Introduction to Load Cells and HX711
Load cells are electromechanical transducers that convert force or weight into an electrical signal. They are widely used in various applications such as weighing scales, industrial automation, and robotics. Load cells come in different types, including Strain Gauge Load Cells, which are the most common. These load cells consist of a metal body with strain gauges attached to it. When a force is applied to the load cell, the strain gauges deform, causing a change in their electrical resistance. This change in resistance is proportional to the applied force and can be measured using a specialized amplifier circuit.
The HX711 is a popular load cell amplifier module that is commonly used with strain gauge load cells. It is designed to interface with microcontrollers such as Arduino, Raspberry Pi, and others, making it easy to integrate load cells into various projects. The HX711 module offers high precision and stability, with a 24-bit analog-to-digital converter (ADC) and a built-in low-pass filter to reduce noise.
How Load Cells Work
Load cells work on the principle of strain measurement. When a force is applied to a load cell, it causes the metal body to deform slightly. This deformation is measured by the strain gauges attached to the load cell. Strain gauges are thin, metallic foil patterns that are bonded to the load cell body. As the load cell deforms, the strain gauges also deform, causing a change in their electrical resistance.
Strain gauge load cells typically have four strain gauges arranged in a Wheatstone bridge configuration. This configuration allows for temperature compensation and provides a linear output signal. The Wheatstone bridge is excited with a constant voltage, and the output voltage varies proportionally to the applied force.
The output signal from the load cell is usually in the range of a few millivolts and requires amplification before it can be used by a microcontroller or other electronic devices. This is where the HX711 module comes into play.
HX711 Load Cell Amplifier
The HX711 is a precision 24-bit analog-to-digital converter (ADC) designed for weigh scales and industrial control applications. It is capable of interfacing directly with a bridge sensor, such as a load cell, and converting the sensor’s differential output into a digital value.
The HX711 module has the following key features:
- High precision: The HX711 has a 24-bit ADC, which provides a high resolution of up to 16,777,216 counts for a full-scale differential input signal.
- Selectable gain: The module allows for selectable gain settings of 128, 64, or 32, which corresponds to a full-scale differential input voltage of ±20mV, ±40mV, or ±80mV, respectively.
- On-chip active low-pass filter: The HX711 has a built-in active low-pass filter to reduce noise and improve stability.
- Simple interface: The module communicates with a microcontroller using a simple two-wire interface (data and clock).
- Low power consumption: The HX711 operates at a low supply voltage (2.6V to 5.5V) and consumes very little power, making it suitable for battery-powered applications.
Interfacing HX711 with a Microcontroller
To use the HX711 module with a microcontroller, you need to connect the module to the microcontroller using the two-wire interface. The HX711 module has the following pins:
- VCC: Power supply (2.6V to 5.5V)
- GND: Ground
- DT (Data): Serial data output
- SCK (Clock): Serial clock input
- RATE: Output data rate selection (10Hz or 80Hz)
Here’s a typical connection diagram for interfacing the HX711 with an Arduino:
HX711 Arduino
----- -------
VCC 5V
GND GND
DT Digital pin (e.g., 2)
SCK Digital pin (e.g., 3)
RATE GND (for 10Hz) or VCC (for 80Hz)
To communicate with the HX711 module, you can use a library such as the “HX711_ADC” library for Arduino. This library provides functions for initializing the module, reading raw data, and converting the raw data to weight units.
Here’s a simple example of how to use the HX711_ADC library to read data from a load cell:
#include <HX711_ADC.h>
const int DOUT_PIN = 2;
const int SCK_PIN = 3;
HX711_ADC loadCell(DOUT_PIN, SCK_PIN);
void setup() {
Serial.begin(9600);
loadCell.begin();
loadCell.start(2000); // Start the load cell with a stabilization time of 2000ms
loadCell.setCalFactor(1.0); // Calibration factor (adjust as needed)
}
void loop() {
if (loadCell.update()) {
float weight = loadCell.getData();
Serial.print("Weight: ");
Serial.print(weight, 3); // Print weight with 3 decimal places
Serial.println(" g");
}
}
In this example, the HX711_ADC library is used to initialize the HX711 module and read data from the connected load cell. The loadCell.update()
function checks if new data is available from the module, and if so, the loadCell.getData()
function retrieves the weight value in grams. The calibration factor (setCalFactor
) needs to be adjusted based on the specific load cell and the desired weight units.
