What is an Automotive PCB?
An automotive PCB is a specialized printed circuit board designed to withstand the harsh conditions and demands of the automotive environment. These PCBs are responsible for controlling and regulating various electronic systems within a vehicle, such as the engine control unit (ECU), infotainment system, and safety features like anti-lock braking systems (ABS) and airbags.
Automotive PCBs differ from standard PCBs in several ways:
- Durability: Automotive PCBs are built to endure extreme temperatures, vibrations, and moisture levels, ensuring reliable performance in demanding conditions.
- High-temperature resistance: With temperatures under the hood often reaching up to 125°C (257°F), automotive PCBs must be able to withstand these extreme heat levels without degrading or malfunctioning.
- Electromagnetic compatibility (EMC): Automotive PCBs are designed to minimize electromagnetic interference (EMI) and ensure compatibility with other electronic components within the vehicle.
- Strict quality control: Due to the critical nature of their applications, automotive PCBs undergo rigorous testing and quality control measures to ensure they meet the highest standards of reliability and safety.
The Role of Automotive PCBs in Modern Vehicles
Automotive PCBs play a vital role in the functioning of modern vehicles. As cars become increasingly sophisticated, with advanced features like driver assistance systems, connected services, and electric powertrains, the importance of reliable and high-performance PCBs continues to grow.
Some of the key areas where automotive PCBs are employed include:
Engine Control Unit (ECU)
The ECU is the brain of your vehicle, responsible for managing and optimizing engine performance. It relies on a complex PCB to process data from various sensors and adjust engine parameters accordingly, ensuring optimal fuel efficiency, emissions control, and overall performance.
Infotainment Systems
Modern vehicles often feature advanced infotainment systems that provide navigation, audio and video playback, and connectivity options like Bluetooth and Wi-Fi. The PCBs within these systems handle the processing and communication of data, enabling seamless integration with smartphones and other devices.
Safety Features
Automotive PCBs are crucial for the operation of safety features such as ABS, electronic stability control (ESC), and airbag deployment systems. These PCBs must be highly reliable and respond quickly to ensure the safety of passengers in the event of an emergency.
Hybrid and Electric Vehicles
As the automotive industry shifts towards electrification, PCBs play an increasingly important role in the management of electric powertrains, battery systems, and regenerative braking. The high-voltage environments in these vehicles require specialized PCBs that can handle the increased power demands and ensure safe operation.
Challenges in Automotive PCB Design and Manufacturing
Designing and manufacturing automotive PCBs presents several unique challenges due to the demanding environment in which they operate and the stringent quality and safety requirements they must meet.
Some of the key challenges include:
- Thermal management: With high temperatures under the hood, automotive PCBs must be designed with effective thermal management in mind. This often involves the use of specialized materials, such as ceramic substrates or metal core PCBs, to dissipate heat and prevent thermal damage.
- Vibration and shock resistance: Automotive PCBs are subjected to constant vibrations and occasional shocks during vehicle operation. Designers must employ techniques like underfill, conformal coating, and robust component mounting to ensure the PCBs can withstand these stresses without failing.
- Miniaturization: As vehicles become more compact and feature-rich, there is a growing need for smaller, more space-efficient PCBs. This requires advanced design techniques and the use of high-density interconnect (HDI) technology to pack more functionality into smaller form factors.
- Regulatory compliance: Automotive PCBs must comply with a range of international standards and regulations, such as ISO 26262 for functional safety and AEC-Q100 for component qualification. Adhering to these standards ensures the PCBs are suitable for use in automotive applications and meet the necessary quality and reliability requirements.
- Supply chain management: With the global nature of the automotive industry, PCB manufacturers must have robust supply chain management processes in place to ensure a steady supply of components and materials, as well as to manage potential disruptions due to geopolitical events or natural disasters.
