What is IoT in Electronics Manufacturing?
IoT in electronics manufacturing refers to the integration of connected devices, sensors, and software into the production process. This technology enables real-time monitoring, data collection, and analysis of various aspects of the manufacturing process, from raw material inventory to final product quality control.
Key Components of IoT in Electronics Manufacturing
- Connected Devices: These include sensors, actuators, and other devices that can collect and transmit data about the manufacturing process.
- Communication Networks: Wireless networks, such as Wi-Fi, Bluetooth, and cellular networks, enable the transmission of data between connected devices and the cloud.
- Cloud Computing: Cloud-based platforms store, process, and analyze the data collected from connected devices, providing insights and actionable information to manufacturers.
- Data Analytics: Advanced analytics tools, such as machine learning and artificial intelligence, help manufacturers make sense of the vast amounts of data collected and identify patterns and trends that can optimize the production process.
Benefits of IoT in Electronics Manufacturing
1. Increased Efficiency and Productivity
IoT technology enables manufacturers to monitor and optimize every aspect of the production process in real-time. By collecting data from connected devices and analyzing it using advanced analytics tools, manufacturers can identify bottlenecks, reduce downtime, and streamline operations. This leads to increased efficiency and productivity, ultimately reducing costs and improving profitability.
2. Improved Quality Control
IoT sensors can monitor various parameters of the production process, such as temperature, humidity, and vibration, ensuring that products are manufactured to the highest quality standards. Real-time data collection and analysis enable manufacturers to detect and address quality issues as they occur, reducing the number of defective products and improving overall product quality.
3. Predictive Maintenance
By monitoring the performance of manufacturing equipment in real-time, IoT technology can help manufacturers predict when maintenance is required, reducing the risk of unplanned downtime and extending the lifespan of the equipment. This predictive maintenance approach can significantly reduce maintenance costs and improve overall equipment effectiveness (OEE).
4. Enhanced Supply Chain Visibility
IoT technology can provide end-to-end visibility of the supply chain, from raw material sourcing to final product delivery. By tracking the movement of goods and materials in real-time, manufacturers can optimize inventory levels, reduce lead times, and improve customer service. This enhanced visibility also enables manufacturers to quickly respond to supply chain disruptions and minimize their impact on production.
5. Customization and Mass Personalization
IoT technology enables manufacturers to collect and analyze data on customer preferences and behavior, allowing them to offer customized and personalized products. By integrating IoT with advanced manufacturing technologies, such as 3D printing and robotics, manufacturers can produce small batches of customized products at a cost-effective price point, meeting the growing demand for personalized products.
Examples of IoT Applications in Electronics Manufacturing
1. Smart Factory
A smart factory is a fully connected and digitized manufacturing facility that leverages IoT technology to optimize every aspect of the production process. Smart factories use connected devices, such as sensors and actuators, to collect data on various parameters, such as machine performance, energy consumption, and product quality. This data is then analyzed using advanced analytics tools to identify opportunities for optimization and improvement.
Component | Description |
---|---|
Connected Devices | Sensors, actuators, and other devices that collect and transmit data about the manufacturing process |
Communication Networks | Wireless networks, such as Wi-Fi, Bluetooth, and cellular networks, that enable data transmission between devices and the cloud |
Cloud Computing | Cloud-based platforms that store, process, and analyze the data collected from connected devices |
Data Analytics | Advanced analytics tools, such as machine learning and artificial intelligence, that help manufacturers make sense of the data and identify optimization opportunities |
2. Asset Tracking and Management
IoT technology can be used to track and manage assets throughout the manufacturing process, from raw materials to finished products. By attaching RFID tags or other tracking devices to assets, manufacturers can monitor their location, condition, and usage in real-time. This enables manufacturers to optimize inventory levels, reduce waste, and improve asset utilization.
Asset Tracking Technology | Description |
---|---|
RFID | Radio-frequency identification tags that can be attached to assets for wireless tracking |
GPS | Global positioning system technology that can track the location of assets in real-time |
Bluetooth | Short-range wireless communication technology that can be used for asset tracking within a facility |
NFC | Near-field communication technology that enables short-range wireless data exchange between devices |
3. Predictive Quality Control
IoT sensors can be used to monitor various parameters of the production process, such as temperature, humidity, and vibration, to predict and prevent quality issues before they occur. By analyzing the data collected from these sensors using machine learning algorithms, manufacturers can identify patterns and trends that indicate potential quality problems. This enables manufacturers to take proactive measures to address quality issues, reducing the number of defective products and improving overall product quality.