Calibrating the Load Cell
To obtain accurate weight measurements from a load cell, it is essential to calibrate the system. Calibration involves determining the relationship between the load cell’s output signal and the actual weight applied to it. This relationship is represented by a calibration factor, which is used to convert the raw ADC values from the HX711 module into weight units.
There are two common methods for calibrating a load cell:
- Two-point calibration
- Single-point calibration
Two-Point Calibration
In two-point calibration, you measure the load cell’s output at two known weights, typically zero weight (no load) and a known reference weight. To perform two-point calibration:
- Connect the load cell to the HX711 module and the microcontroller.
- Ensure that there is no load on the load cell.
- Record the raw ADC value (zero offset) from the HX711 module.
- Place a known reference weight on the load cell.
- Record the raw ADC value corresponding to the reference weight.
- Calculate the calibration factor using the following formula:
calibration_factor = (reference_weight) / (ADC_value_with_weight - zero_offset)
Single-Point Calibration
Single-point calibration is a simplified method that assumes a linear relationship between the load cell’s output and the applied weight. In this method, you only need to measure the load cell’s output at a single known weight. To perform single-point calibration:
- Connect the load cell to the HX711 module and the microcontroller.
- Ensure that there is no load on the load cell.
- Record the raw ADC value (zero offset) from the HX711 module.
- Place a known reference weight on the load cell.
- Record the raw ADC value corresponding to the reference weight.
- Calculate the calibration factor using the following formula:
calibration_factor = (reference_weight) / (ADC_value_with_weight - zero_offset)
Once you have determined the calibration factor, you can use it to convert the raw ADC values from the HX711 module into weight units using the following formula:
weight = (ADC_value - zero_offset) * calibration_factor
It is important to note that the accuracy of the calibration depends on the precision of the reference weights used and the stability of the load cell system. To improve accuracy, you can use multiple reference weights and take an average of the calculated calibration factors.
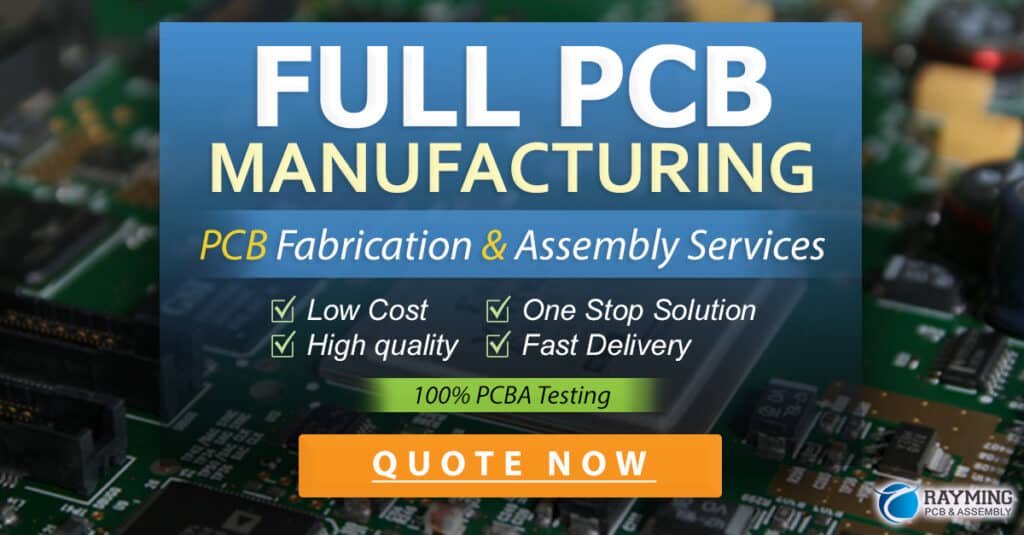
Design Considerations and Tips
When designing a load cell system using the HX711 module, there are several factors to consider and tips to keep in mind:
-
Load cell selection: Choose a load cell with an appropriate capacity and sensitivity for your application. Consider factors such as the maximum weight range, resolution, and environmental conditions (e.g., temperature, humidity).
