Introduction to Signal-Layer Bonding in 10 Layer PCBs
Signal-layer bonding is a crucial process in the manufacturing of high-density, multi-layer printed circuit boards (PCBs), particularly in 10 layer PCBs. As the demand for more complex and compact electronic devices grows, the need for reliable and efficient signal-layer bonding techniques becomes increasingly important. In this article, we will explore the various methods and best practices for bonding the signal layers of 10 layer PCBs, ensuring optimal performance and reliability.
What is a 10 Layer PCB?
A 10 layer PCB is a complex, multi-layer printed circuit board that consists of ten conductive copper layers separated by insulating dielectric materials. These layers are strategically arranged to accommodate the intricate circuitry required for advanced electronic applications, such as high-speed communication systems, aerospace equipment, and medical devices.
The typical structure of a 10 layer PCB includes:
- Top and bottom signal layers
- Power and ground planes
- Inner signal layers
- Dielectric layers separating each conductive layer
The Importance of Signal-Layer Bonding
Signal-layer bonding is the process of joining the conductive copper layers of a multi-layer PCB to ensure proper electrical connectivity and signal integrity. In 10 layer PCBs, the signal layers are responsible for carrying critical electrical signals between components, making their bonding a key factor in the overall performance and reliability of the circuit board.
Proper signal-layer bonding offers several benefits:
-
Improved signal integrity: Well-bonded signal layers minimize signal loss, distortion, and interference, ensuring that electrical signals are transmitted accurately and efficiently.
-
Enhanced mechanical strength: Effective bonding techniques provide structural stability to the PCB, making it more resistant to physical stress and vibration.
-
Increased reliability: Robust signal-layer bonding reduces the risk of delamination, a common failure mode in multi-layer PCBs, thus improving the overall reliability of the circuit board.
-
Better thermal management: Proper bonding helps dissipate heat evenly across the PCB, preventing localized hot spots and thermal stress that can lead to component failure.
Signal-Layer Bonding Techniques for 10 Layer PCBs
There are several methods for bonding the signal layers of 10 layer PCBs, each with its own advantages and limitations. The choice of bonding technique depends on various factors, such as the materials used, the desired performance characteristics, and the manufacturing capabilities.
1. Adhesive Bonding
Adhesive bonding is a widely used method for joining the signal layers of multi-layer PCBs. This technique involves applying a thin layer of adhesive material between the conductive copper layers and the insulating dielectric layers. The adhesive is then cured using heat and pressure, creating a strong bond between the layers.
Advantages of adhesive bonding:
- Relatively simple and cost-effective process
- Suitable for a wide range of materials
- Provides good insulation properties
Limitations of adhesive bonding:
- Possible outgassing during the curing process
- Limited thermal conductivity compared to other methods
- Potential for voids or uneven distribution of the adhesive
2. Fusion Bonding
Fusion bonding, also known as direct bonding, is a technique that involves directly bonding the copper layers to the dielectric layers without the use of an adhesive. This method relies on the application of heat and pressure to create a strong, seamless bond between the layers.
Advantages of fusion bonding:
- Eliminates the need for adhesives, reducing the risk of outgassing and contamination
- Provides excellent thermal conductivity
- Enables thinner dielectric layers, allowing for more compact PCB designs
Limitations of fusion bonding:
- Requires specialized equipment and precise process control
- Limited material compatibility compared to adhesive bonding
- Higher initial investment costs
3. Lamination
Lamination is a process that combines adhesive bonding and fusion bonding techniques to create a multi-layer PCB. In this method, the copper and dielectric layers are alternately stacked and then subjected to heat and pressure in a lamination press. The heat and pressure activate the adhesive and fuse the layers together, forming a solid, unified structure.
Advantages of lamination:
- Combines the benefits of both adhesive and fusion bonding
- Suitable for a wide range of materials
- Provides good mechanical strength and thermal conductivity
Limitations of lamination:
- Requires careful control of the lamination process parameters
- Potential for layer misalignment or registration issues
- Higher equipment and tooling costs compared to adhesive bonding
Best Practices for Signal-Layer Bonding in 10 Layer PCBs
To ensure optimal signal-layer bonding in 10 layer PCBs, consider the following best practices:
-
Material selection: Choose compatible copper and dielectric materials that have similar thermal expansion coefficients to minimize stress and delamination risk.
-
Surface preparation: Ensure that the copper and dielectric surfaces are clean, smooth, and free of contaminants before bonding to promote strong adhesion.
-
Process control: Strictly monitor and control the bonding process parameters, such as temperature, pressure, and duration, to achieve consistent and reliable results.
