What is IoT in Manufacturing?
IoT in manufacturing refers to the integration of connected devices, sensors, and software applications into manufacturing processes. These IoT devices collect real-time data from various parts of the manufacturing process, such as machines, equipment, and products. The data is then analyzed using advanced analytics tools to gain insights into the performance of the manufacturing process and identify areas for improvement.
Benefits of IoT in Manufacturing
The implementation of IoT in manufacturing offers several benefits, including:
-
Improved efficiency: IoT devices can monitor the performance of machines and equipment in real-time, enabling manufacturers to identify and address issues quickly, thereby reducing downtime and improving overall efficiency.
-
Reduced costs: By optimizing manufacturing processes and reducing waste, IoT can help manufacturers reduce operational costs and improve profitability.
-
Enhanced product quality: IoT devices can monitor the quality of products at various stages of the manufacturing process, enabling manufacturers to identify and address quality issues quickly.
-
Predictive maintenance: By analyzing data from IoT devices, manufacturers can predict when machines and equipment are likely to fail and schedule maintenance accordingly, reducing unplanned downtime.
-
Improved safety: IoT devices can monitor the safety of workers and the environment, enabling manufacturers to identify and address potential safety hazards quickly.
8 Use Cases of IoT in Manufacturing
1. Asset Tracking and Management
IoT devices can be used to track the location and status of assets, such as machines, equipment, and products, in real-time. This enables manufacturers to optimize asset utilization, reduce inventory costs, and improve overall efficiency.
2. Predictive Maintenance
By analyzing data from IoT devices, manufacturers can predict when machines and equipment are likely to fail and schedule maintenance accordingly. This reduces unplanned downtime and improves overall equipment effectiveness (OEE).
3. Quality Control
IoT devices can monitor the quality of products at various stages of the manufacturing process, enabling manufacturers to identify and address quality issues quickly. This reduces the risk of defective products reaching customers and improves overall product quality.
4. Energy Management
IoT devices can monitor energy consumption in real-time, enabling manufacturers to identify areas of high energy consumption and implement measures to reduce energy costs.
5. Supply Chain Optimization
IoT devices can track the movement of goods throughout the supply chain, enabling manufacturers to optimize inventory levels, reduce lead times, and improve overall supply chain efficiency.
6. Worker Safety
IoT devices can monitor the safety of workers and the environment, enabling manufacturers to identify and address potential safety hazards quickly. This reduces the risk of accidents and improves overall worker safety.
7. Remote Monitoring and Control
IoT devices can enable manufacturers to monitor and control manufacturing processes remotely, reducing the need for on-site personnel and improving overall efficiency.
8. Customized Production
IoT devices can enable manufacturers to collect data on customer preferences and behavior, enabling them to produce customized products that meet specific customer needs.
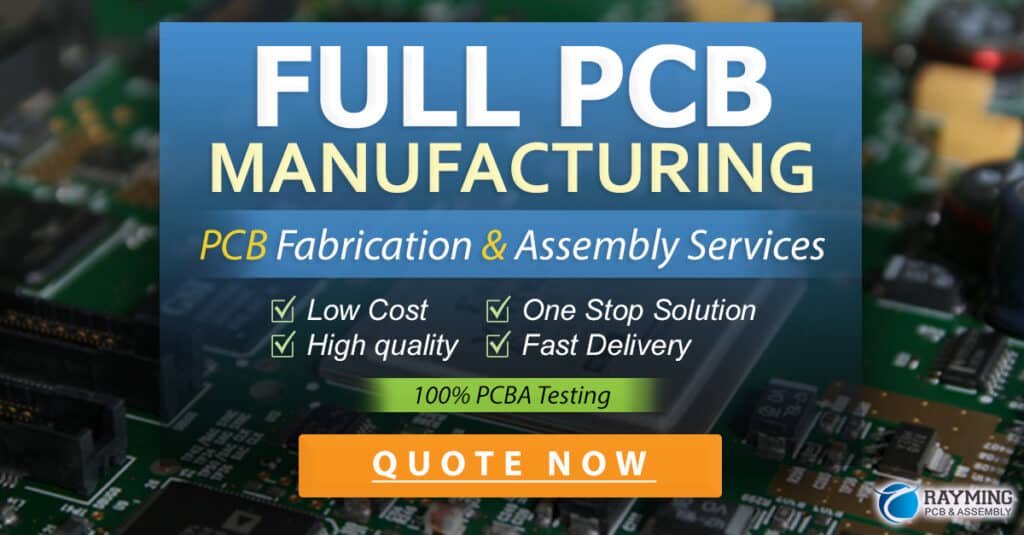
Upcoming Trends in IoT Manufacturing
1. Edge Computing
Edge computing involves processing data closer to the source, rather than sending it to a centralized cloud server. This reduces latency and improves overall system performance, enabling manufacturers to make real-time decisions based on data from IoT devices.
