Introduction to PCB sensor placement
Printed Circuit Boards (PCBs) are the backbone of modern electronic devices. They provide a platform for mounting and interconnecting various electronic components, including sensors. The placement of sensors on a PCB is crucial for ensuring optimal performance, reliability, and functionality of the device. In this article, we will explore the key considerations and best practices for PCB sensor placement.
Types of Sensors Commonly Used on PCBs
There are various types of sensors that can be integrated into PCBs, depending on the application and the desired functionality. Some of the most common sensors include:
- Temperature Sensors
- Thermistors
- Thermocouples
- RTDs (Resistance Temperature Detectors)
- Pressure Sensors
- Piezoresistive Sensors
- Capacitive Sensors
- MEMS (Microelectromechanical Systems) Sensors
- Humidity Sensors
- Capacitive Humidity Sensors
- Resistive Humidity Sensors
- Accelerometers
- MEMS Accelerometers
- Gyroscopes
- MEMS Gyroscopes
- Light Sensors
- Photodiodes
- Phototransistors
- Ambient Light Sensors
Each type of sensor has its own characteristics, operating principles, and placement requirements on the PCB.
Factors Influencing PCB Sensor Placement
When placing sensors on a PCB, several factors need to be considered to ensure optimal performance and reliability. These factors include:
1. Environmental Factors
- Temperature: Sensors should be placed away from heat-generating components and in areas with stable temperature.
- Humidity: Humidity sensors should be placed in areas with minimal exposure to moisture and condensation.
- Vibration: Sensors sensitive to vibration should be placed in areas with minimal mechanical disturbances.
2. Electrical Factors
- Signal Integrity: Sensors should be placed close to their associated circuitry to minimize signal degradation and noise.
- Electromagnetic Interference (EMI): Sensors should be placed away from sources of EMI, such as high-frequency components or power lines.
- Grounding: Proper grounding techniques should be employed to minimize electrical noise and ensure accurate sensor readings.
3. Mechanical Factors
- PCB Layout: The placement of sensors should be considered during the PCB layout design phase to optimize routing and minimize interference.
- Component Placement: Sensors should be placed in a manner that allows for easy assembly and minimizes the risk of damage during handling.
- Mounting: Appropriate mounting techniques, such as through-hole or surface-mount, should be chosen based on the sensor type and application requirements.
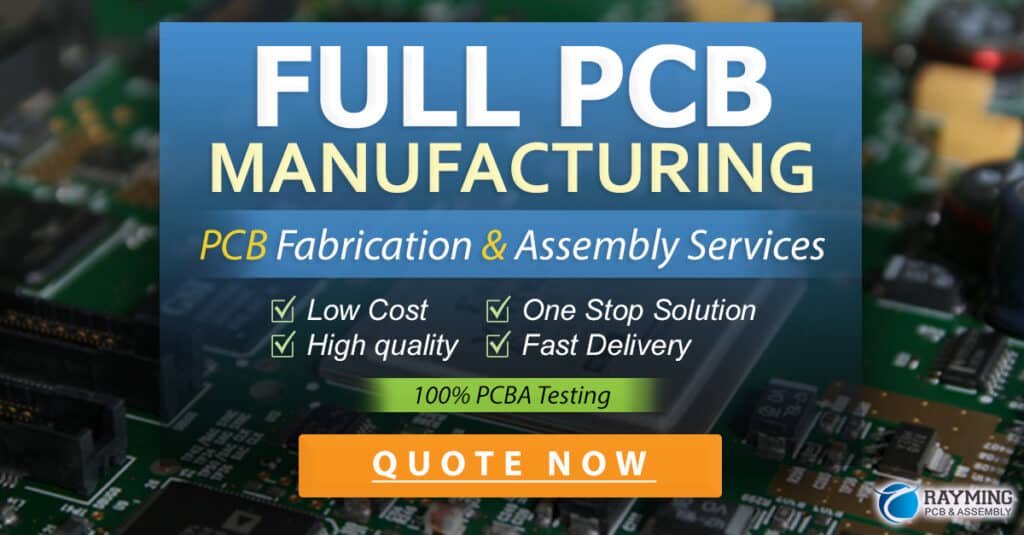
Best Practices for PCB Sensor Placement
To ensure optimal sensor performance and reliability, consider the following best practices when placing sensors on a PCB:
-
Follow the Manufacturer’s Guidelines: Always refer to the sensor manufacturer’s datasheet and application notes for specific placement recommendations.
-
Minimize Distance to Associated Circuitry: Place sensors as close as possible to their associated circuitry to minimize signal degradation and noise.
-
Consider Thermal Management: Place temperature-sensitive sensors away from heat-generating components and provide adequate thermal isolation.
-
Ensure Proper Grounding: Implement proper grounding techniques to minimize electrical noise and ensure accurate sensor readings.
-
Avoid Mechanical Stress: Place sensors in areas with minimal mechanical stress to prevent damage and ensure long-term reliability.
-
Optimize PCB Layout: Consider sensor placement during the PCB layout design phase to optimize routing and minimize interference.
