Understanding ESD and its Impact on SMT Assembly
Electrostatic discharge (ESD) is a common phenomenon that occurs when two objects with different electrical charges come into contact or proximity with each other. In the context of surface mount technology (SMT) assembly, ESD can cause significant damage to sensitive electronic components, leading to reduced product quality, increased failure rates, and costly rework. To minimize the risk of ESD damage in SMT assembly, it is essential to understand the causes, effects, and prevention methods.
What is ESD?
ESD is the sudden flow of electricity between two objects with different electrical potentials. It can occur when a charged object comes into contact with a conductive surface or when a charged object is brought close to another object, causing a rapid transfer of electrons. The intensity of an ESD event depends on factors such as the voltage difference, the distance between the objects, and the humidity level in the environment.
Impact of ESD on SMT Components
SMT components, such as integrated circuits (ICs), transistors, and capacitors, are particularly vulnerable to ESD damage due to their small size and sensitive internal structures. When exposed to an ESD event, these components can suffer from various types of damage, including:
- Oxide breakdown: The thin oxide layers in IC devices can be punctured by high-voltage ESD, causing permanent damage to the component.
- Junction damage: ESD can cause localized melting or vaporization of the semiconductor material at the p-n junctions, leading to short circuits or open circuits.
- Latch-up: In some cases, ESD can trigger a high-current state called latch-up, which can cause the component to fail or even destroy itself.
The consequences of ESD damage in SMT assembly can range from immediate component failure to latent defects that may manifest themselves later during product use. This can lead to increased warranty claims, reduced customer satisfaction, and damage to the manufacturer’s reputation.
ESD Prevention in SMT Assembly
To minimize the risk of ESD damage in SMT assembly, a comprehensive ESD prevention program should be implemented. This program should include a combination of engineering controls, administrative controls, and personal protective equipment (PPE).
ESD-Safe Workstations
One of the most effective ways to prevent ESD damage in SMT assembly is to establish ESD-safe workstations. These workstations should be designed to dissipate static charges and provide a safe environment for handling sensitive components. Key elements of an ESD-safe workstation include:
- Conductive work surfaces: Work surfaces should be made of conductive materials, such as stainless steel or carbon-filled laminate, to allow static charges to dissipate safely.
- Grounding: All conductive surfaces, including the operator, should be properly grounded to a common ground point using grounding wrist straps, heel straps, or conductive flooring.
- Ionizers: Air ionizers can be used to neutralize static charges in the workspace by generating balanced positive and negative ions.
- Shielding: Sensitive components should be stored and transported in ESD-shielding containers, such as static-dissipative bags or conductive foam.
ESD-Safe Material Handling
Proper handling of materials is crucial in preventing ESD damage during SMT assembly. Some best practices for ESD-safe material handling include:
- Handling components only at ESD-safe workstations.
- Using ESD-safe tools, such as conductive tweezers and vacuum pens, when handling sensitive components.
- Avoiding contact with component leads or pins, as this can cause ESD damage.
- Storing components in ESD-shielding containers when not in use.
- Minimizing the use of non-conductive materials, such as paper or plastic, in the workspace.
Material | ESD-Safe Alternative |
---|---|
Plastic trays | Conductive or static-dissipative trays |
Styrofoam | Conductive foam |
Regular tape | ESD-safe tape |
Plastic bags | Static-shielding bags |
Personnel Training and Compliance
ESD prevention in SMT assembly relies heavily on the proper training and compliance of personnel. All employees involved in handling sensitive components should receive comprehensive ESD training, which should cover topics such as:
- Understanding ESD and its impact on electronic components.
- Recognizing ESD-safe workstations and equipment.
- Proper handling and storage of sensitive components.
- The importance of personal grounding and the use of ESD-safe PPE.
- Reporting and addressing ESD-related issues in the workplace.
Regular audits and refresher training should be conducted to ensure ongoing compliance with ESD prevention protocols.
ESD Monitoring and Testing
To ensure the effectiveness of an ESD prevention program, regular monitoring and testing should be performed. This can include:
- Resistance testing of grounding equipment, such as wrist straps and work surfaces, to ensure proper functioning.
- Voltage monitoring using static field meters to identify areas with high static charge levels.
- Periodic testing of ESD-sensitive components to assess their vulnerability to ESD events.
- Investigating and addressing any ESD-related failures or customer complaints.
By continuously monitoring and improving ESD prevention measures, SMT assembly processes can be optimized to minimize the risk of ESD damage and ensure high product quality.
Best Practices for ESD Prevention in SMT Assembly
Implementing a comprehensive ESD prevention program in SMT assembly requires a combination of best practices across various aspects of the manufacturing process. Some key best practices include:
- Establishing a well-defined ESD control plan that outlines the specific measures, responsibilities, and procedures for preventing ESD damage.
- Regularly training and certifying personnel in ESD prevention techniques and protocols.
