Introduction to Halogen-free PCBs
Halogen-free printed circuit boards (PCBs) have gained popularity in recent years due to growing environmental and health concerns associated with the use of halogenated materials in electronic products. Halogens, such as chlorine and bromine, are often used as flame retardants in PCBs to improve their fire resistance. However, when exposed to high temperatures, these materials can release toxic fumes that pose a threat to human health and the environment.
In response to these concerns, halogen-free PCBs have been developed as a safer and more eco-friendly alternative. These PCBs use alternative flame retardants that do not contain halogens, reducing the risk of toxic fume release during a fire.
Benefits of Halogen-free PCBs
- Improved safety: Halogen-free PCBs reduce the risk of toxic fume release during a fire, ensuring a safer environment for users and firefighters.
- Environmental friendliness: By eliminating the use of halogens, these PCBs minimize the release of harmful substances into the environment during production, use, and disposal.
- Compliance with regulations: Many countries and organizations have implemented regulations that restrict or prohibit the use of halogenated materials in electronic products. Using halogen-free PCBs helps manufacturers comply with these regulations.
- Enhanced reliability: Halogen-free PCBs often exhibit improved thermal stability and reduced corrosion, leading to better overall reliability of the electronic product.
Key Considerations When Buying Halogen-free PCBs
When purchasing halogen-free PCBs, there are several key factors to consider to ensure that you select the best product for your needs.
1. Material Composition
Halogen-free PCBs can be made from various base materials, each with its own set of properties and advantages. Some common halogen-free PCB materials include:
Material | Description | Advantages |
---|---|---|
FR-4 | A composite material made of woven fiberglass cloth with an epoxy resin binder. | – Good mechanical and electrical properties – Cost-effective – Widely available |
Polyimide | A high-performance polymer known for its excellent thermal and chemical stability. | – High heat resistance – Excellent dimensional stability – Good electrical properties |
PTFE | Polytetrafluoroethylene, a synthetic fluoropolymer with outstanding electrical and thermal properties. | – Low dielectric constant and loss – High thermal stability – Excellent chemical resistance |
When selecting a material for your halogen-free PCB, consider the specific requirements of your application, such as operating temperature, electrical performance, and mechanical stability.
2. Flame Retardant Rating
Halogen-free PCBs use alternative flame retardants to achieve the desired level of fire resistance. The flame retardant rating of a PCB indicates its ability to withstand and self-extinguish flames. The most common flame retardant ratings for PCBs are:
- UL 94 V-0: The highest rating, indicating that the PCB self-extinguishes within 10 seconds after two flame applications, with no burning drops.
- UL 94 V-1: The PCB self-extinguishes within 30 seconds after two flame applications, with no burning drops.
- UL 94 V-2: The PCB self-extinguishes within 30 seconds after two flame applications, but burning drops are allowed.
When choosing a halogen-free PCB, select a flame retardant rating that meets the requirements of your application and the applicable safety standards.
3. Layer Count and Thickness
The number of layers and thickness of a halogen-free PCB can impact its performance, cost, and manufacturability. Consider the following factors when selecting the layer count and thickness:
- Complexity of the circuit design
- Required signal integrity and power distribution
- Mechanical strength and rigidity
- Space constraints within the end product
- Manufacturing capabilities of the PCB supplier
Work closely with your PCB supplier to determine the optimal layer count and thickness for your specific application.
4. Surface Finish
The surface finish of a halogen-free PCB plays a critical role in ensuring reliable solderability, protecting the exposed copper traces, and enhancing the PCB’s shelf life. Some common halogen-free surface finishes include:
Surface Finish | Description | Advantages |
---|---|---|
ENIG (Electroless Nickel Immersion Gold) | A two-layer finish with a nickel base and a thin gold top layer. | – Excellent solderability – Good shelf life – Suitable for fine-pitch components |
HASL (Hot Air Solder Leveling) | A finish that involves dipping the PCB in molten solder and then removing the excess solder using hot air. | – Cost-effective – Good solderability – Widely available |
OSP (Organic Solderability Preservative) | A thin, organic coating applied to the exposed copper traces to prevent oxidation. | – Low cost – Flat surface finish – Suitable for fine-pitch components |
Select a surface finish that provides the desired level of solderability, protection, and compatibility with your assembly process and end-use environment.
5. Manufacturer Reputation and Certifications
When choosing a halogen-free PCB supplier, consider their reputation, experience, and certifications. Look for manufacturers with:
- Proven track record of producing high-quality halogen-free PCBs
- Strict quality control processes and standards (e.g., ISO 9001, IPC Class 2 or 3)
- Compliance with relevant environmental regulations (e.g., RoHS, REACH)
- Experience in serving your industry or application area
- Responsive customer support and technical assistance
Selecting a reputable manufacturer with the necessary certifications and experience can help ensure that you receive high-quality halogen-free PCBs that meet your specific requirements.
Halogen-free PCB Manufacturing Process
Understanding the manufacturing process of halogen-free PCBs can help you appreciate the complexities involved and make informed decisions when selecting a supplier.
-
Design and Verification: The PCB design is created using CAD software, and the design files are verified for accuracy and manufacturability.
-
Material Selection: The appropriate halogen-free PCB material is selected based on the design requirements and specifications.
-
Imaging and Etching: The circuit pattern is transferred onto the PCB substrate using photolithography, and the unwanted copper is etched away.
-
Drilling and Plating: Holes are drilled in the PCB for component placement and interconnections, and the holes are plated with copper to establish electrical connections between layers.
