What is a Hydrogen Sensor?
A hydrogen sensor is an electronic device designed to detect and measure the presence of hydrogen gas in the surrounding environment. These sensors are crucial safety instruments in industries where hydrogen is used, stored, or transported, as they can provide an early warning of potential leaks or hazardous concentrations of the gas.
Hydrogen sensors work by converting the chemical energy of hydrogen gas into an electrical signal that can be measured and processed. When hydrogen molecules come into contact with the sensor’s sensing element, a chemical reaction occurs, generating an electrical current or changing the sensor’s resistance. The sensor’s electronics then interpret this signal and provide an output indicating the presence and concentration of hydrogen gas.
Why are Hydrogen Sensors Important?
Hydrogen sensors play a vital role in ensuring safety in various applications where hydrogen gas is used or produced. Here are some key reasons why hydrogen sensors are important:
-
Early Leak Detection: Hydrogen sensors can quickly detect even small amounts of hydrogen gas leaking from storage tanks, pipelines, or other equipment. Early detection allows for prompt action to be taken, preventing the accumulation of dangerous concentrations of hydrogen and reducing the risk of fires or explosions.
-
Monitoring Hydrogen Concentrations: In many applications, it is essential to maintain hydrogen concentrations within safe limits. Hydrogen sensors continuously monitor the gas concentration, providing real-time data that can be used to adjust processes or trigger alarms if concentrations exceed predetermined thresholds.
-
Compliance with Safety Regulations: Many industries are subject to strict safety regulations regarding the use and handling of hydrogen gas. Hydrogen sensors help ensure compliance with these regulations by providing accurate and reliable monitoring of hydrogen levels.
-
Protecting Personnel and Equipment: By detecting hydrogen leaks early, hydrogen sensors help protect personnel from exposure to dangerous concentrations of the gas. They also help prevent damage to equipment by allowing for timely shutdown or other protective measures in the event of a leak.
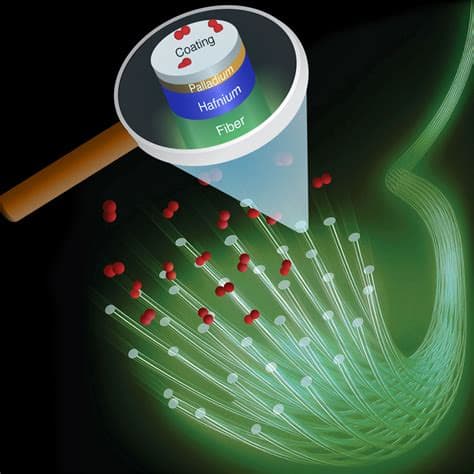
Types of Hydrogen Sensors
There are several types of hydrogen sensors available, each with its own working principle and characteristics. Some of the most common types include:
1. Catalytic Hydrogen Sensors
Catalytic hydrogen sensors, also known as pellistor sensors, use a catalytic bead to detect the presence of hydrogen gas. The sensing element consists of a small pellet of catalyst material, typically platinum or palladium, heated to a high temperature. When hydrogen gas comes into contact with the heated catalyst, it oxidizes, releasing heat and increasing the temperature of the pellet. This temperature change is detected by a Wheatstone Bridge circuit, which generates an electrical signal proportional to the hydrogen concentration.
Catalytic hydrogen sensors are simple, reliable, and have a relatively low cost. However, they have some limitations:
- They require oxygen to function, so they may not be suitable for use in inert atmospheres.
- They can be sensitive to poisoning by certain compounds, such as silicones or sulfur, which can reduce their sensitivity over time.
- They have a limited detection range, typically up to about 4% hydrogen in air.
2. Electrochemical Hydrogen Sensors
Electrochemical hydrogen sensors work on the principle of a fuel cell. They consist of an anode, a cathode, and an electrolyte. When hydrogen gas diffuses into the sensor, it is oxidized at the anode, generating an electrical current. The current is proportional to the concentration of hydrogen gas.
