What is PCB Etching?
PCB etching is a process of removing unwanted copper from a copper-clad board to create conductive traces that form the desired circuit pattern. The process involves applying a resist layer to the copper surface, exposing it to UV light through a mask that defines the circuit pattern, and then using an etchant solution to remove the unprotected copper areas.
Advantages of PCB Etching
- Cost-effective for small-scale production or prototyping
- Allows for customization and flexibility in circuit design
- Can be done with readily available materials and tools
Materials and Tools Required
Before you begin the PCB etching process, you need to gather the necessary materials and tools. Here’s a list of what you’ll need:
Material/Tool | Purpose |
---|---|
Copper-clad board | The base material for the PCB |
Photoresist film or paint | Protects the desired copper areas from etching |
UV exposure unit or sunlight | Exposes the photoresist to harden it |
Transparency film | Used to create the circuit pattern mask |
Laser printer or photoplotter | Prints the circuit pattern onto the transparency film |
Etchant solution | Removes the unprotected copper areas |
Plastic container | Holds the etchant solution during etching |
Rubber gloves and safety goggles | Provides protection while handling chemicals |
Drill or hole punch | Creates holes for component leads |
Scissors or utility knife | Cuts the copper-clad board to size |
Sandpaper or abrasive pad | Cleans and roughens the copper surface |
Step 1: Designing the Circuit
The first step in making an etching PCB is to design the circuit using PCB design software or by hand. When designing the circuit, consider the following factors:
- Component placement and orientation
- Trace width and spacing
- Power and ground planes
- Connectors and mounting holes
Once you have finalized the circuit design, export it as a high-resolution image file (preferably in black and white) that will be used to create the mask.
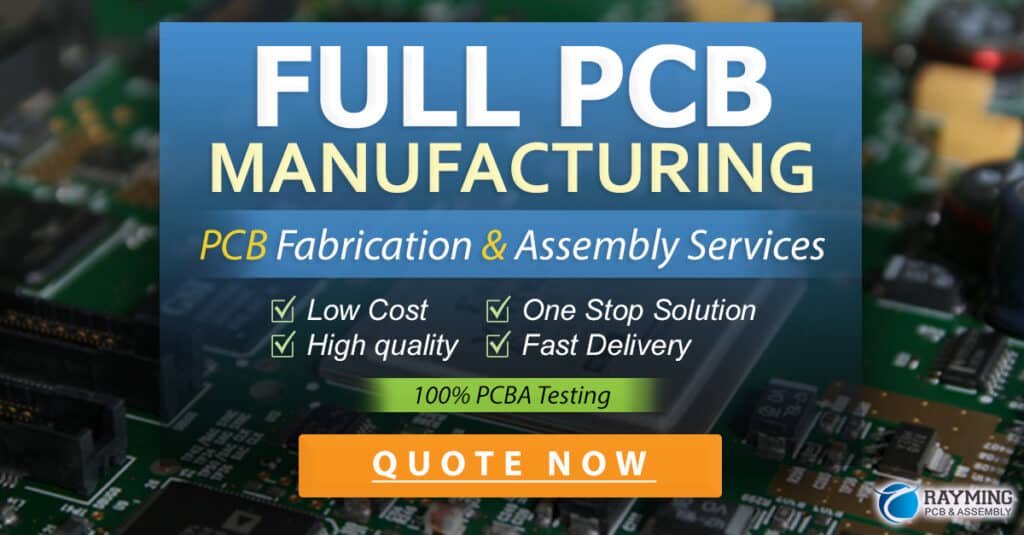
Step 2: Preparing the Copper-Clad Board
Before applying the photoresist, the copper-clad board needs to be prepared. Follow these steps:
- Cut the copper-clad board to the desired size using scissors or a utility knife.
- Clean the copper surface with sandpaper or an abrasive pad to remove any oxidation and roughen the surface for better photoresist adhesion.
- Avoid touching the cleaned copper surface with your bare hands to prevent contamination.
Step 3: Applying the Photoresist
There are two common methods for applying photoresist to the copper-clad board:
Method 1: Photoresist Film
- Cut a piece of photoresist film slightly larger than the copper-clad board.
- Remove the protective backing from the film and carefully place it onto the copper surface, ensuring there are no air bubbles.
- Use a laminator or a household iron (set to medium heat without steam) to firmly adhere the photoresist film to the copper surface.
