Understanding PCB Fabrication
Before delving into the selection criteria, it’s essential to understand the basics of PCB fabrication. PCB fabrication is the process of creating a printed circuit board from a digital design file. The process involves several stages, including:
- PCB Design: Creating a digital layout of the circuit using specialized software.
- PCB Fabrication: Manufacturing the physical board based on the digital design.
- PCB Assembly: Placing and soldering components onto the fabricated board.
- PCB Testing: Verifying the functionality and quality of the assembled board.
Each stage plays a crucial role in the overall quality and reliability of the final product. When choosing a PCB fabrication service, it’s important to consider their capabilities and expertise in each of these areas.
Factors to Consider When Choosing a PCB Fabrication Service
Technical Capabilities
One of the primary factors to consider when selecting a PCB fabrication service is their technical capabilities. Different projects may have varying requirements in terms of board complexity, layer count, material selection, and manufacturing processes. It’s crucial to choose a service provider that can accommodate your specific technical needs. Consider the following aspects:
-
Board Complexity: Assess the complexity of your PCB design, including the number of layers, trace widths, and component density. Ensure that the fabrication service has the capability to handle your board’s complexity level.
-
Material Selection: PCBs can be manufactured using different materials, such as FR-4, high-frequency laminates, or flexible substrates. Make sure the fabrication service offers the materials suitable for your application’s requirements.
-
Manufacturing Processes: Inquire about the manufacturing processes employed by the fabrication service. Advanced processes like HDI (High-Density Interconnect), microvias, and controlled impedance may be necessary for high-performance designs.
-
Certifications and Standards: Check if the fabrication service holds relevant certifications and adheres to industry standards, such as IPC (Institute of Printed Circuits) or ISO (International Organization for Standardization). These certifications ensure that the service provider follows best practices and maintains consistent quality.
Quality Control and Testing
The quality of your PCBs directly impacts the reliability and performance of your final product. When evaluating PCB fabrication services, pay close attention to their quality control measures and testing procedures. Consider the following aspects:
-
Quality Management System: Inquire about the fabrication service’s quality management system (QMS). A well-established QMS ensures that the service provider follows standardized processes, maintains documentation, and continuously improves their quality standards.
-
Inspection and Testing: Ask about the inspection and testing procedures employed by the fabrication service. Automated optical inspection (AOI), X-ray inspection, and electrical testing are common methods used to identify defects and ensure the functionality of the manufactured boards.
-
Failure Analysis: In case of any issues or defects, it’s important to have a fabrication service that can perform thorough failure analysis. This helps identify the root cause of the problem and implement corrective actions to prevent future occurrences.
-
Traceability: A reliable fabrication service should have a robust traceability system in place. This allows for easy tracking of materials, processes, and personnel involved in the manufacturing of your PCBs, facilitating quick resolution of any issues that may arise.
Lead Time and Delivery
Time-to-market is a critical factor in the electronics industry. When selecting a PCB fabrication service, consider their lead time and delivery capabilities. Faster lead times can help you meet tight project deadlines and bring your products to market quickly. However, it’s important to strike a balance between speed and quality. Consider the following aspects:
-
Standard Lead Time: Inquire about the fabrication service’s standard lead time for different board types and quantities. This will give you a baseline understanding of their turnaround capabilities.
-
Expedited Services: Check if the fabrication service offers expedited or rush services for urgent projects. Be aware that expedited services may come at a higher cost.
-
On-Time Delivery: Evaluate the fabrication service’s track record in meeting delivery commitments. Consistent on-time delivery is crucial for maintaining your project timelines and avoiding delays.
-
Shipping and Logistics: Consider the fabrication service’s shipping and logistics capabilities. Do they offer international shipping? Are they able to handle customs clearance and documentation? Efficient shipping and logistics can streamline the delivery process and minimize potential delays.