Electrochemical sensors have several advantages:
- They are highly selective to hydrogen and are not easily cross-sensitive to other gases.
- They have a wide detection range, from low ppm levels up to 100% hydrogen.
- They have a relatively fast response time and good accuracy.
However, they also have some limitations:
- They have a limited lifetime, typically 1-2 years, due to the consumption of the electrolyte.
- They can be sensitive to changes in temperature and humidity.
- They require a bias voltage to operate, which can add complexity to the sensor electronics.
3. Metal Oxide Semiconductor (MOS) Hydrogen Sensors
Metal oxide semiconductor (MOS) hydrogen sensors use a metal oxide sensing element, typically tin dioxide (SnO2), to detect the presence of hydrogen gas. The sensing element is heated to a high temperature, typically 300-500°C. When hydrogen gas comes into contact with the heated metal oxide, it reduces the oxide, changing its electrical resistance. This change in resistance is measured and used to determine the hydrogen concentration.
MOS sensors have several advantages:
- They have a wide detection range, from low ppm levels up to 100% hydrogen.
- They have a long lifetime, as the sensing element is not consumed during operation.
- They are relatively low cost and easy to manufacture.
However, they also have some limitations:
- They can be sensitive to other reducing gases, such as carbon monoxide, which can cause cross-sensitivity.
- They require a high operating temperature, which can lead to high power consumption.
- They can have a slow response time, especially at low hydrogen concentrations.
4. Optical Hydrogen Sensors
Optical hydrogen sensors use the principle of absorption spectroscopy to detect the presence of hydrogen gas. They work by shining a light source, typically a laser or LED, through a sample of gas and measuring the amount of light absorbed at a specific wavelength. Hydrogen gas has a unique absorption spectrum, allowing it to be selectively detected.
Optical sensors have several advantages:
- They are highly selective to hydrogen and are not easily cross-sensitive to other gases.
- They can operate in inert atmospheres, as they do not require oxygen to function.
- They have a fast response time and can detect hydrogen in real-time.
However, they also have some limitations:
- They can be more expensive than other types of sensors due to the cost of the optical components.
- They may require more complex electronics and signal processing to interpret the absorption spectrum.
- They can be sensitive to changes in temperature and pressure, which can affect the absorption spectrum.
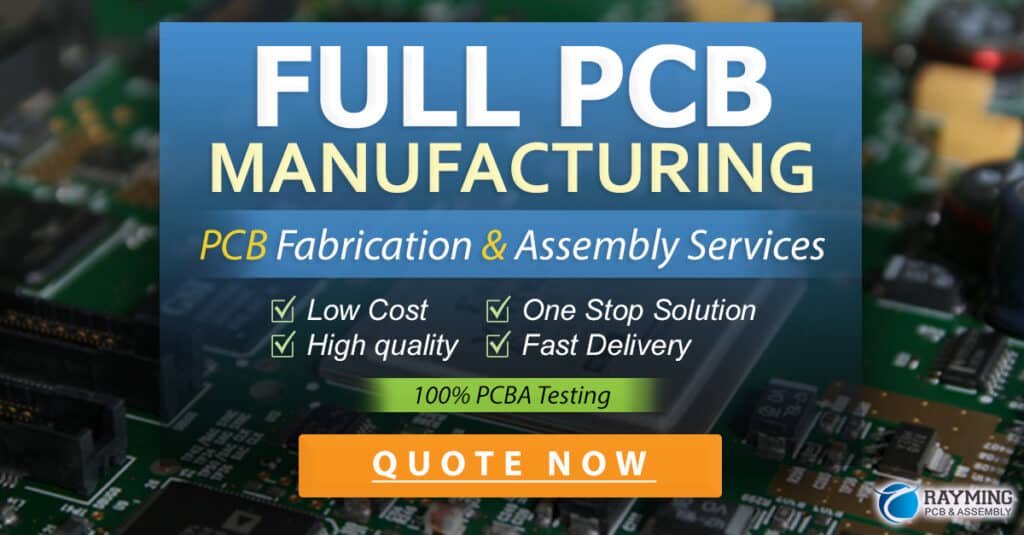
Applications of Hydrogen Sensors
Hydrogen sensors find applications in a wide range of industries where hydrogen is used, stored, or transported. Some of the most common applications include:
1. Fuel Cell Vehicles
Hydrogen fuel cell vehicles use hydrogen as a fuel source to generate electricity, which powers the vehicle’s electric motor. Hydrogen sensors are used to monitor the hydrogen concentration in the fuel cell system and to detect any leaks in the hydrogen storage tanks or fuel lines. This ensures the safe operation of the vehicle and protects the passengers and the environment.
