Introduction to Frequency-Voltage Converters
A frequency-voltage converter, also known as an F/V converter or a tachometer signal conditioner, is an electronic device that converts a frequency signal into a proportional voltage signal. This conversion is essential in various applications where a mechanical signal, such as rotational speed or pulse rate, needs to be translated into an electrical signal for further processing, monitoring, or control purposes.
Frequency-voltage converters play a crucial role in bridging the gap between mechanical systems and electrical systems, enabling seamless integration and communication between them. These converters find extensive use in industrial automation, automotive systems, aerospace applications, and scientific instrumentation.
Key Features of Frequency-Voltage Converters
-
Proportional Output: The output voltage of a frequency-voltage converter is directly proportional to the input frequency signal. This linear relationship allows for accurate representation of the mechanical signal in the electrical domain.
-
Wide Frequency Range: Frequency-voltage converters can handle a wide range of input frequencies, typically from a few hertz to several kilohertz. This versatility makes them suitable for various applications with different frequency requirements.
-
Adjustable Scaling: Most frequency-voltage converters offer adjustable scaling or gain settings, allowing users to customize the output voltage range according to their specific needs. This feature ensures compatibility with different measurement and control systems.
-
High Accuracy: Frequency-voltage converters are designed to provide high accuracy in signal conversion. They minimize errors and maintain a stable output voltage even in the presence of noise or signal fluctuations.
-
Isolation: Many frequency-voltage converters incorporate galvanic isolation between the input and output circuits. This isolation prevents ground loops, reduces noise interference, and enhances the overall signal integrity.
Applications of Frequency-Voltage Converters
Frequency-voltage converters find applications in a wide range of industries and domains. Some common applications include:
-
Motor Speed Control: In industrial automation and robotics, frequency-voltage converters are used to measure and control the speed of motors. The rotational speed of a motor generates a frequency signal, which is converted into a voltage signal for feedback and control purposes.
-
Flow Measurement: Frequency-voltage converters are employed in flow measurement systems, such as turbine flow meters or positive displacement flow meters. The frequency of the pulses generated by the flow meter is converted into a voltage signal, providing an accurate representation of the flow rate.
-
Tachometers: Tachometers, used in automotive and aerospace applications, rely on frequency-voltage converters to measure and display the rotational speed of engines, shafts, or other rotating components.
-
Pulse Counting: In various industrial processes, frequency-voltage converters are used to count pulses generated by sensors or encoders. The frequency of the pulses is converted into a voltage signal, allowing for precise tracking and monitoring of events or quantities.
-
Scientific Instrumentation: Frequency-voltage converters are utilized in scientific instruments, such as oscilloscopes, spectrum analyzers, and data acquisition systems. They enable the conversion of frequency-based signals into voltage signals for analysis and data processing.
Working Principle of Frequency-Voltage Converters
The working principle of a frequency-voltage converter revolves around the conversion of a frequency signal into a proportional voltage signal. Let’s explore the key components and the step-by-step process involved in this conversion.
Block Diagram of a Frequency-Voltage Converter
A typical frequency-voltage converter consists of the following components:
-
Input Stage: The input stage receives the frequency signal from the mechanical system or sensor. It may include signal conditioning circuitry to filter and shape the input signal.
-
Frequency-to-Voltage Conversion Circuit: This is the core component of the converter, responsible for translating the frequency signal into a proportional voltage signal. It typically employs a frequency-to-voltage conversion technique, such as a charge pump or a phase-locked loop (PLL).
-
Scaling and Offset Adjustment: The scaling and offset adjustment circuitry allows users to fine-tune the output voltage range and offset according to their specific requirements. This ensures compatibility with the target measurement or control system.
-
Output Stage: The output stage provides the final voltage signal that represents the input frequency. It may include additional signal conditioning, such as filtering or buffering, to improve the signal quality and drive capability.
Step-by-Step Conversion Process
-
Frequency Signal Input: The frequency signal, generated by a mechanical system or sensor, is fed into the input stage of the frequency-voltage converter. This signal can be in the form of pulses, square waves, or sinusoidal waveforms.
-
Signal Conditioning: The input stage may perform signal conditioning to remove noise, filter out unwanted frequencies, and shape the input signal into a suitable form for the conversion circuit. This ensures a clean and reliable frequency signal for accurate conversion.
-
Frequency-to-Voltage Conversion: The conditioned frequency signal enters the frequency-to-voltage conversion circuit. Depending on the specific technique employed, the circuit converts the frequency into a proportional voltage signal. Common techniques include:
- Charge Pump: In this technique, the frequency signal controls the charging and discharging of a capacitor. The resulting voltage across the capacitor is proportional to the input frequency.
-
Phase-Locked Loop (PLL): PLL-based converters compare the input frequency with a reference frequency and generate an error signal. This error signal is then converted into a proportional voltage using a loop filter and voltage-controlled oscillator (VCO).
-
Scaling and Offset Adjustment: The converted voltage signal may require scaling and offset adjustment to match the desired output voltage range. This is achieved through the scaling and offset adjustment circuitry, which allows users to calibrate the converter for their specific application.
-
Output Signal: The scaled and adjusted voltage signal is provided at the output stage of the frequency-voltage converter. This output voltage is directly proportional to the input frequency and can be used for measurement, monitoring, or control purposes in the target system.
Calibration and Accuracy Considerations
To ensure accurate and reliable frequency-to-voltage conversion, proper calibration of the converter is crucial. Calibration involves setting the appropriate scaling factor and offset to achieve the desired output voltage range.
