Introduction
In today’s complex and globalized business environment, effective supply chain management is crucial for the success of any manufacturing organization. One of the key tools that can help streamline and optimize your supply chain is a well-structured Bill of Materials (BOM). A BOM is a comprehensive list of all the components, materials, and subassemblies required to manufacture a product, along with their quantities and relationships.
This article will explore the various aspects of a BOM and how it can significantly improve your supply chain management. We will discuss the different types of BOMs, their benefits, and the best practices for creating and maintaining an effective BOM. Additionally, we will delve into the role of technology in managing BOMs and the future trends in this field.
What is a Bill of Materials (BOM)?
A Bill of Materials (BOM) is a hierarchical list of all the components, subassemblies, and raw materials required to manufacture a finished product. It serves as a blueprint for the production process, providing a clear understanding of the product structure and the quantities of each component needed.
A typical BOM includes the following information:
- Part numbers and descriptions
- Quantities of each component
- Unit of measure
- Procurement details (e.g., supplier information, lead times)
- Assembly instructions and relationships between components
Types of BOMs
There are several types of BOMs, each serving a specific purpose within the manufacturing process:
-
Engineering BOM (EBOM): This type of BOM is created by the engineering team and focuses on the design aspects of the product. It includes all the components and their specifications required to create the product as designed.
-
Manufacturing BOM (MBOM): The MBOM is derived from the EBOM and is tailored to the specific needs of the manufacturing process. It may include additional information such as assembly instructions, work centers, and tooling requirements.
-
Sales BOM (SBOM): The SBOM is a simplified version of the BOM used by the sales team to communicate the product structure and options to customers. It may include configurable options and pricing information.
-
Service BOM (SBOM): This BOM type is used by the service and maintenance teams to identify the components required for repairs and maintenance tasks. It includes spare parts and their respective quantities.
BOM Type | Purpose | Key Information |
---|---|---|
EBOM | Product design | Components, specifications |
MBOM | Manufacturing process | Assembly instructions, work centers, tooling |
SBOM | Sales and customer communication | Product options, pricing |
SBOM | Service and maintenance | Spare parts, quantities |
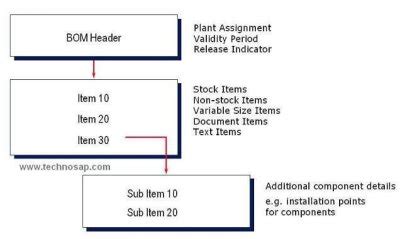
Benefits of Using a BOM in Supply Chain Management
Implementing a well-structured BOM can bring numerous benefits to your supply chain management process:
1. Improved Inventory Management
A BOM provides a clear understanding of the components and materials required for production, enabling better inventory planning and control. By accurately forecasting demand and managing inventory levels based on the BOM, you can minimize stockouts, reduce excess inventory, and improve overall inventory turnover.
2. Enhanced Supplier Collaboration
Sharing the relevant portions of your BOM with suppliers can streamline communication and collaboration. Suppliers can better understand your requirements, leading to improved lead times, quality, and cost management. A BOM also facilitates the identification of alternative suppliers and the evaluation of their capabilities.
3. Streamlined Production Planning
A BOM serves as a foundation for production planning and scheduling. By understanding the relationships between components and subassemblies, you can optimize production sequences, identify bottlenecks, and allocate resources effectively. This leads to improved production efficiency, reduced downtime, and faster time-to-market.
4. Better Quality Control
A BOM helps ensure consistent product quality by providing a standardized list of components and specifications. It reduces the risk of using incorrect or outdated components and enables better traceability in case of quality issues. By maintaining an up-to-date BOM, you can quickly identify and address any quality concerns.
5. Cost Optimization
An accurate BOM allows for better cost management throughout the supply chain. By understanding the cost of each component and subassembly, you can identify opportunities for cost reduction, such as sourcing alternative suppliers, negotiating better prices, or redesigning the product for cost optimization. A BOM also helps in accurate cost estimation and pricing decisions.
