Understanding Motor Drives
What is a Motor Drive?
A motor drive, also known as a variable frequency drive (VFD) or adjustable speed drive (ASD), is an electronic device that controls the speed, torque, and direction of an electric motor. It converts the fixed voltage and frequency of the power supply into variable values, allowing precise control over the motor’s operation.
Types of Motor Drives
There are several types of motor drives available, each with its own characteristics and suitable applications:
-
AC Drives: These drives are used to control AC motors, such as induction motors and synchronous motors. They provide variable speed and torque control by adjusting the frequency and voltage of the power supply.
-
DC Drives: DC drives are used to control DC motors, offering precise speed and torque control. They regulate the voltage and current supplied to the motor to achieve the desired performance.
-
Servo Drives: Servo drives are designed for high-precision positioning and velocity control. They are commonly used in applications that require accurate and dynamic motion control, such as robotics and automation.
-
Stepper Drives: Stepper drives control Stepper Motors, which provide precise incremental motion. They are often used in applications that require accurate positioning, such as 3D printers and CNC machines.
Key Features of Motor Drives
When selecting a motor drive, consider the following key features:
Feature | Description |
---|---|
Power Rating | Ensure the drive has sufficient power capacity to handle the motor’s rated power and the application’s demands. |
Input Voltage | Choose a drive that is compatible with the available power supply voltage. |
Output Voltage and Frequency | The drive should provide the appropriate voltage and frequency range for the motor. |
Control Methods | Consider the required control methods, such as V/Hz, sensorless vector control, or field-oriented control. |
Communication Interfaces | Determine the necessary communication interfaces for integration with other systems, such as Modbus, Ethernet, or CANopen. |
Protection Features | Look for drives with built-in protection features, such as overcurrent, overvoltage, and overtemperature protection. |
User Interface | Consider the ease of use and programming capabilities of the drive’s user interface. |
Understanding Motor Controllers
What is a Motor Controller?
A motor controller is an electronic device that regulates the operation of an electric motor. It receives input signals and generates appropriate output signals to control the motor’s speed, direction, and torque. Motor controllers can be standalone units or integrated into a larger control system.
Types of Motor Controllers
There are various types of motor controllers available, depending on the motor type and application requirements:
-
Brushed DC Motor Controllers: These controllers are used to control brushed DC motors. They regulate the voltage and current supplied to the motor to control its speed and direction.
-
Brushless DC (BLDC) Motor Controllers: BLDC motor controllers are designed specifically for brushless DC motors. They provide commutation control and regulate the motor’s speed and torque.
-
AC Motor Controllers: AC motor controllers are used to control AC motors, such as induction motors and synchronous motors. They adjust the frequency and voltage of the power supply to control the motor’s speed and torque.
-
Stepper Motor Controllers: Stepper motor controllers are used to control stepper motors, providing precise position and speed control. They generate the necessary pulse sequences to drive the motor.
Key Features of Motor Controllers
When selecting a motor controller, consider the following key features:
Feature | Description |
---|---|
Motor Compatibility | Ensure the controller is compatible with the specific motor type and specifications. |
Current and Voltage Ratings | Choose a controller that can handle the motor’s rated current and voltage. |
Control Methods | Consider the required control methods, such as open-loop or closed-loop control, and the availability of feedback options. |
Programmability | Determine the programming capabilities and ease of use of the controller’s software or firmware. |
I/O Interfaces | Evaluate the available input and output interfaces for integration with sensors, encoders, and other devices. |
Protection Features | Look for controllers with built-in protection features, such as overcurrent, overvoltage, and thermal protection. |
Form Factor | Consider the physical size and mounting options of the controller to ensure compatibility with your system. |
Factors to Consider in Motor Selection
Application Requirements
The first step in selecting a motor drive and controller is to understand the specific requirements of your application. Consider the following factors:
- Load characteristics: Determine the torque, speed, and power requirements of the load.
- Motion profile: Define the desired motion profile, including acceleration, deceleration, and positioning accuracy.
- Environmental conditions: Consider the operating environment, such as temperature, humidity, and vibration.
- Safety and reliability: Evaluate the safety and reliability requirements of the application.
Motor Type and Specifications
Based on the application requirements, select the appropriate motor type and specifications:
- Motor type: Choose between AC motors (induction, synchronous) or DC motors (brushed, brushless).
- Power rating: Determine the required power rating of the motor based on the load requirements.
- Speed and torque characteristics: Consider the speed range and torque capabilities of the motor.
- Feedback options: Decide if feedback devices, such as encoders or resolvers, are necessary for position or speed control.
Power Supply
Consider the available power supply and ensure compatibility with the selected motor drive and controller:
- Voltage and frequency: Match the power supply voltage and frequency with the drive and motor specifications.
- Power capacity: Ensure the power supply has sufficient capacity to handle the motor’s power requirements.
- Power quality: Consider the power quality requirements, such as harmonic distortion and voltage fluctuations.
Control Methods
Choose the appropriate control methods based on the application’s performance and precision requirements:
- Open-loop control: Open-loop control methods, such as V/Hz control, are suitable for applications with less stringent speed and torque control requirements.
- Closed-loop control: Closed-loop control methods, such as vector control or field-oriented control, provide precise speed and torque control using feedback devices.
- Positioning control: For applications requiring accurate positioning, consider using servo drives and motors with position feedback.
