Introduction to PCB Cutting
Printed Circuit Boards (PCBs) are essential components in virtually all modern electronic devices. PCBs provide a platform for mounting and interconnecting electronic components to form functional circuits. While PCBs can be manufactured in various shapes and sizes, in many cases, they need to be cut to fit specific device enclosures or to separate individual boards from a larger panel. In this comprehensive guide, we will explore the various methods and techniques for cutting PCBs effectively and efficiently.
Why Cut PCBs?
There are several reasons why you might need to cut a PCB:
-
Separating individual boards: PCBs are often manufactured in large panels containing multiple identical boards. These panels need to be cut to separate the individual boards for use in devices.
-
Fitting into enclosures: PCBs may need to be cut to fit into specific device enclosures or cases. This is especially common in custom electronics projects or when using off-the-shelf enclosures.
-
Prototyping and testing: During the prototyping and testing phase of PCB design, you may need to cut boards to make modifications or to isolate specific sections for testing.
-
Repairs and modifications: In some cases, you may need to cut a PCB to remove a damaged section or to make modifications to an existing board.
PCB Cutting Methods
There are several methods for cutting PCBs, each with its own advantages and limitations. The choice of method depends on factors such as the size and thickness of the board, the required precision, and the available tools and equipment. Let’s explore some of the most common PCB cutting methods:
1. Scoring and Snapping
Scoring and snapping is a simple and inexpensive method for cutting PCBs, especially for small boards or low-volume production. This method involves using a scoring tool, such as a utility knife or a specialized PCB scoring tool, to create a deep groove along the desired cut line on both sides of the board. Once scored, the board can be snapped along the groove by applying pressure with your hands or a pair of pliers.
Advantages:
– Inexpensive and requires minimal tools
– Suitable for small boards and low-volume production
– Can be done quickly without specialized equipment
Limitations:
– Not suitable for thick or multi-layer boards
– Limited precision and accuracy
– May cause stress on components near the cut line
2. Shearing
Shearing is a mechanical cutting method that uses a shear machine or a guillotine cutter to cut PCBs. The board is placed between two blades, and a strong shearing force is applied to cut through the board material. Shearing is suitable for cutting straight lines on medium to large-sized boards.
Advantages:
– Fast and efficient for cutting straight lines
– Suitable for medium to large-sized boards
– Produces clean and burr-free edges
Limitations:
– Limited to straight cuts
– Requires a shear machine or guillotine cutter
– May cause stress on components near the cut line
3. Routing
Routing is a precise and versatile method for cutting PCBs using a CNC router or a handheld rotary tool with a routing bit. The router bit follows a programmed path to cut the desired shape or outline on the board. Routing is ideal for cutting complex shapes, creating holes, and milling pockets in PCBs.
Advantages:
– High precision and accuracy
– Versatile and capable of cutting complex shapes
– Can create holes and mill pockets in addition to cutting
– Suitable for a wide range of board sizes and thicknesses
Limitations:
– Requires specialized equipment (CNC router or handheld rotary tool)
– More time-consuming than other methods
– May generate dust and debris that can settle on the board
4. Laser Cutting
Laser cutting is a highly precise and non-contact method for cutting PCBs using a high-powered laser beam. The laser beam vaporizes the board material along the programmed path, creating a clean and accurate cut. Laser cutting is suitable for cutting intricate shapes, creating holes, and engraving patterns on PCBs.
Advantages:
– Extremely high precision and accuracy
– Non-contact method, minimizing stress on components
– Capable of cutting intricate shapes and creating holes
– Produces clean and smooth edges
Limitations:
– Requires specialized and expensive equipment
– May not be suitable for thick or multi-layer boards
– Can be slower than other methods for simple cuts
5. Punching
Punching is a mechanical cutting method that uses a punch and die set to cut specific shapes or holes in PCBs. The board is placed between the punch and die, and a strong force is applied to cut through the board material. Punching is ideal for creating circular holes or other standard shapes in PCBs.
