Introduction to PWM and the 555 Timer IC
Pulse Width Modulation (PWM) is a powerful technique used in a wide range of applications, from controlling LED brightness to regulating motor speeds. At its core, PWM involves generating a square wave signal with a variable duty cycle, allowing for efficient control of average voltage or current. One of the most popular and versatile tools for creating PWM signals is the 555 timer IC. In this comprehensive article, we will delve into the world of PWM Circuits, focusing on the 555 timer and its role in generating PWM signals.
What is Pulse Width Modulation (PWM)?
Pulse Width Modulation is a method of encoding analog signal levels into a pulsing digital signal. In PWM, the width (duration) of the pulses is modulated, while the frequency remains constant. The ratio of the pulse width to the period (duty cycle) determines the average voltage delivered to the load. By varying the duty cycle, we can control the amount of power sent to a device, such as an LED or a motor.
PWM offers several advantages over traditional analog control methods:
-
Efficiency: PWM allows for efficient power delivery, as the switching devices (transistors) are either fully on or off, minimizing power dissipation.
-
Simplicity: PWM can be easily generated using digital circuits, such as microcontrollers or dedicated PWM ICs.
-
Noise immunity: PWM signals are less susceptible to noise compared to analog signals, making them suitable for use in noisy environments.
The 555 Timer IC
The 555 timer is a versatile integrated circuit that can be used to generate precise timing pulses, oscillations, and PWM signals. It was introduced in 1971 by Signetics and has since become one of the most popular ICs in the world. The 555 timer is available in two package types: the 8-pin DIP (Dual Inline Package) and the 8-pin SOIC (Small Outline Integrated Circuit).
The 555 timer consists of the following key components:
- Two comparators
- An SR (Set-Reset) flip-flop
- A discharge transistor
- A voltage divider network
These components work together to generate output pulses based on the input trigger and threshold voltages.
Basics of PWM Signal Generation
To generate a PWM signal, we need to create a square wave with a variable duty cycle. The duty cycle is defined as the ratio of the pulse width (ton) to the total period (T) of the waveform, expressed as a percentage:
Duty Cycle = (ton / T) × 100%
For example, a 50% duty cycle means that the pulse is high for half of the period and low for the other half.
Controlling the Duty Cycle
To control the duty cycle of a PWM signal, we can use one of the following methods:
-
Analog control: By varying the voltage level of an analog input signal, we can change the duty cycle proportionally. This method is simple but susceptible to noise.
-
Digital control: Using a microcontroller or a digital-to-analog converter (DAC), we can generate precise digital values to set the duty cycle. This method offers better control and noise immunity but requires additional hardware.
Frequency Considerations
The frequency of a PWM signal determines how fast the pulses are generated. The choice of frequency depends on the application and the response time of the load. For example:
-
Low frequencies (100 Hz or less) are suitable for controlling LED brightness or motor speed, as the human eye and mechanical systems have slow response times.
-
High frequencies (1 kHz or more) are used in switch-mode power supplies, audio amplifiers, and other applications where fast switching is required.
It is important to note that higher frequencies may lead to increased switching losses and electromagnetic interference (EMI).
555 Timer-Based PWM Circuits
The 555 timer IC can be configured in various ways to generate PWM signals. In this section, we will explore two common configurations: astable mode and monostable mode.
Astable Mode
In astable mode, the 555 timer generates a continuous square wave with a fixed frequency and duty cycle. The duty cycle can be adjusted by changing the values of the external resistors and capacitors connected to the IC.
Basic Astable Circuit
Here is a basic astable circuit using the 555 timer:
Component | Value |
---|---|
R1 | 1 kΩ |
R2 | 10 kΩ |
C1 | 0.1 μF |
The output frequency (f) and duty cycle (D) can be calculated using the following formulas:
f = 1.44 / ((R1 + 2R2) × C1)
D = (R1 + R2) / (R1 + 2R2)
By varying the values of R1, R2, and C1, we can achieve different frequencies and duty cycles.
PWM Control in Astable Mode
To control the duty cycle in astable mode, we can replace R2 with a potentiometer or use a transistor to modulate the voltage at the discharge pin (pin 7) of the 555 timer. By changing the voltage at pin 7, we can alter the time constant and, consequently, the duty cycle of the output waveform.
Monostable Mode
In monostable mode, the 555 timer generates a single output pulse with a fixed duration (ton) when triggered by an input pulse. The duration of the output pulse can be controlled by an external RC network.
Basic Monostable Circuit
Here is a basic monostable circuit using the 555 timer:
Component | Value |
---|---|
R1 | 10 kΩ |
C1 | 1 μF |
The output pulse duration (ton) can be calculated using the following formula:
ton = 1.1 × R1 × C1
By triggering the monostable circuit with a series of input pulses, we can generate a PWM signal with a variable duty cycle.
PWM Control in Monostable Mode
To control the duty cycle in monostable mode, we can vary the frequency of the input trigger pulses. A higher trigger frequency will result in a higher duty cycle, as the output pulses will occupy a larger portion of the total period.
Alternatively, we can use a microcontroller to generate the trigger pulses with precise timing, allowing for fine control over the duty cycle.