-
Mechanical design: Ensure that the load cell is mounted securely and that the mechanical structure is rigid to minimize errors due to deflection or vibration. Use mounting hardware and load cell accessories (e.g., load buttons, load cell feet) as needed.
-
Wiring and connections: Use appropriate gauge wires for connecting the load cell to the HX711 module to minimize signal loss and noise. Keep the wires as short as possible and avoid routing them near sources of electromagnetic interference (EMI).
-
Shielding and grounding: Shield the load cell and HX711 module from external EMI sources using proper shielding techniques (e.g., metallic enclosures, shielded cables). Ensure that the system is properly grounded to reduce noise and improve stability.
-
Temperature compensation: Load cells are sensitive to temperature changes, which can affect their output. If your application involves significant temperature variations, consider using load cells with built-in temperature compensation or implement software-based temperature compensation techniques.
-
Overload protection: Protect the load cell from overloading by implementing mechanical stops or using load cells with built-in overload protection. Overloading can damage the load cell and affect its accuracy.
-
Filtering and averaging: To reduce noise and improve stability, implement digital filtering techniques (e.g., moving average filter) and data averaging in your software. The HX711 module has a built-in low-pass filter, but additional software filtering can further enhance the signal quality.
-
Calibration and validation: Regularly calibrate your load cell system using known reference weights to ensure accuracy. Validate the system’s performance by comparing its measurements with a trusted reference scale or known weights.
-
Power management: Consider the power requirements of your load cell system and ensure that the power supply is stable and free from noise. If using batteries, monitor their voltage levels and implement low-power techniques to extend battery life.
-
Error handling and diagnostics: Implement error handling and diagnostic features in your software to detect and handle abnormal conditions (e.g., overload, connection errors). Display error messages or use LEDs to indicate the system status.
By considering these design factors and following best practices, you can create a reliable and accurate load cell system using the HX711 module.
Troubleshooting Common Issues
When working with load cells and the HX711 module, you may encounter various issues that can affect the system’s performance. Here are some common problems and troubleshooting tips:
- Inaccurate readings:
- Check the load cell connections and ensure that the wires are securely connected and not damaged.
- Verify that the load cell is mounted properly and that there are no mechanical interferences or sources of friction.
- Recalibrate the load cell using known reference weights.
-
Check the HX711 module’s gain settings and ensure that they are appropriate for your load cell.
-
Unstable or fluctuating readings:
- Ensure that the load cell and HX711 module are properly grounded and shielded from external noise sources.
- Implement software filtering techniques (e.g., moving average filter) to smooth out the readings.
- Increase the sampling rate or averaging time to reduce the impact of noise.
-
Check for mechanical vibrations or disturbances that may affect the load cell’s output.
-
No output or communication errors:
- Double-check the wiring connections between the load cell, HX711 module, and microcontroller.
- Verify that the HX711 module is powered correctly and that the supply voltage is within the specified range.
- Check the data and clock pin connections and ensure that they are not swapped.
-
Review your code and ensure that the communication protocol and timing are implemented correctly.
-
Drifting or shifting zero point:
- Allow sufficient warm-up time for the load cell and HX711 module to stabilize before calibration and measurements.
- Implement auto-zero or tare functionality in your software to compensate for any drift over time.
-
Consider temperature compensation techniques if the drift is caused by temperature changes.
-
Limited resolution or sensitivity:
- Choose a load cell with a higher sensitivity or resolution if needed for your application.
