What is a Glass PCB?
A glass printed circuit board (PCB) is a type of PCB that uses glass as the base material instead of the more commonly used FR-4 (flame retardant 4) material. Glass PCBs offer several advantages over traditional PCBs, including better thermal stability, lower dielectric constant, and higher resistance to chemicals and moisture.
Composition of Glass PCBs
Glass PCBs are made from a combination of glass fabric and epoxy resin. The glass fabric provides the structural strength and stability, while the epoxy resin acts as an insulating layer and binds the glass fabric together. The most common type of glass used in PCBs is E-glass, which is a low-alkali borosilicate glass.
Manufacturing Process of Glass PCBs
The manufacturing process of glass PCBs is similar to that of traditional PCBs, but with a few key differences:
-
Cutting and drilling: The glass fabric is cut to the desired size and shape, and holes are drilled for through-hole components and vias.
-
Lamination: The glass fabric is laminated with epoxy resin under high temperature and pressure to create a solid, stable base material.
-
Copper foil application: A thin layer of copper foil is applied to one or both sides of the laminated glass substrate using an adhesive.
-
Patterning: The desired circuit pattern is transferred onto the copper foil using photolithography or screen printing techniques.
-
Etching: The unwanted copper is removed using a chemical etching process, leaving behind the desired circuit pattern.
-
Solder mask application: A protective solder mask layer is applied over the copper traces to prevent short circuits and improve the PCB’s durability.
-
Surface finish application: A surface finish, such as HASL (Hot Air Solder Leveling) or ENIG (Electroless Nickel Immersion Gold), is applied to the exposed copper areas to prevent oxidation and improve solderability.
Advantages of Glass PCBs
1. Excellent Thermal Stability
Glass PCBs have a coefficient of thermal expansion (CTE) that is much closer to that of silicon chips compared to FR-4 PCBs. This means that glass PCBs experience less thermal stress and are less likely to warp or deform under high temperatures. This makes glass PCBs ideal for applications that require high thermal stability, such as high-power electronics and aerospace systems.
2. Low Dielectric Constant
Glass PCBs have a lower dielectric constant compared to FR-4 PCBs, which means they have lower capacitance and lower signal propagation delay. This makes glass PCBs suitable for high-frequency applications, such as 5G communication systems and radar systems.
3. High Resistance to Chemicals and Moisture
Glass PCBs are highly resistant to chemicals and moisture, thanks to the inert nature of glass and the strong bond between the glass fabric and epoxy resin. This makes glass PCBs suitable for applications that require exposure to harsh environments, such as automotive and industrial systems.
4. Improved Mechanical Strength
Glass PCBs have higher mechanical strength compared to FR-4 PCBs, thanks to the high tensile strength of glass fibers. This makes glass PCBs less likely to crack or break under mechanical stress, improving the overall reliability of the system.
Disadvantages of Glass PCBs
1. Higher Cost
Glass PCBs are generally more expensive than FR-4 PCBs due to the higher cost of glass fabric and the more complex manufacturing process. This can make glass PCBs less attractive for cost-sensitive applications.
2. Limited Flexibility
Glass PCBs are less flexible than FR-4 PCBs due to the rigid nature of glass. This can make glass PCBs unsuitable for applications that require flexibility, such as wearable electronics and flexible displays.
3. Difficulty in Machining
Glass PCBs are harder and more brittle than FR-4 PCBs, which can make them more difficult to machine and drill. This can increase the manufacturing time and cost of glass PCBs.
