Introduction to PCB Printing
Printed Circuit Boards (PCBs) are the backbone of modern electronics. They are used in almost every electronic device, from smartphones and laptops to industrial machinery and medical equipment. PCB printing is a critical process that ensures the proper functioning of these devices. In this article, we will discuss how to make sure PCB printing is done properly.
What is PCB Printing?
PCB printing is the process of applying conductive ink or paste onto a substrate to create electrical connections between components. The conductive material is usually copper, but other materials such as silver, gold, or aluminum can also be used. The substrate is usually made of fiberglass, but other materials such as ceramic or plastic can also be used.
Why is PCB Printing Important?
PCB printing is important because it determines the quality and reliability of the final product. If the printing is not done properly, it can lead to several problems such as:
- Short circuits
- Open circuits
- Poor electrical connections
- Reduced lifespan of the device
Therefore, it is essential to ensure that PCB printing is done correctly to avoid these issues.
Types of PCB Printing
There are several types of PCB printing methods available, each with its own advantages and disadvantages. Here are the most common types of PCB printing:
Screen Printing
Screen printing is the most common method of PCB printing. It involves using a stencil to apply conductive ink or paste onto the substrate. The stencil is made of a fine mesh screen that is stretched over a frame. The conductive material is then forced through the openings in the screen onto the substrate using a squeegee.
Advantages:
– Low cost
– High production speed
– Suitable for large-scale production
Disadvantages:
– Limited resolution
– Requires frequent cleaning of the screen
– Not suitable for complex designs
Inkjet Printing
Inkjet printing is a newer method of PCB printing that uses a printhead to deposit conductive ink onto the substrate. The printhead contains several nozzles that spray the ink onto the substrate in a controlled manner.
Advantages:
– High resolution
– Suitable for complex designs
– Low waste of conductive material
Disadvantages:
– Slow production speed
– Higher cost compared to screen printing
– Requires specialized equipment
Flexographic Printing
Flexographic printing is a method of PCB printing that uses a flexible relief plate to transfer conductive ink onto the substrate. The plate is made of rubber or photopolymer and contains raised areas that correspond to the desired pattern.
Advantages:
– High production speed
– Suitable for large-scale production
– Can print on a variety of substrates
Disadvantages:
– Limited resolution
– Requires frequent replacement of the relief plate
– Higher cost compared to screen printing
Factors Affecting PCB Printing Quality
Several factors can affect the quality of PCB printing. Here are the most important ones:
Substrate Material
The substrate material can affect the adhesion and durability of the conductive ink or paste. Different substrate materials have different surface properties, such as roughness, porosity, and surface energy. Therefore, it is essential to choose the right substrate material for the specific application.
Substrate Material | Advantages | Disadvantages |
---|---|---|
Fiberglass | – High strength – Good thermal stability – Low cost |
– Poor flexibility – Requires surface treatment for better adhesion |
Ceramic | – High thermal conductivity – Good electrical insulation – High strength |
– Brittle – Higher cost compared to fiberglass |
Plastic | – Lightweight – Flexible – Low cost |
– Poor thermal stability – Requires surface treatment for better adhesion |
Conductive Material
The choice of conductive material can affect the conductivity, durability, and cost of the PCB. Copper is the most commonly used conductive material due to its high conductivity and low cost. However, other materials such as silver, gold, or aluminum can also be used for specific applications.
Conductive Material | Advantages | Disadvantages |
---|---|---|
Copper | – High conductivity – Low cost – Easy to solder |
– Prone to oxidation – Requires surface treatment for better adhesion |
Silver | – Highest conductivity – Good durability – Suitable for high-frequency applications |
– Higher cost compared to copper – Prone to migration |
Gold | – Excellent corrosion resistance – Good conductivity – Suitable for high-reliability applications |
– Highest cost compared to other materials – Difficult to solder |
Aluminum | – Lightweight – Good thermal conductivity – Low cost |
– Lower conductivity compared to copper – Prone to oxidation |
Printing Parameters
The printing parameters, such as the screen mesh size, squeegee pressure, and printing speed, can affect the quality of the printed pattern. The screen mesh size determines the resolution and thickness of the printed pattern. A finer mesh size results in higher resolution but thinner printed patterns. The squeegee pressure and printing speed affect the amount of conductive material deposited onto the substrate. Too much pressure or too high speed can result in smearing or bleeding of the printed pattern.
Environmental Conditions
Environmental conditions, such as temperature and humidity, can affect the printing process. High temperature can cause the conductive material to dry too quickly, resulting in poor adhesion or incomplete coverage. High humidity can cause the conductive material to absorb moisture, resulting in poor conductivity or short circuits.
