Understanding the Difference Between HDI and PCB
When it comes to printed circuit boards (PCBs), there are two main types: High Density Interconnect (HDI) and regular PCBs. Understanding the difference between these two types of boards is crucial for determining which one is best suited for your product. In this article, we’ll explore the key differences between HDI and regular PCBs, and provide you with the information you need to make an informed decision.
What is a Regular PCB?
A regular PCB, also known as a traditional PCB, is a printed circuit board that consists of copper traces, pads, and other features etched onto a non-conductive substrate. These boards are typically used for simple electronic devices and have a lower density of components compared to HDI boards.
Regular PCBs are characterized by the following features:
- Larger trace widths and spacing
- Fewer layers (typically 2-4)
- Lower component density
- Lower cost compared to HDI boards
What is an HDI PCB?
An HDI PCB, on the other hand, is a printed circuit board that features a higher density of components and interconnects compared to a regular PCB. These boards are designed to accommodate the increasing complexity and miniaturization of modern electronic devices.
HDI PCBs are characterized by the following features:
- Smaller trace widths and spacing
- More layers (typically 8 or more)
- Higher component density
- Higher cost compared to regular PCBs
Key Differences Between HDI and Regular PCBs
Feature | Regular PCB | HDI PCB |
---|---|---|
Trace Width | ≥ 0.006 inches | ≤ 0.004 inches |
Trace Spacing | ≥ 0.006 inches | ≤ 0.004 inches |
Layers | 2-4 | 8 or more |
Component Density | Lower | Higher |
Cost | Lower | Higher |
Factors to Consider When Choosing Between HDI and Regular PCBs
When deciding between an HDI and a regular PCB for your product, there are several factors to consider:
1. Product Complexity
The complexity of your product is one of the main factors to consider when choosing between HDI and regular PCBs. If your product requires a high density of components and interconnects, an HDI board may be the better choice. On the other hand, if your product is relatively simple and doesn’t require a high level of miniaturization, a regular PCB may suffice.
2. Size Constraints
The size of your product is another important factor to consider. If your product needs to be small and compact, an HDI board may be necessary to accommodate the required components and interconnects within the limited space available. Regular PCBs, with their larger trace widths and spacing, may not be suitable for products with strict size constraints.
3. Cost
Cost is always a consideration when designing and manufacturing a product. HDI boards tend to be more expensive than regular PCBs due to their increased complexity and the specialized manufacturing processes required. If cost is a primary concern and your product doesn’t require the high density and miniaturization offered by HDI boards, a regular PCB may be the more cost-effective choice.
4. Performance Requirements
The performance requirements of your product should also be taken into account when choosing between HDI and regular PCBs. HDI boards, with their smaller trace widths and spacing, can offer improved signal integrity and reduced electromagnetic interference (EMI) compared to regular PCBs. If your product requires high-speed data transmission or is sensitive to EMI, an HDI board may be the better choice.
5. Manufacturing Capabilities
Finally, it’s important to consider the manufacturing capabilities of your chosen PCB supplier. Not all PCB manufacturers have the equipment and expertise necessary to produce HDI boards. Before deciding on an HDI board for your product, ensure that your supplier has the capability to manufacture boards with the required specifications and can do so within your desired timeframe and budget.
How to Determine if Your Product Needs an HDI or Regular PCB
Now that we’ve explored the differences between HDI and regular PCBs and the factors to consider when choosing between them, let’s discuss how to determine which type of board is best suited for your product.
Step 1: Assess Your Product’s Complexity
The first step in determining whether your product needs an HDI or regular PCB is to assess its complexity. Consider the following questions:
- How many components does your product require?
- What is the required component density?
- Are there any high-speed data transmission requirements?
- Are there any strict size constraints?
If your product requires a high number of components, high component density, high-speed data transmission, or has strict size constraints, an HDI board may be necessary.
Step 2: Evaluate Your Product’s Performance Requirements
Next, evaluate your product’s performance requirements. Consider the following questions:
- Does your product require high signal integrity?
- Is your product sensitive to electromagnetic interference (EMI)?
- Are there any specific requirements for impedance control?