2. Hydrogen Refueling Stations
Hydrogen refueling stations are facilities where fuel cell vehicles can be refueled with hydrogen gas. These stations use hydrogen sensors to monitor the hydrogen concentration in the refueling area and to detect any leaks in the storage tanks or dispensing equipment. This ensures the safety of the refueling process and prevents accidents.
3. Industrial Processes
Many industrial processes use hydrogen gas as a feedstock or byproduct. For example, in the oil and gas industry, hydrogen is used in hydrotreating processes to remove sulfur and other impurities from fuels. In the chemical industry, hydrogen is used in the production of ammonia, methanol, and other chemicals. Hydrogen sensors are used to monitor the hydrogen concentration in these processes and to detect any leaks in the piping or equipment.
4. Hydrogen Storage Facilities
Hydrogen storage facilities are used to store large quantities of hydrogen gas for use in various applications. These facilities use hydrogen sensors to monitor the hydrogen concentration in the storage tanks and to detect any leaks in the piping or valves. This ensures the safe storage of hydrogen and prevents accidents.
5. Laboratories and Research Facilities
Laboratories and research facilities that work with hydrogen gas use hydrogen sensors to monitor the hydrogen concentration in the work area and to detect any leaks in the gas lines or equipment. This ensures the safety of the researchers and prevents accidents.
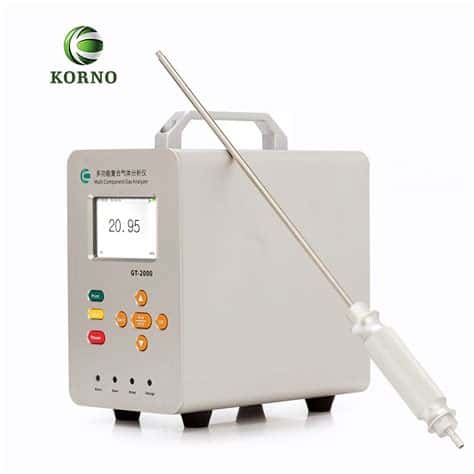
Choosing the Right Hydrogen Sensor
When choosing a hydrogen sensor for a particular application, there are several factors to consider:
-
Detection Range: The sensor should be able to detect hydrogen concentrations over the range required for the application. Different types of sensors have different detection ranges, so it’s important to choose a sensor that matches the expected hydrogen concentrations.
-
Selectivity: The sensor should be selective to hydrogen and not cross-sensitive to other gases that may be present in the application. Some sensors, such as electrochemical sensors, are highly selective to hydrogen, while others, such as MOS sensors, can be cross-sensitive to other reducing gases.
-
Response Time: The sensor should have a fast enough response time to detect hydrogen leaks or changes in concentration quickly. Some applications, such as fuel cell vehicles, require very fast response times to ensure safety.
-
Accuracy: The sensor should provide accurate measurements of hydrogen concentration over the required range. The accuracy required will depend on the application and the safety margins needed.
-
Environmental Conditions: The sensor should be able to operate reliably in the environmental conditions expected in the application. This includes factors such as temperature, humidity, pressure, and the presence of other gases or contaminants.
