Introduction to PCB Stackup
A printed circuit board (PCB) is a crucial component in modern electronic devices, providing a platform for mounting and interconnecting electronic components. The arrangement of layers in a PCB, known as the stackup, plays a vital role in determining the board’s performance, reliability, and manufacturability. In this article, we will focus on the stackup of a 3 layer PCB and explore its characteristics, advantages, and design considerations.
What is a 3 Layer PCB Stackup?
A 3 layer PCB stackup consists of three conductive layers separated by insulating materials. The three layers are typically arranged as follows:
- Top Layer: This is the uppermost conductive layer of the PCB, where components are mounted and signals are routed.
- Inner Layer: Also known as the core layer, this is the middle conductive layer sandwiched between the top and bottom layers.
- Bottom Layer: The lowermost conductive layer of the PCB, often used for power distribution and additional signal routing.
The conductive layers are usually made of copper, while the insulating materials are commonly FR-4, a glass-reinforced epoxy laminate.
Advantages of a 3 Layer PCB Stackup
A 3 layer PCB stackup offers several advantages over simpler 2 layer boards:
- Increased routing density: The additional inner layer allows for more signal routing options, enabling higher component density and more complex designs.
- Improved signal integrity: The inner layer can serve as a ground plane, reducing electromagnetic interference (EMI) and improving signal quality.
- Better power distribution: The inner layer can be used for power distribution, providing a low-impedance path for power delivery to components.
- Enhanced mechanical stability: The additional layer increases the overall thickness and rigidity of the PCB, making it more resistant to warping and vibration.
Designing a 3 Layer PCB Stackup
When designing a 3 layer PCB stackup, several factors must be considered to ensure optimal performance and manufacturability.
Layer Arrangement
The arrangement of layers in a 3 layer PCB stackup can vary depending on the specific requirements of the design. Two common arrangements are:
- Signal-Ground-Signal (S-G-S): In this arrangement, the top and bottom layers are used for signal routing, while the inner layer serves as a ground plane.
- Power-Ground-Signal (P-G-S): Here, the top layer is used for signal routing, the inner layer is a ground plane, and the bottom layer is used for power distribution.
The choice of layer arrangement depends on factors such as signal integrity, power distribution requirements, and EMI considerations.
Layer Thickness
The thickness of each layer in a 3 layer PCB stackup is an important design consideration. Typical layer thicknesses are:
Layer | Thickness (mm) |
---|---|
Copper | 0.018 – 0.070 |
FR-4 | 0.100 – 1.600 |
The thickness of the copper layers affects the current carrying capacity and the impedance of the traces, while the thickness of the FR-4 layers determines the overall board thickness and influences the characteristic impedance of the traces.
Via Design
Vias are conductive holes drilled through the PCB layers to interconnect traces on different layers. In a 3 layer PCB stackup, vias can be used to connect the top and bottom layers to the inner layer. There are two main types of vias:
- Through-hole vias: These vias go through all layers of the PCB and are typically used for component mounting and interconnection.
- Blind vias: These vias connect an outer layer to the inner layer but do not go through the entire board thickness. Blind vias can be used to save space and improve signal integrity.
The size and spacing of vias must be carefully considered to ensure manufacturability and reliability.
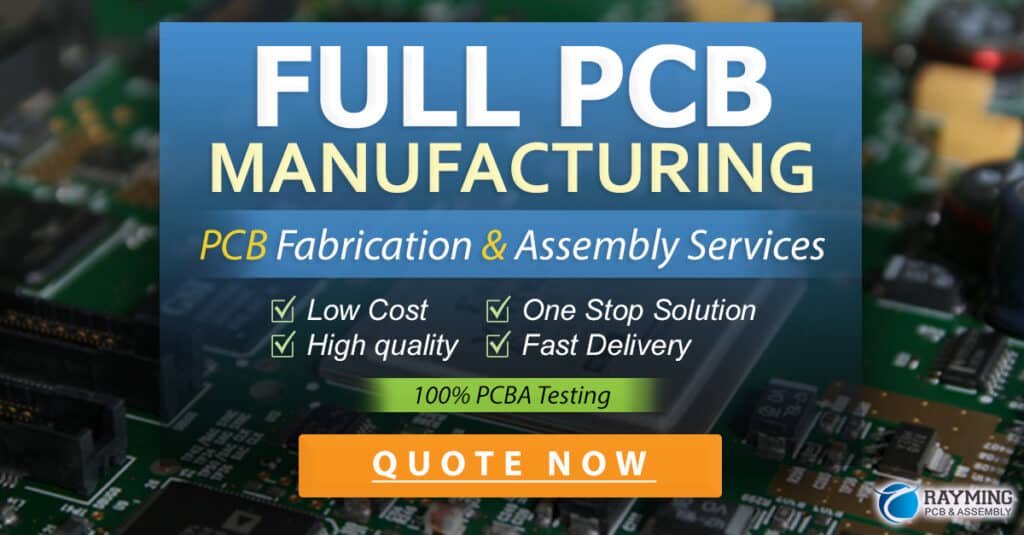
Manufacturing a 3 Layer PCB Stackup
The manufacturing process for a 3 layer PCB stackup involves several steps:
- Inner layer fabrication: The inner layer is etched with the desired conductive pattern and inspected for defects.