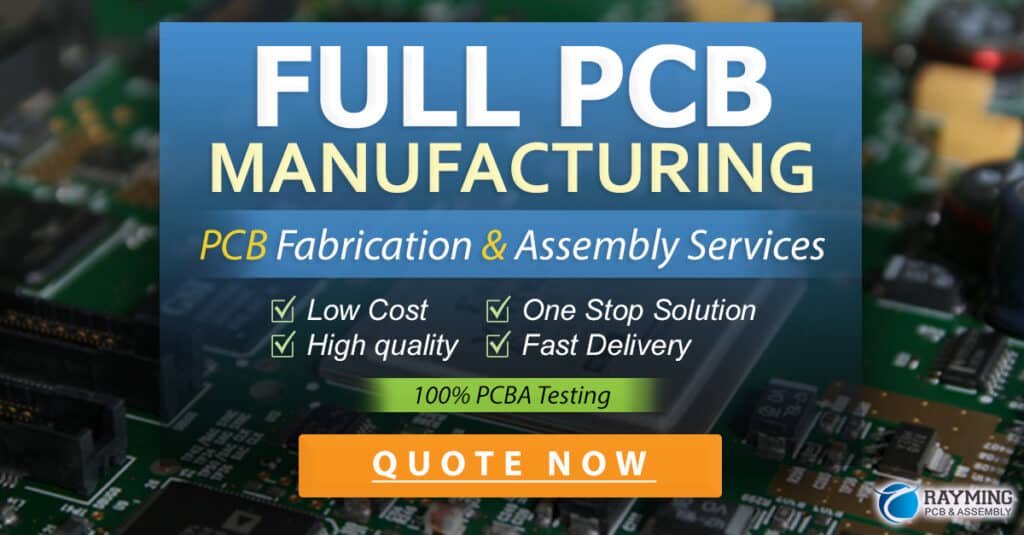
Applications of PWM Circuits
PWM circuits find applications in a wide range of fields, including:
-
LED brightness control: PWM can be used to dim LEDs by varying the duty cycle of the driving signal. This method is more efficient than analog dimming and allows for a wider dimming range.
-
Motor speed control: By applying PWM to the motor driver circuit, we can control the speed of DC motors. The average voltage delivered to the motor is proportional to the duty cycle, allowing for smooth speed regulation.
-
Switch-mode power supplies (SMPS): PWM is used in SMPS to regulate the output voltage by controlling the on/off time of the switching devices (transistors or MOSFETs).
-
Audio amplifiers: PWM-based Class-D audio amplifiers offer high efficiency and reduced heat generation compared to traditional anaLog Amplifiers.
-
Temperature control: PWM can be employed in temperature control systems, such as in PID controllers, to maintain a stable temperature by modulating the power delivered to a heating or cooling element.
Advantages and Limitations of PWM Circuits
Advantages
- Efficient power delivery
- Simple implementation using digital circuits
- Wide range of control (0-100% duty cycle)
- Reduced heat generation in switching devices
- Suitable for battery-powered applications
Limitations
-
EMI: PWM circuits can generate high-frequency noise that may interfere with nearby electronic devices. Proper filtering and shielding techniques must be employed to mitigate EMI.
-
Limited resolution: The resolution of a PWM signal is determined by the frequency and the available clock speed of the generating circuit. Higher resolutions require faster clocks and may be limited by the hardware capabilities.
-
Switching losses: At high frequencies, the switching devices in PWM circuits may experience increased power dissipation due to the finite switching times. This can reduce efficiency and may require additional heat sinking.
Frequently Asked Questions (FAQ)
-
What is the difference between PWM and analog control?
PWM uses digital pulses to control the average voltage or current delivered to a load, while analog control uses continuous voltage or current levels. PWM is more efficient and less susceptible to noise compared to analog control. -
Can I use the 555 timer for high-frequency PWM applications?
The 555 timer is suitable for low to medium-frequency PWM applications (up to 100 kHz). For higher frequencies, specialized PWM ICs or microcontrollers with dedicated PWM modules are recommended. -
How can I change the frequency of a 555 timer-based PWM circuit?
To change the frequency of a 555 timer-based PWM circuit, you can modify the values of the external resistors and capacitors connected to the IC. Refer to the formulas provided in the article for calculating the frequency based on the component values. -
What is the maximum duty cycle I can achieve with a PWM circuit?
Theoretically, the maximum duty cycle is 100%, meaning the pulse is always high. However, in practice, the maximum achievable duty cycle may be limited by the rise and fall times of the generating circuit and the response time of the load. -
Are there any safety concerns when working with PWM circuits?
PWM circuits can generate high voltages and currents, depending on the application. Always follow proper safety guidelines, such as using appropriate voltage and current ratings for components, and ensure proper insulation and grounding. When working with high-power applications, consult a qualified engineer or technician.
Conclusion
Pulse Width Modulation (PWM) is a versatile technique for controlling power delivery in various applications. The 555 timer IC is a popular choice for generating PWM signals due to its simplicity and flexibility. By understanding the basics of PWM and the operation of the 555 timer, you can design and implement efficient PWM circuits for a wide range of projects.
This article has covered the fundamentals of PWM, the 555 timer IC, and common PWM circuit configurations. We have also discussed the applications, advantages, and limitations of PWM circuits.
As with any electronic circuit, proper design and safety considerations are essential when working with PWM. Always refer to the datasheets and application notes of the components you are using and consult with experienced professionals when necessary.
PWM is a powerful tool in the world of electronics, and mastering its principles opens up a wide range of possibilities for efficient and precise control in your projects.
No responses yet