-
Design for manufacturability: Incorporate design features that facilitate proper layer alignment and registration, such as fiducial marks and guide pins.
-
Quality inspection: Implement rigorous quality control measures, including visual inspection, cross-sectional analysis, and electrical testing, to detect and address any bonding defects early in the manufacturing process.
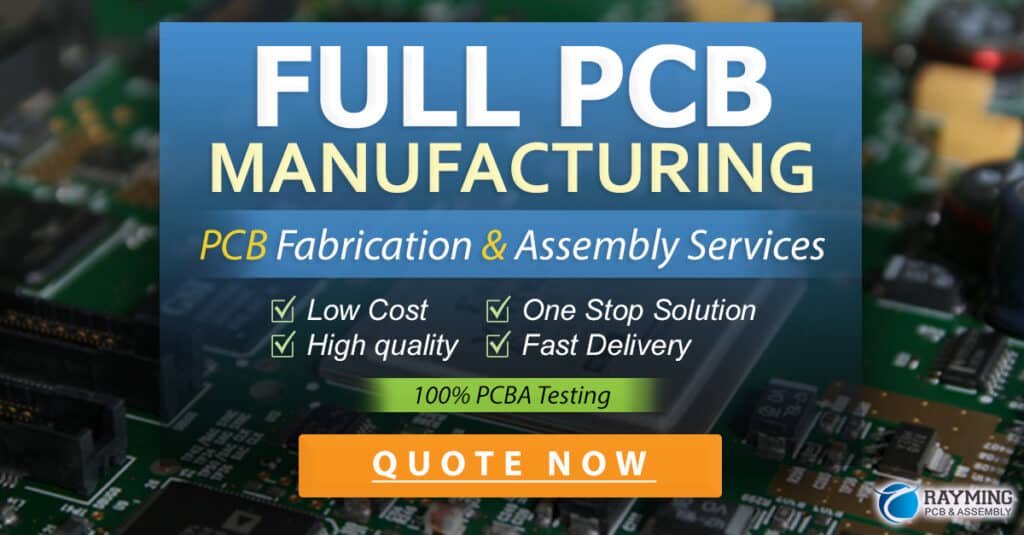
Frequently Asked Questions (FAQ)
-
What is the primary purpose of signal-layer bonding in 10 layer PCBs?
Signal-layer bonding ensures proper electrical connectivity and signal integrity between the conductive copper layers of a 10 layer PCB, enabling the accurate and efficient transmission of electrical signals between components. -
What are the most common signal-layer bonding techniques for 10 layer PCBs?
The most common signal-layer bonding techniques for 10 layer PCBs are adhesive bonding, fusion bonding, and lamination. Each method has its own advantages and limitations, and the choice depends on factors such as materials, performance requirements, and manufacturing capabilities. -
How does proper signal-layer bonding affect the overall performance and reliability of a 10 layer PCB?
Proper signal-layer bonding improves signal integrity, enhances mechanical strength, increases reliability, and enables better thermal management in a 10 layer PCB. Well-bonded signal layers minimize signal loss, distortion, and interference, while also reducing the risk of delamination and other failure modes. -
What are some best practices for achieving optimal signal-layer bonding in 10 layer PCBs?
Best practices for achieving optimal signal-layer bonding in 10 layer PCBs include selecting compatible materials, ensuring proper surface preparation, strictly controlling the bonding process parameters, designing for manufacturability, and implementing rigorous quality inspection measures. -
How can manufacturers address common issues related to signal-layer bonding in 10 layer PCBs?
Manufacturers can address common issues related to signal-layer bonding in 10 layer PCBs by investing in advanced bonding equipment, regularly maintaining and calibrating the equipment, providing thorough training to personnel, and continuously monitoring and optimizing the bonding process. Additionally, collaborating with experienced PCB design and materials experts can help identify and resolve potential issues early in the development process.
Conclusion
Signal-layer bonding is a critical process in the manufacturing of 10 layer PCBs, directly impacting the performance, reliability, and longevity of these complex circuit boards. By understanding the various bonding techniques, their advantages and limitations, and adhering to best practices, manufacturers can ensure optimal signal-layer bonding and deliver high-quality 10 layer PCBs for demanding electronic applications.
As the electronics industry continues to evolve and push the boundaries of PCB technology, the importance of effective signal-layer bonding will only grow. By staying informed about the latest advancements in materials, processes, and equipment, manufacturers can remain competitive and meet the ever-increasing demands for high-performance, reliable, and compact electronic devices.
No responses yet