Introduction to PID Temperature Controllers
A PID (Proportional-Integral-Derivative) temperature controller is a crucial component in various industrial and home applications that require precise temperature control. These controllers use a feedback loop to maintain the desired temperature by continuously adjusting the heating or cooling element based on the difference between the measured and set temperature.
What is a PID Controller?
A PID controller is a control loop mechanism that calculates an error value as the difference between a measured process variable (PV) and a desired setpoint (SP). The controller attempts to minimize the error over time by adjusting a control variable (CV), such as the power supplied to a heating element.
The three components of a PID controller are:
-
Proportional (P): The proportional term produces an output value that is proportional to the current error value. A high proportional gain results in a large change in the output for a given change in the error.
-
Integral (I): The integral term sums the error over time and provides a corrective action to eliminate the steady-state error.
-
Derivative (D): The derivative term determines the rate of change of the error and provides a corrective action to reduce the rate of change of the error.
Applications of PID Temperature Controllers
PID temperature controllers find applications in various fields, including:
- Industrial processes (e.g., chemical manufacturing, food processing)
- HVAC systems
- 3D printing
- Homebrewing and fermentation
- Aquariums and terrariums
Components Required for Setting Up a PID Temperature Controller
To set up a PID temperature controller, you will need the following components:
-
Temperature sensor: A device that measures the current temperature of the system. Common types include thermocouples, RTDs (Resistance Temperature Detectors), and thermistors.
-
Heating or cooling element: The device responsible for adjusting the temperature of the system based on the controller’s output. Examples include heating pads, Peltier modules, and refrigeration units.
-
PID controller: The brain of the system that processes the temperature sensor’s input and controls the heating or cooling element. You can use a dedicated PID controller or a microcontroller (e.g., Arduino, Raspberry Pi) programmed with PID control algorithms.
-
Power supply: A source of electrical power for the PID controller, temperature sensor, and heating or cooling element. Ensure that the power supply is compatible with your components’ voltage and current requirements.
-
Wiring and connectors: Necessary for connecting the components and creating a complete circuit.
-
Enclosure (optional): A protective housing for the PID controller and other components to prevent damage and ensure safe operation.
Step-by-Step Guide to Setting Up Your PID Temperature Controller
Step 1: Choose and Connect the Temperature Sensor
Select a temperature sensor suitable for your application’s temperature range and accuracy requirements. Follow these steps to connect the sensor to your PID controller:
-
Identify the sensor’s pin configuration (e.g., positive, negative, and signal pins for thermocouples; Vcc, ground, and signal pins for thermistors and RTDs).
-
Connect the sensor to the appropriate input pins on the PID controller. Refer to the controller’s documentation for the correct pin assignments.
-
If using a thermocouple, ensure that you use a compatible extension wire and consider cold junction compensation for accurate readings.
Step 2: Set Up the Heating or Cooling Element
Choose a heating or cooling element that can efficiently control the temperature of your system. Follow these steps to set up the element:
-
Determine the power requirements of your heating or cooling element and ensure that your power supply can provide sufficient voltage and current.
-
Connect the heating or cooling element to the PID controller’s output pins. Refer to the controller’s documentation for the correct pin assignments.
-
If the heating or cooling element draws a large current, use a relay or solid-state relay (SSR) to switch the power to the element. Connect the relay’s coil to the PID controller’s output and the heating or cooling element to the relay’s contacts.
Step 3: Configure the PID Controller
Program or configure your PID controller according to your system’s requirements. Follow these steps:
-
If using a dedicated PID controller, refer to the manufacturer’s instructions for setting the temperature setpoint, PID parameters (Kp, Ki, Kd), and other relevant settings.
-
If using a microcontroller, upload a PID control sketch or program to the board. Many open-source libraries, such as the Arduino PID Library, are available to simplify this process. Set the temperature setpoint and PID parameters in the code.
-
Tune the PID parameters to achieve optimal temperature control. Start with a low proportional gain (Kp) and gradually increase it until the system starts to oscillate. Then, introduce a small integral gain (Ki) to eliminate steady-state error. Finally, add a small derivative gain (Kd) to reduce overshoot and improve response time. Fine-tune these parameters through trial and error until the system maintains the desired temperature with minimal overshoot and oscillation.
Step 4: Power Up and Test the System
-
Double-check all connections to ensure that they are secure and correctly wired.
-
Power up the PID controller and the heating or cooling element.
-
Monitor the system’s temperature using the PID controller’s display or by connecting it to a computer for data logging.
-
Observe the system’s response to changes in the setpoint temperature and external disturbances. Make further adjustments to the PID parameters if necessary.
