Introduction to Flexible PCBs
Flexible printed circuit boards (PCBs) have gained significant popularity in recent years due to their versatility and ability to conform to various shapes and sizes. These PCBs are made from flexible materials, such as polyimide or polyester, which allow them to bend, fold, and twist without damaging the electrical connections. Flexible PCBs offer numerous advantages over traditional rigid PCBs, including improved reliability, reduced weight and space, and enhanced design flexibility.
However, working with flexible PCBs also presents unique challenges that must be addressed to ensure optimal performance and reliability. This article will explore the opportunities and challenges associated with flexible PCBs and provide guidance on how to effectively deal with them.
Advantages of Flexible PCBs
Increased Design Flexibility
One of the primary advantages of flexible PCBs is their ability to conform to various shapes and sizes. This increased design flexibility allows for more compact and lightweight electronic devices, as the PCB can be folded or bent to fit within the available space. Flexible PCBs also enable designers to create more ergonomic and user-friendly devices, as they can be shaped to fit the contours of the human body or other objects.
Improved Reliability
Flexible PCBs offer improved reliability compared to rigid PCBs, particularly in applications that are subject to vibration, shock, or thermal stress. The flexibility of the PCB allows it to absorb and dissipate mechanical stress, reducing the risk of damage to the electrical connections. Additionally, flexible PCBs can be designed with strain relief features, such as curved traces or accordion-like folds, which further enhance their resistance to mechanical stress.
Reduced Weight and Space
The use of flexible PCBs can significantly reduce the weight and space requirements of electronic devices. By eliminating the need for bulky connectors and wiring harnesses, flexible PCBs enable more compact and lightweight designs. This is particularly valuable in applications where weight and size are critical factors, such as aerospace, medical devices, and wearable technology.
Cost Savings
While the initial cost of flexible PCBs may be higher than that of rigid PCBs, they can offer significant cost savings in the long run. The increased reliability and reduced weight and space requirements of flexible PCBs can lead to lower maintenance and replacement costs, as well as reduced shipping and handling expenses. Additionally, the ability to integrate multiple components and functions onto a single flexible PCB can streamline the manufacturing process and reduce assembly costs.
Challenges of Flexible PCBs
Material Selection
Selecting the appropriate material for a flexible PCB is crucial to ensuring its performance and reliability. The material must be able to withstand the intended application’s mechanical, thermal, and chemical stresses while maintaining its electrical properties. Common materials used for flexible PCBs include polyimide, polyester, and flexible copper-clad laminates. Each material has its own set of advantages and limitations, and the choice will depend on the specific requirements of the application.
Design Considerations
Designing flexible PCBs requires careful consideration of several factors, such as bend radius, conductor width and spacing, and strain relief features. The bend radius is the minimum radius that the PCB can be bent without causing damage to the electrical connections. This value will depend on the thickness and material of the PCB, as well as the location and orientation of the components. Conductor width and spacing must also be optimized to ensure adequate signal integrity and prevent short circuits or open connections. Strain relief features, such as curved traces or accordion-like folds, can be incorporated into the design to improve the PCB’s resistance to mechanical stress.
Manufacturing Processes
Manufacturing flexible PCBs requires specialized equipment and processes that differ from those used for rigid PCBs. The flexible materials used for the substrate and conductors must be handled carefully to prevent damage or contamination. The etching process must also be carefully controlled to ensure accurate conductor patterns and prevent underetching or overetching. Additionally, the assembly process for flexible PCBs may require specialized techniques, such as adhesive bonding or heat sealing, to ensure a secure and reliable connection between the PCB and the components.
Testing and Inspection
Testing and inspection of flexible PCBs are critical to ensuring their performance and reliability. However, the flexible nature of the PCB can make these processes more challenging than with rigid PCBs. Special fixturing may be required to hold the PCB in place during testing, and the flexible material may require different testing methods or parameters. Visual inspection of flexible PCBs may also be more difficult, as the conductors and components may be hidden within the folds or bends of the PCB.
