What is IoT in Manufacturing?
IoT in manufacturing refers to the use of smart, connected devices and sensors to digitize, automate, and optimize production processes. By connecting machines, equipment, products, and even entire factories to the internet, manufacturers can collect and analyze vast amounts of real-time data to gain unprecedented visibility and control over their operations.
IoT devices in manufacturing can include:
– Smart sensors that monitor machine performance, product quality, and environmental conditions
– Connected robots and automated guided vehicles (AGVs)
– Wearables for workers to enhance safety and productivity
– RFID tags and readers for asset tracking and inventory management
– Industrial gateways and edge computing devices for local data processing
When these IoT devices are integrated with advanced technologies like cloud computing, big data analytics, and artificial intelligence (AI), they form powerful Industry 4.0 solutions that are driving the next wave of manufacturing innovation.
Key Benefits of IoT in Manufacturing
Implementing IoT technology delivers a host of compelling benefits for manufacturers:
Benefit | Description |
---|---|
Operational efficiency | IoT enables manufacturers to streamline processes, minimize downtime, and optimize asset utilization, resulting in significant efficiency gains. |
Cost savings | By improving efficiency and catching issues sooner, IoT helps reduce operating costs related to labor, energy consumption, and maintenance. |
Product quality | IoT sensors can closely monitor production to identify and correct quality issues in real-time, ensuring higher and more consistent quality. |
Worker safety | Wearables and environmental sensors help keep workers safe by monitoring for hazardous conditions and alerting of potential dangers. |
Supply chain visibility | IoT solutions provide real-time visibility into inventory levels, shipments, and supplier activities to optimize the supply chain. |
Time-to-market | Accelerated product development timelines thanks to streamlined processes and early detection of design issues. |
Customization | IoT enables cost-effective, automated mass customization of products to meet individual customer needs. |
With such powerful benefits, it’s no surprise that IoT adoption in manufacturing is rapidly accelerating. The number of connected devices in the industrial manufacturing sector is expected to double from 2017 to 2020.
Key Applications of IoT in Manufacturing
So how are manufacturers actually using IoT to transform their operations? Here are some of the key applications:
Predictive Maintenance
One of the most impactful applications of industrial IoT is predictive maintenance. Smart sensors continuously monitor the condition and performance of production assets to detect potential issues before they result in costly unplanned downtime. Advanced AI algorithms analyze the sensor data in real-time to predict when maintenance will be needed based on factors like vibration, temperature, and runtime.
Armed with these AI-driven insights, manufacturers can optimize their maintenance schedules and replace parts proactively to maximize equipment uptime and useful life. Studies have found that predictive maintenance can reduce machine downtime by 30-50% and increase machine life by 20-40%.
Connected Factory
IoT is also enabling manufacturers to create fully connected, self-optimizing “smart factories.” By connecting machines and other assets across the factory floor, manufacturers gain real-time visibility into every aspect of the production process.
Factory workers are equipped with mobile devices and wearables to connect them to the production line. Environmental sensors monitor the factory conditions to ensure optimal settings. All of this IoT data is collected and analyzed by a centralized factory management platform to orchestrate and optimize the entire operation.
The results are powerful. Smart factories can operate with much greater flexibility and agility, seamlessly adapting production to changes in demand or conditions. Overall equipment effectiveness (OEE) increases while cycle times shrink. Product defects and waste are minimized. Ultimately, the connected factory makes it possible to achieve the long-sought goals of “just in time” and “lot size one” manufacturing.
Automated Quality Assurance
Ensuring consistent, high quality products is an essential task for any manufacturer. Here too, IoT is providing a major assist. Connected cameras and sensors can monitor products at every stage of the manufacturing process, spotting defects in real-time and enabling much faster root cause analysis and corrective action.
In addition to visual inspection, IoT quality assurance solutions also typically incorporate non-visual sensors (e.g. weight, conductivity) as well as functionality tests conducted by connected devices. All inspection data is fed into an AI-powered quality management system that ensures only products meeting specifications make it through to the end customer.
The impact of IoT-based quality assurance is substantial. Defect rates can be reduced by 90%, leading to multi-million dollar annual savings for large manufacturers. And by reducing defects and warranty claims, IoT helps protect the brand’s quality reputation.
