Introduction to Hole Size Calculation
When working on various projects, whether it’s in engineering, manufacturing, or DIY, knowing how to accurately calculate the size of a hole is crucial. The diameter of a hole plays a significant role in ensuring proper fit, functionality, and overall success of the project. In this comprehensive guide, we will explore the different methods and techniques used to determine hole size, along with practical examples and frequently asked questions.
What is Hole Diameter?
Hole diameter refers to the distance across the center of a circular hole, measured from one side to the other. It is a critical dimension that determines the size of the hole and the compatibility of objects that need to fit through or into it. Accurate hole size calculation is essential for creating precise holes in various materials, such as metal, wood, plastic, or concrete.
Why is Accurate Hole Size Important?
Ensuring accurate hole size is crucial for several reasons:
-
Proper fit: When holes are designed to accommodate specific objects, such as bolts, screws, or pipes, the hole diameter must be precise to ensure a secure and proper fit. Incorrect hole sizes can lead to loose or overly tight connections, compromising the integrity of the assembly.
-
Functionality: In many applications, holes serve specific functions, such as allowing fluid flow, providing ventilation, or enabling the movement of components. The hole size directly affects the performance of these functions, and inaccurate sizing can result in reduced efficiency or complete failure.
-
Aesthetics: In some cases, hole size can impact the visual appeal of a project. Mismatched or poorly sized holes can detract from the overall appearance and give an impression of poor craftsmanship.
-
Safety: In certain situations, hole size can have safety implications. For example, in electrical installations, holes that are too small can cause wires to overheat, while oversized holes may not provide adequate support or protection.
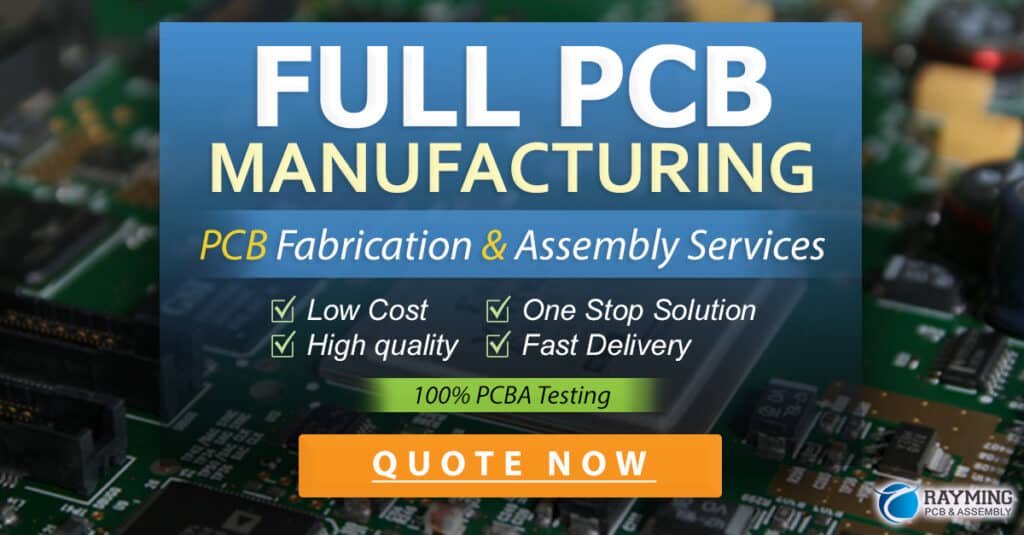
Tools for Measuring Hole Diameter
To accurately measure hole diameter, you will need the following tools:
- Calipers: Calipers are precision measuring instruments that can be used to determine the internal diameter of a hole. There are several types of calipers, including:
- Vernier calipers
- Digital calipers
-
Dial calipers
-
Micrometers: Micrometers are another precision measuring tool that can be used for hole diameter measurement. They offer high accuracy and are particularly useful for measuring small holes.
-
Hole gauges: Hole gauges are specialized tools designed specifically for measuring hole diameters. They consist of a set of precise pins or blades that can be inserted into the hole to determine its size.
-
Rulers and tape measures: While not as precise as calipers or micrometers, rulers and tape measures can be used for rough hole diameter measurements, especially for larger holes.
