Introduction to PCB Manufacturing
Printed Circuit Board (PCB) manufacturing is a critical process in the electronics industry. It involves the fabrication of circuit boards that are used in a wide range of electronic devices, from smartphones and computers to medical equipment and aerospace systems. With the increasing demand for high-quality and reliable electronic products, it is essential to ensure that your PCB manufacturing process is the best in the industry.
In this article, we will discuss the key factors that determine the quality of PCB manufacturing and how you can assess whether your manufacturing process is up to par.
Factors Affecting PCB Manufacturing Quality
1. Material Selection
The choice of materials used in PCB manufacturing plays a crucial role in determining the quality and reliability of the final product. The most common materials used in PCB manufacturing include:
Material | Properties | Applications |
---|---|---|
FR-4 | High strength, good insulation, flame-resistant | General-purpose PCBs |
Polyimide | High temperature resistance, flexible | Flexible PCBs, high-temperature applications |
Aluminum | Excellent thermal conductivity | High-power applications, LED lighting |
Ceramic | High thermal conductivity, low dielectric loss | RF and microwave applications |
To ensure the best quality PCB manufacturing, it is essential to select the appropriate material based on the specific requirements of your application.
2. Design and Layout
The design and layout of the PCB are critical factors in determining the manufacturability and reliability of the final product. A well-designed PCB should consider the following aspects:
- Component placement and routing
- Signal integrity and electromagnetic compatibility (EMC)
- Thermal management
- Mechanical stress and vibration
Using advanced PCB design software and following industry-standard design guidelines can help optimize the design and layout of your PCB, resulting in improved manufacturing quality.
3. Fabrication Process
The fabrication process is the core of PCB manufacturing and directly impacts the quality of the final product. The key steps in the PCB fabrication process include:
- Copper clad laminate preparation
- Drilling and hole plating
- Copper pattern imaging and etching
- Soldermask and silkscreen application
- Surface finishing (e.g., HASL, ENIG, OSP)
Employing state-of-the-art equipment, skilled personnel, and strict process controls can ensure consistent and high-quality PCB fabrication.
4. Quality Control and Testing
Implementing a robust quality control and testing system is essential for maintaining the highest standards in PCB manufacturing. This includes:
- Automated optical inspection (AOI)
- X-ray inspection
- Electrical testing (e.g., continuity, insulation resistance)
- Functional testing
- Reliability testing (e.g., thermal cycling, vibration)
Regular audits and continuous improvement initiatives can help identify and address any quality issues, ensuring that your PCB manufacturing process remains the best in the industry.
Assessing Your PCB Manufacturing Quality
To determine whether your PCB manufacturing process is the best, consider the following steps:
-
Benchmark against industry standards: Compare your manufacturing processes and quality metrics against industry standards, such as IPC (Association Connecting Electronics Industries) and ISO (International Organization for Standardization) standards.
-
Monitor key performance indicators (KPIs): Track and analyze KPIs related to quality, reliability, and efficiency, such as:
- First pass yield (FPY)
- Defects per million opportunities (DPMO)
- On-time delivery (OTD)
-
Customer returns and complaints
-
Conduct regular audits: Perform internal and external audits to assess the effectiveness of your quality management system and identify areas for improvement.
-
Seek customer feedback: Regularly engage with your customers to gather feedback on product quality, reliability, and overall satisfaction. Use this information to drive continuous improvement initiatives.
-
Invest in technology and training: Stay up-to-date with the latest advancements in PCB manufacturing technology and invest in employee training and development to maintain a highly skilled workforce.
By following these steps and continuously monitoring and improving your PCB manufacturing process, you can ensure that you are delivering the best quality products to your customers.
