Understanding temperature correction
What is Temperature Correction?
Temperature correction refers to the process of adjusting measured values to compensate for the effects of temperature variations on the accuracy of the measurement. Many physical properties and measurements are sensitive to temperature changes, and failing to account for these variations can lead to significant errors in the obtained results.
Why is Temperature Correction Important?
Temperature correction is essential for several reasons:
-
Accuracy: Temperature variations can introduce errors in measurements, leading to inaccurate results. By applying temperature correction, the accuracy of the measurements can be significantly improved.
-
Consistency: Temperature correction ensures that measurements taken at different temperatures can be directly compared and analyzed without the need for additional adjustments.
-
Reliability: Correcting for temperature variations enhances the reliability of the measured data, making it more trustworthy for decision-making and further analysis.
-
Compliance: In many industries, such as pharmaceuticals and food processing, temperature correction is mandatory to meet regulatory requirements and quality standards.
Methods of Temperature Correction
There are several methods used for temperature correction, each with its own advantages and limitations. Let’s explore some of the commonly used techniques.
Linear Temperature Correction
Linear temperature correction assumes that the relationship between the measured value and temperature is linear. It involves applying a correction factor based on the temperature difference between the measurement condition and a reference temperature.
The linear temperature correction formula is as follows:
Corrected Value = Measured Value + Correction Factor × (Measurement Temperature - Reference Temperature)
For example, consider a pressure gauge that measures 100 psi at 25°C, with a correction factor of 0.1 psi/°C. If the measurement is taken at 30°C, the corrected value would be:
Corrected Pressure = 100 psi + 0.1 psi/°C × (30°C - 25°C) = 100.5 psi
Linear temperature correction is simple to implement and works well for small temperature ranges where the relationship between the measured value and temperature is approximately linear.
Polynomial Temperature Correction
In some cases, the relationship between the measured value and temperature is not linear, and a more complex correction method is required. Polynomial temperature correction involves using a higher-order polynomial equation to describe the relationship between the measured value and temperature.
The polynomial temperature correction formula can be expressed as:
Corrected Value = a0 + a1×T + a2×T^2 + ... + an×T^n
where:
– a0
, a1
, a2
, …, an
are the polynomial coefficients
– T
is the measurement temperature
– n
is the order of the polynomial
The polynomial coefficients are determined through calibration experiments or provided by the manufacturer of the measurement device. Polynomial temperature correction can accurately describe non-linear relationships and provide more precise corrections over a wider temperature range.
Lookup Table Temperature Correction
Lookup table temperature correction involves using pre-determined correction values for specific temperature points. The correction values are typically obtained through calibration experiments and stored in a lookup table.
During the measurement process, the temperature is measured, and the corresponding correction value is retrieved from the lookup table. The correction value is then added to or subtracted from the measured value to obtain the corrected result.
Lookup table temperature correction is useful when the relationship between the measured value and temperature is complex or when high accuracy is required at specific temperature points. However, it requires extensive calibration and may not provide continuous correction between the temperature points in the lookup table.
Implementing Temperature Correction
To implement temperature correction effectively, follow these steps:
-
Calibration: Perform calibration experiments to establish the relationship between the measured value and temperature. This involves measuring the parameter of interest at different temperatures and recording the corresponding values.
-
Determine the Correction Method: Based on the calibration data and the nature of the relationship between the measured value and temperature, choose the appropriate correction method (linear, polynomial, or lookup table).
-
Calculate Correction Factors: Using the calibration data, calculate the correction factors or coefficients required for the chosen correction method.
-
Implement the Correction: Integrate the temperature correction algorithm into the measurement system or data analysis software. Ensure that the temperature is accurately measured and recorded alongside the measured value.
-
Validate the Correction: Verify the effectiveness of the temperature correction by comparing the corrected values with reference measurements or known standards. Fine-tune the correction factors if necessary.
-
Document and Maintain: Document the temperature correction procedure, including the calibration data, correction method, and any assumptions made. Regularly review and update the correction factors to ensure ongoing accuracy.
