Table of Contents
- What is IoT in Manufacturing?
- Benefits of IoT in Manufacturing
- Key Components of IoT in Manufacturing
- Challenges and Considerations
- IoT-Manufacturing-use-cases”>IoT Manufacturing Use Cases
- Predictive Maintenance
- Asset Tracking and Management
- Quality Control and Inspection
- Energy Management
- Inventory Management
- Implementing IoT in Manufacturing
- Future of IoT in Manufacturing
- Frequently Asked Questions (FAQ)
- Conclusion
What is IoT in Manufacturing?
IoT in manufacturing refers to the integration of connected devices, sensors, and software applications to optimize production processes, enhance efficiency, and improve product quality. By leveraging the power of IoT, manufacturers can collect real-time data from machines, equipment, and products, enabling them to make data-driven decisions and streamline operations.
Benefits of IoT in Manufacturing
Implementing IoT in manufacturing offers numerous benefits, including:
-
Increased Productivity: IoT enables real-time monitoring and optimization of production processes, reducing downtime and increasing overall equipment effectiveness (OEE).
-
Cost Reduction: By minimizing waste, optimizing resource utilization, and reducing maintenance costs, IoT helps manufacturers achieve significant cost savings.
-
Improved Quality: IoT-enabled quality control and inspection systems can detect defects in real-time, ensuring consistent product quality and reducing scrap rates.
-
Enhanced Safety: IoT devices can monitor workplace conditions and alert workers to potential hazards, promoting a safer working environment.
-
Better Decision Making: Real-time data analytics provided by IoT systems enable manufacturers to make informed decisions based on accurate, up-to-date information.
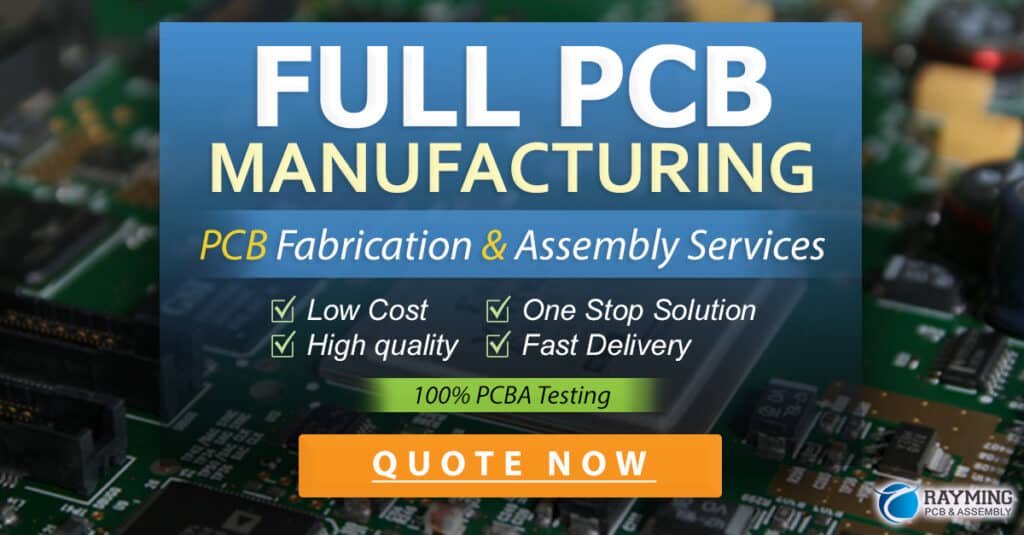
Key Components of IoT in Manufacturing
To successfully implement IoT in manufacturing, several key components are required:
-
Connected Devices: Sensors, actuators, and other IoT devices that collect data from machines, equipment, and products.
-
Network Infrastructure: Robust and secure network infrastructure, such as Wi-Fi, cellular, or low-power wide-area networks (LPWAN), to enable communication between devices and the cloud.
-
Data Analytics: Advanced analytics tools and algorithms to process and analyze the collected data, providing actionable insights for optimization and decision-making.
