What is Quick Turn PCB Assembly?
Quick turn PCB assembly refers to the process of manufacturing PCBs in a short amount of time, typically within a few days to a week. This service is ideal for projects with tight deadlines or for prototyping purposes where multiple iterations may be required.
Benefits of Quick Turn PCB Assembly
There are several benefits to using a quick turn PCB assembly service, including:
-
Faster time-to-market: With quick turn PCB assembly, you can get your product to market faster, giving you a competitive edge.
-
Reduced costs: Quick turn PCB assembly can help reduce costs associated with inventory and storage, as you only need to order what you need when you need it.
-
Flexibility: Quick turn PCB assembly allows for greater flexibility in design changes and modifications, as you can quickly iterate on your design without incurring significant costs or delays.
Factors to Consider When Choosing a Quick Turn PCB Assembly Service
When choosing a quick turn PCB assembly service, there are several factors to consider, including:
1. Turnaround Time
One of the most important factors to consider when choosing a quick turn PCB assembly service is the turnaround time. Some services may offer 24-hour turnaround, while others may take up to a week. Consider your project timeline and choose a service that can meet your deadlines.
2. Quality
Another critical factor to consider is the quality of the PCBs produced by the assembly service. Look for a service that uses high-quality materials and has a proven track record of producing reliable PCBs. Ask for references and samples of their work to ensure they meet your quality standards.
3. Cost
Cost is always a consideration when choosing any service, and quick turn PCB assembly is no exception. However, it’s important to remember that the cheapest option may not always be the best. Consider the value you are getting for your money, including the quality of the PCBs, the turnaround time, and the level of customer service provided.
4. Capabilities
Different PCB assembly services may have different capabilities, such as the ability to handle different PCB sizes, materials, and components. Make sure the service you choose has the capabilities to handle your specific project requirements.
5. Customer Service
Finally, consider the level of customer service provided by the PCB assembly service. Look for a service that is responsive to your inquiries, provides clear communication, and is willing to work with you to ensure your project is a success.
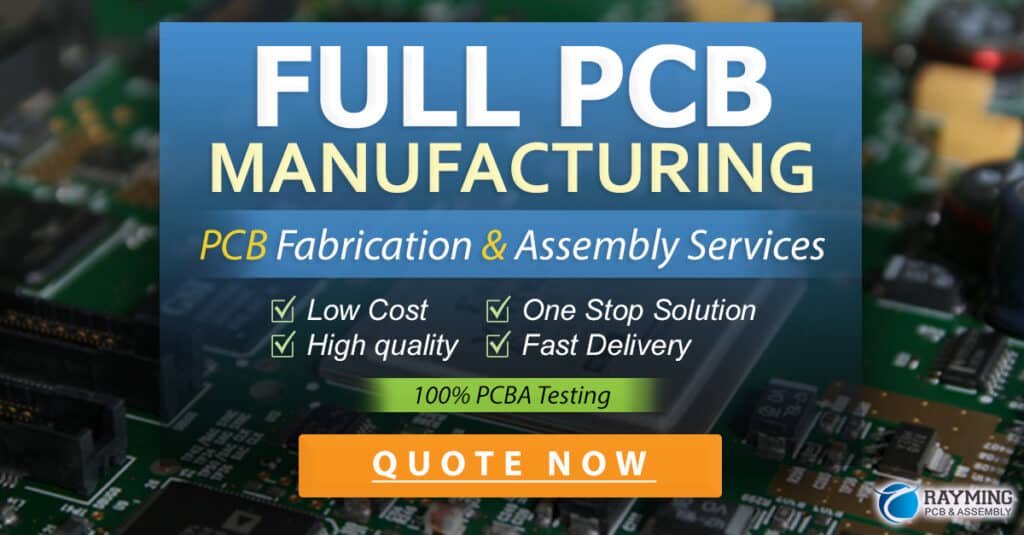
PCB Assembly Process
The PCB assembly process typically involves several steps, including:
-
Design: The first step in the PCB assembly process is to design the PCB using specialized software. This involves creating a schematic diagram and a PCB layout that specifies the location of all the components and the connections between them.
-
Fabrication: Once the design is complete, the PCB is fabricated using a variety of methods, such as etching, drilling, and plating. This process creates the physical board with all the necessary traces and pads for the components.