Methods for Calculating Hole Diameter
There are several methods you can use to calculate hole diameter, depending on the tools available and the level of precision required. Let’s explore some of the most common techniques:
1. Using Calipers
Calipers are the most widely used tool for measuring hole diameter. Here’s how to use them:
- Select the appropriate caliper for your needs (vernier, digital, or dial).
- Clean the hole and the caliper jaws to ensure accurate measurements.
- Open the caliper jaws and carefully insert them into the hole, ensuring that they are perpendicular to the hole’s axis.
- Close the jaws until they gently touch the sides of the hole.
- Read the measurement on the caliper scale or display.
- Repeat the process in multiple locations around the hole to account for any irregularities and take an average measurement.
2. Using Micrometers
Micrometers offer high precision and are ideal for measuring small hole diameters. Here’s the procedure:
- Select a micrometer with the appropriate measuring range for your hole size.
- Clean the hole and the micrometer anvils.
- Place the micrometer anvils inside the hole, ensuring they are perpendicular to the hole’s axis.
- Rotate the micrometer thimble until the anvils gently touch the sides of the hole.
- Read the measurement on the micrometer scale and sleeve.
- Repeat the process in multiple locations and take an average.
3. Using Hole Gauges
Hole gauges are specialized tools that provide a quick and easy way to measure hole diameters. Here’s how to use them:
- Select a hole gauge set that covers the expected range of your hole size.
- Clean the hole and the gauge pins.
- Insert the gauge pins into the hole, starting with the smallest size and progressively increasing until you find the pin that fits snugly without forcing it.
- Read the size marked on the gauge pin that provides the best fit.
4. Calculating Hole Diameter from Circumference
In some cases, you may have the circumference of the hole available instead of direct diameter measurements. You can calculate the diameter using the following formula:
Diameter = Circumference ÷ π
Where π (pi) is approximately 3.14159.
For example, if the circumference of a hole is 25 mm, the diameter would be:
Diameter = 25 mm ÷ 3.14159 ≈ 7.96 mm
5. Calculating Hole Diameter from Area
If you have the area of the hole, you can calculate the diameter using the following formula:
Diameter = 2 × √(Area ÷ π)
Where √ represents the square root operation.
For example, if the area of a hole is 50 mm², the diameter would be:
Diameter = 2 × √(50 mm² ÷ 3.14159) ≈ 7.98 mm
Factors Affecting Hole Size Accuracy
Several factors can influence the accuracy of hole size measurements. It’s important to be aware of these factors and take steps to minimize their impact:
-
Tool calibration: Ensure that your measuring tools are properly calibrated and in good condition. Regularly check and adjust them according to the manufacturer’s guidelines.
-
Material deformation: When measuring holes in soft or flexible materials, be cautious not to deform the hole while measuring, as this can lead to inaccurate results.
-
Temperature variations: Temperature changes can cause materials to expand or contract, affecting hole size. Measure holes at a consistent temperature, preferably the temperature at which the final product will be used.
-
Surface finish: The surface finish of the hole can impact measurements. Rough or uneven surfaces may require multiple measurements to obtain an accurate average.
-
Human error: Operator skill and consistency play a role in accurate hole size measurement. Ensure that measurements are taken correctly and consistently, and consider having multiple operators measure the same hole to reduce the risk of individual errors.
Best Practices for Accurate Hole Size Measurement
To ensure the most accurate hole size measurements, follow these best practices:
-
Clean the hole and measuring tools: Remove any debris, dirt, or burrs from the hole and the measuring tools to prevent interference and ensure accurate measurements.
-
Use the appropriate measuring tool: Select the measuring tool that best suits your needs based on the hole size, required precision, and material.
-
Take multiple measurements: Measure the hole diameter at several locations around the circumference and take an average to account for any irregularities.
-
Ensure proper alignment: When using calipers or micrometers, make sure the tool is perpendicular to the hole’s axis to avoid skewed measurements.
-
Control the measuring environment: Measure holes in a consistent environment, considering factors such as temperature, humidity, and vibrations that could affect the accuracy of the measurements.
-
Record and document measurements: Keep a record of your measurements, including the tools used, the measurement locations, and any specific conditions. This documentation can be useful for future reference and quality control purposes.