If your product has strict performance requirements, such as high signal integrity, EMI sensitivity, or specific impedance control needs, an HDI board may be the better choice.
Step 3: Consider Your Budget and Manufacturing Capabilities
Finally, consider your budget and the manufacturing capabilities of your chosen PCB supplier. HDI boards are typically more expensive than regular PCBs, so if cost is a primary concern, a regular PCB may be the more cost-effective option.
Additionally, ensure that your PCB supplier has the necessary equipment and expertise to manufacture the type of board you require. If you’re considering an HDI board, verify that your supplier can produce boards with the required specifications and can do so within your desired timeframe and budget.
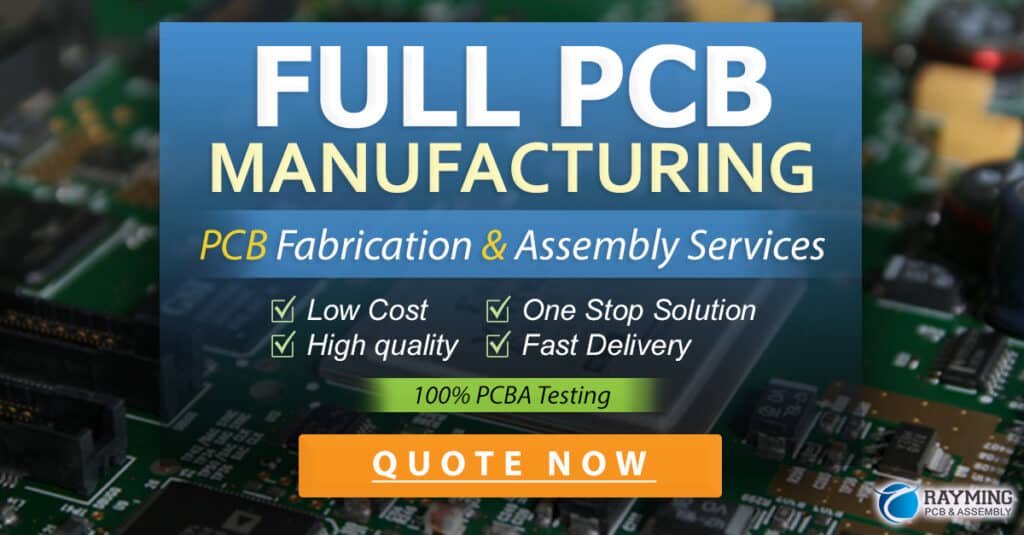
FAQs
-
Q: What is the main difference between HDI and regular PCBs?
A: The main difference between HDI and regular PCBs is the density of components and interconnects. HDI boards feature smaller trace widths and spacing, more layers, and higher component density compared to regular PCBs. -
Q: When should I choose an HDI board over a regular PCB?
A: You should choose an HDI board over a regular PCB if your product requires high component density, strict size constraints, high-speed data transmission, or improved signal integrity and EMI performance. -
Q: Are HDI boards more expensive than regular PCBs?
A: Yes, HDI boards are typically more expensive than regular PCBs due to their increased complexity and the specialized manufacturing processes required. -
Q: Can all PCB manufacturers produce HDI boards?
A: No, not all PCB manufacturers have the equipment and expertise necessary to produce HDI boards. It’s important to verify that your chosen supplier can manufacture boards with the required specifications before deciding on an HDI board for your product. -
Q: How can I determine if my product needs an HDI or regular PCB?
A: To determine if your product needs an HDI or regular PCB, assess your product’s complexity, evaluate its performance requirements, and consider your budget and the manufacturing capabilities of your chosen PCB supplier.
Conclusion
Choosing between an HDI and a regular PCB for your product is a crucial decision that can significantly impact its performance, size, and cost. By understanding the key differences between these two types of boards and considering the factors outlined in this article, you can make an informed decision that best suits your product’s requirements.
Remember to assess your product’s complexity, evaluate its performance requirements, and consider your budget and the manufacturing capabilities of your chosen PCB supplier. By doing so, you’ll be well-equipped to determine whether an HDI or regular PCB is the optimal choice for your product.
No responses yet