Troubleshooting Schematic Capture Issues
Components Not Showing Up in Libraries
If you can’t find a component you need in the EasyEDA libraries, try the following:
- Make sure you are searching in the correct library. EasyEDA has separate libraries for different component categories.
- Search for alternative names or variations of the component. The naming may differ from what you are used to.
- Use the “Search in All Libraries” option to do a broad search across all available component libraries.
- As a last resort, you can create a custom schematic symbol for the component yourself.
Wires or Connections Not Routing Properly
Incorrect or incomplete wire connections in the schematic can lead to problems. Here are some things to check:
- Make sure you are connecting component pins using wires, not just placing them next to each other. Wires need to physically touch the pin targets.
- Check that connection dots appear where wires intersect and connect. Wires that cross without a connection dot are not actually connected.
- For multi-part components like chips, double-check that all the part sections are wired correctly with no dangling pins.
- Verify that power and ground nets are connected as intended throughout the schematic.
Handling Missing or Outdated Models
Sometimes schematic components may be missing simulation models or have outdated models. In these cases:
- Check if there is an updated model available in the EasyEDA libraries or component forum.
- See if you can find a compatible SPICE model online to import into EasyEDA.
- If necessary, you can create a custom symbol with a generic model or one from a similar component as a stand-in for simulation purposes.
Solving Simulation Problems
Convergence Errors or Simulation Failures
Non-convergence errors are a common issue in circuit simulation. To address this:
- Make sure the circuit is wired correctly without any accidental shorts or disconnected nodes.
- Check component values and models for any errors or extreme/unrealistic values.
- Add/adjust convergence aids like series resistors or RC snubbers to improve SPICE solver convergence.
- Simplify the circuit and simulate individual stages separately to isolate problems.
Incorrect or Unexpected Simulation Results
If the simulation runs but the results seem wrong, consider the following:
- Double-check all the component values, models and wiring for mistakes. A wrong value or connection can dramatically change the behavior.
- Make sure you are probing the correct test points and interpreting the waveforms correctly.
- Validate your expectations against hand calculations or simulations in other tools. The problem may be with your design rather than the simulator.
- Simulate with different analysis types and settings to cross-verify the results.
Dealing with Slow Simulation Speeds
Simulations bogging down and taking a long time to run can be frustrating. Some speed-up options include:
- Simplify the circuit as much as possible to reduce the size of the matrices the simulator has to solve.
- Choose the most appropriate simulation type for your analysis needs. Transient is often the slowest.
- Avoid using excessively long simulation times or small time steps unless absolutely necessary.
- Limit the amount of high-frequency content by filtering fast edges and removing unneeded parasitics.
Overcoming PCB Layout Challenges
Component Placement and Routing Struggles
Figuring out the optimal component placement and routing strategy can be tricky. A few tips:
- Put the critical components like ICs first and build the placement around them.
- Partition the board into functional blocks and place related components together.
- Minimize connection distances, prioritizing high-speed and sensitive signals.
- Route power and ground nets first using planes and wide traces.
- Use the autorouter for less critical nets after routing priority traces manually.
Footprint Mismatches or Availability Issues
PCB footprints need to exactly match the components to avoid assembly problems. If you encounter footprint mismatches:
- Double-check the component datasheets and dimensions to verify you have the right footprint.
- See if there is an alternative footprint available in the EasyEDA PCB libraries.
- Search for the footprint in external libraries or online forums to import into EasyEDA.
- Create a custom footprint based on the mechanical drawing if no ready-made match is found.
Dealing with Electrical Rule Check (ERC) Errors
ERC helps catch common PCB design rule violations. To resolve ERC errors:
- Carefully review each error and determine if it is a true violation or a false/acceptable one.
- Adjust trace spacing, widths, and via sizes to satisfy clearance and current density limits.
- Rerooute or move components as needed to eliminate any overlap or violation markers.
- Waive specific ERC rules if violations are known and intentional (with caution).
