cybersecurity, and automation. Manufacturers may need to invest in training and hiring to build the necessary skills and capabilities.
Standardization and Interoperability
The lack of standardization and interoperability among IoT devices and systems can create challenges for manufacturers. Ensuring that devices from different vendors can communicate and work together seamlessly is crucial for realizing the full benefits of IoT.
Future of IoT in Electronic Manufacturing
The future of IoT in electronic manufacturing is promising, with several emerging trends and technologies on the horizon. These include:
5G and Edge Computing
The advent of 5G networks and edge computing will enable faster, more reliable, and more secure IoT deployments in electronic manufacturing. By processing data closer to the source, edge computing can reduce latency and bandwidth requirements, enabling real-time decision-making and control.
Artificial Intelligence and Machine Learning
The integration of artificial intelligence (AI) and machine learning (ML) with IoT will enable more advanced and autonomous manufacturing processes. AI and ML can help manufacturers optimize production schedules, predict maintenance needs, and improve product quality by analyzing vast amounts of IoT data.
Digital Twins
Digital twins, which are virtual replicas of physical objects or processes, will become increasingly important in electronic manufacturing. By creating digital twins of products, processes, and facilities, manufacturers can simulate and optimize operations, test new configurations, and predict performance.
Collaborative Robots
Collaborative robots, or cobots, are designed to work safely alongside human workers and can be easily integrated into IoT-Enabled Manufacturing environments. Cobots can perform repetitive or hazardous tasks, freeing up human workers for higher-value activities and improving overall productivity.
FAQ
-
What is the role of IoT in electronic manufacturing?
IoT plays a crucial role in electronic manufacturing by enabling real-time monitoring, control, and optimization of production processes. It helps manufacturers improve efficiency, reduce costs, enhance product quality, and gain valuable insights into their operations. -
What are some of the key benefits of implementing IoT in electronic manufacturing?
Some of the key benefits of implementing IoT in electronic manufacturing include increased efficiency and productivity, reduced costs, improved quality, enhanced supply chain visibility, and greater customization. -
What are some of the challenges associated with implementing IoT in electronic manufacturing?
Some of the challenges associated with implementing IoT in electronic manufacturing include data security and privacy concerns, integration with legacy systems, the need for a skilled workforce, and standardization and interoperability issues. -
How can IoT help with predictive maintenance in electronic manufacturing?
IoT-enabled predictive maintenance systems can monitor the performance and health of machines in real-time, detecting potential issues before they cause downtime or quality problems. This allows for proactive maintenance, reducing unplanned downtime and extending the lifespan of equipment. -
What are some of the emerging trends and technologies in IoT for electronic manufacturing?
Some of the emerging trends and technologies in IoT for electronic manufacturing include 5G and edge computing, artificial intelligence and machine learning, digital twins, and collaborative robots. These technologies are expected to further enhance the capabilities and benefits of IoT in electronic manufacturing.
Conclusion
IoT is transforming the electronic manufacturing industry, enabling unprecedented levels of automation, optimization, and innovation. By connecting machines, devices, sensors, and systems, IoT helps manufacturers improve efficiency, reduce costs, enhance product quality, and gain valuable insights into their operations.
While there are challenges and considerations to address, such as data security, integration with legacy systems, and the need for a skilled workforce, the benefits of IoT in electronic manufacturing are clear. As new technologies like 5G, edge computing, AI, and digital twins emerge, the potential of IoT in electronic manufacturing will only continue to grow.
To stay competitive in this rapidly evolving landscape, electronic manufacturers must embrace IoT and invest in the necessary technologies, skills, and capabilities. By doing so, they can unlock new opportunities for growth, innovation, and customer value, positioning themselves for success in the Industry 4.0 era.
No responses yet