What is HDI PCB?
HDI PCBs are printed circuit boards that feature higher wiring density than conventional PCBs. They are characterized by:
– Finer line widths and spaces (typically less than 100 µm)
– Smaller vias (microvia and buried vias)
– Higher connection pad density
– Thinner copper foils
– Multiple layers (often 8 or more)
These features enable HDI PCBs to accommodate more components and complex circuitry in a smaller area, making them ideal for applications that require high performance, miniaturization, and reliability.
Advantages of HDI PCBs
HDI PCBs offer several advantages over traditional PCBs:
-
Miniaturization: HDI technology allows for smaller component sizes and denser packaging, resulting in more compact electronic devices.
-
Improved Signal Integrity: The shorter signal paths and reduced layer count in HDI PCBs minimize signal loss and interference, leading to better signal integrity and overall performance.
-
Increased Functionality: With the ability to accommodate more components and complex circuitry, HDI PCBs enable enhanced functionality in a smaller footprint.
-
Reduced Weight: The compact design and fewer layers in HDI PCBs contribute to a lighter overall weight of the end product.
-
Cost-Effective: Although the initial cost of HDI PCBs may be higher, the long-term cost savings from reduced assembly time, improved yield, and better performance make them a cost-effective solution.
Factors to Consider When Choosing an HDI PCB Manufacturer
When selecting an HDI PCB manufacturer, consider the following key factors to ensure you make the right choice for your project:
1. Technical Capabilities
Assess the manufacturer’s technical capabilities to ensure they can meet your specific HDI PCB requirements. Consider factors such as:
- Minimum line width and spacing
- Via sizes and types (microvia, buried via, blind via)
- Maximum layer count
- Material options (FR-4, high-frequency laminates, flexible substrates)
- Surface finishes (ENIG, ENEPIG, OSP, Immersion Silver)
2. Manufacturing Process and Equipment
Inquire about the manufacturer’s production process and equipment to gauge their ability to produce high-quality HDI PCBs consistently. Key aspects include:
- Advanced manufacturing technologies (laser drilling, plasma etching, direct imaging)
- Automated inspection systems (AOI, X-ray, ICT)
- Cleanroom facilities
- IPC certification (IPC-6012, IPC-A-600, IPC-A-610)
3. Quality Control and Testing
A reliable HDI PCB manufacturer should have robust quality control measures and testing procedures in place. Look for:
- Documented quality management system (ISO 9001)
- In-process quality control checkpoints
- Electrical testing (flying probe, boundary scan)
- Environmental testing (thermal cycling, humidity, vibration)
- Failure analysis and corrective action procedures
4. Experience and Expertise
Choose a manufacturer with proven experience and expertise in HDI PCB fabrication. Consider:
- Years of experience in the industry
- Portfolio of successful HDI PCB projects
- Familiarity with your specific industry or application
- Technical support and design assistance capabilities
5. Turnaround Time and Flexibility
In the fast-paced electronics industry, timely delivery is critical. Evaluate the manufacturer’s:
- Standard lead times for prototyping and production
- Expedited service options
- Flexibility to accommodate design changes or rush orders
6. Customer Service and Communication
Effective communication and responsive customer service are essential for a smooth collaboration. Assess the manufacturer’s:
- Ease of communication (language barriers, time zone differences)
- Responsiveness to inquiries and requests
- Proactive project updates and status reporting
- Willingness to collaborate and provide guidance
7. Cost and Value
While cost is an important consideration, it should not be the sole deciding factor. Evaluate the manufacturer’s pricing in relation to:
- Quality and reliability of their HDI PCBs
- Value-added services (design support, testing, logistics)
- Long-term cost savings from fewer defects and improved performance
- Minimum order quantities (MOQs) and volume discounts
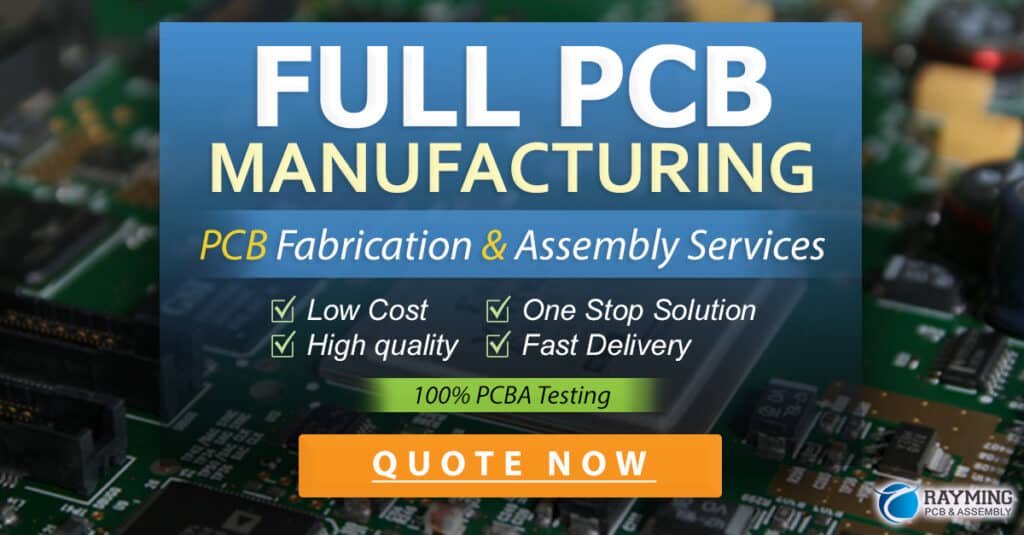
How to Evaluate and Select an HDI PCB Manufacturer
Now that you understand the key factors to consider, follow these steps to evaluate and select the right HDI PCB manufacturer for your needs:
- Define your HDI PCB requirements and specifications
- Research potential manufacturers based on their technical capabilities, experience, and reputation
- Request quotes and compare pricing, lead times, and MOQs
- Evaluate their manufacturing process, quality control measures, and certifications
- Assess their communication, responsiveness, and customer service
- Request references or case studies of similar HDI PCB projects they have completed
- Conduct a site visit or audit, if possible, to verify their facilities and capabilities
- Place a small trial order to gauge their quality, reliability, and service
- Based on the evaluation, select the manufacturer that best aligns with your requirements and expectations
Common Pitfalls to Avoid When Choosing an HDI PCB Manufacturer
To ensure a successful partnership, avoid these common pitfalls when selecting an HDI PCB manufacturer:
- Focusing solely on price without considering quality, reliability, and service
- Failing to clearly communicate your requirements and expectations
- Not verifying the manufacturer’s technical capabilities and manufacturing processes
- Ignoring warning signs such as unresponsive communication or inconsistent information
- Rushing the selection process without thorough evaluation and due diligence
Advantages of Partnering with a Global HDI PCB Manufacturer
Partnering with a global HDI PCB manufacturer, especially those located in strategic locations like China, can offer several advantages:
-
Lower Production Costs: Global manufacturers often have lower labor and material costs, enabling them to offer competitive pricing without compromising quality.
