What is a Hydrogen Sensor?
A hydrogen sensor is a device designed to detect the presence of hydrogen gas in the surrounding environment. These sensors are capable of measuring hydrogen concentrations in the air and triggering an alarm or initiating safety measures when the gas level exceeds a predetermined threshold. Hydrogen sensors are essential for preventing accidents and ensuring the safe handling, storage, and use of hydrogen in various applications.
How Do Hydrogen Sensors Work?
Hydrogen sensors employ different detection principles depending on their type and intended use. Some common detection methods include:
-
Catalytic combustion: These sensors utilize a catalytic material that reacts with hydrogen, causing a temperature change that is measured and converted into an electrical signal.
-
Electrochemical: Electrochemical hydrogen sensors measure the current generated by the oxidation of hydrogen gas on a sensing electrode, which is proportional to the hydrogen concentration.
-
Semiconductor: Semiconductor-based hydrogen sensors rely on the change in electrical conductivity of a metal oxide semiconductor when exposed to hydrogen gas.
-
Thermal conductivity: These sensors measure the difference in thermal conductivity between hydrogen and a reference gas to determine the hydrogen concentration.
Detection Method | Principle | Advantages | Disadvantages |
---|---|---|---|
Catalytic combustion | Temperature change due to catalytic reaction | High sensitivity, wide detection range | Susceptible to poisoning, requires oxygen |
Electrochemical | Current generated by hydrogen oxidation | Low power consumption, good selectivity | Limited lifetime, sensitive to temperature |
Semiconductor | Change in electrical conductivity | Fast response, long lifetime | Cross-sensitivity to other gases |
Thermal conductivity | Difference in thermal conductivity | Simple design, no consumable parts | Low sensitivity, affected by environmental conditions |
Applications of Hydrogen Sensors
Hydrogen sensors find applications in various industries and settings where hydrogen is used, stored, or produced. Some key applications include:
Fuel Cell Systems
Hydrogen fuel cells are increasingly being used as a clean energy source in transportation, stationary power generation, and portable applications. Hydrogen sensors are crucial for monitoring hydrogen leaks and ensuring the safe operation of fuel cell systems.
Industrial Processes
Many industrial processes, such as petroleum refining, chemical manufacturing, and metallurgical operations, involve the use of hydrogen. Hydrogen sensors are employed to monitor hydrogen levels in these environments to prevent accidents and ensure worker safety.
Hydrogen Storage and Distribution
As hydrogen becomes more widely used as an energy carrier, its safe storage and distribution are paramount. Hydrogen sensors are used to monitor hydrogen levels in storage facilities, pipelines, and refueling stations to detect leaks and prevent accidents.
Automotive Industry
With the growing popularity of hydrogen fuel cell vehicles, hydrogen sensors play a vital role in ensuring the safety of passengers and the surrounding environment. These sensors are installed in the vehicle’s hydrogen storage and fuel cell systems to detect leaks and initiate safety measures.
Types of Hydrogen Sensors
There are several types of hydrogen sensors available, each with its own advantages and limitations. Some common types include:
Catalytic Combustion Sensors
Catalytic combustion sensors, also known as pellistor sensors, are widely used for detecting flammable gases, including hydrogen. These sensors consist of a catalytic bead coated with a noble metal catalyst, such as platinum or palladium. When exposed to hydrogen, the catalytic reaction generates heat, causing a change in the electrical resistance of the bead. This change in resistance is measured and converted into a hydrogen concentration reading.
Advantages:
– High sensitivity
– Wide detection range
– Relatively low cost
Limitations:
– Susceptible to catalyst poisoning by contaminants
– Requires the presence of oxygen for the catalytic reaction
– Consumes hydrogen during the detection process
Electrochemical Sensors
Electrochemical hydrogen sensors operate on the principle of electrochemical oxidation of hydrogen gas. These sensors consist of a sensing electrode, a counter electrode, and an electrolyte. When hydrogen gas comes into contact with the sensing electrode, it oxidizes, generating a current proportional to the hydrogen concentration. The current is then measured and converted into a hydrogen concentration reading.