-
Cloud Platforms: Cloud-based IoT platforms that enable data storage, processing, and visualization, as well as integration with other enterprise systems.
-
Security Measures: Strong security protocols and practices to protect sensitive data and prevent unauthorized access to connected devices and systems.
Challenges and Considerations
While IoT offers significant benefits to the manufacturing industry, there are also challenges and considerations to keep in mind:
-
Data Security and Privacy: Ensuring the security and privacy of sensitive data collected by IoT devices is crucial to prevent cyber threats and maintain customer trust.
-
Integration with Legacy Systems: Integrating IoT solutions with existing legacy systems can be complex and may require significant investment in upgrading infrastructure.
-
Skill Gap: Implementing and maintaining IoT systems requires a skilled workforce with expertise in data analytics, cybersecurity, and IoT technologies.
-
Scalability and Interoperability: As the number of connected devices grows, ensuring scalability and interoperability between different systems and platforms becomes increasingly important.
-
Cost of Implementation: The initial cost of implementing IoT solutions, including hardware, software, and infrastructure upgrades, can be significant and may require careful planning and budgeting.
IoT Manufacturing Use Cases
IoT technology is being applied across various aspects of manufacturing, driving innovation and optimization. Some key use cases include:
Predictive Maintenance
Predictive maintenance leverages IoT sensors and data analytics to monitor the health and performance of machines and equipment in real-time. By analyzing data patterns and identifying potential issues before they occur, manufacturers can schedule maintenance proactively, reducing unplanned downtime and extending equipment lifespan.
Traditional Maintenance | Predictive Maintenance |
---|---|
Reactive approach | Proactive approach |
Unplanned downtime | Minimized downtime |
Higher maintenance costs | Lower maintenance costs |
Shorter equipment lifespan | Extended equipment lifespan |
Asset Tracking and Management
IoT-enabled asset tracking and management systems allow manufacturers to monitor the location, status, and condition of their assets in real-time. This helps optimize asset utilization, prevent losses, and streamline inventory management.
Asset Tracking Benefit | Description |
---|---|
Real-time visibility | Track asset location and status in real-time |
Optimized utilization | Ensure assets are being used efficiently |
Loss prevention | Reduce the risk of asset loss or theft |
Inventory optimization | Streamline inventory management processes |
Quality Control and Inspection
IoT sensors and computer vision systems can be used to automate quality control and inspection processes. By detecting defects and anomalies in real-time, manufacturers can ensure consistent product quality and reduce scrap rates.
Quality Control Method | Description |
---|---|
Visual inspection | Automated visual inspection using computer vision |
Sensor-based inspection | Detection of defects using IoT sensors |
Real-time monitoring | Continuous monitoring of product quality |
Data-driven insights | Analysis of quality data for process improvement |
Energy Management
IoT-enabled energy management systems help manufacturers optimize energy consumption and reduce costs. By monitoring energy usage in real-time and identifying areas of inefficiency, manufacturers can implement targeted energy-saving measures.
Energy Management Benefit | Description |
---|---|
Real-time monitoring | Track energy consumption in real-time |
Automated control | Optimize energy usage through automated control |
Predictive maintenance | Identify and address energy-related issues proactively |
Cost reduction | Reduce energy costs through optimization and efficiency |
Inventory Management
IoT technology can streamline inventory management processes by providing real-time visibility into inventory levels, location, and movement. This enables manufacturers to optimize stock levels, reduce stockouts, and improve overall supply chain efficiency.
Inventory Management Benefit | Description |
---|---|
Real-time inventory tracking | Monitor inventory levels and location in real-time |
Automated replenishment | Trigger replenishment orders based on predefined thresholds |
Supply chain optimization | Optimize inventory levels and minimize stockouts |
Improved forecasting | Enhance demand forecasting using real-time data |
Implementing IoT in Manufacturing
Implementing IoT in manufacturing requires careful planning and execution. The following steps can help ensure a successful implementation:
-
Define Objectives: Clearly define the objectives and desired outcomes of the IoT implementation, aligning them with overall business goals.
