What is a Ground Plane in PCB Design?
A ground plane is a large area of copper foil on a printed circuit board (PCB) that is used as a return path for circuit current and to provide a stable reference voltage for circuit components. The ground plane is typically located on one or more layers of the PCB and covers a significant portion of the board area.
The primary purpose of a ground plane is to provide a low-impedance return path for current flowing through the circuit components. By minimizing the impedance of the return path, the ground plane helps to reduce noise, crosstalk, and electromagnetic interference (EMI) in the circuit.
Advantages of Using a Ground Plane in PCB Design
There are several advantages to using a ground plane in PCB design:
-
Reduced Impedance: The large area of the ground plane provides a low-impedance return path for current, which helps to minimize noise and interference in the circuit.
-
Improved Signal Integrity: The ground plane acts as a shield between signal traces, reducing crosstalk and improving signal integrity.
-
Enhanced EMI Suppression: The ground plane helps to suppress electromagnetic radiation from the circuit, reducing EMI and improving electromagnetic compatibility (EMC).
-
Better Heat Dissipation: The large area of the ground plane helps to dissipate heat generated by circuit components, improving thermal performance and reliability.
-
Simplified Layout: Using a ground plane can simplify the PCB layout process by reducing the need for complex routing of return paths.
Designing a Ground Plane PCB
When designing a ground plane PCB, there are several factors to consider to ensure optimal performance and reliability.
Choosing the Right Layer for the Ground Plane
The first step in designing a ground plane PCB is to choose the appropriate layer or layers for the ground plane. In a multi-layer PCB, the ground plane is typically located on one or more of the inner layers, while the outer layers are used for signal traces and components.
The choice of layer for the ground plane depends on several factors, including the frequency and power requirements of the circuit, the available board space, and the manufacturing constraints. In general, placing the ground plane on an inner layer helps to shield the signal traces from external interference and reduces the risk of accidental shorts or damage during assembly.
Determining the Size and Shape of the Ground Plane
The size and shape of the ground plane are critical factors in determining its effectiveness as a return path and EMI shield. In general, the ground plane should cover as much of the board area as possible, with a minimum of interruptions or gaps.
However, there are some situations where it may be necessary to create openings or cutouts in the ground plane, such as to accommodate through-hole components or to provide isolation between different sections of the circuit. When creating openings in the ground plane, it is important to minimize their size and number and to ensure that they do not create discontinuities or impedance mismatches in the return path.
Connecting Components to the Ground Plane
To ensure a low-impedance return path for current, it is important to connect all circuit components directly to the ground plane using short, wide traces or vias. This helps to minimize the inductance and resistance of the return path and reduces the risk of voltage drops or ground loops.
When connecting components to the ground plane, it is also important to consider the current requirements of each component and to ensure that the traces or vias are sized appropriately to handle the expected current flow. In addition, it is important to minimize the number of vias used to connect components to the ground plane, as each via introduces a small amount of inductance and resistance into the return path.
Splitting the Ground Plane for Analog and Digital Circuits
In some cases, it may be necessary to split the ground plane into separate sections for analog and digital circuits to prevent noise coupling between the two domains. This is particularly important in mixed-signal designs where sensitive analog circuits are located near noisy digital circuits.
When splitting the ground plane, it is important to ensure that the separate sections are still connected to a common reference point, such as the power supply ground or chassis ground. This helps to prevent ground loops and ensures that all sections of the circuit have a stable reference voltage.
Implementing a Ground Plane in a High-Speed PCB Design
In high-speed PCB designs, the implementation of a ground plane becomes even more critical due to the increased risk of signal integrity issues and EMI. At high frequencies, the impedance of the return path becomes a significant factor in determining the quality of the signal and the level of noise and interference in the circuit.
To ensure optimal performance in high-speed designs, it is important to use a continuous ground plane with minimal interruptions or gaps. In addition, it may be necessary to use techniques such as high-frequency decoupling and careful placement of components to minimize the effects of parasitic inductance and capacitance.
Ground Plane Materials and Manufacturing Considerations
When choosing materials for a ground plane PCB, there are several factors to consider, including the electrical and thermal properties of the material, the manufacturability of the design, and the cost.
Copper vs. Other Materials for Ground Planes
Copper is the most commonly used material for ground planes in PCB design due to its excellent electrical and thermal conductivity, as well as its relatively low cost and ease of manufacturing. However, in some cases, other materials such as aluminum or carbon fiber may be used for specialized applications.
Aluminum is sometimes used as a ground plane material in high-power applications where heat dissipation is a primary concern. Carbon fiber is another alternative material that offers high strength and stiffness, as well as good electrical and thermal conductivity, but at a higher cost than copper.
Manufacturing Considerations for Ground Plane PCBs
When manufacturing a ground plane PCB, there are several additional considerations to keep in mind to ensure optimal performance and reliability.