- Lamination: The inner layer is sandwiched between the top and bottom layers, along with the insulating materials, and the stack is laminated under high temperature and pressure.
- Drilling: Holes are drilled through the board for vias and component mounting.
- Plating: The drilled holes are plated with copper to create conductive paths between layers.
- Outer layer fabrication: The top and bottom layers are etched with their respective conductive patterns.
- Solder mask application: A protective solder mask is applied to the outer layers, leaving exposed areas for component mounting and soldering.
- Surface finish application: A surface finish, such as HASL or ENIG, is applied to the exposed copper areas to protect them from oxidation and enhance solderability.
Testing and Inspection
After manufacturing, the 3 layer PCB undergoes various testing and inspection procedures to ensure quality and functionality:
- Visual inspection: The board is visually inspected for defects such as missing or incorrect features, contamination, and mechanical damage.
- Automated optical inspection (AOI): An automated camera system checks the board for missing or misaligned components, solder defects, and other issues.
- Electrical testing: The board is tested for short circuits, open circuits, and other electrical faults using specialized equipment such as flying probe testers or bed-of-nails fixtures.
- Functional testing: The assembled board is tested under real-world operating conditions to verify its performance and functionality.
Troubleshooting Common Issues
Despite careful design and manufacturing, issues can sometimes arise with 3 layer PCBs. Some common problems and their solutions include:
- Signal integrity issues: Poor signal integrity can be addressed by optimizing trace routing, using appropriate layer arrangements, and implementing proper grounding and shielding techniques.
- Power distribution problems: Insufficient or noisy power delivery can be mitigated by using dedicated power planes, optimizing via placement, and implementing decoupling capacitors.
- Manufacturability challenges: Issues such as via reliability and layer registration can be addressed by adhering to design for manufacturability (DFM) guidelines and collaborating closely with the PCB manufacturer.
Future Trends in 3 Layer PCB Stackup
As electronic devices continue to advance, so do the requirements for PCB stackups. Some emerging trends in 3 layer PCB stackup design include:
- High-speed designs: With the increasing demand for faster data transmission, designs must account for signal integrity challenges at higher frequencies.
- Flexible and rigid-flex PCBs: The use of flexible and rigid-flex PCBs is growing, requiring specialized stackup designs that accommodate the unique mechanical and electrical properties of these materials.
- Advanced materials: New materials, such as low-loss dielectrics and high-temperature laminates, are being developed to meet the demands of emerging applications.
Conclusion
A well-designed 3 layer PCB stackup is essential for creating reliable, high-performance electronic devices. By understanding the characteristics, advantages, and design considerations of 3 layer stackups, engineers can create boards that meet the specific requirements of their applications. As technology continues to evolve, staying up-to-date with the latest trends and best practices in PCB stackup design will be crucial for success in the electronics industry.
Frequently Asked Questions (FAQ)
-
What is the difference between a 2 layer and a 3 layer PCB stackup?
A 3 layer PCB stackup has an additional inner conductive layer compared to a 2 layer board, allowing for more routing options, better signal integrity, and improved power distribution. -
Can a 3 layer PCB stackup be used for high-speed designs?
Yes, a 3 layer PCB stackup can be used for high-speed designs, but careful consideration must be given to signal integrity, layer arrangement, and material selection to ensure optimal performance. -
What are the advantages of using blind vias in a 3 layer PCB stackup?
Blind vias can save space on the outer layers of a 3 layer PCB stackup and improve signal integrity by reducing the length of the conductive path between layers. -
How does the thickness of the dielectric layers affect the performance of a 3 layer PCB stackup?
The thickness of the dielectric layers influences the characteristic impedance of the traces and the overall thickness of the board, which can impact signal integrity and mechanical stability. -
What are some common testing and inspection methods for 3 layer PCBs?
Common testing and inspection methods for 3 layer PCBs include visual inspection, automated optical inspection (AOI), electrical testing, and functional testing under real-world operating conditions.
No responses yet