Advantages:
– High selectivity towards hydrogen
– Low power consumption
– Good long-term stability
Limitations:
– Limited lifetime due to the consumption of the electrolyte
– Sensitive to temperature fluctuations
– Cross-sensitivity to other gases, such as carbon monoxide
Semiconductor Sensors
Semiconductor hydrogen sensors rely on the change in electrical conductivity of a metal oxide semiconductor, such as tin oxide or tungsten oxide, when exposed to hydrogen gas. These sensors consist of a sensing layer of metal oxide deposited on a substrate with electrodes. The interaction between hydrogen and the metal oxide causes a change in the sensor’s electrical resistance, which is measured and correlated to the hydrogen concentration.
Advantages:
– Fast response time
– Long lifetime
– Relatively low cost
Limitations:
– Cross-sensitivity to other reducing gases
– Sensitivity to humidity and temperature changes
– Requires a heating element to maintain the optimal operating temperature
Thermal Conductivity Sensors
Thermal conductivity hydrogen sensors measure the difference in thermal conductivity between hydrogen and a reference gas, typically air or nitrogen. These sensors consist of two elements: a sensing element exposed to the sample gas and a reference element exposed to the reference gas. The sensing element is heated, and the temperature difference between the two elements is measured. As hydrogen has a higher thermal conductivity than the reference gas, the presence of hydrogen causes a change in the temperature difference, which is used to determine the hydrogen concentration.
Advantages:
– Simple design
– No consumable parts
– Suitable for high hydrogen concentrations
Limitations:
– Low sensitivity compared to other sensor types
– Affected by changes in ambient temperature and pressure
– Cross-sensitivity to other gases with similar thermal conductivities
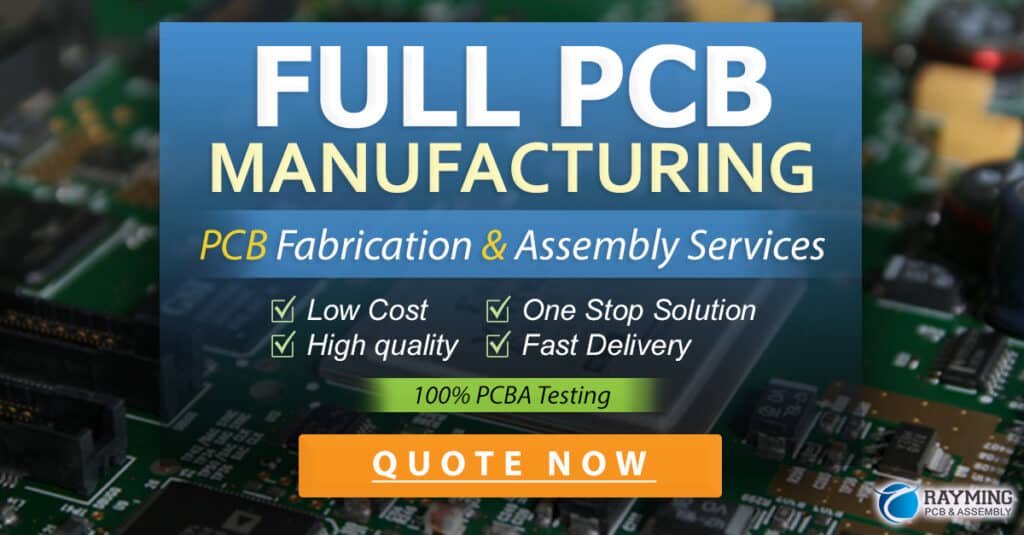
Factors to Consider When Choosing a Hydrogen Sensor
When selecting a hydrogen sensor for a specific application, several factors should be considered to ensure optimal performance and reliability:
-
Detection range: The sensor should be capable of detecting hydrogen concentrations within the expected range for the application.
-
Sensitivity: The sensor should have sufficient sensitivity to detect hydrogen at the required levels.
-
Response time: The sensor should have a fast response time to ensure timely detection and action in case of a hydrogen leak.
-
Selectivity: The sensor should be selective towards hydrogen and minimize cross-sensitivity to other gases present in the environment.
-
Operating environment: The sensor should be suitable for the specific operating conditions, such as temperature, humidity, and pressure.
-
Lifetime: The sensor should have a sufficient lifetime to minimize maintenance and replacement costs.
-
Power consumption: The sensor’s power consumption should be considered, especially for battery-powered or portable applications.
-
Cost: The cost of the sensor should be balanced against its performance and reliability requirements.