- Adjust the HX711 module’s gain settings to optimize the resolution for your load cell.
-
Implement oversampling techniques to increase the effective resolution of the ADC.
-
Nonlinearity or hysteresis:
- Use load cells with better linearity specifications if required for your application.
- Implement linearization techniques in your software to compensate for any nonlinearity.
- Ensure that the load cell is not subjected to excessive or prolonged overloading, which can cause hysteresis effects.
When troubleshooting issues with your load cell system, it is important to approach the problem systematically. Start by verifying the hardware connections and mechanical setup, then move on to reviewing the software and calibration procedures. Use diagnostic tools (e.g., serial monitor, oscilloscope) to monitor the system’s behavior and identify any anomalies.
If the issue persists, consult the load cell and HX711 module datasheets, application notes, and online resources for additional guidance and support. Engaging with the community on forums and discussion groups can also provide valuable insights and solutions from experienced users.
Load Cell and HX711 Applications
Load cells and the HX711 module find applications in a wide range of industries and projects. Here are some common use cases:
- Weighing scales:
- Digital kitchen scales
- Postal and shipping scales
- Jewelry scales
-
Laboratory balances
-
Industrial automation:
- Conveyor belt weighing systems
- Batch weighing and filling machines
- Inventory management systems
-
Quality control and inspection stations
-
Agricultural and food processing:
- Grain and produce weighing
- Livestock monitoring and feeding systems
- Food packaging and portioning machines
-
Ingredient batching and mixing systems
-
Medical and healthcare:
- Patient weighing scales
- Dosage and dispensing systems
- Biomechanical force measurement
-
Prosthetic and orthotic devices
-
Automotive and transportation:
- Vehicle weight monitoring systems
- Cargo and freight weighing
- Tire pressure monitoring systems
-
Suspension and braking force measurement
-
Robotics and mechatronics:
- Force and torque sensors for robotic manipulators
- Tactile sensors for robotic grippers
- Balance and stability control systems
-
Human-robot interaction and collaboration
-
Home automation and IoT:
- Smart bathroom scales
- Inventory tracking systems
- Pet feeders and monitoring devices
- DIY projects and hobby applications
These are just a few examples of the diverse applications where load cells and the HX711 module can be employed. The versatility and precision offered by these components make them valuable tools in fields ranging from industrial automation to consumer electronics.
When designing a load cell system for a specific application, consider factors such as the required measurement range, resolution, response time, environmental conditions, and integration with other components or systems. Tailor the hardware and software design to meet the specific requirements and constraints of your project.
As you explore new applications and push the boundaries of load cell technology, stay informed about the latest advancements, best practices, and community resources. Collaborate with experts, share your experiences, and learn from others to create innovative and impactful solutions using load cells and the HX711 module.
Frequently Asked Questions (FAQ)
- What is the maximum weight capacity of a load cell that can be used with the HX711 module?
-
The maximum weight capacity depends on the specific load cell used. Load cells are available in various capacities, ranging from a few grams to several tons. The HX711 module itself does not limit the weight capacity but rather amplifies the load cell’s output signal. Choose a load cell with a capacity suitable for your application requirements.
-
Can I use multiple load cells with a single HX711 module?
-
Yes, it is possible to use multiple load cells with a single HX711 module by connecting them in parallel or series, depending on your requirements. When using multiple load cells, ensure that the total output signal is within the HX711’s input range and that the load cells are properly balanced and calibrated.
-
How do I convert the HX711 module’s raw ADC values to weight units?
-
To convert the raw ADC values to weight units, you need to calibrate the load cell system using known reference weights. Determine the calibration factor by measuring the ADC values at two or more known weights and calculating the factor using the formulas provided in the calibration section. Once you have the calibration factor, you can multiply it with the difference between the current ADC value and the zero offset to obtain the weight in your desired units.
-
What is the resolution of the HX711 module?
- The HX711 module has a 24-bit analog-to-digital converter (ADC), which provides a resolution of up to 16,
No responses yet