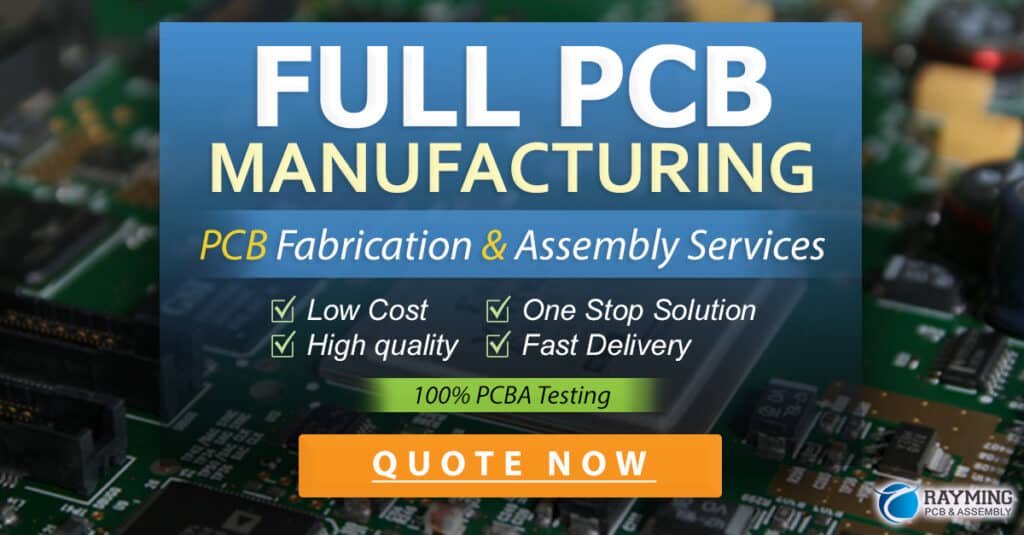
Challenges and Considerations
While temperature correction is essential for accurate measurements, there are several challenges and considerations to keep in mind:
-
Measurement Uncertainty: Temperature correction introduces additional uncertainty into the measurement process. It is important to quantify and report the uncertainty associated with the corrected values.
-
Temperature Sensor Accuracy: The accuracy of the temperature correction depends on the accuracy of the temperature sensor used. Ensure that the temperature sensor is calibrated and has sufficient resolution and stability.
-
Environmental Factors: Other environmental factors, such as humidity and pressure, can also influence the measured values. Consider whether additional corrections are necessary to account for these factors.
-
Correction Limits: Temperature correction methods have limitations and may not be applicable outside the calibrated temperature range. Be aware of the valid temperature range for the correction method used.
-
Computation and Data Storage: Implementing temperature correction requires additional computation and data storage resources. Ensure that the measurement system or data analysis software can handle the increased processing requirements.
Frequently Asked Questions (FAQ)
-
What is the purpose of temperature correction?
Temperature correction aims to compensate for the effects of temperature variations on the accuracy of measured values, ensuring consistent and reliable results. -
When is temperature correction necessary?
Temperature correction is necessary when the measured parameter is sensitive to temperature changes and the accuracy of the measurement is critical for the application or process. -
How do I choose the appropriate temperature correction method?
The choice of temperature correction method depends on the nature of the relationship between the measured value and temperature, the required accuracy, and the available calibration data. Linear correction is suitable for small temperature ranges with a linear relationship, while polynomial or lookup table correction is used for more complex relationships. -
Can temperature correction eliminate all measurement errors?
While temperature correction can significantly reduce measurement errors due to temperature variations, it cannot eliminate all sources of error. Other factors, such as calibration errors, sensor drift, and environmental influences, may still affect the accuracy of the measurements. -
How often should I review and update the temperature correction factors?
The frequency of reviewing and updating temperature correction factors depends on the stability of the measurement system and the criticality of the application. It is recommended to periodically validate the correction factors against reference standards and update them if necessary to maintain long-term accuracy.
Conclusion
Temperature correction is a vital process in ensuring the accuracy, consistency, and reliability of measured values across various fields. By understanding the concept of temperature correction, the available methods, and the implementation steps, you can effectively compensate for the effects of temperature variations on your measurements.
Remember to consider the challenges and limitations associated with temperature correction and regularly validate and update the correction factors to maintain the integrity of your results. With proper implementation, temperature correction can significantly enhance the quality and trustworthiness of your measurements, leading to better decision-making and process control.
Method | Advantages | Limitations |
---|---|---|
Linear Temperature Correction | Simple to implement Works well for small temperature ranges |
Limited to linear relationships May not be accurate for wide temperature ranges |
Polynomial Temperature Correction | Can handle non-linear relationships Provides accurate corrections over wider temperature ranges |
Requires calibration experiments to determine polynomial coefficients More computationally intensive |
Lookup Table Temperature Correction | Provides high accuracy at specific temperature points Useful for complex relationships |
Requires extensive calibration May not provide continuous correction between temperature points |
By leveraging the appropriate temperature correction method and following best practices, you can ensure that your measurements are accurate, consistent, and reliable, enabling you to make informed decisions and optimize your processes.
No responses yet