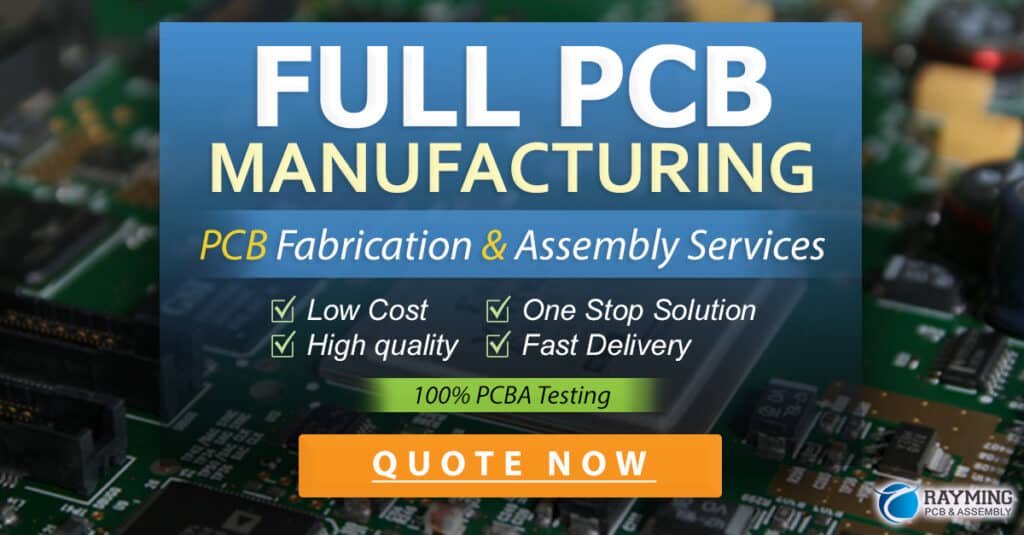
Future Trends in Automotive PCB Technology
As the automotive industry continues to evolve, so too will the technology behind automotive PCBs. Some of the key trends shaping the future of automotive PCBs include:
Advanced Driver Assistance Systems (ADAS) and Autonomous Driving
The proliferation of ADAS features and the development of autonomous driving technologies will require increasingly sophisticated PCBs to handle the processing and communication of vast amounts of data from sensors, cameras, and other sources. These PCBs will need to be highly reliable, secure, and capable of real-time processing to ensure the safe operation of the vehicle.
Vehicle-to-Everything (V2X) Communication
V2X communication, which enables vehicles to communicate with each other, infrastructure, and pedestrians, will rely on advanced PCBs to handle the high-speed, low-latency data transmission required for these applications. PCBs will need to be designed with robust wireless connectivity and security features to ensure the integrity and privacy of the data being exchanged.
Flexible and Stretchable PCBs
As vehicles become more connected and feature-rich, there will be a growing demand for flexible and stretchable PCBs that can conform to the curves and contours of the vehicle interior. These PCBs will enable the integration of electronics into previously inaccessible areas, such as the steering wheel or door panels, opening up new possibilities for innovative features and designs.
Sustainability and Recycling
With increasing focus on environmental sustainability, the automotive industry will need to address the challenge of recycling and disposing of PCBs at the end of a vehicle’s life. This will require the development of more eco-friendly PCB materials and manufacturing processes, as well as improved recycling technologies to recover valuable materials from used PCBs.
Conclusion
Automotive PCBs are the unsung heroes of the modern vehicle, quietly working behind the scenes to ensure the smooth operation of the complex electronic systems that keep our cars running safely and efficiently. As the automotive industry continues to evolve, with the rise of electric vehicles, autonomous driving, and connected services, the importance of high-quality, reliable automotive PCBs will only continue to grow.
By understanding the unique challenges and requirements of automotive PCB design and manufacturing, and staying abreast of the latest trends and technologies, PCB manufacturers and automotive engineers can work together to create the next generation of vehicles that are smarter, safer, and more sustainable than ever before.
FAQ
1. What is the difference between an automotive PCB and a standard PCB?
Automotive PCBs are designed to withstand the harsh conditions and demands of the automotive environment, such as extreme temperatures, vibrations, and moisture levels. They also have higher standards for quality control and electromagnetic compatibility compared to standard PCBs.
2. Why are automotive PCBs important for the safety of a vehicle?
Automotive PCBs are crucial for the operation of safety features such as anti-lock braking systems (ABS), electronic stability control (ESC), and airbag deployment systems. These PCBs must be highly reliable and respond quickly to ensure the safety of passengers in the event of an emergency.
3. What are some of the challenges in designing and manufacturing automotive PCBs?
Some of the key challenges include thermal management, vibration and shock resistance, miniaturization, regulatory compliance, and supply chain management. Automotive PCBs must be designed to withstand high temperatures, constant vibrations, and occasional shocks, while also meeting strict quality and safety standards.
4. How are automotive PCBs adapting to the trend of vehicle electrification?
As the automotive industry shifts towards electric vehicles, PCBs play an increasingly important role in the management of electric powertrains, battery systems, and regenerative braking. The high-voltage environments in these vehicles require specialized PCBs that can handle the increased power demands and ensure safe operation.
5. What are some of the future trends in automotive PCB technology?
Some of the key trends shaping the future of automotive PCBs include the development of advanced driver assistance systems (ADAS) and autonomous driving technologies, vehicle-to-everything (V2X) communication, flexible and stretchable PCBs, and a focus on sustainability and recycling.
Component | Function |
---|---|
Engine Control Unit (ECU) | Manages and optimizes engine performance using a complex PCB to process data from sensors and adjust engine parameters. |
Infotainment Systems | Provides navigation, audio/video playback, and connectivity options using PCBs to handle data processing and communication. |
Safety Features (ABS, ESC, Airbags) | Ensures passenger safety using highly reliable PCBs that respond quickly in emergency situations. |
Hybrid and Electric Vehicle Systems | Manages electric powertrains, battery systems, and regenerative braking using specialized PCBs designed for high-voltage environments. |
No responses yet