Introduction to HASL and ENIG Surface Treatment Methods
When it comes to printed circuit board (PCB) manufacturing, choosing the right surface treatment method is crucial for ensuring the reliability, durability, and performance of the final product. Two of the most commonly used surface treatment methods are Hot Air Solder Leveling (HASL) and Electroless Nickel Immersion Gold (ENIG). In this article, we will delve into the details of these two methods, comparing their advantages, disadvantages, and applications to help you make an informed decision for your PCB project.
What is HASL?
HASL, short for Hot Air Solder Leveling, is a surface treatment method that involves immersing the PCB in a molten solder bath, typically consisting of a tin-lead alloy. The excess solder is then blown off using hot air knives, resulting in a uniform and level surface finish. HASL has been a popular choice for decades due to its cost-effectiveness and ease of implementation.
What is ENIG?
ENIG, or Electroless Nickel Immersion Gold, is a more advanced surface treatment method that deposits a thin layer of nickel followed by a layer of gold onto the copper pads of the PCB. The nickel layer acts as a barrier, preventing the diffusion of copper into the gold layer, while the gold layer provides excellent solderability and protection against oxidation. ENIG has gained popularity in recent years due to its flat surface finish and compatibility with fine-pitch components.
Comparing HASL and ENIG
To make an informed decision between HASL and ENIG, it is essential to understand their key differences and how they impact the PCB’s performance. Let’s compare these two methods based on several critical factors:
1. Surface Flatness
One of the most significant differences between HASL and ENIG is the surface flatness they provide. HASL, due to the nature of the solder leveling process, results in a slightly uneven surface with a typical flatness of around 50-100 micrometers. This unevenness can pose challenges when mounting fine-pitch components or high-density interconnects.
On the other hand, ENIG provides an extremely flat surface finish, with a typical flatness of less than 5 micrometers. This flatness makes ENIG ideal for applications that require precise component placement and high-density designs.
2. Solderability
Both HASL and ENIG offer excellent solderability, ensuring a reliable connection between the components and the PCB. However, there are some differences in their soldering characteristics.
HASL, with its tin-lead alloy coating, provides a tried-and-true soldering surface that is compatible with a wide range of soldering processes. The solder layer also acts as a protective barrier, preventing oxidation of the copper pads.
ENIG, with its gold surface, offers superior wettability and solderability compared to HASL. The gold layer remains oxidation-free, ensuring consistent soldering results even after prolonged storage. However, the gold layer can dissolve into the solder joint during the soldering process, potentially affecting the joint’s mechanical properties if not controlled properly.
3. Shelf Life
The shelf life of a PCB refers to the duration it can be stored before the surface finish deteriorates and affects solderability. In this aspect, ENIG has a clear advantage over HASL.
HASL, being a tin-lead alloy, is prone to oxidation over time, which can degrade its solderability. The shelf life of a HASL-treated PCB is typically around 6-12 months, depending on the storage conditions.
ENIG, with its gold surface, provides excellent oxidation resistance and can maintain its solderability for up to 12-24 months or even longer. This extended shelf life makes ENIG a preferred choice for projects with longer lead times or where PCBs need to be stored for extended periods.
4. Cost
Cost is often a critical factor when choosing between HASL and ENIG. In general, HASL is more cost-effective than ENIG, making it a popular choice for budget-constrained projects.
The raw materials used in the HASL process, primarily tin and lead, are relatively inexpensive compared to the nickel and gold used in ENIG. Additionally, the HASL process is simpler and faster, requiring less processing time and resources.
ENIG, due to the use of more expensive materials and the additional processing steps involved, comes with a higher cost. However, the superior surface flatness, solderability, and longer shelf life offered by ENIG can justify the added cost in applications that demand high reliability and performance.
5. Environmental Considerations
Environmental regulations and sustainability concerns have become increasingly important in the electronics industry. In this context, ENIG has an advantage over HASL.
HASL, traditionally, uses a tin-lead alloy that contains lead, a hazardous substance known to have adverse effects on human health and the environment. With the introduction of the Restriction of Hazardous Substances (RoHS) directive, many manufacturers have shifted towards lead-free HASL alternatives, such as tin-silver-copper (SAC) alloys. However, these lead-free alternatives often have higher melting points and may require adjustments to the soldering process.
ENIG, being a lead-free surface treatment method, complies with RoHS regulations and is considered a more environmentally friendly option. The nickel and gold used in the ENIG process are not classified as hazardous substances, making it a preferred choice for eco-conscious projects.
