Introduction to Flexible Heater Optimization
Flexible heaters have become increasingly popular in various industries due to their versatility, efficiency, and ease of use. These heaters are designed to conform to irregular shapes and surfaces, making them ideal for applications where traditional rigid heaters may not be suitable. To maximize the value of flexible heaters, it is essential to optimize their performance, durability, and overall effectiveness. In this article, we will explore the key aspects of flexible heater optimization and provide guidance on how to make these heaters the most valuable asset in your heating applications.
Understanding the Basics of Flexible Heaters
Before diving into optimization strategies, it is crucial to understand the fundamentals of flexible heaters. These heaters typically consist of a heating element, such as a wire or etched foil, embedded in a flexible substrate material. The substrate can be made from various materials, including silicone rubber, polyimide, or other flexible polymers. The heating element is connected to a power source, which supplies the necessary energy to generate heat.
Types of Flexible Heaters
There are several types of flexible heaters available, each with its own unique characteristics and applications. Some of the most common types include:
- Silicone Rubber Heaters
- Polyimide Heaters
- Etched Foil Heaters
- Carbon Fiber Heaters
- Heating Tapes and Cables
Heater Type | Characteristics | Applications |
---|---|---|
Silicone Rubber Heaters | High flexibility, excellent durability, wide temperature range | Aerospace, automotive, medical devices |
Polyimide Heaters | Thin profile, lightweight, high temperature resistance | Electronics, aerospace, medical equipment |
Etched Foil Heaters | Precise heat distribution, rapid heating, low power consumption | Semiconductor processing, analytical instruments |
Carbon Fiber Heaters | Fast heating, even heat distribution, high strength-to-weight ratio | Aerospace, automotive, industrial heating |
Heating Tapes and Cables | Easy installation, versatile, suitable for pipe and tube heating | Process heating, freeze protection, temperature maintenance |
Key Considerations for Flexible Heater Selection
When selecting a flexible heater for your application, there are several key factors to consider:
- Temperature Requirements
- Power Density
- Size and Shape
- Environmental Conditions
- Electrical Requirements
By carefully evaluating these factors, you can choose the most suitable flexible heater for your specific needs, ensuring optimal performance and value.
Strategies for Flexible Heater Optimization
Now that we have a better understanding of flexible heaters, let’s explore the various strategies for optimizing their performance and value.
Proper Heater Sizing and Placement
One of the most critical aspects of flexible heater optimization is ensuring proper sizing and placement. Heaters that are too small may not provide sufficient heat, while oversized heaters can lead to energy inefficiency and potential damage to the heated object. To determine the appropriate heater size, consider factors such as the target temperature, the size and shape of the heated object, and the available power supply.
Proper placement is equally important, as it directly affects heat distribution and overall effectiveness. Place the heater in close contact with the object to be heated, ensuring even coverage and minimizing heat loss. In some cases, using multiple smaller heaters strategically placed may be more effective than a single large heater.
Insulation and Heat Retention
Insulation plays a crucial role in flexible heater optimization, as it helps to minimize heat loss and improve energy efficiency. By properly insulating the heated object and the surrounding area, you can reduce the amount of power required to maintain the desired temperature, ultimately extending the heater’s life and reducing operating costs.
There are various insulation materials available, such as fiberglass, ceramic fiber, and aerogel. Choose the most suitable insulation based on the application’s temperature requirements, environmental conditions, and space constraints. In addition to insulation, consider using reflective materials to further enhance heat retention and distribution.
Temperature Control and Monitoring
Accurate temperature control and monitoring are essential for optimizing flexible heater performance and ensuring safety. Overheating can lead to material degradation, reduced heater lifespan, and potential fire hazards. To prevent these issues, implement a reliable temperature control system that includes sensors, thermostats, and controllers.
Temperature sensors, such as thermocouples or resistance temperature detectors (RTDs), should be placed in close proximity to the heated object to provide accurate temperature readings. Thermostats and controllers use this data to regulate the power supply, maintaining the desired temperature within a specified range. Advanced controllers may also incorporate features like PID (proportional-integral-derivative) control for more precise temperature regulation.