Hole Size Tolerances and Fit
In many applications, hole size is specified with a tolerance, which defines the acceptable range of deviation from the nominal size. Tolerances are typically expressed as a plus or minus value, such as ±0.1 mm.
The choice of tolerance depends on the specific requirements of the project, such as the desired fit between mating parts, the material properties, and the manufacturing processes involved. Common types of fits include:
-
Clearance fit: A clearance fit allows for a small gap between the hole and the mating part, enabling easy assembly and disassembly. This type of fit is commonly used for parts that require relative motion or thermal expansion.
-
Interference fit: An interference fit involves a hole that is slightly smaller than the mating part, resulting in a tight, press-fit connection. This type of fit is often used for parts that need to be securely fastened together without the use of additional hardware.
-
Transition fit: A transition fit falls between clearance and interference fits, providing a snug fit with minimal clearance or interference. This type of fit is used when a balance between easy assembly and secure connection is required.
When specifying hole sizes and tolerances, it’s important to consider the manufacturing processes involved and consult with the relevant standards and guidelines for your specific industry or application.
Hole Size Calculation Examples
Let’s work through a few examples to illustrate the process of calculating hole size:
Example 1: Measuring a hole with calipers
Suppose you need to measure the diameter of a hole in a metal plate using digital calipers. You take measurements at three different locations around the hole and obtain the following readings:
- Measurement 1: 12.35 mm
- Measurement 2: 12.38 mm
- Measurement 3: 12.33 mm
To calculate the average hole diameter:
Average diameter = (12.35 mm + 12.38 mm + 12.33 mm) ÷ 3 = 12.35 mm
Therefore, the hole diameter is approximately 12.35 mm.
Example 2: Calculating hole diameter from circumference
You have a circular hole with a measured circumference of 31.4 mm. To find the diameter:
Diameter = Circumference ÷ π
Diameter = 31.4 mm ÷ 3.14159 ≈ 10 mm
The hole diameter is approximately 10 mm.
Example 3: Calculating hole diameter from area
A circular hole has a measured area of 78.5 mm². Calculate the hole diameter:
Diameter = 2 × √(Area ÷ π)
Diameter = 2 × √(78.5 mm² ÷ 3.14159) ≈ 10 mm
The hole diameter is approximately 10 mm.
Frequently Asked Questions (FAQ)
- What is the most accurate tool for measuring hole diameter?
-
Calipers and micrometers are the most accurate tools for measuring hole diameter, with micrometers offering the highest precision for small holes. The choice between the two depends on the size of the hole and the required level of accuracy.
-
How do I choose the right tolerance for a hole?
-
The choice of tolerance depends on the specific requirements of your project, such as the desired fit, material properties, and manufacturing processes. Consult with the relevant standards and guidelines for your industry or application, and consider factors such as the function of the hole, the mating parts, and the assembly method.
-
What should I do if I don’t have access to specialized measuring tools?
-
In the absence of calipers, micrometers, or hole gauges, you can use a combination of rulers, tape measures, and pi tape (a flexible ruler marked with circumference measurements). While these tools may not provide the same level of precision, they can still offer a reasonable estimate of hole size for less critical applications.
-
How do I measure the diameter of a non-circular hole?
-
For non-circular holes, such as squares or rectangles, measure the distance between opposite sides and calculate the average. For irregular shapes, determine the longest and shortest dimensions and calculate their average. Keep in mind that these measurements will not represent a true diameter but can serve as a useful approximation.
-
Can I use a 3D scanner to measure hole diameter?
- Yes, 3D scanning technology can be used to measure hole diameter, particularly for complex or hard-to-reach holes. 3D scanners create a digital model of the object, which can then be analyzed using specialized software to extract hole dimensions. This method is particularly useful for reverse engineering or quality control purposes.
Conclusion
Accurately calculating hole size is a critical skill for various applications, from engineering and manufacturing to DIY projects. By understanding the different methods and tools available for measuring hole diameter, you can ensure proper fit, functionality, and overall success of your projects.
Remember to consider factors such as tool calibration, material properties, and environmental conditions that can affect the accuracy of your measurements. Always follow best practices, such as cleaning the hole and measuring tools, taking multiple measurements, and ensuring proper alignment.
By mastering the art of hole size calculation and measurement, you can achieve precise and reliable results, enabling you to create high-quality products and solutions.
No responses yet