Applications of HASL and ENIG
When deciding between HASL and ENIG, it is essential to consider the specific requirements and constraints of your PCB application. Here are some common applications where each method excels:
HASL Applications
- Consumer electronics
- Low-cost, high-volume production
- Applications with larger component pitches
- Projects with shorter lead times and storage requirements
ENIG Applications
- High-density designs with fine-pitch components
- Medical and aerospace electronics
- Applications requiring long shelf life and storage
- Projects demanding superior surface flatness and solderability
- Environmentally sensitive applications
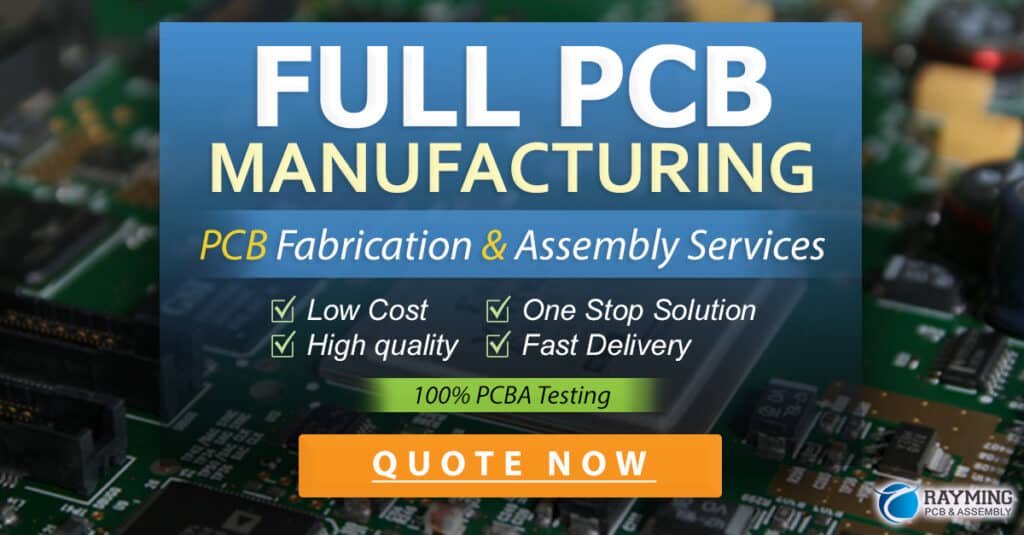
FAQ
-
Q: Can HASL be used for fine-pitch components?
A: While HASL can be used for fine-pitch components, the uneven surface finish may pose challenges in achieving reliable solder joints. ENIG is generally preferred for fine-pitch applications due to its superior surface flatness. -
Q: Is ENIG compatible with all soldering processes?
A: Yes, ENIG is compatible with a wide range of soldering processes, including reflow soldering, wave soldering, and hand soldering. However, it is essential to control the soldering temperature and duration to prevent excessive dissolution of the gold layer into the solder joint. -
Q: Are there any lead-free alternatives to HASL?
A: Yes, lead-free HASL alternatives, such as tin-silver-copper (SAC) alloys, have been developed to comply with RoHS regulations. These alternatives provide similar performance to traditional tin-lead HASL but may require adjustments to the soldering process due to their higher melting points. -
Q: How does the shelf life of HASL and ENIG compare?
A: ENIG offers a significantly longer shelf life compared to HASL. ENIG-treated PCBs can maintain their solderability for up to 12-24 months or more, while HASL-treated PCBs typically have a shelf life of 6-12 months. -
Q: Is it possible to use both HASL and ENIG on the same PCB?
A: While it is technically possible to use both HASL and ENIG on the same PCB, it is generally not recommended. The different surface finishes may have different soldering characteristics, which can lead to inconsistencies in the solder joints. It is best to choose one surface treatment method that suits the specific requirements of your application.
Conclusion
Choosing the right surface treatment method between HASL and ENIG depends on a variety of factors, including surface flatness requirements, solderability, shelf life, cost, and environmental considerations. HASL, with its cost-effectiveness and compatibility with a wide range of soldering processes, remains a popular choice for many PCB applications. However, ENIG has gained popularity in recent years due to its superior surface flatness, excellent solderability, and longer shelf life, making it ideal for high-density designs and applications demanding high reliability.
When deciding between HASL and ENIG, it is crucial to carefully evaluate the specific requirements and constraints of your PCB project. By understanding the strengths and limitations of each method, you can make an informed decision that ensures the optimal performance, reliability, and cost-effectiveness of your PCB assembly.
Factor | HASL | ENIG |
---|---|---|
Surface Flatness | Uneven (50-100 μm) | Flat (<5 μm) |
Solderability | Good, compatible with various processes | Excellent, superior wettability |
Shelf Life | 6-12 months | 12-24 months or longer |
Cost | Lower, cost-effective | Higher, due to materials and processing |
Environmental | Contains lead (RoHS non-compliant) | Lead-free, RoHS compliant |
Applications | Consumer electronics, low-cost production | High-density designs, medical, aerospace |
Ultimately, the choice between HASL and ENIG comes down to finding the right balance between performance, reliability, cost, and environmental considerations for your specific PCB application. By carefully weighing these factors and consulting with experienced PCB manufacturers, you can ensure that your PCB assembly meets the highest standards of quality and functionality.
No responses yet