What is a High-Voltage PCB?
A high-voltage printed circuit board (HV PCB) is a specialized type of PCB designed to handle high voltages, typically over 50V. These boards are used in various applications such as power supplies, automotive electronics, medical devices, aerospace systems, and industrial equipment.
High-voltage PCBs differ from standard PCBs in several ways:
- Thicker copper traces to handle higher currents
- Larger clearances between conductors to prevent arcing
- Specialized materials with higher dielectric strength
- Unique design considerations for safety and reliability
Importance of High-Voltage PCB Design
Proper high-voltage PCB design is crucial for several reasons:
- Safety: Improper design can lead to electrical hazards, posing risks to users and equipment.
- Reliability: Well-designed HV PCBs ensure consistent performance and longer product lifespans.
- Efficiency: Optimized designs minimize power losses and heat generation.
- Cost-effectiveness: Proper design reduces manufacturing costs and prevents expensive failures.
High-Voltage PCB Design Considerations
To create a satisfactory high-voltage PCB design, consider the following factors:
1. Clearance and Creepage Distances
Clearance is the shortest distance through air between two conductors, while creepage is the shortest distance along the surface of the insulating material. Adequate clearance and creepage distances prevent arcing and leakage currents.
Factors affecting clearance and creepage include:
- Voltage level
- Pollution degree
- Material group (CTI)
- Altitude
Refer to IPC-2221B for recommended clearance and creepage distances based on these factors.
2. Conductor Sizing and Spacing
High-voltage PCBs require thicker copper traces to handle higher currents without excessive heating. Use the IPC-2152 standard to determine the appropriate trace width for your application.
Conductor spacing is also crucial to prevent arcing. Maintain sufficient space between traces, pads, and vias.
3. Material Selection
Choose PCB materials with high dielectric strength, low dissipation factor, and good thermal stability. Some common high-voltage PCB materials include:
- FR-4
- Polyimide
- Ceramic
- Teflon
Consider the material’s CTI (Comparative Tracking Index) when determining creepage distances.
4. Grounding and Shielding
Proper grounding is essential for high-voltage PCBs to ensure safety and minimize EMI. Use dedicated ground planes and connect them to the system ground.
Employ shielding techniques to reduce EMI and protect sensitive components. This can include:
- Copper pours
- Grounded traces
- Shielded cables and connectors
5. Component Selection and Placement
Select components rated for the expected voltage and power levels. Pay attention to the voltage ratings of capacitors, resistors, and other components.
Place components strategically to minimize trace lengths and loop areas. Keep high-voltage components away from sensitive low-voltage circuits.
6. Thermal Management
High-voltage PCBs often generate significant heat due to higher power dissipation. Proper thermal management is essential to prevent overheating and ensure reliability.
Consider the following thermal management techniques:
- Adequate copper thickness for heat dissipation
- Thermal vias to transfer heat to other layers
- Heat sinks and cooling fans
- Proper component placement for even heat distribution
7. Testing and Certification
High-voltage PCBs require thorough testing and certification to ensure safety and compliance with relevant standards. Some common tests include:
- Dielectric withstand voltage (DWV) test
- Insulation resistance (IR) test
- Partial discharge (PD) test
- Functional testing under various environmental conditions
Obtain necessary certifications such as UL, CE, or IEC based on your target market and application.
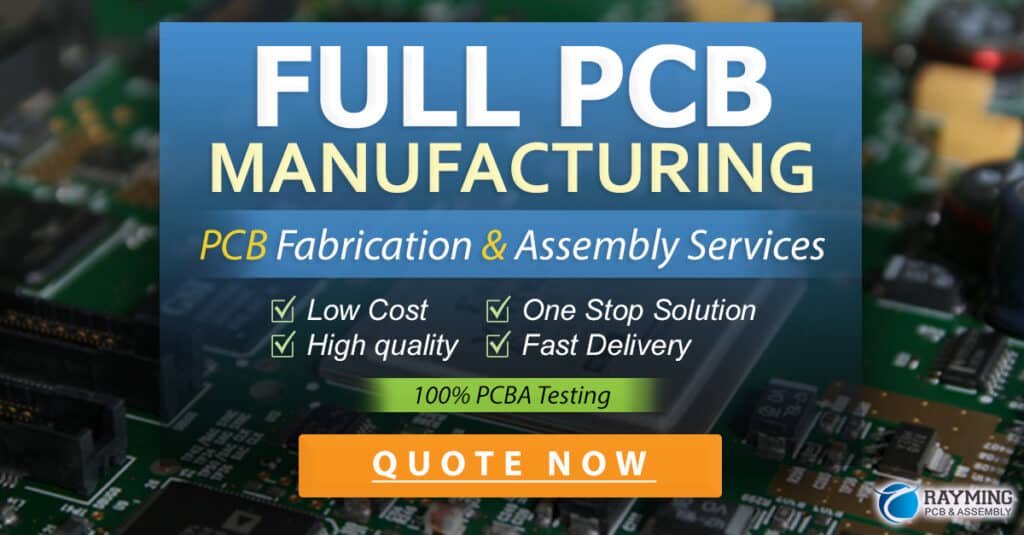
High-Voltage PCB Design Workflow
A typical high-voltage PCB design workflow consists of the following steps:
- Schematic design: Create a schematic diagram of the circuit, including all components and their connections.