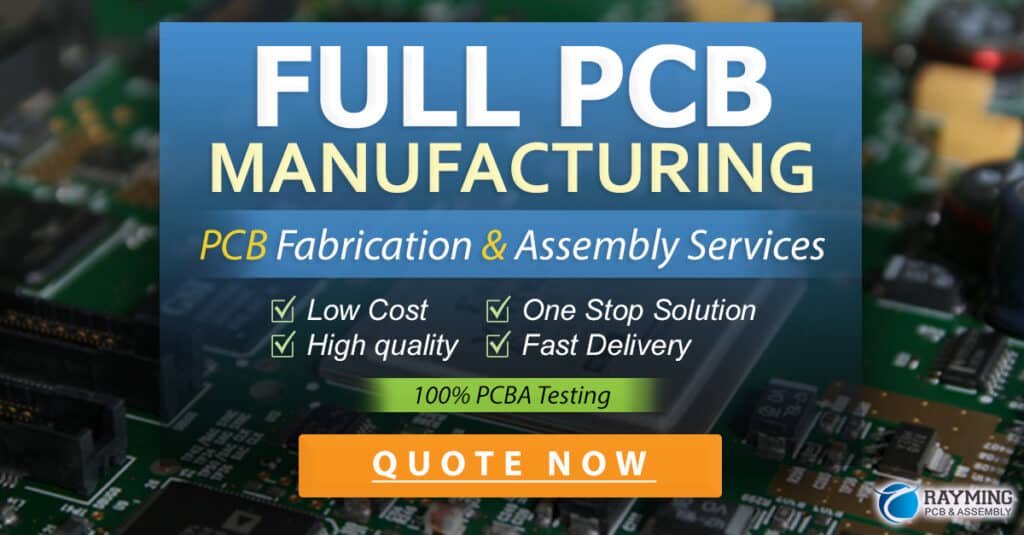
Manufacturing and Assembly Considerations
Generating Proper Manufacturing Outputs
To avoid production delays or issues, make sure you provide the fab and assembly houses with the necessary outputs:
- Generate Gerber files covering all the needed copper, mask, silk, and drill layers.
- Provide drill files, centroid files, and pick & place files in the required formats.
- Include detailed fabrication and assembly drawings with all the key parameters specified.
- Communicate clearly with the fab and assembly teams to understand their requirements.
Panelization and Breakout Routing
Panelizing multiple copies of a PCB design can save cost but requires some additional steps:
- Decide on the optimal panel size and number of copies based on the vendor’s capabilities.
- Add breakout tabs, rails, and tooling features according to the fab’s specifications.
- Verify that the panelized design still passes ERC and DRC checks.
- Generate manufacturing outputs for the entire panel, not just the individual PCB copies.
Design for Manufacturing (DFM) Best Practices
Following some basic DFM guidelines can improve yields and reduce assembly defects:
- Use standard component sizes, pitches and packaging wherever possible.
- Provide adequate spacing and clearances around components and traces.
- Minimize the use of vias, especially blind and buried types.
- Prefer surface mount over through-hole components for easier assembly.
- Add fiducials, test points, and other assembly aid features to the PCB.
Frequently Asked Questions (FAQ)
Q: What should I do if I can’t find a component I need in the EasyEDA libraries?
A: First, try searching for the component under different names or categories. If that doesn’t work, you can create a custom schematic symbol and PCB footprint for the component based on its datasheet. You can also request the component on the EasyEDA forums or import it from an external library.
Q: How can I speed up my simulations when they are taking too long to run?
A: There are a few things you can try to speed up simulations:
1. Simplify the circuit schematic by removing unnecessary components and complexities.
2. Choose the most appropriate simulation type and analysis settings for your needs.
3. Avoid using overly long simulation times or small step sizes unless required.
4. Limit high-frequency content and parasitics that can slow down the simulator.
Q: What should I do if I encounter ERC errors in my PCB layout?
A: Electrical Rule Check (ERC) errors indicate potential issues with your PCB design. To resolve them:
1. Review each error and determine if it is a true violation or an acceptable/false one.
2. Adjust trace widths, clearances, and via sizes to satisfy spacing and current rules.
3. Move components or re-route traces to eliminate overlap and violation markers.
4. Waive specific ERC rules only if the violations are known and intentional.
Q: How do I generate the necessary manufacturing files for PCB fabrication and assembly?
A: To create manufacturing outputs in EasyEDA:
1. Go to the “Fabrication Output” menu and select “PCB Fabrication Output” to generate Gerber files, drill files, and drawings.
2. Use the “Generate Pick and Place File” and “Generate BOM” options for assembly outputs.
3. Specify all the required parameters like copper weights, finishes, and solder mask colors.
4. Communicate with your fab and assembly houses to ensure you are providing files in the formats they need.
Q: What are some best practices to follow for design for manufacturing (DFM)?
A: Some key DFM guidelines include:
1. Use standard component packages, sizes, and pitches as much as possible.
2. Provide sufficient clearances and spacing around components and traces.
3. Minimize the number of vias and avoid blind/buried types if you can.
4. Prefer surface mount devices (SMD) over through-hole for ease of assembly.
5. Include fiducials, tooling holes, and other assembly aid features in the PCB design.
By following the troubleshooting tips and solutions outlined in this article, you should be able to overcome many common issues and challenges in EasyEDA. As you gain more experience with the tool and design process, you will develop an intuition for how to tackle different problems that may arise. Don’t hesitate to consult the EasyEDA documentation, forums, and community for further assistance and advice. With practice and persistence, you can master the art of electronics design with EasyEDA.
No responses yet