-
Power Consumption: The sensor should have a power consumption that is compatible with the available power supply in the application. Some sensors, such as MOS sensors, have relatively high power consumption due to their high operating temperature.
-
Cost: The cost of the sensor should be considered in relation to the overall cost of the application and the required performance. Some sensors, such as optical sensors, can be more expensive than others due to the cost of the optical components.
Here’s a table summarizing some of the key characteristics of the different types of hydrogen sensors:
Sensor Type | Detection Range | Selectivity | Response Time | Power Consumption | Cost |
---|---|---|---|---|---|
Catalytic | Up to 4% H2 | Moderate | Fast | Low | Low |
Electrochemical | ppm to 100% H2 | High | Fast | Moderate | Moderate |
MOS | ppm to 100% H2 | Moderate | Slow | High | Low |
Optical | ppm to 100% H2 | High | Fast | Moderate | High |
Frequently Asked Questions (FAQ)
1. What is the difference between a hydrogen sensor and a hydrogen detector?
A hydrogen sensor and a hydrogen detector are essentially the same things. Both terms refer to a device that can detect the presence of hydrogen gas and provide a measurable output signal. The term “sensor” is more commonly used in technical and industrial contexts, while “detector” is often used in more general or consumer-oriented applications.
2. Can a hydrogen sensor detect a hydrogen leak in a fuel cell vehicle?
Yes, hydrogen sensors are an essential safety feature in fuel cell vehicles. They are installed in various locations in the vehicle, such as near the hydrogen storage tanks and in the fuel cell stack compartment, to detect any leaks that may occur. If a leak is detected, the sensor will trigger an alarm and may also initiate safety measures, such as shutting down the fuel cell system and activating ventilation to disperse the hydrogen gas.
3. How often do hydrogen sensors need to be calibrated?
The calibration frequency for hydrogen sensors depends on the type of sensor and the application. Some sensors, such as electrochemical sensors, may require calibration every few months to ensure accurate readings. Other sensors, such as MOS sensors, may be more stable and require less frequent calibration. In general, it’s important to follow the manufacturer’s recommendations for calibration and to have a regular calibration schedule to ensure the reliability of the sensor.
4. Can hydrogen sensors be used in explosive atmospheres?
Yes, some hydrogen sensors are designed for use in explosive atmospheres. These sensors are typically certified as intrinsically safe, which means they are designed to prevent the ignition of flammable gases or vapors in the event of a fault or failure. Intrinsically safe sensors use low-power electronic circuits and are enclosed in flameproof housings to prevent the release of sparks or heat that could ignite an explosive atmosphere.
5. What is the typical lifespan of a hydrogen sensor?
The lifespan of a hydrogen sensor depends on the type of sensor and the application. Electrochemical sensors typically have a lifespan of 1-2 years, limited by the consumption of the electrolyte. MOS sensors and optical sensors can have longer lifespans, up to 5-10 years, as they do not have consumable components. However, the actual lifespan of a sensor can be affected by factors such as the operating environment, exposure to contaminants, and the frequency of calibration and maintenance. It’s important to follow the manufacturer’s recommendations for sensor replacement and to have a regular maintenance schedule to ensure the reliability of the sensor.
Conclusion
Hydrogen sensors are essential safety instruments in any application where hydrogen gas is used, stored, or transported. They provide early detection of hydrogen leaks and allow for the continuous monitoring of hydrogen concentrations to ensure safe operation. There are several types of hydrogen sensors available, each with its own advantages and limitations, and the choice of sensor depends on the specific requirements of the application.
As the use of hydrogen as a clean energy source continues to grow, the demand for reliable and accurate hydrogen sensors will also increase. Ongoing research and development in sensor technology will lead to improvements in sensor performance, reliability, and cost, making hydrogen sensors an even more valuable tool in the transition to a hydrogen-based economy.
By understanding the principles and applications of hydrogen sensors, and by choosing the right sensor for the job, we can ensure the safe and effective use of hydrogen in a wide range of industries and applications.
No responses yet