Cost and Pricing
Cost is an important consideration when choosing a PCB fabrication service, as it directly impacts your project budget. However, it’s essential to balance cost with quality and reliability. The lowest price may not always provide the best value in the long run. Consider the following aspects:
-
Pricing Structure: Understand the fabrication service’s pricing structure. Do they offer per-unit pricing, volume discounts, or tiered pricing based on quantity? Evaluate how their pricing aligns with your budget and production volumes.
-
NRE (Non-Recurring Engineering) Costs: Inquire about any NRE costs associated with your project, such as tooling, setup, or design review fees. These one-time costs can impact the overall project budget.
-
Cost vs. Quality: While cost is important, it shouldn’t be the sole determining factor. Cheap PCBs may compromise on quality, leading to potential reliability issues and higher costs in the long run. Strike a balance between cost and quality to ensure the best value for your project.
-
Hidden Costs: Be aware of any hidden costs or additional charges that may not be explicitly stated in the initial pricing. These can include handling fees, packaging costs, or minimum order quantities (MOQs). Clarify all costs upfront to avoid surprises later.
Customer Support and Communication
Effective communication and reliable customer support are vital when working with a PCB fabrication service. You want a service provider that is responsive, knowledgeable, and willing to address your concerns and requirements. Consider the following aspects:
-
Responsiveness: Evaluate the fabrication service’s responsiveness to inquiries and requests. Do they provide timely and accurate responses? Are they easily accessible through various communication channels, such as email, phone, or live chat?
-
Technical Support: Assess the level of technical support offered by the fabrication service. Do they have experienced engineers or technicians who can provide guidance and assistance with your PCB design and manufacturing processes?
-
Communication Channels: Consider the communication channels available for interacting with the fabrication service. Do they offer a dedicated account manager or a single point of contact? Are there language barriers that may hinder effective communication?
-
Problem Resolution: Inquire about the fabrication service’s approach to problem resolution. How do they handle issues or concerns that may arise during the manufacturing process? A proactive and solution-oriented approach is essential for ensuring a smooth collaboration.
Reputation and Experience
The reputation and experience of a PCB fabrication service can provide valuable insights into their reliability and track record. Consider the following aspects:
-
Industry Experience: Look for a fabrication service with extensive experience in the PCB industry. Longer-standing companies often have well-established processes, a broader range of capabilities, and a deeper understanding of industry trends and best practices.
-
Customer References: Ask for customer references or case studies from the fabrication service. Reach out to these references to gather feedback on their experience working with the service provider, including quality, reliability, and communication aspects.
-
Online Reviews: Research online reviews and ratings of the fabrication service on industry forums, social media, or review platforms. While individual experiences may vary, a consistent pattern of positive or negative feedback can provide valuable insights.
-
Industry Certifications: Check if the fabrication service holds relevant industry certifications, such as IPC, ISO, or UL (Underwriters Laboratories). These certifications demonstrate the service provider’s commitment to quality, reliability, and adherence to industry standards.
Frequently Asked Questions (FAQ)
-
What is the minimum order quantity (MOQ) for PCB fabrication?
The minimum order quantity for PCB fabrication varies among service providers. Some fabrication services may offer low MOQs to accommodate prototype or small-batch production, while others may require higher quantities for cost-effectiveness. It’s important to discuss your specific requirements with the fabrication service to determine their MOQ policies. -
How long does PCB fabrication typically take?
The lead time for PCB fabrication depends on various factors, such as the complexity of the board, the selected materials, and the manufacturing processes involved. Standard lead times can range from a few days to several weeks. Rush or expedited services may be available for urgent projects, but they often come at a higher cost. It’s best to communicate your timeline requirements with the fabrication service upfront to ensure they can meet your needs. -
Can I provide my own PCB design files for fabrication?
Yes, most PCB fabrication services allow you to provide your own design files for manufacturing. The fabrication service will typically specify the acceptable file formats, such as Gerber files or ODB++ files. It’s important to ensure that your design files adhere to the fabrication service’s design guidelines and specifications to avoid any issues during the manufacturing process. -
What should I do if I receive PCBs with defects or quality issues?