2. 5G Networks
The deployment of 5G networks will enable manufacturers to connect more IoT devices and transmit data faster and more reliably. This will enable manufacturers to implement more advanced IoT applications, such as real-time monitoring and control of manufacturing processes.
3. Artificial Intelligence and Machine Learning
The integration of artificial intelligence (AI) and machine learning (ML) with IoT devices will enable manufacturers to analyze large volumes of data and gain insights into manufacturing processes. This will enable manufacturers to optimize processes, reduce costs, and improve overall efficiency.
4. Blockchain Technology
The use of blockchain technology in IoT manufacturing can enable secure and transparent data sharing among various stakeholders, such as suppliers, manufacturers, and customers. This can improve supply chain efficiency and reduce the risk of counterfeit products.
5. Digital Twins
Digital twins are virtual replicas of physical assets, such as machines and equipment, that can be used to simulate and optimize manufacturing processes. The integration of IoT devices with digital twins can enable manufacturers to identify potential issues and optimize processes before they are implemented in the physical world.
Challenges in Implementing IoT in Manufacturing
While the benefits of IoT in manufacturing are significant, there are also several challenges that manufacturers must overcome:
-
Data security and privacy: IoT devices generate large volumes of data, which can be vulnerable to cyber attacks. Manufacturers must implement robust security measures to protect sensitive data and ensure the privacy of their customers.
-
Integration with legacy systems: Many manufacturers have legacy systems that may not be compatible with IoT devices. Integrating these systems with IoT can be a complex and costly process.
-
Skilled workforce: Implementing IoT in manufacturing requires a skilled workforce that can design, implement, and maintain IoT systems. Manufacturers must invest in training and development programs to ensure that their workforce has the necessary skills.
-
Cost: Implementing IoT in manufacturing can be a costly process, requiring significant investments in hardware, software, and infrastructure. Manufacturers must carefully evaluate the costs and benefits of IoT before implementing it.
FAQs
1. What is the difference between IoT and Industry 4.0?
IoT is a key enabling technology for Industry 4.0, which refers to the fourth industrial revolution. Industry 4.0 encompasses a range of technologies, including IoT, AI, robotics, and 3D printing, that are transforming manufacturing processes and enabling new business models.
2. How can manufacturers ensure the security of IoT devices?
Manufacturers can ensure the security of IoT devices by implementing robust security measures, such as encryption, authentication, and access control. They should also regularly update IoT devices with the latest security patches and conduct regular security audits to identify and address potential vulnerabilities.
3. What are the benefits of predictive maintenance in IoT manufacturing?
Predictive maintenance enables manufacturers to predict when machines and equipment are likely to fail and schedule maintenance accordingly. This reduces unplanned downtime, improves overall equipment effectiveness (OEE), and reduces maintenance costs.
4. How can manufacturers overcome the challenge of integrating IoT with legacy systems?
Manufacturers can overcome the challenge of integrating IoT with legacy systems by conducting a thorough assessment of their existing systems and identifying areas where IoT can be integrated. They can also work with IoT solution providers to develop custom integration solutions that meet their specific needs.
5. What are the key considerations for manufacturers when implementing IoT?
When implementing IoT, manufacturers should consider factors such as the specific use cases for IoT, the costs and benefits of implementation, the availability of skilled personnel, and the potential risks and challenges associated with IoT. They should also develop a clear roadmap for implementation and ensure that all stakeholders are aligned and committed to the project.
Conclusion
IoT in manufacturing has the potential to transform the way products are designed, produced, and delivered to customers. By integrating IoT devices and sensors into manufacturing processes, manufacturers can improve efficiency, reduce costs, and enhance product quality. The upcoming trends in IoT manufacturing, such as edge computing, 5G networks, and AI, will enable manufacturers to implement more advanced IoT applications and gain even greater benefits.
However, manufacturers must also be aware of the challenges associated with implementing IoT, such as data security and privacy, integration with legacy systems, and the need for a skilled workforce. By addressing these challenges and developing a clear roadmap for implementation, manufacturers can successfully implement IoT and reap the benefits of this transformative technology.
No responses yet