Material Selection and Durability
The choice of materials for both the heating element and the substrate can significantly impact the performance and longevity of a flexible heater. When selecting materials, consider factors such as temperature resistance, flexibility, chemical compatibility, and mechanical strength.
For high-temperature applications, materials like polyimide, mica, or ceramic may be more suitable than silicone rubber. In environments with corrosive chemicals or moisture, opt for materials with excellent chemical resistance and waterproofing properties. Reinforced substrates, such as those with fiberglass or Kevlar, can provide added durability and mechanical strength.
Energy Efficiency and Power Optimization
Optimizing energy efficiency is crucial for maximizing the value of flexible heaters. By reducing power consumption, you can lower operating costs and extend the heater’s lifespan. One way to achieve this is through the use of high-efficiency heating elements, such as etched foil or carbon fiber, which offer rapid heating and precise temperature control.
Another approach is to implement advanced power control techniques, such as pulse-width modulation (PWM) or variable frequency drives (VFDs). These methods allow for more precise power regulation, reducing energy waste and improving overall efficiency.
Maintenance and Troubleshooting
Regular maintenance and prompt troubleshooting are essential for ensuring the long-term performance and value of flexible heaters. Develop a comprehensive maintenance plan that includes regular inspections, cleaning, and testing of heaters and associated components.
During inspections, look for signs of wear, damage, or contamination on the heater surface and electrical connections. Clean the heater using appropriate methods and materials, taking care not to damage the heating element or substrate. Test the heater’s performance, including its ability to reach and maintain the desired temperature, and address any issues promptly.
Common problems with flexible heaters include:
- Uneven heating
- Reduced output
- Electrical shorts or open circuits
- Physical damage or delamination
By identifying and addressing these issues early on, you can prevent more serious problems and extend the heater’s lifespan.
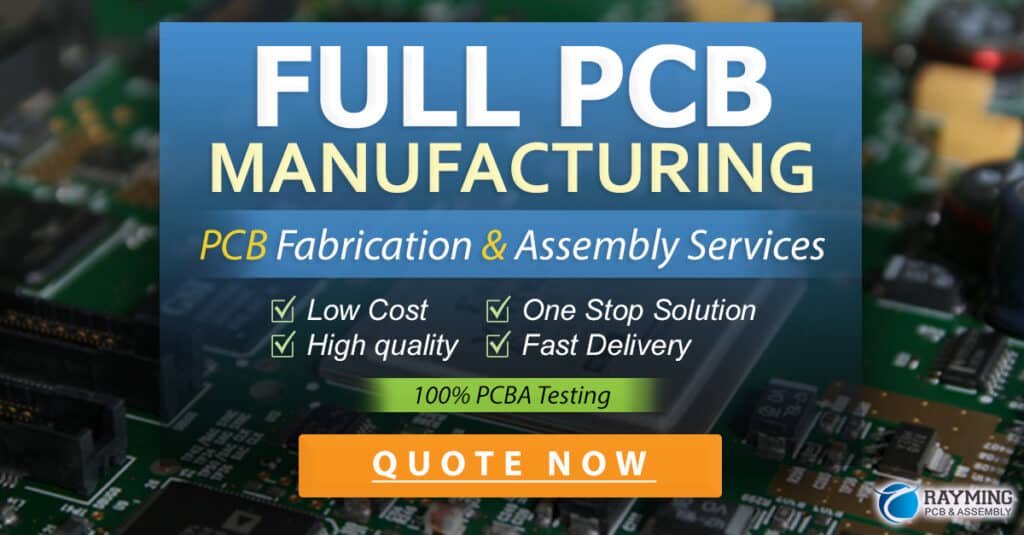
Case Studies and Real-World Applications
To better understand the value of flexible heater optimization, let’s explore some real-world applications and case studies.