If you receive PCBs with defects or quality issues, the first step is to contact the fabrication service’s customer support or your designated account manager. Provide detailed information about the issues you have encountered, including photos or videos if applicable. A reliable fabrication service should have a well-defined process for handling quality issues, including root cause analysis, corrective actions, and replacement or rework of the affected boards. -
Can I request custom PCB specifications or materials?
Many PCB fabrication services offer the flexibility to accommodate custom specifications or materials based on your project requirements. If you have specific needs, such as unique board shapes, non-standard materials, or special finishes, it’s important to discuss these requirements with the fabrication service upfront. They can provide guidance on feasibility, any additional costs involved, and the impact on lead time.
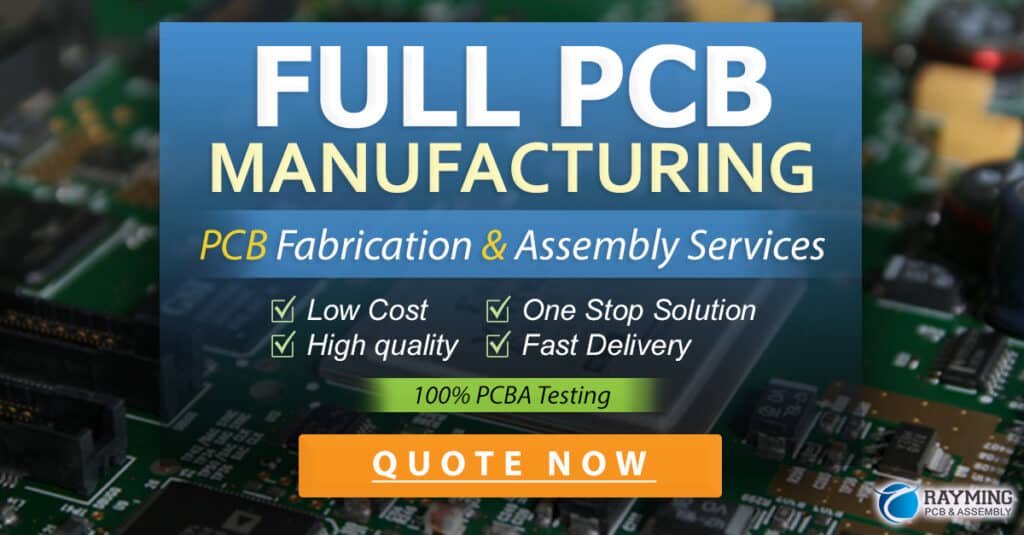
Conclusion
Choosing a reliable PCB fabrication service is a critical decision that can significantly impact the success of your electronics projects. By considering factors such as technical capabilities, quality control, lead time, cost, customer support, and reputation, you can make an informed choice that aligns with your specific needs and requirements.
Remember to prioritize quality and reliability over solely focusing on cost. Cheap PCBs may save you money upfront but can lead to costly failures and delays down the line. Establish clear communication channels with your chosen fabrication service and maintain an open dialogue throughout the manufacturing process to ensure a smooth collaboration.
By following the guidelines outlined in this article and conducting thorough research, you can find a PCB fabrication service that becomes a trusted partner in bringing your electronic designs to life. Invest the time and effort in selecting the right service provider, and you’ll be well on your way to creating high-quality, reliable PCBs that meet your project goals and exceed customer expectations.
Factor | Considerations |
---|---|
Technical Capabilities | Board complexity, material selection, manufacturing processes, certifications and standards |
Quality Control and Testing | Quality management system, inspection and testing procedures, failure analysis, traceability |
Lead Time and Delivery | Standard lead time, expedited services, on-time delivery, shipping and logistics |
Cost and Pricing | Pricing structure, NRE costs, cost vs. quality, hidden costs |
Customer Support and Communication | Responsiveness, technical support, communication channels, problem resolution |
Reputation and Experience | Industry experience, customer references, online reviews, industry certifications |
By carefully evaluating PCB fabrication services based on these key factors, you can make an informed decision that meets your project requirements and ensures the successful production of high-quality PCBs.
No responses yet