Integration and Communication
Consider the integration and communication requirements of the motor drive and controller:
- Communication protocols: Determine the necessary communication protocols, such as Modbus, Ethernet, or CANopen, for integration with other systems.
- I/O interfaces: Evaluate the available input and output interfaces for connecting sensors, encoders, and other devices.
- Software and programming: Consider the software and programming tools provided by the drive and controller manufacturers for configuration and monitoring.
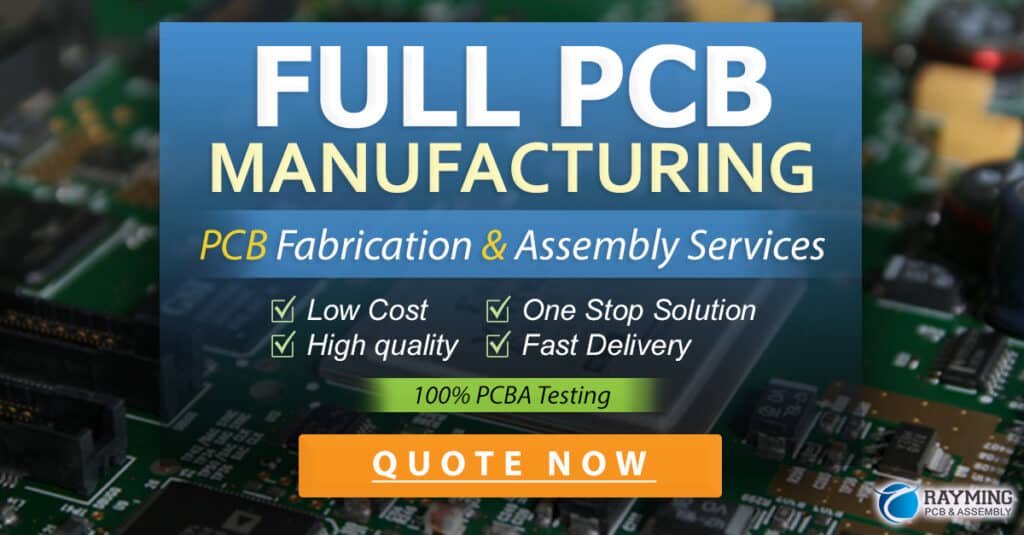
Sizing and Selection Process
Motor Sizing
Properly sizing the motor is crucial for optimal performance and efficiency. Follow these steps:
- Calculate the load torque and speed requirements.
- Determine the required power rating based on the load characteristics.
- Select a motor with a power rating that exceeds the calculated value by a safety margin (typically 10-20%).
- Verify that the motor’s speed and torque characteristics match the application requirements.
Drive and Controller Sizing
Once the motor is selected, size the drive and controller accordingly:
- Ensure the drive and controller have sufficient power capacity to handle the motor’s rated power.
- Verify that the drive and controller’s voltage and current ratings are compatible with the motor specifications.
- Consider the required control methods and ensure the drive and controller support them.
- Evaluate the drive and controller’s features, such as protection functions and communication interfaces, to meet the application requirements.
Simulation and Testing
Before finalizing the selection, it is recommended to perform simulations and testing to validate the system’s performance:
- Use simulation tools provided by the drive and controller manufacturers to model the system’s behavior.
- Conduct testing with the selected components to verify the performance and identify any potential issues.
- Optimize the system parameters, such as gains and limits, to achieve the desired performance.
FAQ
-
Q: What is the difference between a motor drive and a motor controller?
A: A motor drive is an electronic device that controls the speed, torque, and direction of an electric motor by converting the fixed voltage and frequency of the power supply into variable values. A motor controller, on the other hand, is a device that regulates the operation of an electric motor by receiving input signals and generating appropriate output signals to control the motor’s speed, direction, and torque. -
Q: How do I determine the power rating of the motor drive and controller?
A: The power rating of the motor drive and controller should be selected based on the motor’s rated power. Ensure that the drive and controller have sufficient power capacity to handle the motor’s power requirements, considering any safety margins. -
Q: What are the different control methods used in motor drives and controllers?
A: The common control methods used in motor drives and controllers include V/Hz control, sensorless vector control, field-oriented control, and closed-loop control with feedback devices. The choice of control method depends on the application’s performance and precision requirements. -
Q: How important is motor sizing in the selection process?
A: Proper motor sizing is crucial for optimal performance and efficiency. It involves calculating the load torque and speed requirements, determining the required power rating, and selecting a motor with a power rating that exceeds the calculated value by a safety margin. -
Q: What are the key factors to consider when integrating a motor drive and controller into a larger system?
A: When integrating a motor drive and controller into a larger system, consider the communication protocols, I/O interfaces, and software and programming tools provided by the manufacturers. Ensure compatibility with other system components and evaluate the ease of configuration and monitoring.
Conclusion
Selecting the right motor drive and motor controller is essential for achieving optimal performance and efficiency in your motion control system. By understanding the key aspects of motor drives, motor controllers, and the factors to consider in the selection process, you can make informed decisions tailored to your specific application requirements.
Remember to evaluate the application’s load characteristics, motor type and specifications, power supply, control methods, and integration requirements. Properly size the motor, drive, and controller, and perform simulations and testing to validate the system’s performance.
By following this comprehensive guide and considering the FAQs, you can confidently navigate the process of choosing a motor drive and motor controller that best suits your needs, ensuring reliable and efficient operation of your motion control system.
No responses yet