- Implementing a strict compliance monitoring system to ensure adherence to ESD prevention guidelines.
- Investing in high-quality ESD-safe equipment, such as grounding systems, ionizers, and shielding materials.
- Maintaining a clean and organized workspace to minimize the accumulation of static charges.
- Conducting regular audits and assessments of the ESD prevention program to identify areas for improvement.
- Staying up-to-date with the latest industry standards and best practices for ESD prevention, such as the ANSI/ESD S20.20 standard.
By adopting these best practices, SMT assembly processes can significantly reduce the risk of ESD damage, leading to improved product quality, reduced failure rates, and increased customer satisfaction.
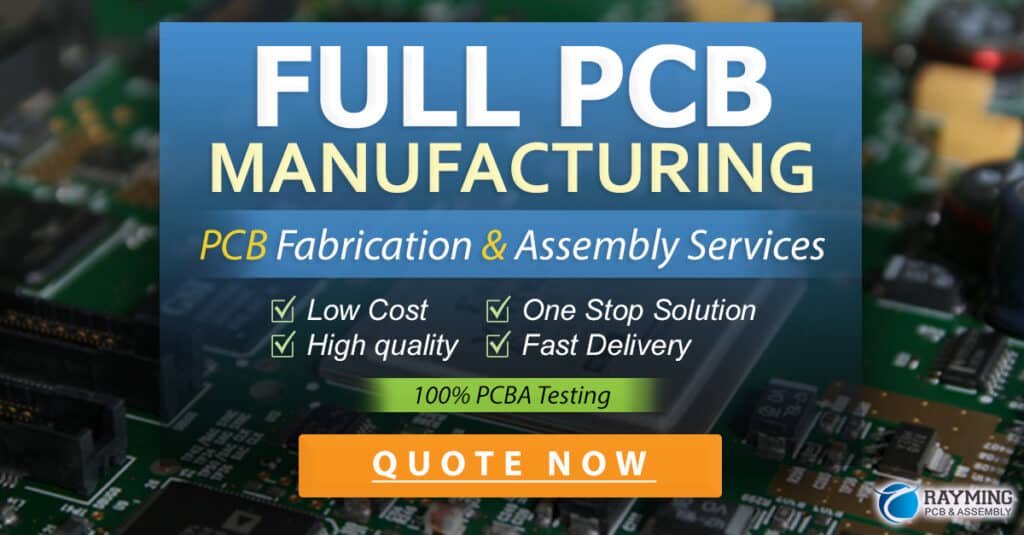
Frequently Asked Questions (FAQ)
1. What is the most common cause of ESD damage in SMT assembly?
The most common cause of ESD damage in SMT assembly is improper handling of sensitive components. This can occur when personnel are not properly grounded, when components are not stored in ESD-safe containers, or when non-ESD-safe tools and materials are used in the assembly process.
2. How can I tell if a component has suffered ESD damage?
ESD damage can be difficult to detect, as it may not always result in immediate component failure. Some signs of ESD damage include visible damage to component packages, altered electrical characteristics, or increased failure rates during testing or in the field. In some cases, specialized equipment, such as scanning electron microscopes, may be needed to confirm ESD damage.
3. Are all electronic components equally susceptible to ESD damage?
No, different types of electronic components have varying levels of sensitivity to ESD. In general, components with smaller geometries and higher pin counts, such as modern ICs, are more susceptible to ESD damage than larger, simpler components. However, it is essential to treat all components as ESD-sensitive to ensure a comprehensive ESD prevention approach.
4. Can ESD damage occur even if I can’t feel a static discharge?
Yes, ESD damage can occur even when the static discharge is not perceptible to human senses. In fact, many ESD events that cause damage to electronic components are below the human perception threshold, which is typically around 3,000 volts. This is why it is crucial to implement ESD prevention measures regardless of whether static discharge is felt or not.
5. How often should I replace my ESD-safe equipment, such as grounding wrist straps?
The lifespan of ESD-safe equipment varies depending on factors such as usage frequency, storage conditions, and maintenance. In general, grounding wrist straps should be tested daily before use and replaced if they fail the resistance test or show signs of wear and tear. Other equipment, such as work surface mats and ionizers, should be tested and replaced according to the manufacturer’s recommendations or industry standards. Regular maintenance and testing can help extend the life of ESD-safe equipment and ensure ongoing effectiveness in preventing ESD damage.
Conclusion
ESD prevention is a critical aspect of ensuring high-quality, reliable SMT assembly. By understanding the causes and effects of ESD, implementing comprehensive prevention measures, and adopting industry best practices, manufacturers can significantly reduce the risk of ESD damage to sensitive electronic components. A well-designed ESD prevention program, combined with regular training, monitoring, and continuous improvement, can lead to increased product quality, reduced failure rates, and enhanced customer satisfaction in the competitive world of electronics manufacturing.
No responses yet