Understanding PWM Basics
Before diving into the design process, let’s review the fundamentals of PWM. PWM is a method of controlling the average power delivered to a load by rapidly switching the power source on and off. The key parameters of a PWM signal are:
- Duty Cycle: The percentage of time the signal is in the “on” state during one period.
- Frequency: The number of on/off cycles per second, measured in Hertz (Hz).
- Amplitude: The voltage level of the PWM signal in the “on” state.
By varying the duty cycle, we can control the average power delivered to the load. For example, a 50% duty cycle means the signal is “on” for half of the period and “off” for the other half, resulting in an average power of 50% of the maximum.
Determining Your PWM Requirements
To design an effective PWM Circuit, you must first identify your specific requirements. Consider the following factors:
-
Load Characteristics: What type of load will your PWM circuit control? Common loads include motors, LEDs, heaters, and power converters. Each load type has unique voltage, current, and power requirements.
-
Control Range: Determine the minimum and maximum duty cycles needed to achieve the desired control range for your application. For example, LED dimming may require a 0-100% duty cycle range, while a motor speed control may only need 20-80%.
-
PWM Frequency: Select an appropriate PWM frequency based on your load and application. Higher frequencies are generally better for reducing audible noise and minimizing ripple current, but they may increase switching losses. Lower frequencies may be sufficient for slower-responding loads like heaters.
-
Resolution: Consider the required resolution of your PWM control. Higher resolution allows for finer control but may require a more complex design. An 8-bit resolution provides 256 discrete duty cycle steps, while a 12-bit resolution offers 4096 steps.
Selecting PWM Components
With your requirements defined, you can now select the appropriate components for your PWM circuit. The key components include:
Microcontroller or PWM IC
You can generate PWM signals using a microcontroller with built-in PWM functionality or a dedicated PWM integrated circuit (IC). Popular options include:
- Arduino Boards: Many Arduino boards, such as the Arduino Uno and Nano, have built-in PWM capabilities on certain pins.
- PIC microcontrollers: Microchip’s PIC microcontroller family offers a wide range of devices with PWM functionality.
- 555 Timer IC: The classic 555 timer can be configured to generate PWM signals with adjustable duty cycles.
- Dedicated PWM ICs: ICs like the TL494 and SG3525 are designed specifically for PWM applications.
MOSFET or BJT Switching Devices
To handle higher power loads, you’ll need a switching device capable of rapidly turning the load on and off. Two common options are:
- MOSFETs: Metal-Oxide-Semiconductor Field-Effect Transistors (MOSFETs) are voltage-controlled devices well-suited for PWM switching. They offer fast switching speeds, low on-resistance, and high efficiency.
- BJTs: Bipolar Junction Transistors (BJTs) are current-controlled devices that can also be used for PWM switching. They are generally less efficient than MOSFETs but may be appropriate for lower-power applications.
When selecting a switching device, consider the following parameters:
Parameter | Description |
---|---|
Voltage Rating | Must exceed the maximum voltage across the device |
Current Rating | Must handle the peak and average current through the device |
Switching Speed | Faster switching allows for higher PWM frequencies |
Package Type | Affects power dissipation and ease of assembly |
Gate Driver (Optional)
If your switching device requires a high gate current or a voltage level beyond what your PWM controller can provide, you may need a gate driver circuit. Gate drivers amplify the PWM signal to ensure proper switching of the MOSFET or BJT. Common gate driver ICs include:
- IR2110: A high-speed, high-voltage gate driver for MOSFETs and IGBTs.
- TC4427: A dual-channel, low-side MOSFET gate driver with fast switching speeds.
- UCC27511: A single-channel, high-speed, low-side gate driver for power MOSFETs.
Passive Components
Your PWM circuit will also require various passive components, such as resistors and capacitors, for setting PWM parameters, filtering signals, and ensuring stable operation. The specific values and types of these components will depend on your PWM controller, switching device, and application requirements.
