What is a BGA Rework Station?
A BGA rework station is a specialized machine used to remove and replace BGA components from printed circuit boards (PCBs). It typically consists of a heating element, a vacuum pickup tool, a vision system for alignment, and a control system to manage the rework process.
BGA rework stations come in various sizes and configurations to accommodate different types of BGA packages and PCB sizes. Some common features of BGA rework stations include:
- Precise temperature control
- Multiple heating zones
- Vision system for component alignment
- Vacuum pickup for component placement
- Adjustable air flow for even heating
- Automatic and manual modes of operation
Why Use a BGA Rework Station?
There are several reasons why you might need to use a BGA rework station:
-
Repairing Defective Components: If a BGA component fails or is found to be defective, it needs to be removed and replaced. A BGA rework station allows you to do this quickly and accurately.
-
Upgrading Components: As technology advances, you may need to upgrade BGA components on existing PCBs. A BGA rework station makes it easy to swap out old components for new ones.
-
Prototyping and Low-Volume Production: For prototyping and low-volume production runs, a BGA rework station provides a cost-effective alternative to full-scale SMT assembly lines.
-
Reworking Pb-Free Components: Lead-free (Pb-free) BGA components require higher reflow temperatures compared to leaded components. A BGA rework station with precise temperature control is essential for successful Pb-free rework.
Factors to Consider When Choosing a BGA Rework Station
When selecting a BGA rework station, there are several key factors to consider:
1. Package Size and Type
BGA packages come in various sizes and configurations, such as plastic BGA (PBGA), ceramic BGA (CBGA), and fine-pitch BGA (FBGA). Make sure the rework station you choose is compatible with the package types and sizes you work with.
2. PCB Size and Thickness
Consider the maximum PCB size and thickness that the rework station can accommodate. If you work with large or thick PCBs, make sure the machine has enough clearance and heating power to handle them.
3. Heating Method
BGA rework stations use different heating methods, such as infrared (IR), hot air, or a combination of both. IR heating provides faster ramp-up times but may not be suitable for all component types. Hot air heating offers more even heat distribution but may have slower ramp-up times. Consider the heating method that best suits your requirements.
4. Temperature Control
Precise temperature control is critical for successful BGA rework. Look for a station with accurate temperature sensors and closed-loop control to maintain stable temperatures throughout the reflow process. The ability to create and store custom temperature profiles is also useful.
5. Vision System
A high-quality vision system is essential for accurate component alignment. Look for a station with a high-resolution camera, adjustable lighting, and image processing software to ensure precise placement of components.
6. Ease of Use
Consider the user interface and ease of operation when selecting a BGA rework station. Look for features such as intuitive controls, clear displays, and software-guided workflows to simplify the rework process.
7. Automation Level
Decide on the level of automation you require. Fully automatic systems are more expensive but offer higher throughput and consistency. Semi-automatic systems provide a balance between operator control and automation. Manual systems are the most affordable but rely heavily on operator skill.
8. Accessories and Upgrades
Consider the available accessories and upgrade options for the rework station. Useful accessories include various nozzle sizes, component carriers, and thermal barriers. The ability to upgrade the machine with new features or capabilities in the future is also beneficial.
9. Price and Maintenance Costs
BGA rework stations range in price from a few thousand to tens of thousands of dollars. Consider your budget and the long-term costs of ownership, including maintenance, spare parts, and consumables.
10. Manufacturer Support and Training
Look for a reputable manufacturer that provides comprehensive technical support, training, and aftersales service. Having access to knowledgeable support staff and training resources can help you get the most out of your BGA rework station.
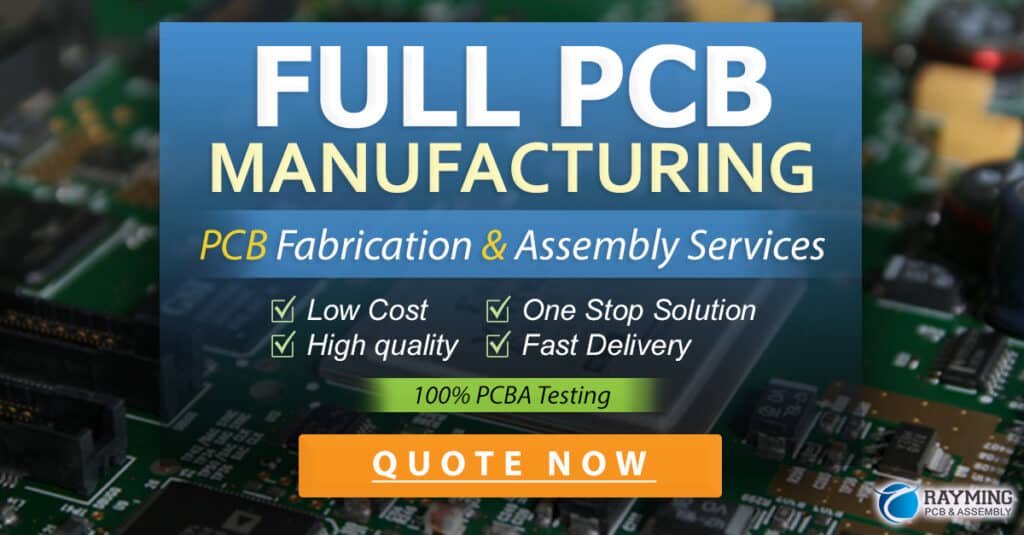
Top BGA Rework Station Brands
There are several well-known manufacturers of BGA rework stations, each with their own strengths and product offerings. Some of the top brands include:
Brand | Key Features |
---|---|
PACE | Widely used in the aerospace and defense industries. Known for high-quality systems with advanced process control. |
ZEPHYRTRONICS | Offers a range of manual to fully automatic systems. Specializes in systems for high-mix, low-volume production. |
SEAMARK | Provides affordable systems with user-friendly interfaces. Popular choice for small to medium-sized enterprises. |
HELLER | Offers high-end systems with advanced features such as multi-zone heating and automatic component alignment. |
MATRA | Known for compact, portable systems suitable for field service and repair applications. |
BGA Rework Station Setup and Operation
Once you have selected a BGA rework station, it is important to set it up correctly and follow proper operating procedures to ensure successful rework. Here are some general guidelines:
-
Workstation Setup: Position the rework station in a clean, static-free environment with good lighting and ventilation. Ensure that the machine is properly grounded and connected to a stable power supply.