-
Assess Current Infrastructure: Evaluate the existing infrastructure and identify areas that require upgrades or modifications to support IoT integration.
-
Choose the Right IoT Platform: Select an IoT platform that meets the specific needs of the manufacturing environment, considering factors such as scalability, security, and ease of integration.
-
Develop a Robust Security Strategy: Implement a comprehensive security strategy that addresses data privacy, device security, and network protection.
-
Pilot and Scale: Start with a pilot project to validate the IoT solution and gather insights before scaling up the implementation across the organization.
-
Train and Upskill the Workforce: Provide training and upskilling opportunities to ensure the workforce has the necessary skills to operate and maintain the IoT systems.
-
Continuously Monitor and Optimize: Regularly monitor the performance of the IoT implementation and make data-driven decisions to optimize processes and drive continuous improvement.
Future of IoT in Manufacturing
As IoT technology continues to evolve, the future of IoT in manufacturing looks promising. Some key trends and developments to watch out for include:
-
Edge Computing: The increasing adoption of edge computing will enable real-time data processing and decision-making closer to the point of data generation, reducing latency and improving responsiveness.
-
5G Networks: The rollout of 5G networks will provide faster, more reliable, and low-latency connectivity, enabling the deployment of more advanced IoT applications in manufacturing.
-
Artificial Intelligence (AI) Integration: The integration of AI with IoT will enable more sophisticated data analysis, predictive capabilities, and autonomous decision-making in manufacturing processes.
-
Digital Twins: The use of digital twins, virtual replicas of physical assets and processes, will allow manufacturers to simulate and optimize operations in a virtual environment before implementing changes in the real world.
-
Collaborative Robots (Cobots): The increasing adoption of cobots, robots designed to work safely alongside human workers, will enhance productivity and flexibility in manufacturing environments.
Frequently Asked Questions (FAQ)
-
What is the role of IoT in smart manufacturing?
IoT plays a crucial role in enabling smart manufacturing by connecting machines, sensors, and devices to collect real-time data, optimize processes, and make data-driven decisions. -
How does IoT improve production efficiency in manufacturing?
IoT improves production efficiency by enabling real-time monitoring, predictive maintenance, and process optimization, reducing downtime and increasing overall equipment effectiveness (OEE). -
What are the main challenges in implementing IoT in manufacturing?
The main challenges include ensuring data security and privacy, integrating with legacy systems, addressing the skill gap, ensuring scalability and interoperability, and managing the cost of implementation. -
How can manufacturers ensure the security of their IoT systems?
Manufacturers can ensure IoT security by implementing strong security protocols, regularly updating firmware and software, using encryption and authentication, and providing employee training on security best practices. -
What are some common IoT platforms used in manufacturing?
Some common IoT platforms used in manufacturing include PTC ThingWorx, Siemens MindSphere, GE Predix, IBM Watson IoT, and Microsoft Azure IoT.
Conclusion
IoT is transforming the manufacturing industry by enabling smart factories, optimized processes, and data-driven decision-making. By leveraging the power of connected devices, real-time data analytics, and advanced technologies, manufacturers can achieve significant benefits, including increased productivity, cost reduction, improved quality, and enhanced safety.
However, implementing IoT in manufacturing also presents challenges, such as ensuring data security, integrating with legacy systems, and addressing the skill gap. To successfully adopt IoT, manufacturers must carefully plan their implementation, choose the right IoT platform, develop a robust security strategy, and continuously monitor and optimize their systems.
As IoT technology continues to evolve, the future of manufacturing looks promising, with trends such as edge computing, 5G networks, AI integration, digital twins, and collaborative robots set to drive further innovation and optimization in the industry.
By embracing IoT and its transformative potential, manufacturers can stay competitive, adapt to changing market demands, and unlock new opportunities for growth and success in the digital age.
No responses yet