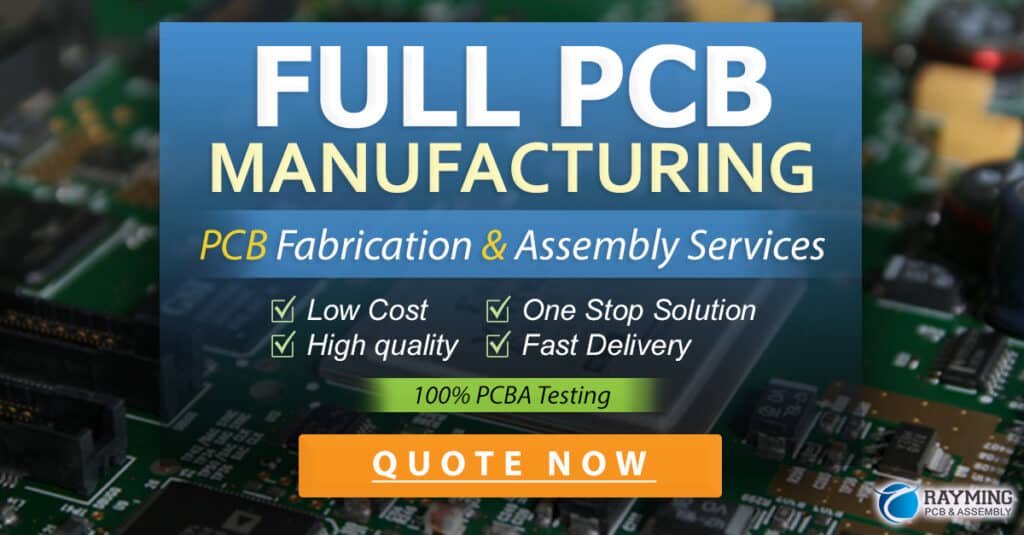
Best Practices for Creating and Maintaining an Effective BOM
To maximize the benefits of a BOM in your supply chain management, consider the following best practices:
1. Establish a Standardized BOM Format
Develop a consistent and standardized format for your BOMs across the organization. This includes defining the structure, naming conventions, and the level of detail required. A standardized format ensures clarity, reduces errors, and facilitates seamless communication between different departments and stakeholders.
2. Maintain Accurate and Up-to-Date Information
Regularly review and update your BOMs to reflect any changes in product design, components, or suppliers. Establish a process for version control and change management to ensure that everyone is working with the most current and accurate information. Automated BOM management tools can help streamline this process.
3. Collaborate with Cross-Functional Teams
Involve cross-functional teams, including engineering, manufacturing, procurement, and sales, in the BOM creation and maintenance process. Each team brings valuable insights and requirements that should be incorporated into the BOM. Regular collaboration ensures that the BOM meets the needs of all stakeholders and aligns with the overall business objectives.
4. Integrate with Other Systems
Integrate your BOM with other key systems, such as Enterprise Resource Planning (ERP), Product Lifecycle Management (PLM), and Manufacturing Execution Systems (MES). This integration ensures data consistency, reduces manual data entry, and enables real-time visibility into the supply chain. It also facilitates better decision-making and collaboration across the organization.
5. Conduct Regular Audits and Reviews
Perform regular audits and reviews of your BOMs to ensure their accuracy, completeness, and compliance with industry standards and regulations. This helps identify any discrepancies, obsolete components, or potential risks in the supply chain. Regular reviews also provide opportunities for continuous improvement and optimization of the BOM and related processes.
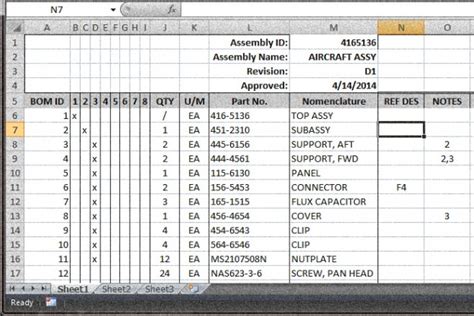
The Role of Technology in BOM Management
Technology plays a crucial role in managing BOMs effectively and efficiently. Here are some key technologies and systems that can support BOM management in your supply chain:
1. BOM Management Software
Specialized BOM management software provides a centralized platform for creating, maintaining, and sharing BOMs across the organization. These tools offer features such as version control, change management, access control, and collaboration capabilities. They help streamline the BOM process, reduce errors, and improve overall efficiency.
2. Product Lifecycle Management (PLM) Systems
PLM systems provide a comprehensive solution for managing product-related information, including BOMs, throughout the entire product lifecycle. They enable seamless collaboration between different teams, from design to manufacturing and service. PLM systems help ensure data consistency, facilitate change management, and provide real-time visibility into the product development process.