One important factor is the thickness of the copper foil used for the ground plane. Thicker copper foil provides lower impedance and better heat dissipation, but may also increase the cost and complexity of manufacturing.
Another consideration is the surface finish of the ground plane. In some cases, it may be necessary to apply a surface finish such as ENIG (Electroless Nickel Immersion Gold) or OSP (Organic Solderability Preservative) to protect the copper from oxidation and improve solderability.
Finally, it is important to ensure that the manufacturing process is capable of producing a high-quality ground plane with minimal defects or discontinuities. This may require specialized equipment and processes, such as controlled impedance routing or high-density interconnect (HDI) technology.
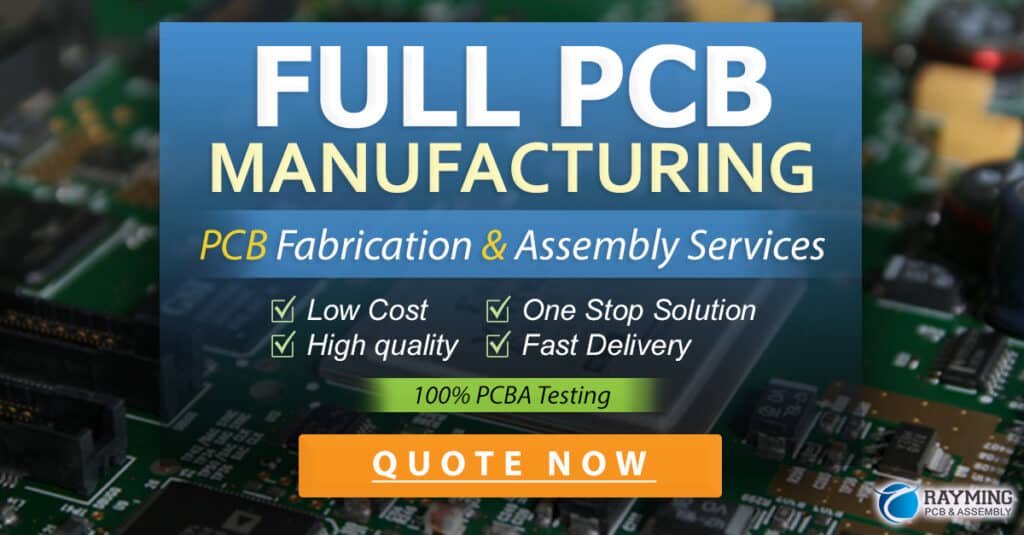
Frequently Asked Questions (FAQ)
1. What is the purpose of a ground plane in PCB design?
The primary purpose of a ground plane in PCB design is to provide a low-impedance return path for current flowing through the circuit components, and to provide a stable reference voltage for the circuit. The ground plane also helps to reduce noise, crosstalk, and electromagnetic interference (EMI) in the circuit.
2. How does a ground plane improve signal integrity in a PCB?
A ground plane improves signal integrity in a PCB by acting as a shield between signal traces, reducing crosstalk and minimizing the effects of external interference. The low-impedance return path provided by the ground plane also helps to maintain a stable reference voltage for the signals, reducing noise and improving signal quality.
3. Can a ground plane be split into separate sections for analog and digital circuits?
Yes, in some cases it may be necessary to split the ground plane into separate sections for analog and digital circuits to prevent noise coupling between the two domains. However, it is important to ensure that the separate sections are still connected to a common reference point, such as the power supply ground or chassis ground, to prevent ground loops and ensure a stable reference voltage.
4. What materials can be used for ground planes in PCB design?
Copper is the most commonly used material for ground planes in PCB design due to its excellent electrical and thermal conductivity, as well as its relatively low cost and ease of manufacturing. However, in some specialized applications, other materials such as aluminum or carbon fiber may be used for their unique properties.
5. What are some manufacturing considerations for ground plane PCBs?
Some important manufacturing considerations for ground plane PCBs include the thickness of the copper foil used for the ground plane, the surface finish applied to protect the copper from oxidation and improve solderability, and the capability of the manufacturing process to produce a high-quality ground plane with minimal defects or discontinuities. Specialized equipment and processes, such as controlled impedance routing or HDI technology, may be required to ensure optimal performance and reliability.
Conclusion
Ground planes are a critical component of PCB design, providing a low-impedance return path for current and a stable reference voltage for circuit components. By minimizing noise, crosstalk, and EMI, ground planes help to ensure signal integrity and improve the overall performance and reliability of the circuit.
When designing a ground plane PCB, it is important to consider factors such as the size and shape of the ground plane, the placement of components and vias, and the choice of materials and manufacturing processes. By following best practices and carefully considering these factors, designers can create high-quality ground plane PCBs that meet the performance and reliability requirements of even the most demanding applications.
No responses yet