Advantages:
– Fast and efficient for creating specific shapes or holes
– Produces clean and burr-free edges
– Suitable for high-volume production
Limitations:
– Limited to specific shapes and sizes based on available punch and die sets
– Requires specialized equipment and tooling
– May cause stress on components near the punched area
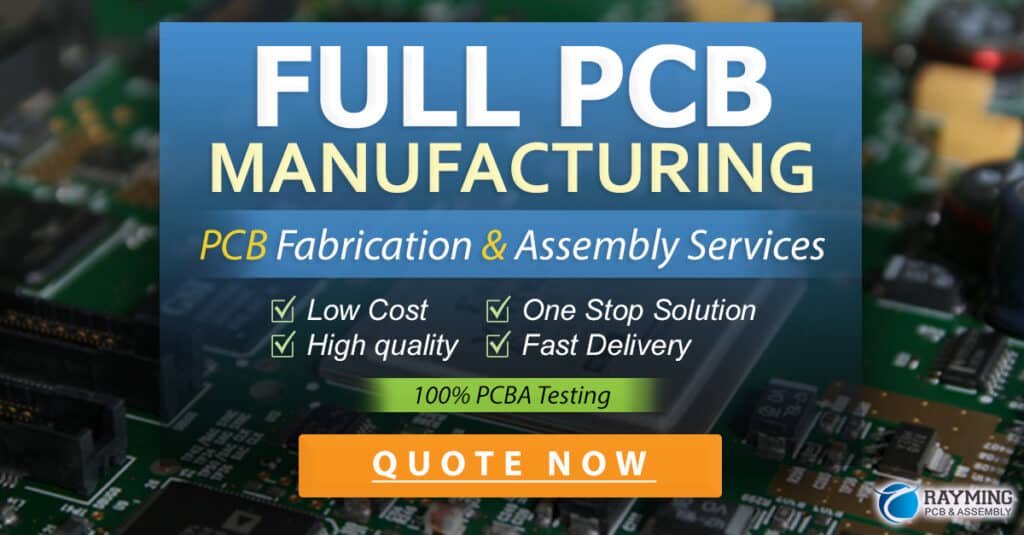
Choosing the Right PCB Cutting Method
When deciding on the best PCB cutting method for your project, consider the following factors:
-
Board size and thickness: The size and thickness of your PCB will influence the choice of cutting method. Thicker boards may require more robust methods like routing or shearing, while thinner boards can be cut using scoring and snapping or laser cutting.
-
Required precision: If your PCB requires high precision cuts or intricate shapes, methods like laser cutting or routing may be more suitable. For less precise cuts, scoring and snapping or shearing can be sufficient.
-
Production volume: The volume of PCBs you need to cut will also impact your choice of method. For low-volume production or prototyping, manual methods like scoring and snapping or handheld routing may be adequate. For high-volume production, automated methods like shearing, punching, or CNC routing may be more efficient.
-
Available tools and equipment: Consider the tools and equipment you have access to. If you have a CNC router or laser cutter, those methods may be more feasible. If you have limited equipment, manual methods like scoring and snapping or handheld routing may be more practical.
-
Budget: The cost of equipment and tooling for different cutting methods varies significantly. Manual methods like scoring and snapping are typically the most affordable, while specialized equipment like laser cutters or CNC routers can be more expensive.
Safety Considerations
When cutting PCBs, it’s essential to prioritize safety to prevent injuries and protect yourself from potential hazards. Here are some safety considerations to keep in mind:
-
Wear protective gear: Always wear appropriate personal protective equipment (PPE) when cutting PCBs. This may include safety glasses or goggles to protect your eyes from debris, a dust mask to avoid inhaling particles, and gloves to protect your hands from sharp edges or heat.
-
Work in a well-ventilated area: Some PCB cutting methods, such as laser cutting or routing, can generate fumes or dust particles. Ensure that you work in a well-ventilated area or use a fume extraction system to minimize exposure to harmful particles.
