What is HASL?
HASL is a widely used PCB surface finish that involves dipping the board into a molten solder bath and then using hot air to level the surface. The process results in a thin layer of solder covering the exposed copper pads and traces, providing protection against oxidation and enhancing solderability.
Advantages of HASL
- Cost-effective: HASL is one of the most affordable surface finish options available.
- Excellent solderability: The solder layer on the surface ensures good wetting and strong solder joints.
- Durability: HASL provides adequate protection against oxidation and corrosion.
Disadvantages of HASL
- Uneven surface: The hot air leveling process can result in an uneven surface, which may cause issues with fine-pitch components.
- Limited flatness: HASL boards may not be suitable for high-density designs that require a high degree of flatness.
- Thermal shock: The high-temperature process can cause thermal shock to the PCB, potentially leading to warping or other defects.
What is ENIG?
ENIG is a more advanced PCB surface finish that involves depositing a thin layer of electroless nickel followed by a thin layer of immersion gold. The nickel layer provides a barrier against copper diffusion, while the gold layer protects the nickel from oxidation and enhances solderability.
Advantages of ENIG
- Flat surface: ENIG provides a flat and uniform surface, making it suitable for fine-pitch components and high-density designs.
- Excellent solderability: The gold layer ensures good wetting and strong solder joints.
- Longer shelf life: ENIG offers better protection against oxidation, resulting in a longer shelf life compared to HASL.
- Wire bonding compatibility: The gold surface is suitable for wire bonding applications.
Disadvantages of ENIG
- Higher cost: ENIG is more expensive than HASL due to the additional processing steps and materials involved.
- Black pad syndrome: In some cases, the nickel layer may separate from the copper pad, causing a defect known as “black pad syndrome.”
- Brittle solder joints: The presence of a thick nickel layer can lead to brittle solder joints, especially with lead-free solder alloys.
HASL-ENIG-Comparison“>HASL-ENIG-Comparison
Parameter | HASL | ENIG |
---|---|---|
Cost | Low | High |
Surface Flatness | Uneven | Flat |
Solderability | Excellent | Excellent |
Shelf Life | Moderate | Long |
Fine-Pitch Compatibility | Limited | Excellent |
Wire Bonding Compatibility | Not Suitable | Suitable |
Thermal Shock Risk | High | Low |
Black Pad Syndrome Risk | None | Moderate |
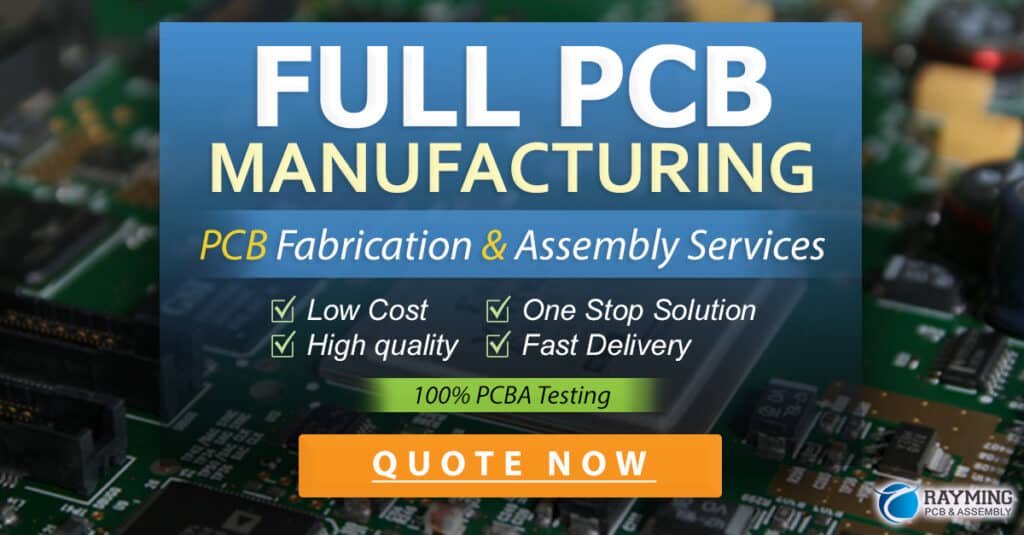
10 Tips on How to Choose ENIG Plating
-
Consider your budget: ENIG is more expensive than HASL, so ensure that your project budget can accommodate the additional cost.
-
Evaluate your design requirements: If your PCB design involves fine-pitch components or requires a high degree of surface flatness, ENIG may be the better choice.
-
Assess your shelf life needs: If your PCBs need to be stored for an extended period before assembly, ENIG’s longer shelf life may be advantageous.
-
Determine wire bonding requirements: If your application requires wire bonding, ENIG’s gold surface makes it a suitable option.
-
Consider the risk of black pad syndrome: While rare, black pad syndrome can occur with ENIG. Work with your PCB manufacturer to minimize this risk.
-
Evaluate your soldering process: Ensure that your soldering process is compatible with ENIG, as the nickel layer can affect solder joint formation.
-
Assess your thermal shock concerns: If your PCB is sensitive to thermal shock, ENIG may be preferable to HASL due to its lower processing temperatures.
-
Consider your reliability requirements: ENIG generally offers better long-term reliability compared to HASL, especially in harsh environments.
-
Evaluate your PCB manufacturer’s capabilities: Ensure that your chosen PCB manufacturer has experience and expertise in producing ENIG boards.
-
Conduct thorough testing: Before committing to ENIG for your entire production run, conduct thorough testing to ensure that it meets your performance and reliability requirements.
Frequently Asked Questions (FAQ)
-
Q: Is ENIG always better than HASL?
A: Not necessarily. The choice between ENIG and HASL depends on your specific project requirements, budget, and design constraints. While ENIG offers several advantages, such as better surface flatness and longer shelf life, HASL remains a cost-effective and reliable option for many applications. -
Q: Can ENIG be used for both lead-free and leaded soldering processes?
A: Yes, ENIG is compatible with both lead-free and leaded soldering processes. However, it’s essential to optimize your soldering process parameters to ensure good solder joint formation and minimize the risk of brittle joints, especially with lead-free solder alloys. -
Q: How can I minimize the risk of black pad syndrome with ENIG?
A: To minimize the risk of black pad syndrome, work closely with your PCB manufacturer to ensure that they follow best practices for ENIG processing, such as proper control of the nickel and gold plating thicknesses, optimized plating bath chemistry, and thorough cleaning and inspection procedures. -
Q: Is ENIG suitable for high-temperature applications?
A: Yes, ENIG is generally suitable for high-temperature applications due to its excellent thermal stability and resistance to oxidation. However, it’s essential to consider the specific requirements of your application and consult with your PCB manufacturer to ensure that ENIG is the best choice for your needs. -
Q: Can I switch from HASL to ENIG without redesigning my PCB?
A: In most cases, you can switch from HASL to ENIG without significant changes to your PCB design. However, it’s always a good idea to review your design with your PCB manufacturer to ensure that it is optimized for ENIG processing and to identify any potential issues or concerns.
In conclusion, choosing between HASL and ENIG for your PCB surface finish requires careful consideration of your project requirements, budget, and design constraints. By understanding the advantages and disadvantages of each option and following the tips outlined in this article, you can make an informed decision and ensure the success of your PCB project.
No responses yet