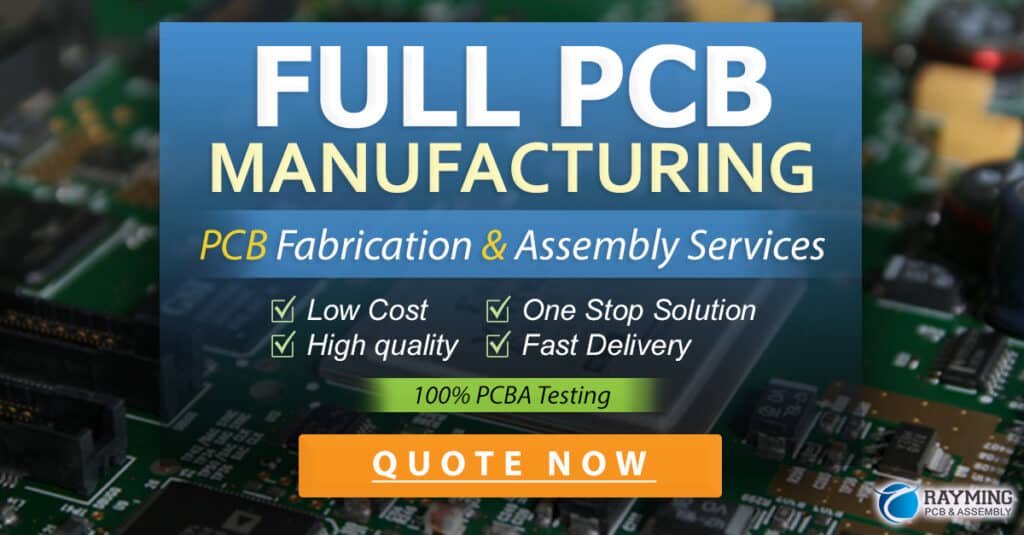
PWM Circuit Design Considerations
When designing your PWM circuit, keep the following considerations in mind:
Switching Losses
PWM Circuits experience switching losses due to the finite time required for the switching device to transition between on and off states. Higher PWM frequencies generally result in higher switching losses. To minimize losses, choose a switching device with low on-resistance and fast switching times, and consider implementing soft-switching techniques.
Heat Dissipation
Switching losses and conduction losses in the switching device and other components can generate significant heat. Ensure your circuit includes proper heat dissipation measures, such as heat sinks, thermal pads, and adequate ventilation. Monitor component temperatures during testing and adjust your design as needed.
Electromagnetic Interference (EMI)
PWM circuits can generate high-frequency noise that may interfere with nearby electronic devices. To minimize EMI, consider the following techniques:
- Keep PWM traces short and away from sensitive circuits
- Use ground planes and proper shielding
- Implement Snubber Circuits to suppress voltage spikes
- Add input and output filters to attenuate high-frequency noise
Feedback and Control
For precise control of your load, you may need to incorporate feedback and control mechanisms into your PWM circuit. This can involve:
- Sensing load current or voltage and adjusting PWM duty cycle accordingly
- Implementing closed-loop control algorithms, such as PID or fuzzy logic
- Adding protection features, like over-current or over-temperature shutdown
PWM Circuit Testing and Optimization
After designing your PWM circuit, it’s crucial to thoroughly test and optimize its performance. Follow these steps:
-
Breadboard Prototype: Begin by building a breadboard prototype of your PWM circuit. This allows for easy modification and troubleshooting.
-
Functional Testing: Verify that your PWM circuit generates the expected PWM signals and controls your load as intended. Use an oscilloscope to observe the PWM waveform and measure its frequency, duty cycle, and amplitude.
-
Performance Optimization: Optimize your PWM circuit for efficiency, heat dissipation, and EMI reduction. Experiment with different component values, layouts, and switching frequencies to find the best combination for your application.
-
Stress Testing: Subject your PWM circuit to realistic operating conditions, including maximum load, temperature extremes, and extended duration tests. Monitor circuit performance and component temperatures to identify any potential issues.
-
Final Assembly: Once you’ve optimized your design, assemble the final PWM circuit on a printed circuit board (PCB) or breadboard. Ensure all connections are secure and components are properly rated for your application.
Frequently Asked Questions (FAQ)
-
What is the difference between PWM and analog control?
PWM control uses digital pulses to control the average power delivered to a load, while analog control uses a continuous voltage or current signal. PWM is more efficient and offers more precise control, especially for digital systems. -
Can I use a microcontroller with built-in PWM for high-power loads?
Microcontrollers with built-in PWM can generate the necessary control signals, but they may not have the power handling capability for high-power loads. In such cases, you’ll need to use external switching devices like MOSFETs or BJTs to handle the load current. -
How do I select the appropriate PWM frequency for my application?
The choice of PWM frequency depends on your load and application requirements. Higher frequencies are better for reducing audible noise and minimizing ripple current but may increase switching losses. Lower frequencies may be sufficient for slower-responding loads. Experiment with different frequencies to find the best balance for your application. -
What is the purpose of a gate driver in a PWM circuit?
A gate driver is used to amplify the PWM control signal to ensure proper switching of the MOSFET or BJT switching device. It provides the necessary voltage and current to quickly charge and discharge the gate capacitance, enabling fast and efficient switching. -
How can I reduce electromagnetic interference (EMI) in my PWM circuit?
To reduce EMI, keep PWM traces short and away from sensitive circuits, use ground planes and proper shielding, implement snubber circuits to suppress voltage spikes, and add input and output filters to attenuate high-frequency noise. Proper layout and component selection can also help minimize EMI.
Designing a PWM circuit requires careful consideration of your application requirements, component selection, and circuit layout. By following the steps outlined in this guide and keeping the key design considerations in mind, you can create a PWM circuit that effectively controls your load while minimizing losses and electromagnetic interference. Remember to thoroughly test and optimize your design to ensure reliable performance in your intended application.
No responses yet