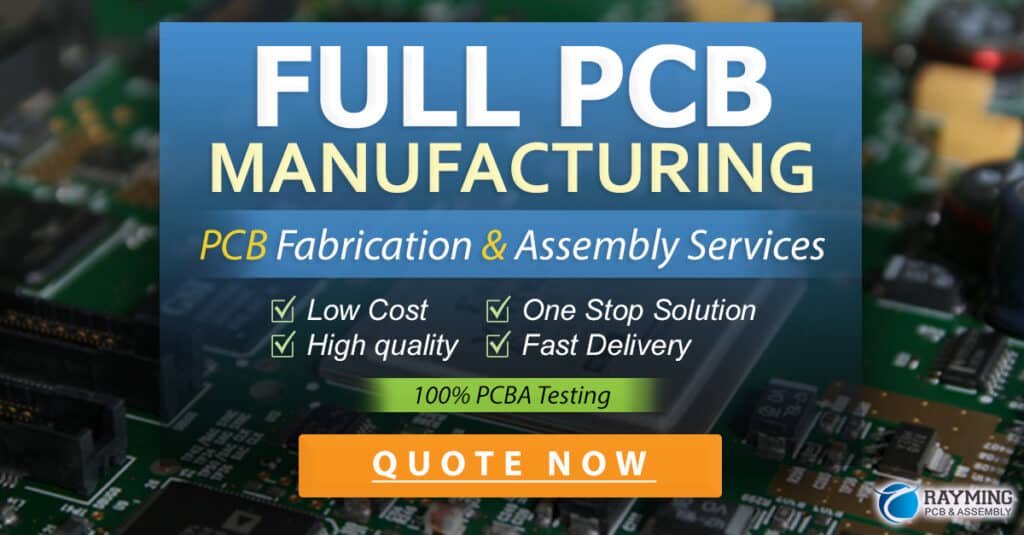
Best Practices for Working with Flexible PCBs
Collaborate with Experienced Suppliers
Working with experienced and reputable suppliers is essential when designing and manufacturing flexible PCBs. These suppliers should have a proven track record of producing high-quality flexible PCBs and be familiar with the latest materials, processes, and design techniques. Collaborating closely with the supplier throughout the design and manufacturing process can help ensure that the PCB meets all performance and reliability requirements.
Conduct Thorough Testing and Inspection
Thorough testing and inspection are critical to ensuring the performance and reliability of flexible PCBs. This may require specialized equipment and techniques, such as 3D X-ray inspection or thermal cycling tests. It is important to establish a comprehensive testing and inspection plan early in the design process and to work closely with the supplier to ensure that all necessary tests are conducted.
Consider Environmental Factors
Flexible PCBs are often used in applications that are subject to harsh environmental conditions, such as extreme temperatures, humidity, or chemical exposure. It is important to consider these environmental factors when selecting materials and designing the PCB. Special coatings or encapsulants may be required to protect the PCB from environmental stresses, and the design may need to incorporate features such as ventilation or heat dissipation to ensure reliable operation.
Plan for Manufacturing and Assembly
Manufacturing and assembly of flexible PCBs require specialized processes and equipment that may differ from those used for rigid PCBs. It is important to work closely with the supplier to ensure that the PCB design is optimized for manufacturability and that the necessary processes and equipment are in place. This may involve conducting design for manufacturability (DFM) reviews or creating detailed assembly instructions to ensure a smooth and efficient production process.
Frequently Asked Questions (FAQ)
1. What are the most common materials used for flexible PCBs?
The most common materials used for flexible PCBs are polyimide, polyester, and flexible copper-clad laminates. Polyimide is known for its high temperature resistance and excellent mechanical properties, while polyester is a lower-cost alternative that is suitable for less demanding applications. Flexible copper-clad laminates combine a flexible substrate with a thin layer of copper for the conductors.
2. How do I determine the appropriate bend radius for my flexible PCB?
The appropriate bend radius for a flexible PCB depends on several factors, including the thickness and material of the PCB, the location and orientation of the components, and the intended application. As a general rule, the bend radius should be at least 10 times the thickness of the PCB to prevent damage to the electrical connections. However, it is important to consult with the supplier and conduct thorough testing to determine the optimal bend radius for a specific design.
3. What are some common challenges associated with manufacturing flexible PCBs?
Some common challenges associated with manufacturing flexible PCBs include handling and processing the flexible materials, controlling the etching process to ensure accurate conductor patterns, and developing specialized assembly techniques such as adhesive bonding or heat sealing. Additionally, the flexible nature of the PCB can make testing and inspection more difficult, requiring specialized fixturing and testing methods.
4. How can I ensure the reliability of my flexible PCB in harsh environmental conditions?
To ensure the reliability of a flexible PCB in harsh environmental conditions, it is important to select materials that are suitable for the intended application and to consider incorporating protective features such as coatings or encapsulants. The design should also incorporate features such as strain relief or ventilation to mitigate the effects of thermal or mechanical stress. Thorough testing and inspection, including environmental testing, can help identify potential issues and ensure reliable operation.
5. What are the benefits of using flexible PCBs in my electronic device?
The benefits of using flexible PCBs in electronic devices include increased design flexibility, improved reliability, reduced weight and space requirements, and potential cost savings. Flexible PCBs can conform to the shape of the device, enabling more compact and ergonomic designs. They also offer improved resistance to vibration, shock, and thermal stress, leading to higher reliability. By reducing the need for connectors and wiring harnesses, flexible PCBs can help reduce the weight and size of the device, as well as simplify the assembly process and reduce costs.
Conclusion
Flexible PCBs offer numerous opportunities for designers and manufacturers of electronic devices, enabling more compact, lightweight, and reliable designs. However, working with flexible PCBs also presents unique challenges that must be addressed through careful material selection, design considerations, manufacturing processes, and testing and inspection.
By collaborating with experienced suppliers, conducting thorough testing and inspection, considering environmental factors, and planning for manufacturing and assembly, designers and manufacturers can effectively deal with the challenges of flexible PCBs and realize their full potential. As the demand for smaller, more complex, and more reliable electronic devices continues to grow, flexible PCBs will play an increasingly important role in enabling the next generation of innovative products.
No responses yet