-
Component Preparation: Clean the component and PCB pads to remove any dirt, debris, or oxidation. Apply flux to the pads to help with heat transfer and solder wetting.
-
Preheat: Preheat the PCB and component to the desired temperature using the bottom-side heater. This helps to minimize thermal shock and reduce the risk of component or PCB damage.
-
Component Removal: Use the top-side heater to reflow the solder joints and gently lift the component off the PCB using the vacuum pickup tool. Be careful not to apply excessive force or twisting motion, as this can damage the pads or neighboring components.
-
Site Cleaning: After removing the component, clean the PCB pads using a soldering iron and desoldering braid or a solder sucker. Make sure the pads are clean and level before installing the new component.
-
Component Placement: Apply solder paste or flux to the PCB pads. Place the new component using the vision system for alignment. Make sure the component is seated properly and the balls are aligned with the pads.
-
Reflow: Use the reflow profile recommended by the component manufacturer to heat the component and PCB. Monitor the temperature closely to ensure it stays within the specified range.
-
Inspection: After the reflow process is complete, visually inspect the solder joints for any defects such as bridging, insufficient wetting, or voids. Use a microscope or x-ray inspection system for more detailed analysis if needed.
Maintenance and Calibration
Regular maintenance and calibration are essential to keep your BGA rework station in top condition and ensure consistent results. Some key maintenance tasks include:
- Cleaning the machine and work area to remove flux residue, dust, and debris
- Inspecting and replacing worn or damaged parts such as nozzles, heaters, and thermocouples
- Calibrating the temperature sensors and vision system to maintain accuracy
- Updating the machine’s software and firmware as new versions become available
It is also a good idea to have the machine serviced periodically by a qualified technician to ensure optimal performance and catch any potential issues before they cause problems.
Frequently Asked Questions (FAQ)
-
What is the difference between a BGA rework station and a soldering iron?
A BGA rework station is a specialized machine designed for removing and installing BGA components, while a soldering iron is a handheld tool used for general soldering tasks. A BGA rework station provides precise temperature control, component alignment, and automated features that are essential for successful BGA rework. -
Can I use a hot air gun instead of a BGA rework station?
While a hot air gun can be used for some BGA rework tasks, it lacks the precision, control, and automation of a dedicated BGA rework station. Using a hot air gun increases the risk of component damage, PCB warping, and inconsistent results. For best results, it is recommended to use a BGA rework station specifically designed for the task. -
How much does a BGA rework station cost?
The cost of a BGA rework station varies depending on the features, automation level, and brand. Entry-level manual systems can cost a few thousand dollars, while high-end fully automatic systems can cost tens of thousands of dollars. When considering the cost, it is important to factor in the long-term benefits of improved rework quality, productivity, and reduced scrap rates. -
What training is required to operate a BGA rework station?
While BGA rework stations are designed to be user-friendly, some training is recommended to ensure optimal results and avoid costly mistakes. Many manufacturers offer training courses or video tutorials to help operators familiarize themselves with the machine’s features and best practices for BGA rework. It is also beneficial to have a basic understanding of electronics manufacturing principles and soldering techniques. -
Can I rework other types of components with a BGA rework station?
While BGA rework stations are primarily designed for BGA components, they can often be used for other types of surface mount components such as QFNs, LGAs, and SMDs. However, the specific capabilities and accessories required may vary depending on the component type and size. It is best to consult with the manufacturer or a technical expert to determine the feasibility of reworking other component types with your specific machine.
Conclusion
Choosing the right BGA rework station is essential for any electronics manufacturing or repair facility that works with BGA components. By considering factors such as package size and type, PCB size and thickness, heating method, temperature control, vision system, ease of use, automation level, accessories and upgrades, price and maintenance costs, and manufacturer support and training, you can select a machine that meets your specific needs and budget.
Proper setup, operation, and maintenance of your BGA rework station are also critical to ensure consistent, high-quality results and maximize the lifespan of your machine. By following best practices and staying up to date with the latest techniques and technologies, you can achieve successful BGA rework and improve your overall electronics manufacturing and repair capabilities.
No responses yet