-
Solder Mask Application: A protective solder mask is applied to the PCB surface, leaving only the exposed pads and contact points.
-
Surface Finish Application: The chosen surface finish is applied to the exposed copper areas to improve solderability and protect against oxidation.
-
Silkscreen Printing: Text, logos, and component identifiers are printed onto the PCB surface using silkscreen printing.
-
Electrical Testing and Inspection: The manufactured PCBs undergo thorough electrical testing and visual inspection to ensure they meet the required quality standards.
-
Packaging and Shipping: The finished halogen-free PCBs are packaged and shipped to the customer.
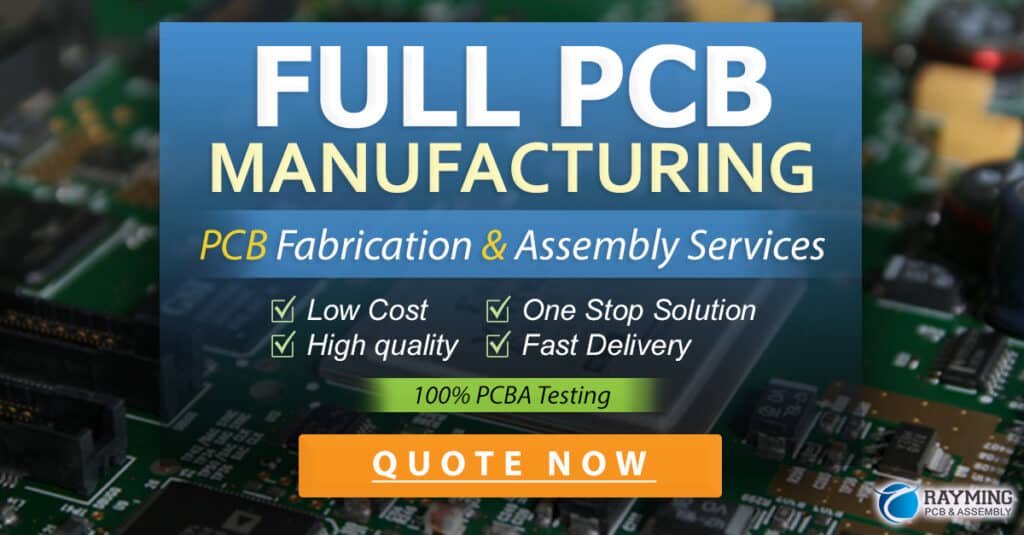
Halogen-free PCB Applications
Halogen-free PCBs find applications in various industries and product categories, particularly where environmental friendliness, human health, and safety are of utmost importance. Some common applications include:
- Consumer Electronics: Smartphones, tablets, laptops, and other portable devices.
- Automotive Electronics: In-vehicle infotainment systems, sensors, and control units.
- Medical Devices: Diagnostic equipment, monitoring systems, and implantable devices.
- Industrial Automation: Process control systems, sensors, and communication devices.
- Aerospace and Defense: Avionics, communication systems, and satellite components.
- Green Energy: Solar inverters, wind turbine control systems, and energy storage devices.
As environmental regulations become more stringent and consumer awareness grows, the demand for halogen-free PCBs is expected to increase across various industries.
FAQ
-
What are the main differences between halogen-free and traditional PCBs?
Halogen-free PCBs use alternative flame retardants that do not contain halogens (chlorine and bromine), while traditional PCBs often use halogenated flame retardants. Halogen-free PCBs offer improved safety, environmental friendliness, and compliance with regulations, but may come at a higher cost. -
Are halogen-free PCBs more expensive than traditional PCBs?
Yes, halogen-free PCBs are generally more expensive than traditional PCBs due to the specialized materials and processes involved in their manufacture. However, the added cost is often justified by the improved safety, environmental benefits, and compliance with regulations. -
Can halogen-free PCBs be used in high-temperature applications?
Yes, certain halogen-free PCB materials, such as polyimide and PTFE, offer excellent thermal stability and can be used in high-temperature applications. However, it is essential to select the appropriate material and work closely with your PCB supplier to ensure the PCB meets your specific thermal requirements. -
Are all halogen-free PCBs RoHS compliant?
While most halogen-free PCBs are designed to be RoHS compliant, it is essential to verify compliance with your PCB supplier. Some halogen-free PCBs may still contain other restricted substances, so it is crucial to ensure that the PCB meets all the necessary environmental regulations for your application. -
How do I choose the right halogen-free PCB supplier for my project?
When selecting a halogen-free PCB supplier, consider factors such as their reputation, experience, certifications, quality control processes, and customer support. Look for suppliers with a proven track record of producing high-quality halogen-free PCBs, compliance with relevant regulations, and experience in serving your industry or application area.
Conclusion
Halogen-free PCBs offer a safer, more environmentally friendly alternative to traditional PCBs that use halogenated flame retardants. By eliminating the use of halogens, these PCBs reduce the risk of toxic fume release during a fire and minimize the environmental impact of electronic products.
When purchasing halogen-free PCBs, consider key factors such as material composition, flame retardant rating, layer count and thickness, surface finish, and manufacturer reputation and certifications. By carefully evaluating these factors and working closely with a reputable PCB supplier, you can ensure that you select the best halogen-free PCB for your specific application.
As environmental regulations continue to evolve and consumer demand for eco-friendly products grows, the adoption of halogen-free PCBs is expected to increase across various industries. By staying informed about the latest developments in halogen-free PCB technology and best practices for procurement, you can make informed decisions that benefit both your business and the environment.
No responses yet