What is an IMS PCB?
An Insulated Metal Substrate (IMS) PCB is a specialized type of printed circuit board that offers superior thermal management compared to traditional FR-4 PCBs. IMS PCBs consist of a metal base layer, typically aluminum, that is bonded to a thin dielectric layer and topped with a copper circuit layer. This unique construction allows heat to be efficiently conducted away from electronic components, making IMS PCBs ideal for applications that generate significant amounts of heat.
Key Features of IMS PCBs
- Metal substrate (usually aluminum) for excellent heat dissipation
- Thin dielectric layer for electrical insulation
- Copper circuit layer for component mounting and interconnections
- High thermal conductivity
- Improved reliability and lifespan of electronic components
Advantages of Using IMS PCBs
Superior Heat Dissipation
The primary advantage of using an IMS PCB is its ability to efficiently dissipate heat generated by electronic components. The metal substrate, typically aluminum, has a much higher thermal conductivity than the FR-4 material used in traditional PCBs. This allows heat to be quickly conducted away from components and spread evenly across the board, preventing hot spots and thermal damage.
Comparison of Thermal Conductivity
Material | Thermal Conductivity (W/mK) |
---|---|
Aluminum | 205 |
Copper | 385 |
FR-4 | 0.3 |
As shown in the table above, aluminum has a thermal conductivity nearly 700 times higher than FR-4, making it an excellent choice for heat dissipation in IMS PCBs.
Improved Reliability and Lifespan
By effectively managing heat, IMS PCBs can significantly improve the reliability and lifespan of electronic components. Excessive heat is one of the primary causes of component failure, as it can lead to thermal stress, material degradation, and reduced performance. By keeping components cooler, IMS PCBs reduce the risk of thermal damage and extend the operational life of the electronic device.
Compact Design and Weight Reduction
IMS PCBs enable more compact designs compared to traditional PCBs with external heatsinks. The metal substrate serves as a built-in heatsink, eliminating the need for additional cooling components. This allows for smaller form factors and reduced overall weight, which is particularly important in applications where space and weight are critical factors, such as in the automotive and aerospace industries.
Applications of IMS PCBs
Power Electronics
IMS PCBs are widely used in power electronic applications, such as:
– Power converters
– Motor drives
– Inverters
– Battery management systems
These applications often involve high current densities and generate significant amounts of heat. IMS PCBs provide the necessary thermal management to ensure reliable operation and prevent component failure.
LED Lighting
LED lighting applications benefit greatly from the use of IMS PCBs. High-power LEDs generate a considerable amount of heat, which must be effectively dissipated to maintain optimal performance and longevity. IMS PCBs offer a compact and efficient solution for thermal management in LED lighting fixtures, allowing for brighter and more reliable illumination.
Automotive Electronics
The automotive industry relies heavily on IMS PCBs for various electronic systems, including:
– Engine control units (ECUs)
– Power steering controls
– Braking systems
– Infotainment systems
These applications are subject to harsh environmental conditions, such as high temperatures and vibrations. IMS PCBs provide the necessary thermal stability and mechanical strength to withstand these challenges and ensure reliable operation.
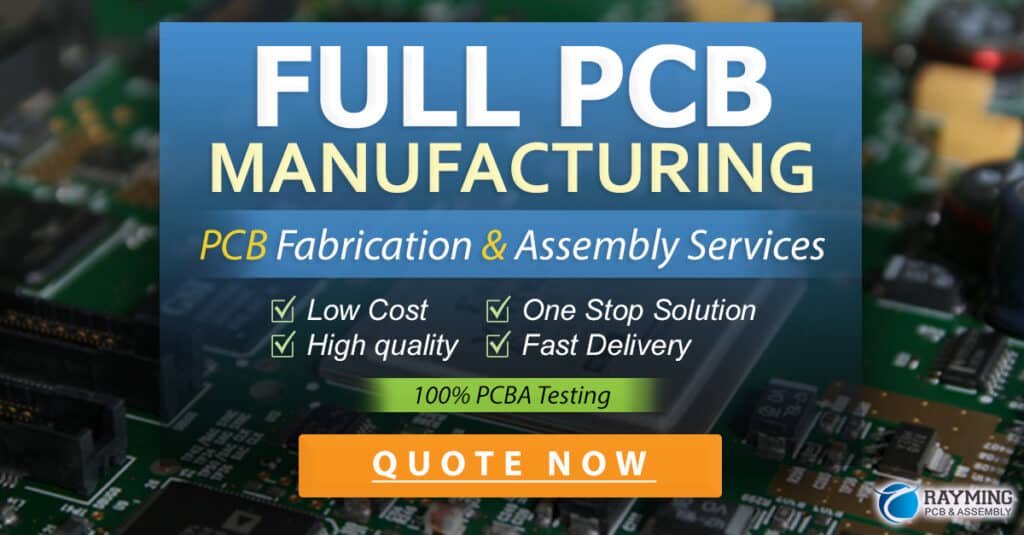
Designing with IMS PCBs
Thermal Design Considerations
When designing with IMS PCBs, it is essential to consider the thermal characteristics of the board and the components. Thermal simulations and analysis should be performed to identify potential hot spots and optimize the placement of components for effective heat dissipation. Factors such as copper thickness, dielectric layer thickness, and component power dissipation should be carefully considered to ensure optimal thermal performance.