-
Component Placement: After the PCB is fabricated, the components are placed on the board using automated pick-and-place machines. These machines use computer vision and precision placement to ensure each component is placed accurately on the board.
-
Soldering: Once the components are placed, the board is sent through a soldering process to secure the components in place. This can be done using a variety of methods, such as wave soldering, reflow soldering, or hand soldering.
-
Inspection: After soldering, the PCB undergoes a thorough inspection to ensure all the connections are properly made and there are no defects or short circuits. This can be done using automated optical inspection (AOI) machines or manual inspection.
-
Testing: Finally, the PCB is tested to ensure it functions as intended. This can involve a variety of tests, such as functional testing, in-circuit testing, and boundary scan testing.
Step | Description |
---|---|
Design | Create a schematic diagram and PCB layout using specialized software |
Fabrication | Create the physical board with traces and pads using etching, drilling, and plating |
Component Placement | Place components on the board using automated pick-and-place machines |
Soldering | Secure components in place using wave soldering, reflow soldering, or hand soldering |
Inspection | Inspect the board for defects or short circuits using AOI machines or manual inspection |
Testing | Test the board for functionality using various testing methods |
Choosing the Right Components
When designing a PCB, it’s important to choose the right components for your specific application. Some factors to consider when choosing components include:
-
Functionality: Make sure the components you choose have the necessary functionality for your application. This includes factors such as voltage and current ratings, frequency response, and power dissipation.
-
Size: Consider the size of the components and how they will fit on the PCB. Smaller components can help reduce the overall size of the PCB, but may be more difficult to work with.
-
Cost: Consider the cost of the components and how they fit into your overall budget. While it may be tempting to choose the cheapest components available, this can often lead to reliability issues and increased costs in the long run.
-
Availability: Make sure the components you choose are readily available from your supplier. Long lead times or supply chain disruptions can significantly delay your project.
Common PCB Assembly Challenges
While the PCB assembly process has become increasingly automated and reliable in recent years, there are still several common challenges that can arise, including:
-
Solder Defects: Solder defects, such as bridging or insufficient solder, can lead to short circuits or poor connections between components. These defects can often be difficult to detect and can lead to reliability issues down the line.
-
Component Placement Errors: Automated pick-and-place machines are highly accurate, but errors can still occur, particularly with smaller or oddly-shaped components. These errors can lead to incorrect component placement or orientation, which can cause functionality issues.
-
Thermal Management: As PCBs become more complex and power-dense, thermal management becomes increasingly important. Overheating can lead to component failure and reduced reliability, so it’s important to design PCBs with appropriate thermal management techniques, such as heat sinks or cooling fans.
-
Electromagnetic Interference (EMI): EMI can cause signal interference and distortion, particularly in high-frequency applications. Proper PCB design techniques, such as ground planes and shielding, can help mitigate EMI issues.
FAQ
-
Q: How long does quick turn PCB assembly typically take?
A: Quick turn PCB assembly can take anywhere from 24 hours to a week, depending on the complexity of the board and the specific service provider. -
Q: What is the minimum order quantity for quick turn PCB assembly?
A: Minimum order quantities can vary depending on the service provider, but many offer low minimum order quantities (MOQs) for quick turn services, often as low as a single unit. -
Q: How much does quick turn PCB assembly cost?
A: The cost of quick turn PCB assembly can vary depending on the complexity of the board, the number of layers, and the specific service provider. In general, quick turn services may be more expensive than standard lead time services due to the expedited nature of the service. -
Q: What file formats are typically required for quick turn PCB assembly?
A: Most quick turn PCB assembly services require Gerber files, which are a standard file format used for PCB design. Some services may also accept other file formats, such as ODB++ or IPC-2581. -
Q: Can I get a prototype PCB assembled through a quick turn service?
A: Yes, many quick turn PCB assembly services specialize in prototype and low-volume production runs, making them ideal for prototyping and testing new designs.
Conclusion
Choosing the right quick turn PCB assembly service is critical for the success of your project. By considering factors such as turnaround time, quality, cost, capabilities, and customer service, you can find a service that meets your specific needs and expectations.
When designing your PCB, it’s important to choose the right components and consider common challenges such as solder defects, component placement errors, thermal management, and EMI. By working closely with your PCB assembly service provider and following best practices for PCB design, you can ensure a successful and reliable end product.
No responses yet