3. Enterprise Resource Planning (ERP) Systems
ERP systems integrate various business processes, including supply chain management, inventory control, and financial management. By integrating your BOM with an ERP system, you can ensure accurate inventory planning, procurement, and production scheduling. ERP systems provide real-time visibility into the supply chain, enabling better decision-making and optimization.
4. Cloud-Based Solutions
Cloud-based BOM management solutions offer scalability, accessibility, and flexibility. They allow teams to access and collaborate on BOMs from anywhere, at any time, using any device. Cloud solutions also provide automatic updates, data backup, and enhanced security features, reducing the burden on internal IT resources.
Future Trends in BOM Management
As technology continues to evolve, BOM management is also expected to undergo significant advancements. Some of the future trends in BOM management include:
1. Artificial Intelligence (AI) and Machine Learning (ML)
AI and ML technologies can be leveraged to automate and optimize various aspects of BOM management. For example, AI algorithms can help identify potential issues in the BOM, suggest alternative components, or optimize production schedules based on real-time data. ML can also be used to improve demand forecasting and inventory planning.
2. Internet of Things (IoT)
IoT devices and sensors can provide real-time data on the performance and status of components and products throughout the supply chain. This information can be integrated with the BOM to enable predictive maintenance, optimize inventory levels, and improve overall Supply chain visibility. IoT data can also help in identifying quality issues and tracing the root cause of problems.
3. Digital Twins
Digital twins are virtual replicas of physical products or processes that can be used for simulation, testing, and optimization. By creating digital twins of products and their BOMs, organizations can optimize product designs, simulate production scenarios, and predict the impact of changes in the supply chain. Digital twins can also facilitate collaboration between different teams and stakeholders.
4. Blockchain Technology
Blockchain technology can be used to create a secure and transparent record of BOM-related transactions and changes. It can help ensure data integrity, traceability, and immutability throughout the supply chain. Blockchain-based BOM management can also facilitate collaboration and trust among different stakeholders, such as suppliers, manufacturers, and customers.
Frequently Asked Questions (FAQ)
-
What is the difference between an Engineering BOM (EBOM) and a Manufacturing BOM (MBOM)?
An Engineering BOM (EBOM) focuses on the design aspects of the product and includes all the components and specifications required to create the product as designed. On the other hand, a Manufacturing BOM (MBOM) is tailored to the specific needs of the manufacturing process and may include additional information such as assembly instructions, work centers, and tooling requirements. -
How often should I update my BOM?
It is recommended to update your BOM whenever there are changes in product design, components, or suppliers. The frequency of updates may vary depending on the complexity of your product and the dynamics of your industry. Establishing a regular review and update process helps ensure that your BOM remains accurate and up-to-date. -
Can a BOM be used for multiple products?
Yes, a BOM can be used for multiple products that share common components or subassemblies. This is known as a modular or configurable BOM. It allows for greater flexibility and efficiency in managing product variations and customizations. -
How can I ensure data consistency between my BOM and other systems?
To ensure data consistency between your BOM and other systems, such as ERP or PLM, it is crucial to establish integration and synchronization mechanisms. This can be achieved through APIs, data exchange formats, or specialized integration tools. Regular data audits and reconciliation processes can also help identify and resolve any discrepancies. -
What are the key challenges in implementing a BOM management system?
Some of the key challenges in implementing a BOM management system include: - Establishing a standardized BOM format and structure across the organization
- Ensuring data accuracy and completeness
- Managing change control and version management
- Integrating with existing systems and processes
- Securing buy-in and adoption from different stakeholders
- Providing adequate training and support for users
Conclusion
A well-structured and effectively managed Bill of Materials (BOM) is a powerful tool for improving your supply chain management. It provides a clear and comprehensive view of the components, materials, and relationships required to manufacture a product, enabling better inventory planning, supplier collaboration, production efficiency, quality control, and cost optimization.
To maximize the benefits of a BOM, it is essential to establish a standardized format, maintain accurate and up-to-date information, collaborate with cross-functional teams, integrate with other systems, and conduct regular audits and reviews. Technology solutions such as BOM management software, PLM systems, ERP systems, and cloud-based solutions can greatly support and streamline the BOM management process.
Looking ahead, emerging technologies such as AI, ML, IoT, digital twins, and blockchain are expected to revolutionize BOM management, offering new opportunities for optimization, automation, and collaboration.
By embracing best practices and leveraging technology, organizations can harness the full potential of their BOMs to drive supply chain efficiency, agility, and competitiveness in today’s dynamic business landscape.
No responses yet