-
Advanced Manufacturing Capabilities: Many global manufacturers have invested in state-of-the-art equipment and technologies to stay competitive, ensuring access to the latest HDI PCB manufacturing capabilities.
-
Scalability and Capacity: Global manufacturers typically have larger production capacities, allowing them to accommodate higher volume orders and scale up production as needed.
-
Access to Global Supply Chain: Partnering with a global manufacturer can provide access to a wider network of suppliers, ensuring a stable and reliable supply of materials and components.
-
Diverse Industry Experience: Global manufacturers often serve a wide range of industries, offering valuable insights and expertise that can benefit your HDI PCB project.
How to Manage Communication and Collaboration with a Global HDI PCB Manufacturer
Effective communication and collaboration are crucial when working with a global HDI PCB manufacturer. Follow these tips to ensure a smooth partnership:
- Establish clear communication channels and protocols
- Use collaboration tools (e.g., video conferencing, project management software) to bridge geographical distances
- Assign dedicated points of contact on both sides to streamline communication
- Set regular progress updates and milestones to keep the project on track
- Be mindful of cultural differences and adapt your communication style accordingly
- Foster a long-term partnership based on trust, transparency, and mutual benefit
Future Trends in HDI PCB Manufacturing
As the electronics industry evolves, HDI PCB manufacturing will continue to advance to meet the ever-increasing demands for miniaturization, performance, and functionality. Some key trends to watch for include:
-
Finer Feature Sizes: Manufacturers will push the boundaries of line widths, spacing, and via sizes to enable even denser PCB designs.
-
Advanced Materials: The adoption of high-performance materials, such as low-loss laminates and ultra-thin copper foils, will become more widespread to support higher frequencies and signal speeds.
-
Embedded Components: The integration of active and passive components within the PCB substrate will gain traction, enabling further miniaturization and improved performance.
-
3D Printing: Additive manufacturing techniques, like 3D printing, will play a growing role in HDI PCB fabrication, allowing for more complex geometries and faster prototyping.
-
Sustainability: Manufacturers will increasingly focus on eco-friendly materials and processes to reduce environmental impact and meet regulatory requirements.
Conclusion
Choosing the right HDI PCB manufacturer is a critical decision that can significantly impact the success of your electronic products. By considering the key factors outlined in this guide and following a systematic evaluation process, you can select a manufacturer that aligns with your technical requirements, quality expectations, and business objectives. Partnering with a reputable and experienced HDI PCB manufacturer will ensure the optimal performance, reliability, and competitiveness of your products in the dynamic electronics market.
Frequently Asked Questions (FAQ)
-
What is the difference between HDI PCBs and conventional PCBs?
HDI PCBs feature finer line widths and spaces, smaller vias, higher connection pad density, and thinner copper foils compared to conventional PCBs. These characteristics enable HDI PCBs to accommodate more complex designs in a smaller form factor. -
What are the benefits of using HDI PCBs in electronic products?
HDI PCBs offer several benefits, including miniaturization, improved signal integrity, increased functionality, reduced weight, and cost-effectiveness. These advantages make HDI PCBs well-suited for applications that require high performance, compact size, and reliability. -
How do I evaluate the technical capabilities of an HDI PCB manufacturer?
When evaluating a manufacturer’s technical capabilities, consider factors such as their minimum line width and spacing, via sizes and types, maximum layer count, material options, and surface finishes. Request information on their manufacturing processes, equipment, and certifications to gauge their ability to meet your specific HDI PCB requirements. -
What quality control measures should I look for in an HDI PCB manufacturer?
A reliable HDI PCB manufacturer should have a documented quality management system (e.g., ISO 9001), in-process quality control checkpoints, electrical and environmental testing procedures, and failure analysis and corrective action processes in place. These measures ensure consistent production of high-quality HDI PCBs. -
How can I manage communication and collaboration with a global HDI PCB manufacturer?
To effectively manage communication and collaboration with a global HDI PCB manufacturer, establish clear communication channels and protocols, use collaboration tools to bridge geographical distances, assign dedicated points of contact, set regular progress updates, and be mindful of cultural differences. Foster a long-term partnership based on trust, transparency, and mutual benefit to ensure a smooth collaboration.
No responses yet