What is HDI PCB Design?
HDI PCB design is a specialized form of printed circuit board design that focuses on achieving higher component density and improved electrical performance. HDI PCBs typically have finer pitch components, smaller vias, and thinner traces compared to traditional PCBs. These features allow for more components to be placed on a smaller board area, resulting in more compact and efficient designs.
Key Features of HDI PCBs
- Fine pitch components: HDI PCBs can accommodate components with a pitch of 0.5mm or less, enabling the use of smaller and more densely packed components.
- Smaller vias: HDI PCBs use microvias, which are smaller than traditional through-hole vias. Microvias can have diameters as small as 0.1mm, allowing for more efficient use of board space.
- Thinner traces: HDI PCBs often feature trace widths and spacings of 0.1mm or less, enabling higher routing density and improved signal integrity.
- Multiple layers: HDI PCBs can have up to 20 or more layers, allowing for more complex routing and better signal integrity.
Advantages of HDI PCB Design
HDI PCB design offers several advantages over traditional PCB designs, making it an attractive choice for many applications. Some of the key benefits include:
- Reduced board size: By using smaller components and more efficient routing, HDI PCBs can be made much smaller than traditional PCBs, allowing for more compact device designs.
- Improved signal integrity: The use of thinner traces and smaller vias in HDI PCBs reduces signal reflections and crosstalk, resulting in better signal integrity and higher-speed performance.
- Lower power consumption: The shorter trace lengths and reduced parasitic capacitance in HDI PCBs lead to lower power consumption, which is particularly important for battery-powered devices.
- Enhanced thermal management: The higher component density in HDI PCBs can make thermal management more challenging, but the use of advanced materials and design techniques can help to mitigate this issue.
HDI PCB Design Considerations
When designing an HDI PCB, there are several key considerations to keep in mind to ensure the best possible performance and reliability.
Component Selection
Choosing the right components is critical for HDI PCB design. Some factors to consider include:
- Package size: Smaller packages, such as chip-scale packages (CSPs) and ball grid arrays (BGAs), are well-suited for HDI designs.
- Pitch: Components with a pitch of 0.5mm or less are ideal for HDI PCBs.
- Thermal requirements: High-power components may require special thermal management techniques, such as the use of thermal vias or heat spreaders.
Via Types and Placement
HDI PCBs typically use microvias, which can be categorized into three main types:
- Blind vias: Connect an outer layer to an inner layer, but do not penetrate through the entire board.
- Buried vias: Connect two or more inner layers, but do not extend to the outer layers.
- Through-hole vias: Extend through the entire thickness of the board, connecting all layers.
When placing vias, it is important to consider the following:
- Via size: Smaller vias allow for more efficient use of board space, but may be more challenging to manufacture.
- Via stacking: Stacking microvias can help to save space and reduce the number of layers required, but may increase manufacturing complexity.
- Via-in-pad: Placing vias directly in component pads can save space, but requires careful design and manufacturing considerations.
Trace Routing
Trace routing is a critical aspect of HDI PCB design, as it directly affects signal integrity and electromagnetic compatibility (EMC). Some key considerations include:
- Trace width and spacing: Thinner traces and smaller spacings allow for higher routing density, but may be more susceptible to signal integrity issues.
- Impedance control: Maintaining consistent impedance throughout the trace length is important for high-speed signals.
- Length matching: Ensuring that traces carrying related signals are of equal length can help to minimize timing skew and improve signal integrity.
Layer Stackup
The layer stackup of an HDI PCB can have a significant impact on its performance and manufacturability. Some factors to consider include:
- Number of layers: More layers allow for more complex routing and better signal integrity, but also increase manufacturing cost and complexity.
- Material selection: The choice of dielectric materials can affect the board’s electrical and thermal properties, as well as its manufacturability.
- Copper weight: Thicker copper layers can improve current-carrying capacity and thermal dissipation, but may increase manufacturing cost and complexity.
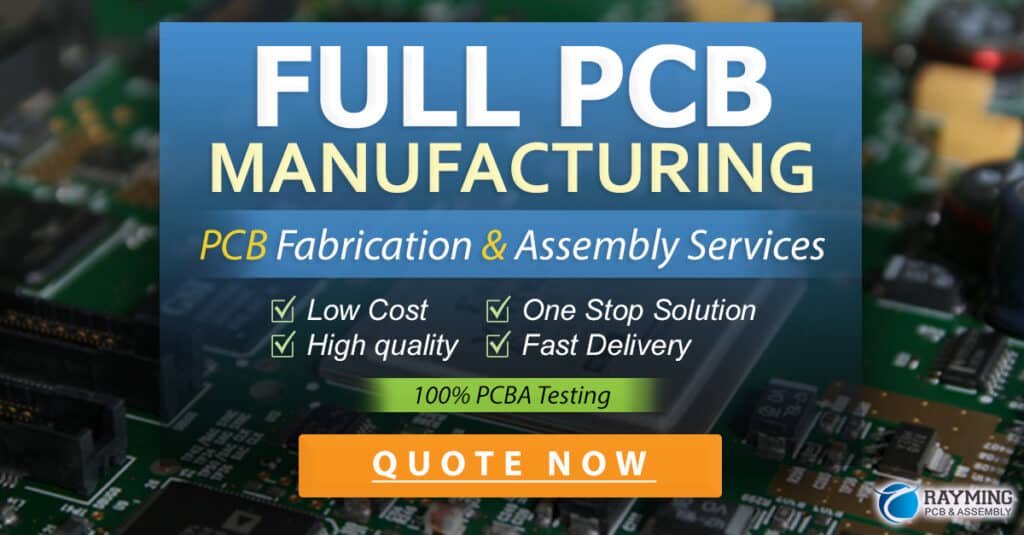
HDI PCB Manufacturing Process
The manufacturing process for HDI PCBs is more complex than that of traditional PCBs, due to the smaller features and tighter tolerances involved. The typical HDI PCB manufacturing process includes the following steps:
- Drilling: Microvias are drilled using laser or mechanical drilling techniques.
