Understanding PCB Extreme Environments
Printed Circuit Boards (PCBs) are essential components in modern electronic devices, serving as the backbone for electrical connections and component mounting. However, not all PCBs are created equal, especially when it comes to operating in extreme environments. In this article, we will explore the challenges faced by PCBs in high temperature and extreme conditions, and how heavy copper PCBs provide a reliable solution.
What Are Extreme Environments for PCBs?
Extreme environments for PCBs can be characterized by several factors:
-
High temperatures: Environments where the operating temperature exceeds 125°C (257°F) are considered extreme for standard PCBs.
-
Thermal cycling: Rapid and frequent changes in temperature can cause stress on the PCB and its components.
-
Vibration and shock: Mechanical stresses from vibration and sudden impacts can damage PCBs and cause component failure.
-
Corrosive atmospheres: Exposure to chemicals, humidity, or other corrosive elements can degrade PCB materials and affect performance.
-
High altitude: Low atmospheric pressure at high altitudes can impact the PCB’s ability to dissipate heat effectively.
Industries Requiring PCB Extreme Solutions
Several industries require PCBs that can withstand extreme conditions:
-
Aerospace and defense: Aircraft, satellites, and military equipment often operate in harsh environments with high temperatures, vibration, and altitude.
-
Automotive: Under-the-hood applications, such as engine control units and power electronics, must withstand high temperatures and vibration.
-
Oil and gas: Downhole drilling equipment and sensors are subjected to high temperatures, pressures, and corrosive environments.
-
Industrial: Heavy machinery, power plants, and other industrial applications often expose PCBs to extreme temperatures and vibration.
-
Medical: Certain medical devices, such as autoclave-sterilized equipment, must withstand high temperatures and humidity.
Heavy Copper PCBs: A Solution for Extreme Environments
Heavy copper PCBs are designed to address the challenges posed by extreme environments. By utilizing thicker copper layers, these PCBs offer several advantages over standard designs.
Benefits of Heavy Copper PCBs
-
Enhanced thermal management: Thicker copper layers provide better heat dissipation, allowing the PCB to operate at higher temperatures without compromising performance.
-
Improved current carrying capacity: Heavy copper PCBs can handle higher current loads, reducing the risk of overheating and component failure.
-
Increased mechanical strength: The additional copper thickness provides better mechanical stability, making the PCB more resistant to vibration and shock.
-
Longer product lifespan: By withstanding extreme conditions, heavy copper PCBs offer a longer operational life, reducing maintenance and replacement costs.
Copper Weight and Thickness
Standard PCBs typically use copper layers ranging from 0.5 oz to 2 oz per square foot (17 to 68 μm). Heavy copper PCBs, on the other hand, utilize copper layers from 3 oz to 20 oz per square foot (102 to 680 μm).
Copper Weight (oz/ft²) | Copper Thickness (μm) |
---|---|
0.5 | 17 |
1 | 34 |
2 | 68 |
3 | 102 |
4 | 136 |
6 | 204 |
8 | 272 |
10 | 340 |
12 | 408 |
14 | 476 |
16 | 544 |
18 | 612 |
20 | 680 |
Thermal Management with Heavy Copper PCBs
One of the primary advantages of heavy copper PCBs is their superior thermal management capabilities. The thicker copper layers allow for better heat dissipation, which is crucial in high-temperature environments.
Thermal Conductivity of Copper
Copper is an excellent thermal conductor, with a thermal conductivity of approximately 401 W/(m·K). This high thermal conductivity allows heat to be efficiently transferred from hot spots on the PCB to the surrounding environment.
Thermal Vias and Heat Sinks
In addition to using heavy copper layers, PCB designers can further enhance thermal management by incorporating thermal vias and heat sinks.
-
Thermal vias: These are small, plated holes that connect the copper layers, allowing heat to be transferred vertically through the PCB.
-
Heat sinks: Attached to the PCB, heat sinks provide additional surface area for heat dissipation and can be cooled by convection or forced air.
Designing Heavy Copper PCBs
When designing heavy copper PCBs for extreme environments, several factors must be considered:
-
Layer stackup: Determine the appropriate number of layers and copper weights based on the thermal and electrical requirements of the application.
-
Trace width and spacing: Ensure that trace widths are sufficient to handle the required current, and maintain adequate spacing to prevent short circuits and signal interference.
-
Via size and placement: Optimize via size and placement to enhance thermal transfer and maintain signal integrity.
-
Component selection: Choose components that are rated for the expected operating temperature range and environmental conditions.
-
Manufacturing considerations: Work closely with the PCB manufacturer to ensure that the design can be reliably produced using heavy copper processes.
Case Studies: Heavy Copper PCBs in Action
Aerospace Application: Satellite Power Supply
A satellite manufacturer required a power supply PCB that could operate reliably in the harsh environment of space, where temperatures can fluctuate from -200°C to 200°C (-328°F to 392°F) and radiation levels are high.