Dielectric Material Selection
The choice of dielectric material is crucial in IMS PCB design. The dielectric layer must provide adequate electrical insulation while minimizing thermal resistance. Common dielectric materials used in IMS PCBs include:
– Aluminum oxide (Al2O3)
– Aluminum nitride (AlN)
– Boron nitride (BN)
Each material has its own thermal and electrical properties, and the selection depends on the specific requirements of the application.
Circuit Layer Design
The copper circuit layer in an IMS PCB should be designed to maximize heat transfer from components to the metal substrate. This can be achieved by using wider traces and larger copper pours around high-power components. Thermal vias can also be incorporated to provide additional heat conduction paths through the dielectric layer.
Manufacturing Process of IMS PCBs
Substrate Preparation
The manufacturing process of IMS PCBs begins with the preparation of the metal substrate, typically aluminum. The substrate is cleaned and treated to ensure proper adhesion of the dielectric layer. Surface treatments such as anodizing or brushing may be applied to enhance bonding and improve thermal performance.
Dielectric Layer Application
The dielectric layer is applied to the metal substrate using techniques such as screen printing, lamination, or direct bonding. The dielectric material is carefully selected to provide the desired thermal and electrical properties. The thickness of the dielectric layer is precisely controlled to ensure optimal insulation and heat transfer.
Circuit Layer Formation
The copper circuit layer is formed on top of the dielectric layer using standard PCB fabrication techniques, such as photolithography and etching. The copper thickness and trace widths are designed to meet the electrical and thermal requirements of the application. Thermal vias may be drilled and plated to establish thermal connections between the circuit layer and the metal substrate.
Finishing and Assembly
After the circuit layer formation, the IMS PCB undergoes finishing processes such as solder mask application, surface finish (e.g., ENIG, OSP), and silkscreen printing. The board is then ready for component assembly, which can be performed using standard SMT or through-hole techniques. Special care must be taken during the assembly process to ensure proper thermal interface between components and the IMS PCB.
FAQ
1. What is the difference between an IMS PCB and a standard FR-4 PCB?
An IMS PCB has a metal substrate, typically aluminum, that provides superior thermal conductivity compared to the FR-4 material used in standard PCBs. This allows IMS PCBs to efficiently dissipate heat generated by electronic components, improving reliability and lifespan.
2. Can IMS PCBs be used for high-frequency applications?
Yes, IMS PCBs can be used for high-frequency applications. However, the metal substrate may introduce some signal integrity challenges due to its electrical conductivity. Proper design techniques, such as the use of ground planes and controlled impedance traces, can help mitigate these issues.
3. Are IMS PCBs more expensive than traditional PCBs?
IMS PCBs are generally more expensive than traditional FR-4 PCBs due to the specialized materials and manufacturing processes involved. However, the increased cost is often justified by the improved thermal performance and reliability, especially in applications where thermal management is critical.
4. Can IMS PCBs be manufactured with multiple layers?
Yes, IMS PCBs can be manufactured with multiple copper layers, allowing for more complex circuit designs. The additional layers are separated by dielectric materials and connected through vias, similar to traditional multi-layer PCBs.
5. How do I choose the right dielectric material for my IMS PCB?
The choice of dielectric material depends on the specific requirements of your application. Factors to consider include the required electrical insulation, thermal conductivity, and compatibility with the metal substrate and copper layer. It is recommended to consult with an experienced IMS PCB manufacturer to select the most appropriate dielectric material for your project.
Conclusion
IMS PCBs offer a superior solution for thermal management in electronic applications, providing excellent heat dissipation, improved reliability, and extended component lifespan. By utilizing a metal substrate, typically aluminum, and a thin dielectric layer, IMS PCBs efficiently conduct heat away from electronic components, preventing thermal damage and ensuring optimal performance.
The unique properties of IMS PCBs make them ideal for a wide range of applications, including power electronics, LED lighting, automotive electronics, and more. When designing with IMS PCBs, careful consideration must be given to thermal design, dielectric material selection, and circuit layer layout to maximize the benefits of this technology.
As electronic devices continue to push the boundaries of performance and power density, the demand for effective thermal management solutions like IMS PCBs will only continue to grow. By understanding the advantages, applications, and design considerations of IMS PCBs, engineers and manufacturers can create more reliable, efficient, and compact electronic products that meet the ever-increasing demands of the market.
No responses yet