Quality Parameter | IoT Sensor |
---|---|
Temperature | Thermocouple, RTD, thermistor |
Humidity | Capacitive, resistive, thermal humidity sensors |
Vibration | Accelerometers, piezoelectric sensors |
Pressure | Piezoresistive, capacitive, optical pressure sensors |
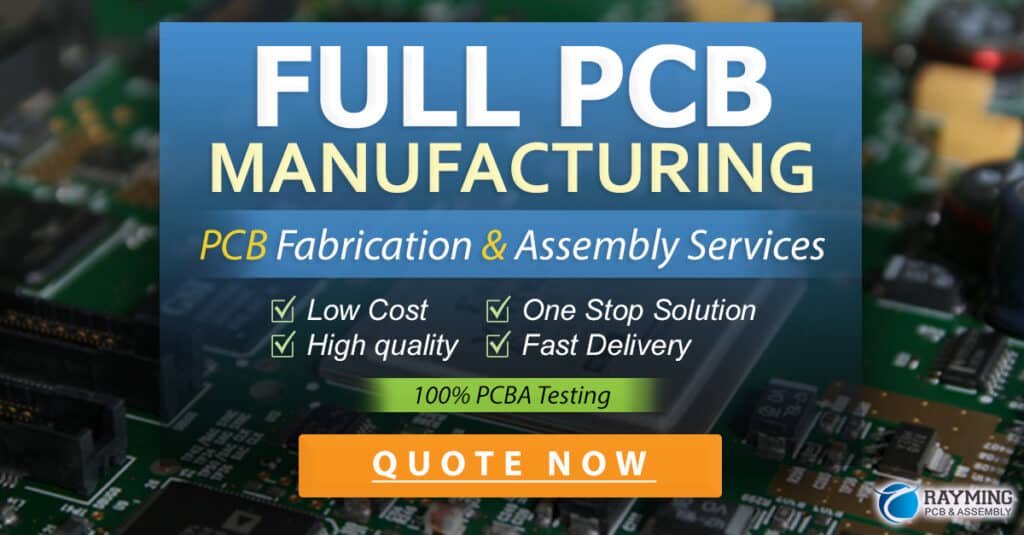
Challenges and Considerations
While IoT technology offers numerous benefits to the electronics manufacturing industry, there are also several challenges and considerations that manufacturers must address:
-
Data Security: With the increasing amount of data being collected and transmitted through IoT devices, data security becomes a critical concern. Manufacturers must implement robust security measures to protect sensitive data from unauthorized access and cyber threats.
-
Integration with Legacy Systems: Many electronics manufacturers have legacy systems and equipment that may not be compatible with IoT technology. Integrating these legacy systems with IoT can be a complex and costly process.
-
Skill Gap: Implementing and maintaining IoT technology requires a skilled workforce with expertise in areas such as data analytics, cybersecurity, and software development. Manufacturers may need to invest in training and upskilling their existing workforce or hire new talent to bridge the skill gap.
-
Return on Investment (ROI): Implementing IoT technology can require significant upfront investment, and manufacturers must carefully evaluate the potential ROI before embarking on an IoT project. This involves identifying the specific use cases where IoT can provide the most value and developing a clear business case for investment.
Future of IoT in Electronics Manufacturing
As IoT technology continues to evolve, we can expect to see even more transformative applications in the electronics manufacturing industry. Some of the future trends and developments to watch out for include:
-
5G Networks: The rollout of 5G networks will enable faster, more reliable, and more secure data transmission between IoT devices, opening up new possibilities for real-time monitoring and control of manufacturing processes.
-
Edge Computing: Edge computing, which involves processing data closer to the source rather than in the cloud, will become increasingly important in IoT applications. This will enable faster decision-making, reduced latency, and improved data security.
-
Digital Twins: Digital twins, which are virtual replicas of physical assets or processes, will become more prevalent in electronics manufacturing. By creating digital twins of manufacturing equipment and processes, manufacturers can simulate and optimize production in a virtual environment before implementing changes in the real world.
-
Collaborative Robots: IoT-enabled collaborative robots, or cobots, will increasingly be used in electronics manufacturing to work alongside human workers. These cobots can be programmed to perform repetitive or dangerous tasks, freeing up human workers to focus on higher-value activities.
FAQ
- What are the key benefits of IoT in electronics manufacturing?
-
IoT technology enables increased efficiency and productivity, improved quality control, predictive maintenance, enhanced supply chain visibility, and customization and mass personalization.
-
What are some examples of IoT applications in electronics manufacturing?
-
Examples of IoT applications in electronics manufacturing include smart factories, asset tracking and management, and predictive quality control.
-
What are the main challenges and considerations when implementing IoT in electronics manufacturing?
-
The main challenges and considerations include data security, integration with legacy systems, skill gap, and return on investment (ROI).
-
What are some future trends and developments in IoT for electronics manufacturing?
-
Future trends and developments include the rollout of 5G networks, edge computing, digital twins, and collaborative robots (cobots).
-
How can manufacturers evaluate the potential ROI of an IoT project?
- To evaluate the potential ROI of an IoT project, manufacturers should identify the specific use cases where IoT can provide the most value and develop a clear business case for investment. This involves considering factors such as the cost of implementation, potential cost savings, and the impact on key performance indicators (KPIs) such as efficiency, quality, and customer satisfaction.
Conclusion
IoT technology is transforming the electronics manufacturing industry, enabling manufacturers to optimize every aspect of the production process, from raw material sourcing to final product delivery. By leveraging connected devices, advanced analytics, and cloud computing, manufacturers can increase efficiency, improve product quality, and offer customized and personalized products to meet the growing demand for personalization.
While there are challenges and considerations to address, such as data security and integration with legacy systems, the potential benefits of IoT in electronics manufacturing are significant. As IoT technology continues to evolve, we can expect to see even more transformative applications in the industry, from 5G networks and edge computing to digital twins and collaborative robots.
To stay competitive in the rapidly evolving electronics manufacturing landscape, manufacturers must embrace IoT technology and develop a clear strategy for implementation. By carefully evaluating the potential ROI and addressing the challenges and considerations involved, manufacturers can unlock the full potential of IoT and position themselves for success in the digital age.
No responses yet