Method 2: Photoresist Paint
- Apply a thin, even layer of photoresist paint to the copper surface using a foam brush or spray can.
- Allow the photoresist to dry completely in a dark, dust-free environment.
Step 4: Exposing the Photoresist
To transfer the circuit pattern onto the photoresist, you need to expose it to UV light. Follow these steps:
- Print the circuit pattern onto a transparency film using a laser printer or photoplotter. Ensure that the printed side of the transparency is facing the photoresist.
- Place the transparency film on top of the photoresist-coated copper-clad board and secure it in place using tape or a glass plate.
- Expose the photoresist to UV light using an exposure unit or sunlight. The exposure time depends on the type of photoresist and the intensity of the UV light source. Refer to the photoresist manufacturer’s instructions for recommended exposure times.
Step 5: Developing the Photoresist
After exposure, the photoresist needs to be developed to reveal the circuit pattern. Follow these steps:
- Prepare the developer solution according to the manufacturer’s instructions.
- Immerse the exposed board in the developer solution and gently agitate it for the recommended time.
- Rinse the board with water to stop the development process and remove any remaining developer solution.
- Inspect the board to ensure that the circuit pattern is clearly visible and free of defects. If necessary, touch up any areas using a permanent marker.
Step 6: Etching the PCB
With the photoresist developed, it’s time to etch away the unwanted copper. Follow these steps:
- Prepare the etchant solution according to the manufacturer’s instructions. Common etchants include ferric chloride, ammonium persulfate, and sodium persulfate.
- Pour the etchant solution into a plastic container.
- Wear rubber gloves and safety goggles to protect yourself from the chemicals.
- Immerse the developed board in the etchant solution and agitate it gently. The etching process may take several minutes, depending on the strength of the etchant and the thickness of the copper layer.
- Periodically check the progress of the etching process. Remove the board from the solution when all the unwanted copper has been removed.
- Rinse the board thoroughly with water to stop the etching process and remove any remaining etchant.
Step 7: Removing the Photoresist
After etching, the photoresist layer needs to be removed to expose the remaining copper traces. Follow these steps:
- Use a photoresist stripper solution or acetone to dissolve the photoresist.
- Gently scrub the board with a soft brush to remove the photoresist.
- Rinse the board with water and dry it with a clean cloth or compressed air.
Step 8: Drilling and Finishing
The final step is to drill holes for component leads and apply a protective finish to the PCB. Follow these steps:
- Use a drill or hole punch to create holes at the desired locations on the PCB.
- Apply a soldermask (optional) to protect the copper traces and prevent oxidation.
- Apply a silkscreen (optional) to add component labels and other markings to the PCB.
FAQ
-
Q: Can I use any type of paper for the transparency film?
A: No, regular paper is not suitable for creating the mask. Use a specialized transparency film designed for laser printers or photoplotters to ensure sharp and accurate circuit patterns. -
Q: How do I determine the exposure time for the photoresist?
A: The exposure time depends on factors such as the type of photoresist, the intensity of the UV light source, and the distance between the light source and the board. Refer to the photoresist manufacturer’s instructions or conduct exposure tests to determine the optimal exposure time for your setup. -
Q: Can I reuse the etchant solution?
A: Yes, etchant solutions can be reused multiple times until they become exhausted and no longer effectively remove copper. However, the etching process will become slower with each use, so it’s essential to monitor the etching progress and replace the solution when necessary. -
Q: What safety precautions should I take when handling chemicals?
A: Always wear rubber gloves and safety goggles when handling etchant solutions and other chemicals. Work in a well-ventilated area and avoid inhaling fumes. Dispose of used chemicals properly according to local regulations. -
Q: How can I improve the resolution and quality of my etched PCBs?
A: To achieve higher resolution and quality, use a high-resolution printer or photoplotter to create the transparency mask. Ensure proper exposure and development of the photoresist. Maintain consistent agitation during the etching process to promote even copper removal. Finally, consider using a professionally manufactured soldermask and silkscreen for a polished finish.
Conclusion
Etching PCBs at home is a rewarding and cost-effective way to create custom circuit boards for your projects. By following the steps outlined in this article and taking the necessary safety precautions, you can produce high-quality PCBs using readily available materials and tools. With practice and patience, you’ll be able to refine your skills and take your electronics projects to the next level.
No responses yet