The Rise of IoT in Electronics Manufacturing
IoT has emerged as a game-changer in the electronics manufacturing industry, enabling the creation of smart, connected devices that can communicate and exchange data seamlessly. The integration of IoT technology has led to the development of innovative products and services, such as smart home appliances, wearable devices, and industrial automation systems.
Benefits of IoT in Electronics Manufacturing
-
Enhanced Efficiency and Productivity: IoT enables real-time monitoring and control of manufacturing processes, leading to improved efficiency and productivity. Manufacturers can collect and analyze data from connected devices and sensors to optimize production lines, reduce downtime, and minimize waste.
-
Predictive Maintenance: IoT sensors can monitor the health and performance of manufacturing equipment, enabling predictive maintenance. By analyzing data patterns and identifying potential issues before they occur, manufacturers can schedule maintenance proactively, reducing unplanned downtime and improving overall equipment effectiveness (OEE).
-
Improved Quality Control: IoT-enabled quality control systems can detect defects and anomalies in real-time, ensuring that only high-quality products leave the production line. By integrating IoT sensors and machine vision technology, manufacturers can automate quality inspections and reduce the risk of human error.
-
Customization and Personalization: IoT enables manufacturers to offer customized and personalized products to meet individual customer preferences. By leveraging data collected from connected devices, manufacturers can gain insights into consumer behavior and preferences, allowing them to tailor their offerings accordingly.
-
Supply Chain Optimization: IoT can streamline supply chain operations by providing real-time visibility into inventory levels, shipment tracking, and demand forecasting. By integrating IoT sensors and RFID technology, manufacturers can optimize inventory management, reduce stockouts, and improve overall supply chain efficiency.
Challenges and Considerations
While IoT offers numerous benefits to the electronics manufacturing industry, it also presents several challenges and considerations:
-
Data Security and Privacy: IoT devices generate vast amounts of data, raising concerns about data security and privacy. Manufacturers must implement robust security measures to protect sensitive information and prevent unauthorized access to connected devices.
-
Interoperability and Standards: The lack of standardization in IoT protocols and communication standards can hinder interoperability between devices from different manufacturers. Establishing industry-wide standards is crucial to ensure seamless integration and compatibility.
-
Skill Gap and Workforce Training: Implementing IoT in electronics manufacturing requires a skilled workforce with expertise in IoT technologies, data analytics, and cybersecurity. Manufacturers must invest in training and upskilling programs to bridge the skill gap and ensure a competent workforce.
-
Infrastructure and Connectivity: Reliable and robust network infrastructure is essential for the successful implementation of IoT in manufacturing. Manufacturers must ensure adequate connectivity, bandwidth, and edge computing capabilities to support the seamless flow of data between devices and systems.
IoT Applications in Electronics Manufacturing
IoT has found numerous applications in the electronics manufacturing industry, transforming various aspects of the production process. Let’s explore some key areas where IoT is making a significant impact:
Smart Factory and Industry 4.0
IoT is a key enabler of the smart factory concept, also known as Industry 4.0. Smart factories leverage IoT technologies to create a fully connected and automated manufacturing environment. By integrating IoT sensors, robotics, and artificial intelligence (AI), smart factories can optimize production processes, improve quality control, and enhance overall efficiency.
Technology | Application in Smart Factory |
---|---|
IoT Sensors | Real-time monitoring of equipment, environment, and processes |
Robotics | Automated assembly, material handling, and quality inspection |
AI and Machine Learning | Predictive maintenance, process optimization, and anomaly detection |
Cloud Computing | Data storage, analysis, and remote monitoring |
Asset Tracking and Inventory Management
IoT-enabled asset tracking and inventory management systems can significantly improve supply chain visibility and efficiency. By attaching IoT sensors or RFID tags to raw materials, components, and finished products, manufacturers can track their location, movement, and usage in real-time. This data can be used to optimize inventory levels, prevent stockouts, and streamline logistics operations.
Technology | Application in Asset Tracking and Inventory Management |
---|---|
RFID | Automatic identification and tracking of items |
GPS and Beacons | Real-time location tracking of assets and shipments |
IoT Sensors | Monitoring environmental conditions (temperature, humidity) |
Cloud Platforms | Centralized data storage and analysis for inventory management |
Predictive Maintenance and Equipment Monitoring
IoT sensors embedded in manufacturing equipment can continuously monitor their performance, health, and usage patterns. By analyzing this data using AI and machine learning algorithms, manufacturers can predict potential failures and schedule maintenance proactively. Predictive maintenance helps reduce unplanned downtime, extend equipment lifespan, and optimize maintenance costs.
Technology | Application in Predictive Maintenance |
---|---|
Vibration Sensors | Detecting abnormal vibrations indicating potential failures |
Temperature Sensors | Monitoring equipment temperature to prevent overheating |
Pressure Sensors | Monitoring fluid pressure in hydraulic systems |
AI and Machine Learning | Analyzing sensor data to predict failures and optimize maintenance schedules |
Quality Control and Inspection
IoT-enabled quality control systems can automate the inspection process and improve the accuracy of defect detection. By integrating IoT sensors, machine vision cameras, and AI algorithms, manufacturers can detect anomalies, inconsistencies, and defects in real-time. This helps reduce scrap, rework, and customer returns, ultimately improving product quality and customer satisfaction.