Connected Worker
While much of the discussion around industrial IoT focuses on machines and automation, the technology is also transforming the role of human workers on the factory floor. IoT-enabled connected worker solutions equip factory workers with an array of smart devices and wearables – smart glasses, mobile devices, smartwatches, location badges, etc. – to augment and enhance their work.
These connected worker devices can deliver information and guidance to help workers complete tasks faster and more accurately – step-by-step visual instructions, checklists, diagrams and other AR content. The devices also capture data on worker activities to optimize training, workflows, and ergonomics.
From a safety perspective, wearables monitor worker health metrics and alert of any dangers, while location tracking ensures workers are only accessing equipment they are authorized and trained for. The end result is a more skilled, productive and safe manufacturing workforce empowered by IoT technology.
Adaptive Robotics
As costs have fallen and capabilities advanced, connected robots have found rapidly increasing adoption in manufacturing environments. Industrial IoT robotics solutions go beyond traditional single-purpose robots to create flexible, adaptive robotics systems that can be quickly trained and deployed for a variety of applications.
Using machine learning and computer vision, these robotic systems can adapt to real-world variability and learn by example. A factory worker can train a robot simply by walking it through a task, rather than requiring specialized programming. The robot’s learning is then shared with a network of connected robots.
These adaptive IoT robotics solutions dramatically lower the cost and expertise barriers to implementing automation for manufacturing tasks. Manufacturers can deploy flexible, multi-purpose robots that can be efficiently re-trained and re-deployed as needs change. IoT is making robotics accessible and cost-effective for manufacturers of all sizes.
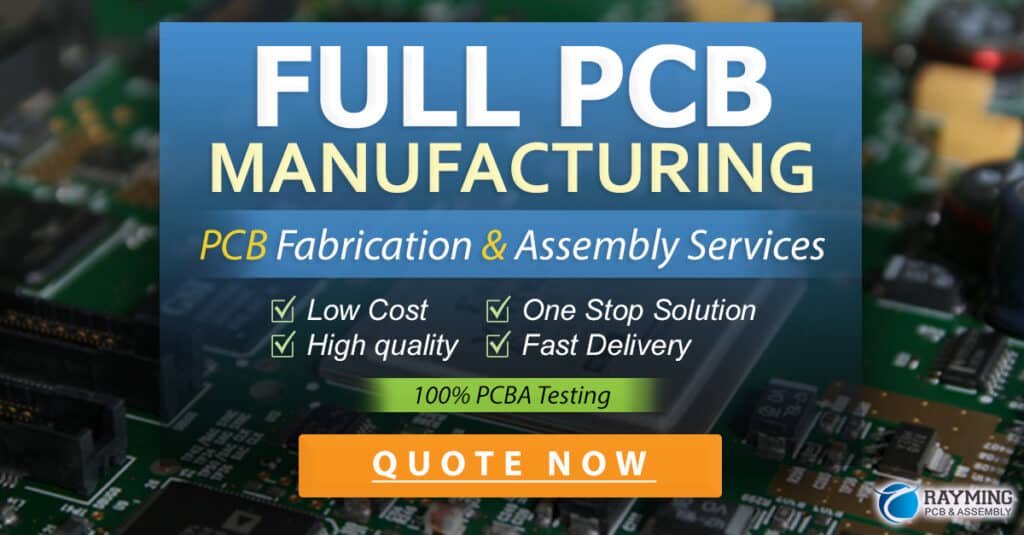
Challenges of Industrial IoT Adoption
While the benefits of IoT in manufacturing are clear, there are also challenges manufacturers must navigate in adopting the technology:
Challenge | Description |
---|---|
Integration with legacy systems | Most manufacturers have extensive legacy equipment and systems that were not designed for IoT connectivity. Integrating these assets can be complex and costly. |
Data security concerns | With so many connected devices and vast amounts of data, IoT significantly expands the attack surface for cyber threats. Robust security is essential. |
Finding the right talent | Implementing industrial IoT requires specialized skills in areas like data science, cybersecurity, and AI that many manufacturers lack. |
Difficulty proving ROI | Manufacturers may struggle to build a compelling business case and ROI model for IoT investments, slowing adoption. |
Keeping pace with rapid change | IoT technologies and use cases are evolving at a breakneck pace, making it difficult for manufacturers to keep up. |
Despite these challenges, IoT adoption in manufacturing continues to accelerate as more and more companies recognize that the technology is crucial to their future competitiveness. With the right strategies, partners, and best practices, manufacturing leaders can harness the power of IoT to drive operational excellence and business success.