Calibration and Maintenance of Hydrogen Sensors
To ensure the accurate and reliable performance of hydrogen sensors, regular calibration and maintenance are essential. Calibration involves exposing the sensor to a known concentration of hydrogen and adjusting its output to match the reference value. The frequency of calibration depends on the sensor type, application, and manufacturer’s recommendations.
Maintenance of hydrogen sensors may include cleaning the sensor surface, replacing consumable components, such as electrolytes or filters, and checking for any physical damage. Regular maintenance helps to prolong the sensor’s life and maintain its accuracy.
Safety Considerations
When using hydrogen sensors, it is crucial to follow proper safety guidelines to minimize the risk of accidents and ensure the protection of personnel and equipment. Some key safety considerations include:
-
Proper installation: Hydrogen sensors should be installed in accordance with the manufacturer’s instructions and relevant safety standards.
-
Alarm settings: The alarm threshold should be set at an appropriate level to provide early warning of hydrogen leaks while minimizing false alarms.
-
Ventilation: Adequate ventilation should be provided in areas where hydrogen is used or stored to prevent the accumulation of the gas in case of a leak.
-
Explosion protection: In potentially explosive atmospheres, hydrogen sensors should be certified for use in such environments (e.g., intrinsically safe or explosion-proof).
-
Personal protective equipment: Personnel working with hydrogen should wear appropriate personal protective equipment, such as gas detectors, to ensure their safety.
Future Developments in Hydrogen Sensor Technology
As the demand for hydrogen as a clean energy source continues to grow, ongoing research and development efforts are focused on improving the performance, reliability, and cost-effectiveness of hydrogen sensors. Some areas of interest include:
-
Nanostructured materials: The use of nanostructured materials, such as nanowires and nanotubes, can enhance the sensitivity and response time of hydrogen sensors.
-
Wireless sensor networks: The development of wireless hydrogen sensor networks can enable remote monitoring and control of hydrogen systems, improving safety and efficiency.
-
Integration with IoT: The integration of hydrogen sensors with the Internet of Things (IoT) can facilitate real-time monitoring, data analysis, and predictive maintenance of hydrogen systems.
-
Advanced manufacturing techniques: The adoption of advanced manufacturing techniques, such as 3D printing and microfabrication, can enable the production of miniaturized, high-performance hydrogen sensors at lower costs.
FAQ
- What is the difference between a hydrogen sensor and a hydrogen detector?
-
A hydrogen sensor is a device that measures the concentration of hydrogen gas in the surrounding environment, while a hydrogen detector is a broader term that encompasses various devices, including sensors, that are used to detect the presence of hydrogen.
-
Can hydrogen sensors detect hydrogen leaks in fuel cell vehicles?
-
Yes, hydrogen sensors are an essential component in fuel cell vehicles for detecting hydrogen leaks in the storage and fuel cell systems. These sensors are strategically placed to monitor hydrogen levels and initiate safety measures in case of a leak.
-
How often should hydrogen sensors be calibrated?
-
The frequency of calibration depends on the sensor type, application, and manufacturer’s recommendations. In general, hydrogen sensors should be calibrated at least annually or more frequently if required by the specific application or regulatory standards.
-
Are hydrogen sensors expensive?
-
The cost of hydrogen sensors varies depending on the sensor type, performance, and features. While some advanced hydrogen sensors can be relatively expensive, there are also cost-effective options available for various applications. The cost should be balanced against the sensor’s performance and reliability requirements.
-
Can hydrogen sensors be used in potentially explosive atmospheres?
- Yes, hydrogen sensors can be used in potentially explosive atmospheres, but they must be certified for use in such environments. Intrinsically safe or explosion-proof hydrogen sensors are specifically designed to prevent the ignition of flammable gases in hazardous areas.
Conclusion
Hydrogen sensors play a crucial role in ensuring the safe and efficient use of hydrogen as a clean energy source. By detecting the presence of hydrogen gas in various industrial, commercial, and residential settings, these sensors help prevent accidents and protect personnel and equipment. With the growing demand for hydrogen, ongoing research and development efforts are focused on improving the performance, reliability, and cost-effectiveness of hydrogen sensors.
As the hydrogen economy continues to evolve, the importance of reliable hydrogen detection instruments will only increase. By understanding the fundamentals of hydrogen sensors, their types, applications, and safety considerations, stakeholders can make informed decisions when selecting and implementing these critical safety devices in their hydrogen-related projects and operations.
No responses yet