Introduction to PCB Soldering
Printed Circuit Board (PCB) soldering is a crucial process in the assembly of electronic devices. It involves joining electronic components to the PCB using a molten metal alloy called solder. The quality of the solder joint determines the reliability and performance of the electronic device. One of the most critical aspects of PCB soldering is creating a good solder ball.
What is a Solder Ball?
A solder ball is a small sphere of solder that is used to create a connection between the electronic component and the PCB. The solder ball is placed on the PCB pad, and when heated, it melts and forms a strong bond with the component lead. The size and shape of the solder ball are critical to the quality of the solder joint.
Why is a Good Solder Ball Important?
A good solder ball ensures a strong and reliable connection between the electronic component and the PCB. It also helps to prevent short circuits and other defects that can cause the device to malfunction. A poorly formed solder ball can lead to a weak or incomplete connection, resulting in device failure.
Factors Affecting Solder Ball Formation
Several factors can affect the formation of a good solder ball. These include:
Solder Alloy Composition
The composition of the solder alloy used can affect the formation of the solder ball. Different alloys have different melting points, wetting properties, and mechanical strengths. The most common solder alloys used in PCB soldering are tin-lead (SnPb) and lead-free (SAC) alloys.
Solder Paste Printing
The solder paste printing process can also affect the formation of the solder ball. The solder paste must be applied evenly and accurately to the PCB pads to ensure a good solder ball formation. The stencil design, paste viscosity, and printing parameters must be optimized to achieve the desired results.
Reflow Profile
The reflow profile is the temperature and time profile used to melt the solder paste and form the solder ball. The reflow profile must be carefully controlled to ensure that the solder paste melts completely and forms a good solder ball. The peak temperature, time above liquidus, and cooling rate are critical parameters that must be optimized.
PCB Surface Finish
The surface finish of the PCB can also affect the formation of the solder ball. Different surface finishes have different wetting properties and can affect the spread of the molten solder. The most common surface finishes used in PCB soldering are Hot Air Solder Leveling (HASL), Organic Solderability Preservative (OSP), and Electroless Nickel Immersion Gold (ENIG).
Steps to Make a Good Solder Ball
To make a good solder ball, follow these steps:
Step 1: Choose the Right Solder Alloy
Choose a solder alloy that is suitable for your application. Consider factors such as melting point, wetting properties, and mechanical strength. For example, lead-free solder alloys are preferred for RoHS-compliant applications.
Step 2: Optimize the Solder Paste Printing Process
Optimize the solder paste printing process to ensure even and accurate solder paste deposition. Use a stencil with the appropriate aperture size and shape, and adjust the printing parameters such as squeegee pressure, speed, and separation speed.
Step 3: Control the Reflow Profile
Control the reflow profile to ensure complete melting of the solder paste and formation of a good solder ball. Use a reflow oven with accurate temperature control and monitoring capabilities. Optimize the peak temperature, time above liquidus, and cooling rate for your specific application.
Step 4: Use the Right PCB Surface Finish
Use a PCB surface finish that is compatible with your solder alloy and application. HASL is a common and cost-effective surface finish, while OSP and ENIG offer better wetting properties and longer shelf life.
Step 5: Inspect the Solder Balls
After the reflow process, inspect the solder balls to ensure that they are well-formed and free of defects. Use visual inspection or automated inspection systems to check for solder ball size, shape, and placement accuracy.