Aerospace Industry
In the aerospace industry, flexible heaters are used for a wide range of applications, including wing and engine de-icing, cabin heating, and equipment temperature regulation. Optimizing these heaters is critical for ensuring the safety, comfort, and performance of aircraft.
One example is the use of carbon fiber heaters for wing de-icing. These heaters offer fast and even heat distribution, allowing for rapid de-icing and improved energy efficiency compared to traditional methods. By properly sizing and placing these heaters, aerospace engineers can ensure optimal de-icing performance while minimizing power consumption and weight.
Medical Devices
Flexible heaters are also widely used in medical devices, such as patient warming blankets, fluid warmers, and diagnostic equipment. In these applications, precise temperature control and uniform heat distribution are crucial for patient safety and comfort.
For instance, a manufacturer of patient warming blankets implemented a polyimide heater with a high-precision temperature controller. By optimizing the heater design and control system, they were able to achieve a more uniform temperature distribution across the blanket surface, reducing the risk of hot spots and ensuring patient comfort. Additionally, the improved energy efficiency resulted in lower operating costs for healthcare facilities.
Industrial Process Heating
In industrial settings, flexible heaters are used for a variety of process heating applications, such as tank and vessel heating, pipe tracing, and surface heating. Optimizing these heaters can lead to significant improvements in process efficiency, product quality, and energy savings.
A chemical processing plant recently upgraded its tank heating system, replacing traditional band heaters with custom-designed silicone rubber heaters. By carefully selecting the heater material, size, and placement, the plant was able to achieve more uniform heating and improved temperature control. This optimization resulted in reduced processing times, improved product consistency, and lower energy consumption.
Frequently Asked Questions (FAQ)
-
Q: How do I determine the appropriate wattage for my flexible heater?
A: The required wattage depends on factors such as the target temperature, the size of the heated object, and the available power supply. It is best to consult with a heater manufacturer or thermal engineering expert to determine the optimal wattage for your specific application. -
Q: Can flexible heaters be used in wet or corrosive environments?
A: Yes, certain types of flexible heaters, such as silicone rubber heaters, are designed to withstand wet and corrosive environments. However, it is essential to choose the appropriate heater material and ensure proper waterproofing and chemical resistance for your specific application. -
Q: How can I extend the lifespan of my flexible heater?
A: To extend the lifespan of your flexible heater, follow proper maintenance practices, such as regular inspections, cleaning, and testing. Additionally, ensure that the heater is properly sized, placed, and insulated to minimize stress on the heating element and substrate. -
Q: What should I do if my flexible heater is not reaching the desired temperature?
A: If your flexible heater is not reaching the desired temperature, first check for any visible damage or contamination on the heater surface and electrical connections. If no issues are found, verify that the heater is receiving the correct voltage and amperage. If the problem persists, consult with the heater manufacturer or a thermal engineering expert for further guidance. -
Q: Can flexible heaters be customized for specific applications?
A: Yes, many flexible heater manufacturers offer custom design services to meet the unique requirements of specific applications. This may include customizing the heater size, shape, wattage, and temperature range, as well as incorporating additional features like built-in temperature sensors or specialized coatings.
Conclusion
Flexible heater optimization is a critical aspect of maximizing the value and performance of these versatile heating solutions. By understanding the basics of flexible heaters, implementing optimization strategies, and learning from real-world applications, you can ensure that your heaters are operating at peak efficiency and delivering the best possible results for your specific needs.
Remember to consider factors such as proper sizing and placement, insulation and heat retention, temperature control and monitoring, material selection, energy efficiency, and regular maintenance when optimizing your flexible heaters. By taking a comprehensive approach to optimization, you can unlock the full potential of these heaters and make them the most valuable assets in your heating applications.
As flexible heater technology continues to advance, staying informed about the latest optimization techniques and best practices will be essential for staying ahead of the curve. By investing in the right strategies and working with experienced heater manufacturers and thermal engineering experts, you can ensure that your flexible heaters are always performing at their best and delivering maximum value for your organization.
No responses yet