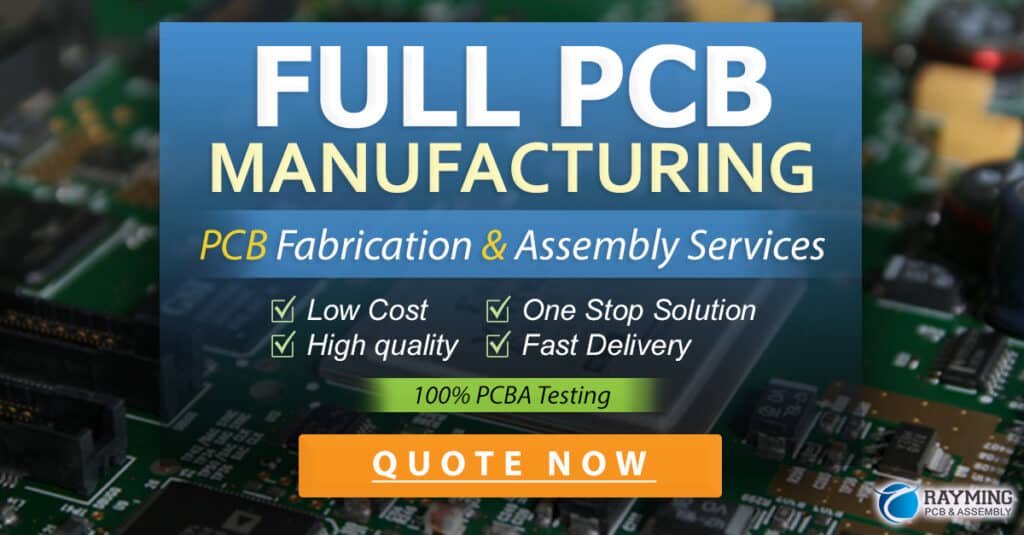
Applications of Glass PCBs
1. High-Frequency Applications
Glass PCBs are widely used in high-frequency applications, such as:
- 5G communication systems
- Radar systems
- Satellite communication systems
- High-speed digital systems
The low dielectric constant and low loss tangent of glass PCBs make them ideal for these applications, as they enable faster signal propagation and lower signal attenuation.
2. High-Power Applications
Glass PCBs are also used in high-power applications, such as:
- Power electronics
- Electric vehicles
- Renewable energy systems
- Aerospace systems
The excellent thermal stability and high mechanical strength of glass PCBs make them suitable for these applications, as they can withstand high temperatures and mechanical stresses.
3. Harsh Environment Applications
Glass PCBs are used in applications that require exposure to harsh environments, such as:
- Automotive systems
- Industrial systems
- Oil and gas systems
- Medical devices
The high resistance to chemicals and moisture of glass PCBs makes them suitable for these applications, as they can withstand exposure to corrosive substances and extreme conditions.
Frequently Asked Questions (FAQ)
1. Are glass PCBs more expensive than traditional PCBs?
Yes, glass PCBs are generally more expensive than traditional FR-4 PCBs due to the higher cost of glass fabric and the more complex manufacturing process.
2. Can glass PCBs be used for flexible applications?
No, glass PCBs are less flexible than FR-4 PCBs due to the rigid nature of glass. They are not suitable for applications that require flexibility, such as wearable electronics and flexible displays.
3. What are the main advantages of using glass PCBs?
The main advantages of using glass PCBs include excellent thermal stability, low dielectric constant, high resistance to chemicals and moisture, and improved mechanical strength.
4. What are the most common applications of glass PCBs?
The most common applications of glass PCBs include high-frequency applications (e.g., 5G communication systems, radar systems), high-power applications (e.g., power electronics, electric vehicles), and harsh environment applications (e.g., automotive systems, industrial systems).
5. How do glass PCBs differ from ceramic PCBs?
Glass PCBs and ceramic PCBs are both used in high-performance applications, but they differ in their composition and properties. Glass PCBs are made from glass fabric and epoxy resin, while ceramic PCBs are made from ceramic materials such as alumina or aluminum nitride. Ceramic PCBs have even higher thermal stability and lower dielectric constant compared to glass PCBs, but they are also more expensive and more difficult to manufacture.
Conclusion
Glass PCBs are a high-performance alternative to traditional FR-4 PCBs, offering excellent thermal stability, low dielectric constant, high resistance to chemicals and moisture, and improved mechanical strength. While they are more expensive and less flexible than FR-4 PCBs, glass PCBs are widely used in applications that require high reliability and performance, such as high-frequency systems, high-power electronics, and harsh environment applications.
As the demand for high-performance electronics continues to grow, glass PCBs are expected to play an increasingly important role in enabling the next generation of technologies, from 5G communication systems to electric vehicles and aerospace systems. By understanding the advantages and limitations of glass PCBs, engineers and designers can make informed decisions when selecting the best materials and manufacturing processes for their applications.
No responses yet