-
Follow equipment safety guidelines: When using specialized equipment like CNC routers, laser cutters, or shear machines, always follow the manufacturer’s safety guidelines and instructions. Ensure that you are properly trained and familiar with the equipment before use.
-
Secure the PCB: When cutting PCBs, make sure the board is securely clamped or fixed in place to prevent slipping or movement during the cutting process. This will help ensure a clean cut and prevent accidents.
-
Handle sharp edges with care: After cutting PCBs, the edges may be sharp or have burrs. Handle the cut boards carefully to avoid cuts or injuries. Use a deburring tool or sandpaper to smooth any rough edges if necessary.
Tips for Successful PCB Cutting
To achieve the best results when cutting PCBs, consider the following tips:
-
Plan your cuts: Before cutting your PCB, carefully plan the desired shape or outline. Consider the placement of components, traces, and other features to ensure that the cut does not damage or interfere with the board’s functionality.
-
Use the right tools: Choose the appropriate tools for your chosen cutting method. For example, if you are scoring and snapping, use a sharp utility knife or a specialized PCB scoring tool. If you are routing, use a high-quality router bit suitable for the board material and thickness.
-
Measure and mark accurately: Accurate measurements and markings are crucial for precise cuts. Use a ruler, caliper, or measuring tool to determine the dimensions of your cut. Mark the cut line clearly on the board using a pencil, marker, or scribe.
-
Practice on scrap boards: If you are new to PCB cutting or using a new method, practice on scrap boards or test pieces before cutting your final board. This will help you develop a feel for the tools and techniques and allow you to make any necessary adjustments.
-
Take your time: Rushing the cutting process can lead to mistakes or inaccuracies. Take your time and make sure each cut is precise and clean. Rushing can also increase the risk of accidents or injuries.
-
Clean the board after cutting: After cutting your PCB, remove any dust, debris, or burrs from the board’s surface and edges. This will help ensure proper component placement and soldering during the assembly process.
Frequently Asked Questions (FAQ)
-
What is the easiest method for cutting PCBs at home?
The easiest method for cutting PCBs at home is typically scoring and snapping. This method requires minimal tools and can be done quickly with a sharp utility knife and a straight edge. -
Can I cut a PCB with scissors?
While it is possible to cut thin, single-layer PCBs with scissors, it is not recommended. Scissors can cause the board to bend or deform, and the cut edges may be rough or uneven. It’s best to use a proper PCB cutting method for better results. -
How do I choose the right router bit for cutting PCBs?
When choosing a router bit for cutting PCBs, consider the board material, thickness, and the desired cut quality. Carbide router bits are suitable for most PCB materials, and the bit diameter should be appropriate for the cut width and depth. Consult the router bit manufacturer’s guidelines or seek advice from experienced professionals. -
Can I cut a PCB with a laser cutter designed for wood or acrylic?
While some laser cutters designed for wood or acrylic may be capable of cutting PCBs, it’s important to note that the power, speed, and focus settings may need to be adjusted for the specific PCB material. Additionally, cutting PCBs with a laser cutter may release harmful fumes, so proper ventilation and safety precautions are essential. -
How do I ensure that my PCB cuts are straight and accurate?
To ensure straight and accurate PCB cuts, use a straight edge or guide when marking and cutting the board. Measure carefully and double-check your dimensions before making the cut. If using a mechanical cutting method, make sure the board is securely clamped and the cutting tool is properly aligned. If using a CNC router or laser cutter, ensure that the machine is calibrated and the programmed path is accurate.
Conclusion
Cutting PCBs is an essential skill for anyone involved in electronics prototyping, manufacturing, or repairs. By understanding the various methods and techniques for cutting PCBs, you can choose the most suitable approach for your project based on factors such as board size, required precision, production volume, and available tools. Remember to prioritize safety, plan your cuts carefully, and take your time to achieve the best results. With practice and the right tools, you can master the art of PCB cutting and create high-quality, custom-shaped boards for your electronic projects.
No responses yet