What is a High-Current PCB?
A high-current printed circuit board (PCB) is a specialized type of PCB designed to handle high levels of electrical current. These boards are used in various applications that require the efficient and reliable transfer of large amounts of power, such as power supplies, motor controllers, and industrial equipment.
Key Features of High-Current PCBs
High-current PCBs have several distinct features that set them apart from standard PCBs:
-
Thicker copper traces: To accommodate higher currents, high-current PCBs use thicker copper traces than standard PCBs. The increased thickness allows for better current-carrying capacity and heat dissipation.
-
Wider traces: In addition to being thicker, the traces on high-current PCBs are also wider. This further enhances their ability to handle high currents without overheating or suffering from voltage drops.
-
Larger vias: Vias, which are the holes that connect different layers of the PCB, are also larger on high-current boards. This ensures that the current can flow freely through the board without encountering bottlenecks.
-
High-quality substrate materials: High-current PCBs often use high-quality substrate materials, such as FR-4 or ceramic, which offer excellent thermal and electrical properties. These materials help to minimize power loss and ensure reliable operation.
Designing High-Current PCBs
When designing a high-current PCB, several factors must be taken into consideration to ensure optimal performance and reliability.
Trace Width and Thickness
One of the most critical aspects of high-current PCB design is determining the appropriate trace width and thickness. The required trace dimensions depend on several factors, including the amount of current flowing through the trace, the ambient temperature, and the maximum allowable temperature rise.
To calculate the required trace width and thickness, designers can use online calculators or reference tables provided by PCB manufacturers. These tools take into account various parameters, such as the copper weight, the maximum current, and the temperature rise, to determine the optimal trace dimensions.
Copper Weight (oz) | Trace Width (mm) | Current Capacity (A) |
---|---|---|
1 | 0.5 | 2.5 |
1 | 1.0 | 5.0 |
2 | 0.5 | 3.5 |
2 | 1.0 | 7.0 |
Table 1: Example trace width and current capacity for different copper weights
Thermal Management
Another essential consideration in high-current PCB design is thermal management. As current flows through the traces, it generates heat, which can lead to performance issues and even failure if not properly managed.
To mitigate the effects of heat, designers can employ several techniques:
-
Using thicker copper layers: As mentioned earlier, thicker copper traces can help to dissipate heat more efficiently.
-
Adding thermal vias: Thermal vias are holes drilled through the PCB that are filled with conductive material, such as copper. These vias help to transfer heat from the components and traces to the other side of the board, where it can be dissipated more easily.
-
Incorporating heatsinks: Heatsinks are metal components that are attached to the PCB to help dissipate heat. They work by increasing the surface area available for heat transfer, allowing the heat to be removed more efficiently.
-
Using thermal interface materials: Thermal interface materials, such as thermal pads or thermal paste, can be used to improve the thermal conductivity between components and the PCB or heatsink.
Component Selection
When designing a high-current PCB, it is crucial to select components that are rated for the expected current levels. This includes choosing:
- Power connectors with sufficient current ratings
- Capacitors and inductors with appropriate voltage and current ratings
- Semiconductors, such as MOSFETs and diodes, with suitable current and power dissipation capabilities
Failure to select appropriate components can result in overheating, reduced performance, and even device failure.
Manufacturing High-Current PCBs
The manufacturing process for high-current PCBs is similar to that of standard PCBs, but with a few key differences to accommodate the unique requirements of these boards.
Copper Plating
One of the most significant differences in the manufacturing of high-current PCBs is the copper plating process. To achieve the desired trace thickness, these boards typically undergo a process called “heavy copper plating.”
In heavy copper plating, additional layers of copper are deposited onto the base copper layer of the PCB. This process can be repeated multiple times to achieve the desired thickness, which can range from 2 oz to 10 oz or more.
Copper Weight (oz) | Trace Thickness (mm) |
---|---|
1 | 0.035 |
2 | 0.070 |
3 | 0.105 |
4 | 0.140 |
Table 2: Trace thickness for different copper weights
Drilling and Plating Vias
Another critical aspect of high-current PCB manufacturing is the drilling and plating of vias. As mentioned earlier, high-current PCBs require larger vias to ensure adequate current flow and heat dissipation.
To create these larger vias, specialized drilling equipment is used. After drilling, the vias are plated with copper to ensure good electrical conductivity and thermal transfer.
Solder Mask and Silkscreen
The solder mask and silkscreen application processes for high-current PCBs are similar to those used for standard PCBs. However, designers may need to pay special attention to the solder mask clearances around the larger traces and components to ensure proper insulation and prevent short circuits.
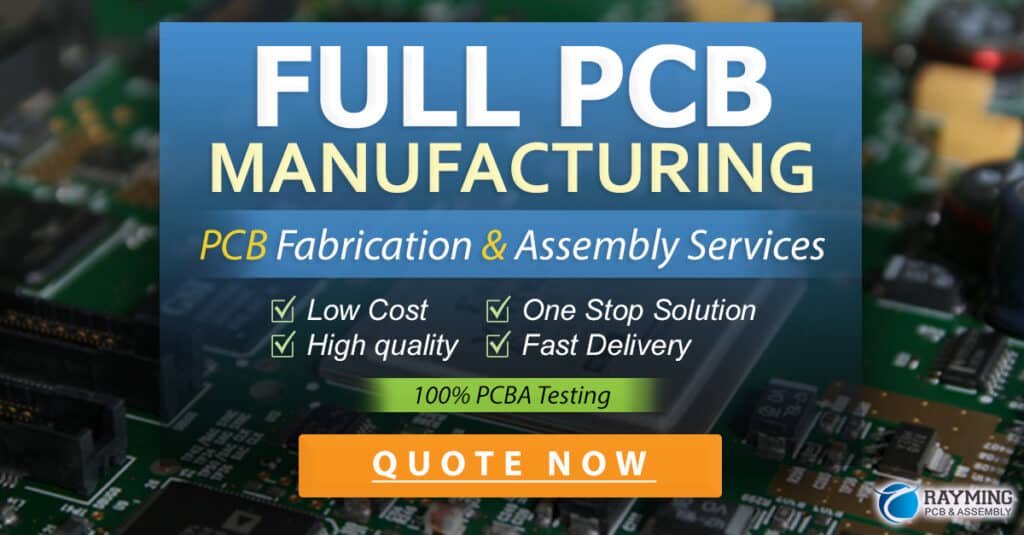
Testing and Quality Control
Given the critical nature of high-current applications, thorough testing and quality control are essential to ensure the reliability and performance of high-current PCBs.