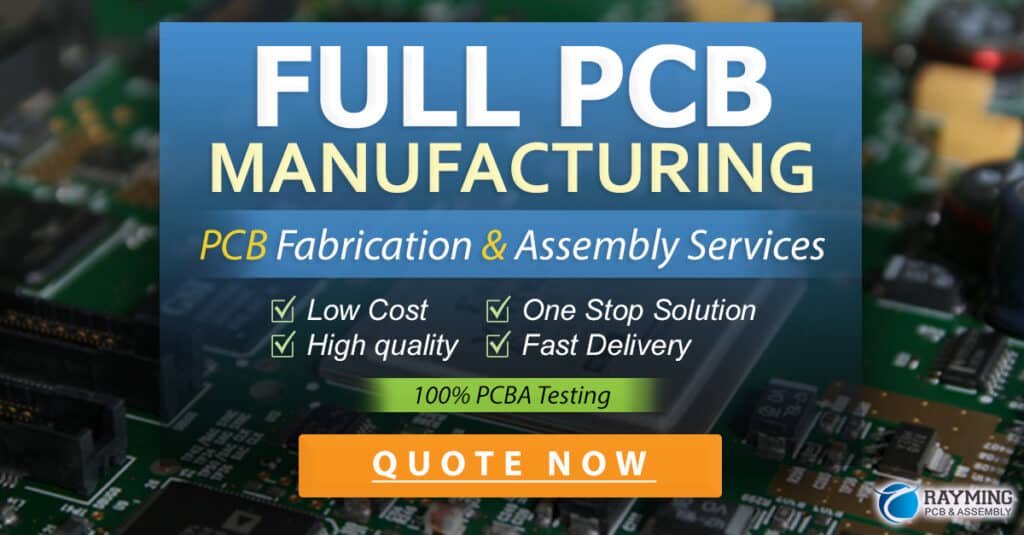
Best Practices for PCB Printing
To ensure proper PCB printing, it is essential to follow best practices. Here are some of the most important ones:
Design Considerations
The design of the PCB should take into account the limitations of the printing process. The minimum feature size, spacing, and pad size should be within the capabilities of the printing method used. The design should also consider the substrate material and conductive material used.
Substrate Preparation
The substrate should be properly cleaned and treated before printing. Any contaminants or residues on the surface can affect the adhesion and conductivity of the printed pattern. The substrate should also be properly aligned and secured to prevent shifting or warping during printing.
Printing Process Control
The printing process should be carefully controlled to ensure consistent and accurate results. The screen mesh size, squeegee pressure, and printing speed should be optimized for the specific application. The conductive material should be properly mixed and applied to prevent clogging or drying of the screen.
Post-Printing Processing
After printing, the PCB should be properly cured and cleaned to ensure good adhesion and conductivity. The curing process should be optimized for the specific conductive material and substrate used. Any residual conductive material should be removed to prevent short circuits or contamination.
Quality Control
Quality control is essential to ensure that the printed PCBs meet the required specifications. Visual inspection, electrical testing, and mechanical testing should be performed to detect any defects or issues. Any non-conforming products should be identified and corrected before final assembly.
Common Pitfalls in PCB Printing
Despite following best practices, there are still some common pitfalls that can occur in PCB printing. Here are some of the most common ones:
Incomplete Coverage
Incomplete coverage occurs when the conductive material does not fully cover the desired pattern. This can be caused by insufficient material, clogged screens, or improper printing parameters. Incomplete coverage can result in poor conductivity or open circuits.
Smearing or Bleeding
Smearing or bleeding occurs when the conductive material spreads beyond the desired pattern. This can be caused by excessive squeegee pressure, high printing speed, or improper screen tension. Smearing or bleeding can result in short circuits or reduced spacing between features.
Poor Adhesion
Poor adhesion occurs when the conductive material does not properly adhere to the substrate. This can be caused by contamination, insufficient curing, or incompatible materials. Poor adhesion can result in peeling or flaking of the printed pattern.
Inconsistent Thickness
Inconsistent thickness occurs when the printed pattern has variations in thickness across the board. This can be caused by uneven screen tension, worn squeegees, or improper printing parameters. Inconsistent thickness can result in variations in conductivity or impedance.
FAQ
Q1: What is the most common method of PCB printing?
A1: Screen printing is the most common method of PCB printing due to its low cost and high production speed.
Q2: What is the best conductive material for PCB printing?
A2: Copper is the most commonly used conductive material for PCB printing due to its high conductivity and low cost. However, other materials such as silver, gold, or aluminum can also be used for specific applications.
Q3: How can I prevent incomplete coverage in PCB printing?
A3: To prevent incomplete coverage, ensure that the screen is properly cleaned and not clogged, use sufficient conductive material, and optimize the printing parameters such as squeegee pressure and printing speed.
Q4: What causes poor adhesion in PCB printing?
A4: Poor adhesion can be caused by contamination on the substrate surface, insufficient curing of the conductive material, or incompatible materials between the substrate and conductive material.
Q5: How can I ensure consistent thickness in PCB printing?
A5: To ensure consistent thickness, maintain proper screen tension, use fresh and undamaged squeegees, and optimize the printing parameters such as squeegee pressure and printing speed.
Conclusion
PCB printing is a critical process that ensures the proper functioning of electronic devices. To ensure proper PCB printing, it is essential to choose the right substrate material, conductive material, and printing method for the specific application. It is also important to follow best practices such as design considerations, substrate preparation, process control, post-printing processing, and quality control. By avoiding common pitfalls such as incomplete coverage, smearing or bleeding, poor adhesion, and inconsistent thickness, PCB manufacturers can produce high-quality and reliable printed circuit boards.
No responses yet