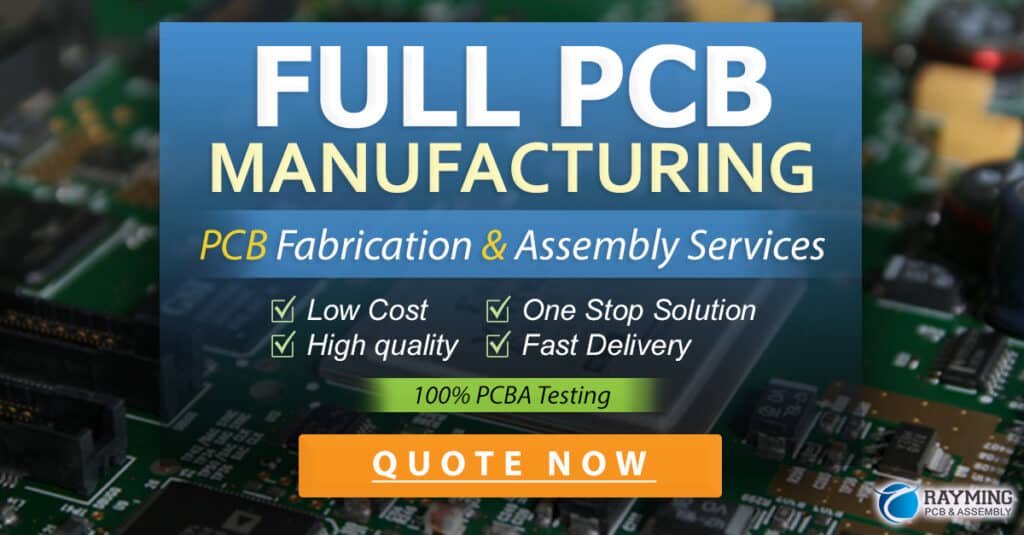
Tips for Optimizing Your PID Temperature Controller
-
Properly place the temperature sensor: Ensure that the temperature sensor is placed close to the area where you want to control the temperature. Avoid placing the sensor near heat sources or cold spots that may affect its readings.
-
Use insulation: Minimize heat loss or gain from the environment by insulating your system. This will help the PID controller maintain the desired temperature more efficiently.
-
Implement a low-pass filter: If the temperature sensor’s readings are noisy, consider implementing a low-pass filter in your PID controller’s code to smooth out the input signal. This can help prevent the controller from overreacting to short-term fluctuations.
-
Set appropriate PID parameters: Properly tuned PID parameters are crucial for optimal temperature control. Take the time to experiment with different values and observe the system’s response to find the best settings for your application.
-
Monitor and log data: Regularly monitor your PID temperature controller’s performance and log temperature data over time. This will help you identify any issues or areas for improvement, as well as ensure that your system is maintaining the desired temperature consistently.
Troubleshooting Common Issues
-
Temperature oscillations: If the temperature oscillates around the setpoint, the proportional gain (Kp) may be too high. Reduce Kp and increase the integral gain (Ki) to stabilize the system.
-
Slow response time: If the system takes too long to reach the setpoint temperature, increase the proportional gain (Kp) and/or the integral gain (Ki). Be cautious not to set these values too high, as it may lead to overshoot and oscillations.
-
Overshoot: If the temperature overshoots the setpoint and then oscillates, the derivative gain (Kd) may be too low. Increase Kd to dampen the system’s response and reduce overshoot.
-
Sensor inaccuracy: If the temperature readings seem inconsistent or inaccurate, check the sensor’s connections and ensure that it is properly calibrated. Replace the sensor if necessary.
-
Heating or cooling element failure: If the temperature does not change despite the PID controller’s output, check the heating or cooling element for any signs of damage or malfunction. Ensure that it is properly connected and receiving power. Replace the element if needed.
FAQ
-
Can I use a PID temperature controller for both heating and cooling applications?
Yes, a PID temperature controller can be used for both heating and cooling applications. However, you will need to set up the appropriate heating or cooling element and ensure that the PID controller is configured to output the correct control signal for your application. -
How do I choose the right temperature sensor for my PID controller?
When selecting a temperature sensor for your PID controller, consider factors such as the temperature range, accuracy, response time, and compatibility with your controller. Thermocouples, RTDs, and thermistors are common choices, each with their own advantages and limitations. Choose a sensor that best suits your application’s requirements and budget. -
What is the difference between a PID controller and an on/off controller?
An on/off controller simply switches the heating or cooling element on or off based on a temperature threshold. This can result in large temperature fluctuations and poor control. In contrast, a PID controller continuously adjusts the output to the heating or cooling element based on the difference between the measured and set temperature, providing more precise and stable temperature control. -
How often should I tune my PID controller?
The frequency of tuning your PID controller depends on the stability of your system and the consistency of its performance. If your system’s temperature control is satisfactory and the environment remains relatively constant, you may not need to tune the controller frequently. However, if you notice a decline in performance or change in the system’s behavior, it may be time to re-tune the PID parameters. -
Can I control multiple temperature zones with a single PID controller?
While it is possible to control multiple temperature zones with a single PID controller, it is generally recommended to use a separate controller for each zone. This allows for more precise control and easier troubleshooting, as each zone may have different thermal characteristics and requirements. If you must use a single controller for multiple zones, ensure that the controller has multiple input and output channels and that the PID parameters are tuned separately for each zone.
Conclusion
Setting up a PID temperature controller can greatly enhance the precision and stability of temperature control in various applications. By following this step-by-step guide and understanding the principles behind PID control, you can create a reliable and efficient temperature control system tailored to your specific needs. Remember to choose compatible components, properly configure your PID controller, and regularly monitor and maintain your system for optimal performance.
No responses yet