Electrical Testing
Electrical testing is performed to verify that the PCB meets the specified current-carrying capacity and voltage requirements. This may involve:
- Continuity testing to ensure that all connections are properly made
- Isolation testing to check for shorts or leakage between different parts of the board
- High-voltage testing to verify the board’s ability to withstand the expected voltage levels
Thermal Testing
Thermal testing is conducted to assess the PCB’s ability to dissipate heat effectively. This may involve:
- Thermographic imaging to identify hot spots on the board
- Temperature monitoring during operation to ensure that the board stays within acceptable limits
- Power cycling to simulate real-world conditions and check for any performance degradation over time
Visual Inspection
Visual inspection is performed to check for any manufacturing defects, such as:
- Incorrect component placement
- Poor solder joints
- Trace or via defects
- Contamination or foreign object debris (FOD)
By conducting thorough testing and quality control, manufacturers can ensure that high-current PCBs meet the necessary performance and reliability standards for their intended applications.
Applications of High-Current PCBs
High-current PCBs find use in a wide range of applications across various industries. Some common applications include:
Power Supplies
High-current PCBs are essential components in power supplies, particularly those designed for high-power applications. These boards are used in:
- Switched-mode power supplies (SMPS)
- Uninterruptible power supplies (UPS)
- Battery management systems (BMS)
Motor Controllers
Motor controllers, especially those for high-power motors, rely on high-current PCBs to handle the large currents required to drive the motors efficiently. Applications include:
- Industrial automation systems
- Electric vehicles
- Robotics
Renewable Energy Systems
High-current PCBs are used in various renewable energy systems, such as:
- Solar inverters
- Wind turbine controllers
- Fuel cell systems
These boards help to manage the high currents generated by these systems and ensure efficient power conversion and distribution.
Automotive Electronics
In the automotive industry, high-current PCBs are used in a variety of applications, including:
- Engine control units (ECUs)
- Power steering controllers
- Lighting systems
- Electric vehicle charging systems
As the demand for high-power electronic systems in vehicles continues to grow, the importance of high-current PCBs in the automotive industry is expected to increase.
Future Trends in High-Current PCBs
As technology advances and the demand for high-power electronic systems grows, several trends are expected to shape the future of high-current PCBs:
Advanced Materials
The development of advanced substrate materials, such as ceramic and metal-core PCBs, is expected to improve the thermal performance and reliability of high-current PCBs. These materials offer better heat dissipation and higher thermal stability compared to traditional FR-4 substrates.
3D Printing
The use of 3D printing technology in PCB manufacturing is expected to enable the creation of more complex and customized high-current PCB designs. This could lead to improved performance and reduced manufacturing costs for small-batch or prototype production.
Embedded Components
The integration of passive components, such as capacitors and resistors, directly into the PCB substrate is another trend that could benefit high-current PCBs. Embedded components can help to reduce the overall board size, improve signal integrity, and enhance thermal performance.
Increased Automation
As with other areas of PCB manufacturing, increased automation is expected to play a significant role in the production of high-current PCBs. Automated assembly, inspection, and testing processes can help to improve efficiency, reduce human error, and ensure consistent quality.
Frequently Asked Questions (FAQ)
-
What is the difference between a high-current PCB and a standard PCB?
- A high-current PCB is designed to handle higher levels of electrical current than a standard PCB. It features thicker and wider traces, larger vias, and high-quality substrate materials to accommodate the increased current flow and heat dissipation requirements.
-
How do I determine the appropriate trace width and thickness for my high-current PCB?
- The required trace width and thickness depend on factors such as the amount of current, ambient temperature, and maximum allowable temperature rise. You can use online calculators or reference tables provided by PCB manufacturers to determine the optimal trace dimensions for your specific application.
-
What are some common applications for high-current PCBs?
- High-current PCBs are used in a variety of applications, including power supplies, motor controllers, renewable energy systems, and automotive electronics.
-
How does thermal management affect the design of high-current PCBs?
- Thermal management is a critical consideration in high-current PCB design. Techniques such as using thicker copper layers, adding thermal vias, incorporating heatsinks, and using thermal interface materials can help to dissipate heat more effectively and prevent performance issues or failure.
-
What are some future trends in high-current PCB technology?
- Future trends in high-current PCBs include the use of advanced substrate materials, 3D printing for more complex and customized designs, embedded components for improved performance and reduced board size, and increased automation in manufacturing processes.
As the demand for high-power electronic systems continues to grow across various industries, the importance of high-current PCBs will only increase. By understanding the unique design, manufacturing, and testing requirements of these boards, engineers and manufacturers can create reliable and efficient solutions for a wide range of high-current applications.
No responses yet