- Component selection: Choose components based on voltage ratings, power handling capability, and other requirements.
- Layout design: Arrange components and route traces on the PCB, considering clearance, creepage, and other design factors.
- Simulation: Perform simulations to verify the design’s performance, signal integrity, and thermal behavior.
- Prototyping: Fabricate and assemble prototype boards for testing and validation.
- Testing and certification: Conduct necessary tests and obtain required certifications.
- Production: Release the design for mass production, ensuring proper documentation and version control.
High-Voltage PCB Design Software
Several PCB design software packages offer features specifically for high-voltage designs. Some popular options include:
- Altium Designer
- OrCAD PCB Designer
- PADS PCB Design
- Eagle PCB
- KiCad EDA
These software tools provide functions such as clearance and creepage checking, automatic trace sizing, and design rule checks (DRC) to help create compliant and reliable high-voltage PCB designs.
High-Voltage PCB Manufacturing
High-voltage PCB manufacturing requires specialized equipment and processes to ensure the boards’ integrity and performance. Some key aspects of HV PCB manufacturing include:
- Material handling: Proper storage and handling of high-voltage PCB materials to prevent contamination and damage.
- Drilling: High-precision drilling to create clean, burr-free holes for vias and component leads.
- Plating: Copper plating to achieve the required trace thickness and ensure reliable connections.
- Solder mask application: Accurate solder mask application to maintain clearance and creepage distances.
- Inspection: Thorough visual and automated inspection to detect defects and ensure conformance to specifications.
Choose a PCB manufacturer with experience in high-voltage PCB fabrication and a proven track record of quality and reliability.
High-Voltage PCB Assembly
Assembling high-voltage PCBs requires special considerations to ensure safety and reliability:
- Soldering: Use appropriate soldering techniques and materials to prevent overheating and damage to components.
- Cleaning: Thorough cleaning to remove flux residues and contaminants that can cause leakage currents or arcing.
- Conformal coating: Apply conformal coating to protect the board from moisture, dust, and other environmental factors.
- Potting: Encapsulate high-voltage components or sections of the board in potting compound for added insulation and protection.
Follow best practices for ESD (electrostatic discharge) protection during assembly to prevent damage to sensitive components.
High-Voltage PCB Testing
Rigorous testing is essential to validate the performance and safety of high-voltage PCBs. Some common tests include:
- Continuity test: Verify that all connections are intact and there are no short circuits.
- Insulation resistance test: Measure the resistance between conductors to ensure adequate insulation.
- Dielectric withstand test: Apply high voltage between conductors to check for breakdown or leakage.
- Functional test: Test the board’s performance under various operating conditions.
- Environmental testing: Expose the board to different environmental factors (e.g., temperature, humidity, vibration) to assess its durability.
Document all test results and address any issues before releasing the board for use.
High-Voltage PCB Maintenance and Repair
Proper maintenance and timely repairs are crucial for the long-term reliability and safety of high-voltage PCBs. Some key considerations include:
- Regular inspections: Perform visual inspections to check for signs of damage, corrosion, or contamination.
- Cleaning: Clean the board periodically to remove dust, dirt, and other contaminants that can degrade performance.
- Component replacement: Replace faulty or degraded components promptly to prevent further damage.
- Retrofit and upgrades: Implement necessary retrofits or upgrades to address design issues or improve performance.
Always follow appropriate safety precautions when handling high-voltage PCBs during maintenance and repair.
FAQ
-
What is the difference between clearance and creepage?
Clearance is the shortest distance through air between two conductors, while creepage is the shortest distance along the surface of the insulating material. -
How do I determine the appropriate trace width for my high-voltage PCB?
Use the IPC-2152 standard to determine the appropriate trace width based on the expected current, temperature rise, and other factors. -
What materials are commonly used for high-voltage PCBs?
Common materials for high-voltage PCBs include FR-4, polyimide, ceramic, and Teflon. Choose a material with high dielectric strength, low dissipation factor, and good thermal stability. -
Why is proper grounding important for high-voltage PCBs?
Proper grounding ensures safety and minimizes EMI. Use dedicated ground planes and connect them to the system ground to provide a low-impedance path for currents. -
What certifications may be required for high-voltage PCBs?
Depending on your target market and application, you may need certifications such as UL, CE, or IEC. These certifications ensure that your high-voltage PCB meets relevant safety and performance standards.
Conclusion
Designing high-voltage PCBs requires careful consideration of various factors, including clearance and creepage distances, conductor sizing and spacing, material selection, grounding and shielding, component selection and placement, thermal management, and testing and certification. By following best practices and using appropriate tools and techniques, you can create safe, reliable, and efficient high-voltage PCBs that meet your application’s requirements. Remember to work with experienced PCB manufacturers and assemblers, and always prioritize safety and compliance with relevant standards.
Key Takeaways
- Understand the unique design considerations for high-voltage PCBs
- Follow industry standards and guidelines for clearance, creepage, and conductor sizing
- Choose appropriate materials and components for your application
- Implement proper grounding, shielding, and thermal management techniques
- Conduct thorough testing and obtain necessary certifications
- Work with experienced partners for manufacturing, assembly, and maintenance
By keeping these factors in mind, you can create high-voltage PCB designs that deliver satisfactory performance and reliability while ensuring the safety of users and equipment.
No responses yet