Industrial IoT Success Stories
Many manufacturers are already realizing significant value from their IoT initiatives. Here are a few notable examples:
-
BMW: The automaker has implemented IoT and Industry 4.0 technologies across its factories worldwide. At its plant in Regensburg, Germany, an IoT platform connects 2,000 machines and 4,000 devices, enabling predictive maintenance that has reduced downtime by 80%.
-
Airbus: The aerospace giant has deployed a factory-wide IoT solution incorporating robots, AGVs, and smart tools to streamline aircraft assembly. The solution has reduced production time by 30% and inspection time by 60%.
-
Hitachi: Hitachi has harnessed the power of IoT and AI to create its “Lumada” industrial IoT platform. The platform has delivered powerful results, including a 5% productivity improvement and 8% reduction in manufacturing defects for Hitachi’s own factories.
-
Brembo: The high-performance brake manufacturer has created a fully IoT-enabled “factory of the future” in Italy. Leveraging connected equipment and AI, the factory can automatically configure itself to produce any brake disc model on demand, reducing production time by over 50%.
These are just a few examples of how manufacturing leaders are driving transformative impact with IoT technology today. As IoT continues to advance and adoption grows, we can expect to see many more such success stories in the years ahead.
The Future of IoT in Manufacturing
Looking ahead, the potential of IoT in manufacturing is truly limitless. As 5G networks enable even faster, more reliable connectivity and edge computing brings more processing power directly to the factory floor, manufacturers will be able to realize IoT use cases that are impossible today.
In the factory of the future, pervasive IoT connectivity and AI will make it possible to achieve true lights-out manufacturing – fully automated production that can run 24×7 with minimal human intervention. IoT will also merge the physical and digital worlds in manufacturing, enabling innovations like digital twins – real-time virtual replicas of physical assets that can be used to optimize designs and processes.
At the same time, the boundary between the factory and the rest of the supply chain will continue to blur as IoT enables seamless, real-time connectivity and collaboration across the extended manufacturing ecosystem. Ultimately, IoT is paving the way for the emergence of the autonomous, self-organizing factory that can operate with unprecedented efficiency, agility, and resilience.
Of course, realizing this future will require manufacturing leaders to continue to push the boundaries of IoT capabilities while also collaborating to address challenges around security, interoperability, and workforce skills gaps. But one thing is certain: IoT will continue to be a driving force in shaping the future of manufacturing in the years and decades to come.
FAQ
What is the Industrial Internet of Things (IIoT)?
The Industrial Internet of Things, or IIoT, refers to the application of IoT technologies in industrial and manufacturing environments. IIoT involves connecting industrial assets like machines, tools, and products to collect and analyze data to optimize operations.
How does IoT help with supply chain management?
IoT solutions provide real-time visibility across the entire supply chain, from raw materials to finished products. By tracking the location and condition of goods and assets, IoT helps manufacturers optimize inventory levels, improve demand forecasting, and proactively address supply chain disruptions.
Is IoT secure in manufacturing settings?
Robust security is absolutely critical for any industrial IoT deployment given the sensitivity of the data involved and the potential impact of breaches. Manufacturers must implement a rigorous, multi-layered cybersecurity strategy spanning devices, networks, applications, and data. Key measures can include device authentication, data encryption, network segmentation, and continuous security monitoring.
What skills are needed for industrial IoT?
Succeeding with industrial IoT requires a range of specialized skills, including:
- IoT architecture and engineering
- Data science and analytics
- AI and machine learning
- Cybersecurity
- Domain expertise in areas like manufacturing processes and automation
Many manufacturers will need to invest in upskilling their existing workforce and attracting new talent to assemble the right capabilities for IoT success.
How do I get started with IoT in my manufacturing organization?
The key steps to get started with an industrial IoT initiative are:
- Identify a high-impact use case to start with
- Assess your IoT readiness and identify capability gaps
- Build the business case and secure stakeholder buy-in
- Create a phased roadmap for implementation
- Establish partnerships with experienced IoT providers
- Start with a focused pilot to prove value before scaling
With the right approach and expert guidance, any manufacturer can begin harnessing the transformative power of IoT.
No responses yet