Technology | Application in Quality Control and Inspection |
---|---|
Machine Vision Cameras | Automated visual inspection of products and components |
IoT Sensors | Monitoring process parameters (temperature, pressure, speed) |
AI and Machine Learning | Analyzing sensor data to detect anomalies and defects |
Cloud Platforms | Storing and analyzing quality data for continuous improvement |
Future Trends and Innovations
As IoT continues to evolve, several trends and innovations are shaping the future of the electronics manufacturing industry:
-
5G and Edge Computing: The advent of 5G networks and edge computing will enable faster data transmission, lower latency, and real-time processing of IoT data. This will unlock new possibilities for remote monitoring, control, and automation in manufacturing.
-
Digital Twin Technology: Digital twins, virtual replicas of physical assets or processes, will become increasingly prevalent in electronics manufacturing. By creating digital twins of products, production lines, and supply chains, manufacturers can simulate and optimize processes, predict performance, and make data-driven decisions.
-
Augmented Reality (AR) and Virtual Reality (VR): AR and VR technologies will revolutionize training, maintenance, and remote collaboration in manufacturing. Technicians can use AR-enabled devices to access real-time instructions and guidance, while VR can be used for immersive training and virtual prototyping.
-
Blockchain Integration: Blockchain technology can enhance supply chain transparency, traceability, and security in electronics manufacturing. By creating a tamper-proof and decentralized ledger of transactions, blockchain can ensure the authenticity of components, prevent counterfeiting, and facilitate secure data sharing among stakeholders.
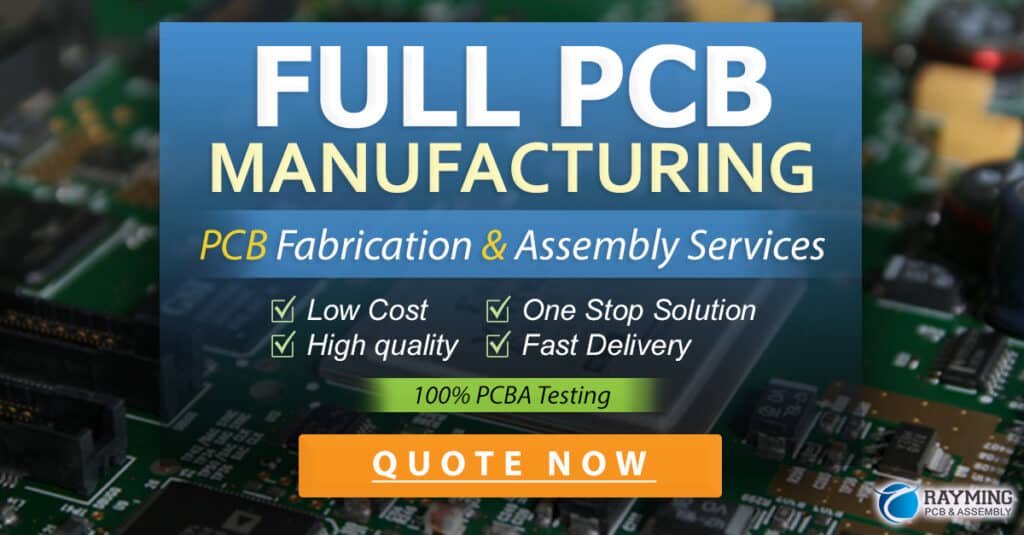
Frequently Asked Questions (FAQ)
-
What is the Internet of Things (IoT)?
The Internet of Things (IoT) refers to the network of connected devices, sensors, and objects that can communicate and exchange data over the internet. IoT enables devices to collect and share data, leading to improved efficiency, automation, and decision-making. -
How does IoT benefit the electronics manufacturing industry?
IoT offers several benefits to the electronics manufacturing industry, including enhanced efficiency and productivity, predictive maintenance, improved quality control, customization and personalization, and supply chain optimization. IoT enables real-time monitoring, data-driven insights, and automation, leading to improved manufacturing processes and outcomes. -
What are some key IoT applications in electronics manufacturing?
IoT has various applications in electronics manufacturing, including smart factories and Industry 4.0, asset tracking and inventory management, predictive maintenance and equipment monitoring, and quality control and inspection. IoT technologies such as sensors, robotics, AI, and machine learning are used to optimize production processes, improve quality, and streamline operations. -
What challenges does the electronics manufacturing industry face in adopting IoT?
The adoption of IoT in electronics manufacturing poses challenges such as data security and privacy concerns, interoperability and standardization issues, skill gaps and workforce training requirements, and infrastructure and connectivity limitations. Addressing these challenges is crucial for the successful implementation of IoT in manufacturing. -
What future trends and innovations are expected in IoT for electronics manufacturing?
The future of IoT in electronics manufacturing is shaped by trends such as 5G and edge computing, digital twin technology, augmented reality (AR) and virtual reality (VR), and blockchain integration. These innovations will enable faster data processing, virtual simulations, immersive experiences, and enhanced supply chain transparency and security.
Conclusion
The Internet of Things (IoT) has transformed the electronics manufacturing industry, enabling smart, connected, and data-driven manufacturing processes. IoT technologies such as sensors, robotics, AI, and machine learning have revolutionized various aspects of manufacturing, from smart factories and predictive maintenance to quality control and supply chain optimization.
While the adoption of IoT in electronics manufacturing offers numerous benefits, it also presents challenges related to data security, interoperability, skill gaps, and infrastructure. As IoT continues to evolve, emerging trends such as 5G, edge computing, digital twins, AR/VR, and blockchain will shape the future of the industry.
To stay competitive and leverage the full potential of IoT, electronics manufacturers must embrace digital transformation, invest in workforce training, and collaborate with technology partners to implement IoT solutions effectively. By doing so, they can unlock new opportunities for innovation, efficiency, and growth in the ever-evolving landscape of electronics manufacturing.
No responses yet