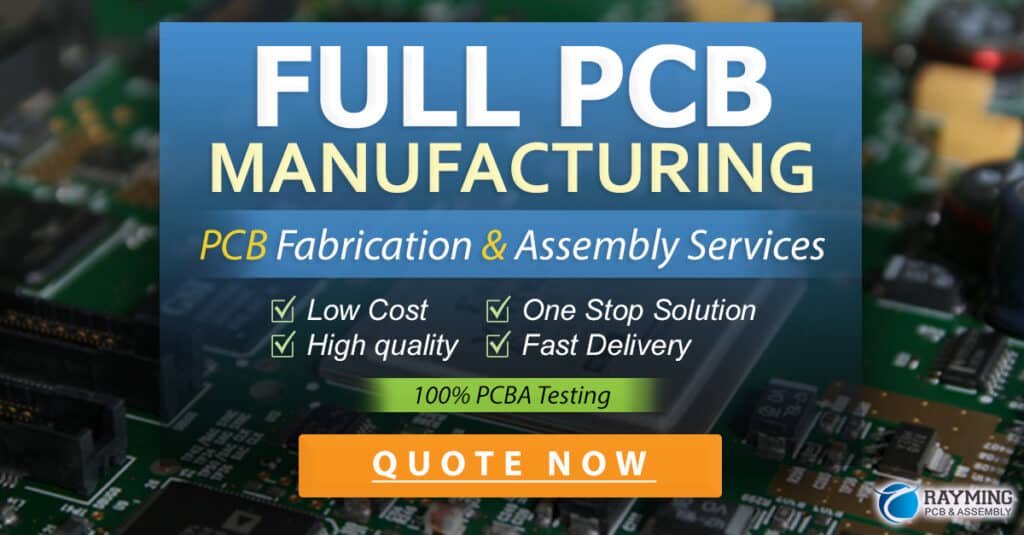
Common Solder Ball Defects and How to Prevent Them
Despite following the above steps, solder ball defects can still occur. Some common solder ball defects and their causes are:
Defect | Cause | Prevention |
---|---|---|
Solder Ball Voids | Entrapped air or moisture in the solder paste | Use fresh solder paste and optimize the reflow profile |
Solder Ball Bridging | Excessive solder paste or incorrect stencil design | Optimize the stencil design and printing parameters |
Solder Ball Misalignment | Incorrect component placement or PCB Warpage | Use accurate component placement and control PCB warpage |
Solder Ball Oxidation | Exposure to air during reflow or incorrect reflow atmosphere | Use nitrogen reflow or control the oxygen level in the reflow oven |
To prevent these defects, it is important to follow best practices in PCB soldering, such as:
- Using fresh and high-quality solder paste
- Optimizing the stencil design and printing parameters
- Controlling the reflow profile and atmosphere
- Using accurate component placement and PCB handling methods
- Conducting regular maintenance and calibration of soldering equipment
Frequently Asked Questions (FAQ)
1. What is the difference between lead-based and lead-free solder alloys?
Lead-based solder alloys, such as SnPb, contain lead, which is a hazardous substance. Lead-free solder alloys, such as SAC, do not contain lead and are RoHS-compliant. Lead-free solder alloys have higher melting points and different wetting properties compared to lead-based alloys.
2. How do I choose the right solder alloy for my application?
The choice of solder alloy depends on factors such as the application requirements, component compatibility, and regulatory compliance. For example, lead-free solder alloys are required for RoHS-compliant applications, while lead-based alloys may be used for non-RoHS applications. Consult with your solder supplier or industry standards for guidance.
3. What is the optimal reflow profile for my solder alloy?
The optimal reflow profile depends on the specific solder alloy and PCB design. Generally, the reflow profile should have a preheat stage, a soak stage, a reflow stage, and a cooling stage. The peak temperature, time above liquidus, and cooling rate should be optimized for the specific solder alloy and PCB design. Consult with your solder supplier or use industry-standard profiles as a starting point.
4. How can I prevent solder ball bridging?
Solder ball bridging can be prevented by optimizing the stencil design and printing parameters. Use a stencil with the appropriate aperture size and shape, and adjust the printing parameters such as squeegee pressure, speed, and separation speed. Also, ensure that the PCB and components are clean and free of contaminants that can cause bridging.
5. What is the shelf life of solder paste, and how should it be stored?
The shelf life of solder paste depends on the specific formulation and storage conditions. Generally, solder paste has a shelf life of 6-12 months when stored at a temperature of 0-10°C and a relative humidity of 30-70%. Solder paste should be stored in a refrigerator and allowed to warm up to room temperature before use. Expired or improperly stored solder paste can cause defects such as solder ball voids and poor wetting.
Conclusion
Making a good solder ball is critical to the reliability and performance of electronic devices. By following best practices in PCB soldering, such as choosing the right solder alloy, optimizing the solder paste printing process, controlling the reflow profile, using the right PCB surface finish, and inspecting the solder balls, you can ensure that your solder balls are well-formed and free of defects. Regular maintenance and calibration of soldering equipment, as well as adherence to industry standards and guidelines, can also help to ensure consistent and high-quality solder ball formation.
No responses yet