The solution was a heavy copper PCB with 6 oz copper layers, providing enhanced thermal management and increased resistance to thermal cycling. The PCB also incorporated radiation-hardened components and conformal coating to protect against the effects of radiation and vacuum.
Automotive Application: Engine Control Unit
An automotive supplier needed an engine control unit (ECU) PCB that could withstand the high temperatures and vibration present in the engine compartment.
The heavy copper PCB design utilized 4 oz copper layers and a high glass transition temperature (Tg) substrate material. Thermal vias and a custom heat sink were incorporated to further enhance thermal management. The PCB was also subjected to rigorous vibration and thermal cycling tests to ensure reliable operation in the automotive environment.
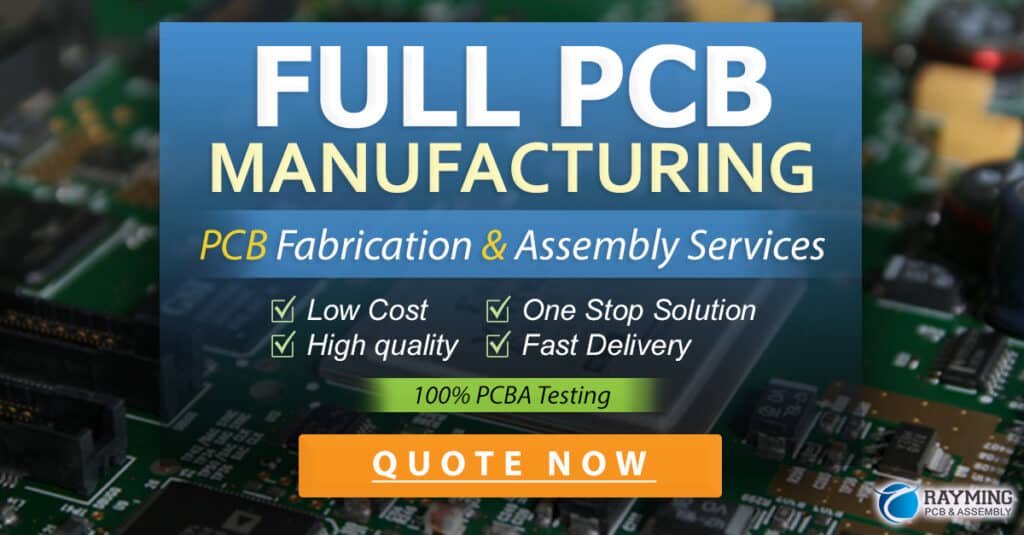
Frequently Asked Questions (FAQ)
-
Q: Can heavy copper PCBs be used in standard PCB designs?
A: Yes, heavy copper layers can be incorporated into standard PCB designs to improve thermal management and current carrying capacity in specific areas, such as power delivery or high-heat components. -
Q: How does the cost of heavy copper PCBs compare to standard PCBs?
A: Heavy copper PCBs are generally more expensive than standard PCBs due to the additional copper material and specialized manufacturing processes required. However, the increased cost is often justified by the improved performance and reliability in extreme environments. -
Q: Are there any limitations to the number of layers in a heavy copper PCB?
A: The number of layers in a heavy copper PCB is limited by the manufacturing capabilities of the PCB fabricator. Most manufacturers can produce heavy copper PCBs with up to 24 layers, but this may vary depending on the specific copper weights and other design requirements. -
Q: Can heavy copper PCBs be combined with other PCB technologies, such as high-frequency materials or embedded components?
A: Yes, heavy copper layers can be integrated with other PCB technologies to create highly specialized designs for demanding applications. However, the compatibility of different technologies must be carefully evaluated to ensure optimal performance and manufacturability. -
Q: How can I determine if a heavy copper PCB is the right solution for my application?
A: If your application involves high temperatures, thermal cycling, vibration, or other extreme environmental conditions, a heavy copper PCB may be a suitable solution. Consult with a PCB design expert or manufacturer to assess your specific requirements and determine the most appropriate PCB technology for your needs.
Conclusion
Heavy copper PCBs offer a robust solution for electronic devices operating in high temperature and extreme environments. By utilizing thicker copper layers, these PCBs provide enhanced thermal management, improved current carrying capacity, increased mechanical strength, and longer product lifespans.
When designing heavy copper PCBs, it is essential to consider factors such as layer stackup, trace width and spacing, via size and placement, component selection, and manufacturing considerations. Collaborating closely with experienced PCB designers and manufacturers can help ensure the successful development and production of heavy copper PCBs for demanding applications.
As technology continues to advance and electronic devices are deployed in increasingly challenging environments, heavy copper PCBs will play a crucial role in ensuring reliable performance and long-term durability.
No responses yet