- Plating: The microvias are plated with copper to create electrical connections between layers.
- Patterning: The copper layers are patterned using photolithography and etching processes.
- Lamination: The patterned layers are laminated together using heat and pressure.
- Surface finishing: The outer layers are finished with a protective coating, such as solder mask or hard gold.
HDI PCB Design Tools and Software
To create an effective HDI PCB design, it is important to use the right tools and software. Some popular options include:
- Altium Designer
- Cadence Allegro
- Mentor Graphics PADS
- Zuken CR-8000
These tools offer features specifically tailored for HDI PCB design, such as advanced via placement, trace routing, and impedance control capabilities.
Creating the Most Suitable HDI PCB Design for Your Needs
To create the most suitable HDI PCB design for your specific needs, follow these steps:
- Define your requirements: Clearly identify your design’s functional, electrical, and mechanical requirements.
- Choose appropriate components: Select components that are well-suited for HDI design, considering factors such as package size, pitch, and thermal requirements.
- Develop a layer stackup: Create a layer stackup that balances performance, manufacturability, and cost.
- Place components and route traces: Use HDI-specific design techniques, such as via stacking and via-in-pad, to optimize component placement and trace routing.
- Simulate and verify your design: Use simulation tools to verify signal integrity, power integrity, and EMC performance, and make adjustments as needed.
- Collaborate with your manufacturer: Work closely with your PCB manufacturer to ensure that your design is optimized for their specific capabilities and processes.
HDI PCB Design Examples
To illustrate the principles of HDI PCB design, let’s consider a few examples:
Example 1: Smartphones
Smartphones are a prime example of devices that rely heavily on HDI PCB design. A typical smartphone PCB may have the following characteristics:
- 8-12 layers
- 0.4mm pitch BGA components
- 0.1mm trace width and spacing
- Blind and buried microvias
- High-density interconnect (HDI) structures, such as via-in-pad and stacked microvias
Example 2: Wearable Devices
Wearable devices, such as smartwatches and fitness trackers, also benefit from HDI PCB design. A wearable device PCB may have the following characteristics:
- 4-6 layers
- 0.5mm pitch CSP components
- 0.1mm trace width and spacing
- Blind microvias
- Flexible or rigid-flex construction
Example 3: Medical Implants
Medical implants, such as pacemakers and neurostimulators, require extremely compact and reliable PCB designs. An implantable device PCB may have the following characteristics:
- 6-8 layers
- 0.3mm pitch chip-scale package (CSP) components
- 0.075mm trace width and spacing
- Blind and buried microvias
- High-temperature, biocompatible materials
Frequently Asked Questions (FAQ)
-
What is the minimum trace width and spacing for HDI PCBs?
Typically, HDI PCBs can have trace widths and spacings as small as 0.1mm or less. However, the specific minimum dimensions will depend on the capabilities of your PCB manufacturer and the requirements of your design. -
Can HDI PCBs be used for high-power applications?
Yes, HDI PCBs can be used for high-power applications, but special considerations must be made for thermal management. This may include the use of thicker copper layers, thermal vias, or heat spreaders. -
Are HDI PCBs more expensive than traditional PCBs?
In general, HDI PCBs are more expensive than traditional PCBs due to the more complex manufacturing processes and tighter tolerances required. However, the cost difference may be offset by the reduced board size and improved performance offered by HDI designs. -
What are the most common applications for HDI PCBs?
HDI PCBs are commonly used in applications that require high component density and performance, such as smartphones, wearable devices, medical implants, aerospace and defense systems, and high-performance computing. -
How can I ensure that my HDI PCB design is manufacturable?
To ensure that your HDI PCB design is manufacturable, it is important to work closely with your PCB manufacturer from the early stages of the design process. Discuss your requirements and design choices with them, and be prepared to make adjustments based on their feedback and capabilities.
Conclusion
HDI PCB design is a powerful tool for creating compact, high-performance electronic devices. By understanding the key principles and techniques involved in HDI PCB design, you can create the most suitable design for your specific needs. Remember to consider factors such as component selection, via placement, trace routing, and layer stackup, and work closely with your PCB manufacturer to ensure the best possible results.
No responses yet