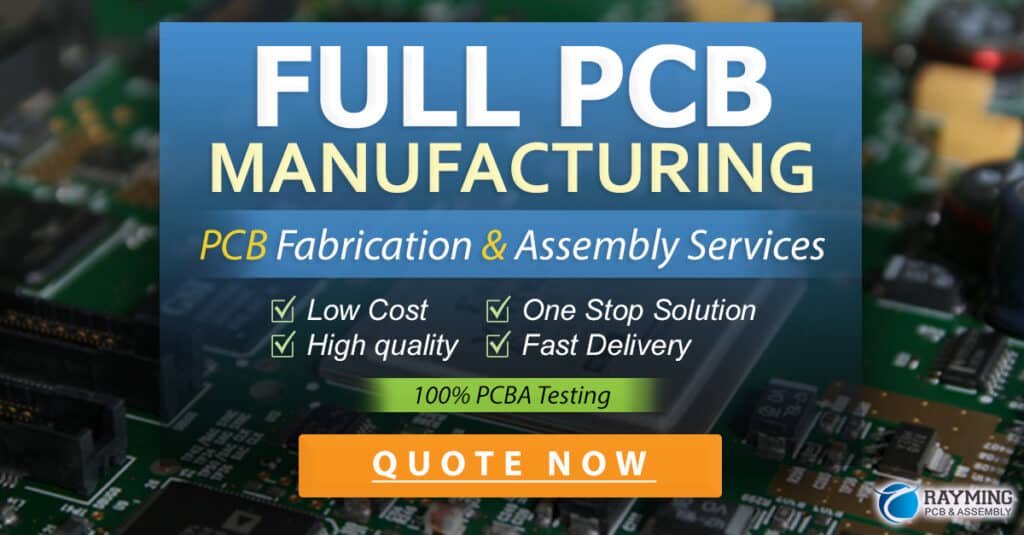
Frequently Asked Questions (FAQ)
1. What is the difference between single-sided and double-sided PCBs?
Single-sided PCBs have conductive traces on only one side of the substrate, while double-sided PCBs have conductive traces on both sides. Double-sided PCBs offer higher component density and better signal integrity compared to single-sided PCBs.
2. What is the purpose of soldermask in PCB manufacturing?
Soldermask is a protective layer applied to the PCB surface to prevent accidental bridging of the conductive traces during the soldering process. It also provides insulation and protection against environmental factors such as moisture and dust.
3. What are the common surface finishes used in PCB manufacturing?
The most common surface finishes used in PCB manufacturing include:
– Hot Air Solder Leveling (HASL)
– Electroless Nickel Immersion Gold (ENIG)
– Organic Solderability Preservative (OSP)
– Immersion Silver (IAg)
– Immersion Tin (ISn)
Each surface finish has its own advantages and disadvantages, and the choice depends on the specific requirements of the application.
4. How can I ensure the reliability of my PCB in harsh environments?
To ensure the reliability of your PCB in harsh environments, consider the following:
– Choose appropriate materials with high temperature and chemical resistance
– Use conformal coating to protect against moisture and contaminants
– Implement proper thermal management techniques to dissipate heat
– Conduct thorough reliability testing, such as thermal cycling and vibration testing
5. What is the role of automated optical inspection (AOI) in PCB manufacturing?
Automated optical inspection (AOI) is a crucial quality control step in PCB manufacturing. It uses high-resolution cameras and advanced image processing algorithms to detect and identify defects such as shorts, opens, and misaligned components on the PCB surface. AOI helps catch defects early in the manufacturing process, reducing rework and improving overall product quality.
Conclusion
Determining whether your PCB manufacturing process is the best requires a comprehensive approach that takes into account various factors, including material selection, design and layout, fabrication process, and quality control. By benchmarking against industry standards, monitoring key performance indicators, conducting regular audits, seeking customer feedback, and investing in technology and training, you can ensure that your PCB manufacturing process remains at the forefront of the industry.
Remember, delivering high-quality and reliable PCBs is essential for the success of your electronic products and the satisfaction of your customers. By continuously striving to improve your PCB manufacturing process, you can establish a strong reputation in the industry and drive the growth of your business.
No responses yet