-
Use Shielding Techniques: Employ shielding techniques, such as Faraday cages or ground planes, to protect sensors from electromagnetic interference.
-
Perform Thorough Testing: Conduct comprehensive testing and validation of the PCB with the placed sensors to ensure proper functionality and reliability.
Sensor Placement Techniques
There are several techniques commonly used for placing sensors on PCBs. The choice of technique depends on factors such as the sensor type, package size, and application requirements. Some common sensor placement techniques include:
1. Through-Hole Mounting
Through-hole mounting involves inserting the sensor leads through holes drilled in the PCB and soldering them on the opposite side. This technique provides a strong mechanical connection and is suitable for larger sensors or those subjected to mechanical stress.
2. Surface-Mount Technology (SMT)
Surface-mount technology involves placing the sensor directly on the surface of the PCB and soldering it using solder paste and reflow techniques. SMT is widely used for smaller sensors and allows for higher component density on the PCB.
3. Flex PCBs
Flex PCBs are flexible printed circuit boards that can conform to various shapes and contours. They are ideal for placing sensors in tight spaces or on curved surfaces. Flex PCBs provide flexibility in sensor placement and can be used in wearable devices or applications with limited space.
4. Connector-Based Placement
In some cases, sensors may be connected to the PCB using connectors instead of direct soldering. This approach allows for easy replacement or swapping of sensors without the need for soldering. Connector-based placement is commonly used for modular designs or applications that require frequent sensor replacement.
Sensor Placement Examples
To illustrate the concepts discussed, let’s look at a few examples of sensor placement on PCBs:
Example 1: Temperature Sensor Placement
Component | Placement Consideration |
---|---|
Thermistor | Place near the heat source for accurate temperature sensing |
Microcontroller | Place away from the thermistor to minimize self-heating |
Voltage Regulator | Place away from the thermistor to avoid heat dissipation |
In this example, the thermistor is placed near the heat source to accurately measure the temperature. The microcontroller and voltage regulator are placed away from the thermistor to minimize self-heating and avoid influencing the temperature readings.
Example 2: Accelerometer Placement
Component | Placement Consideration |
---|---|
Accelerometer | Place at the center of mass for accurate motion sensing |
Gyroscope | Place adjacent to the accelerometer for sensor fusion |
Microcontroller | Place close to the sensors for minimal signal degradation |
In this example, the accelerometer is placed at the center of mass of the PCB to accurately capture the motion dynamics. The gyroscope is placed adjacent to the accelerometer for sensor fusion and improved motion tracking. The microcontroller is placed close to the sensors to minimize signal degradation.
FAQ
-
Q: What is the most important factor to consider when placing sensors on a PCB?
A: The most important factor to consider is the specific requirements and characteristics of the sensor itself. Always refer to the sensor manufacturer’s datasheet and application notes for guidelines on placement, including recommended distances from other components, thermal considerations, and shielding requirements. -
Q: How can I minimize electromagnetic interference (EMI) when placing sensors on a PCB?
A: To minimize EMI, place sensors away from sources of high-frequency noise, such as switching power supplies or high-speed digital circuits. Use proper grounding techniques, such as dedicating a ground plane for the sensor, and consider employing shielding techniques like Faraday cages or metal enclosures. -
Q: What are the advantages of using surface-mount technology (SMT) for sensor placement?
A: SMT offers several advantages, including smaller footprint, higher component density, and automated assembly processes. SMT sensors are generally smaller in size compared to through-hole counterparts, allowing for more compact PCB designs. Additionally, SMT allows for automated pick-and-place assembly, reducing manual labor and improving production efficiency. -
Q: Can I place sensors on both sides of a PCB?
A: Yes, sensors can be placed on both sides of a PCB, depending on the specific design requirements and available space. However, it’s important to consider factors such as component height, accessibility for soldering and inspection, and potential interference between components on opposite sides of the board. -
Q: How do I ensure proper grounding for sensors on a PCB?
A: To ensure proper grounding, follow these guidelines: - Use a dedicated ground plane for the sensor and its associated circuitry.
- Keep the ground plane as continuous as possible and avoid splitting it unnecessarily.
- Use wide and short traces for the ground connection to minimize resistance and inductance.
- Place ground vias close to the sensor to provide a low-impedance path to the ground plane.
- Consider using guard rings or shielding techniques to isolate the sensor from noise sources.
Conclusion
PCB sensor placement is a critical aspect of Electronic design that directly impacts the performance, reliability, and functionality of the device. By considering factors such as environmental conditions, electrical requirements, and mechanical constraints, engineers can optimize sensor placement on PCBs.
Following best practices, such as minimizing distance to associated circuitry, ensuring proper grounding, and using appropriate placement techniques, can help achieve optimal sensor performance. Additionally, thorough testing and validation of the PCB with the placed sensors are essential to ensure proper functionality and reliability.
As technology advances and new sensor technologies emerge, the importance of proper PCB sensor placement will continue to grow. By staying up-to-date with the latest techniques and guidelines, engineers can design robust and reliable electronic systems that leverage the full potential of sensors in various applications.
No responses yet