The accuracy of a frequency-voltage converter depends on several factors, including:
-
Linearity: The linearity of the conversion process determines how closely the output voltage follows the input frequency. A highly linear converter minimizes errors and provides a more accurate representation of the frequency signal.
-
Temperature Stability: Temperature variations can affect the performance of frequency-voltage converters. High-quality converters incorporate temperature compensation techniques to maintain accuracy over a wide temperature range.
-
Noise Immunity: The ability of a frequency-voltage converter to reject noise and interference is essential for reliable operation. Proper shielding, grounding, and filtering techniques are employed to minimize the impact of noise on the conversion process.
-
Resolution: The resolution of a frequency-voltage converter refers to the smallest detectable change in frequency that results in a measurable change in the output voltage. Higher resolution converters provide more precise measurements and control.
Regular calibration and maintenance of frequency-voltage converters ensure optimal performance and accuracy over time. Manufacturers often provide calibration procedures and guidelines to help users maintain the desired level of accuracy in their applications.
Selecting the Right Frequency-Voltage Converter
When choosing a frequency-voltage converter for a specific application, several key factors should be considered to ensure optimal performance and compatibility. Let’s explore these factors in detail.
Input Frequency Range
The input frequency range is a critical consideration when selecting a frequency-voltage converter. The converter should be capable of handling the expected range of frequencies generated by the mechanical system or sensor.
Consider the following aspects related to input frequency range:
-
Minimum and Maximum Frequencies: Determine the minimum and maximum frequencies that the converter needs to accommodate. Ensure that the selected converter’s input frequency range covers this span.
-
Frequency Response: Evaluate the converter’s frequency response, which indicates how accurately it can track changes in the input frequency. A fast frequency response ensures that the converter can capture rapid variations in the frequency signal.
-
Input Signal Characteristics: Consider the characteristics of the input frequency signal, such as waveform shape (square wave, sinusoidal, etc.), amplitude, and duty cycle. Ensure that the converter is compatible with these signal characteristics.
Output Voltage Range
The output voltage range of a frequency-voltage converter determines the span of voltages that the converter can produce in response to the input frequency. Consider the following factors related to output voltage range:
-
Desired Voltage Span: Determine the desired output voltage range based on the requirements of the target measurement or control system. The converter should be able to provide voltages within this range.
-
Scaling Adjustability: Check if the converter offers adjustable scaling or gain settings. Adjustable scaling allows you to fine-tune the output voltage range to match the specific needs of your application.
-
Offset Adjustment: Some applications may require an offset adjustment to shift the output voltage range. Ensure that the converter provides offset adjustment capabilities if needed.
Accuracy and Linearity
Accuracy and linearity are crucial factors to consider when selecting a frequency-voltage converter. The converter’s accuracy determines how closely the output voltage represents the input frequency, while linearity refers to the consistency of the conversion process across the entire frequency range.
Consider the following aspects related to accuracy and linearity:
-
Accuracy Specification: Review the accuracy specification provided by the manufacturer. It indicates the maximum deviation of the output voltage from the ideal value. Higher accuracy converters provide more precise measurements.
-
Linearity Error: Evaluate the linearity error specification, which quantifies the deviation from a perfect linear relationship between the input frequency and output voltage. Lower linearity error ensures consistent performance across the frequency range.
-
Temperature Stability: Consider the converter’s temperature stability, especially if the application involves a wide temperature range. Temperature variations can affect the accuracy and linearity of the converter.
Interface and Connectivity
The interface and connectivity options of a frequency-voltage converter are important considerations for seamless integration with the target system. Consider the following factors:
-
Output Signal Type: Determine the required output signal type, such as voltage, current, or digital. Ensure that the converter provides the appropriate output signal format.
-
Connector Compatibility: Check the compatibility of the converter’s output connector with the target system’s input interface. Common connectors include BNC, screw terminals, or specialized connectors.
-
Isolation: If electrical isolation is required between the input and output circuits, ensure that the converter provides galvanic isolation. Isolation helps prevent ground loops and reduces noise interference.
Power Supply Requirements
Consider the power supply requirements of the frequency-voltage converter to ensure compatibility with the available power source in the application. Take into account the following aspects:
-
Supply Voltage Range: Verify that the converter’s supply voltage range matches the available power supply voltage in the system.
-
Power Consumption: Evaluate the power consumption of the converter and ensure that the power supply can provide sufficient current to meet the converter’s requirements.
-
Power Supply Noise: Consider the power supply noise tolerance of the converter. If the application involves a noisy power environment, choose a converter with good power supply noise rejection.
Physical Characteristics and Environment
The physical characteristics and environmental conditions of the application should also be considered when selecting a frequency-voltage converter. Take into account the following factors:
-
Size and Mounting: Evaluate the physical dimensions of the converter and ensure that it fits within the available space in the application. Consider the mounting options, such as DIN rail, panel mount, or PCB mount.
-
Operating Temperature Range: Verify that the converter’s operating temperature range is compatible with the expected environmental conditions of the application.
-
Ingress Protection: If the converter will be exposed to harsh environments, dust, or moisture, consider the ingress protection (IP) rating. Higher IP ratings indicate better protection against environmental factors.
Cost and Availability
Finally, consider the cost and availability of the frequency-voltage converter. Evaluate the following aspects:
-
Budget: Determine the budget allocated for the converter and select a device that meets the performance requirements within the available budget.
-
Availability and Lead Time: Check the availability and lead time of the converter from the manufacturer or distributor. Ensure that the converter can be procured within the required timeframe for the application.
-
Manufacturer Support: Consider the level of technical support and documentation provided by the manufacturer. Good customer support can be valuable for troubleshooting and ensuring successful implementation.
By carefully evaluating these factors and aligning them with the specific requirements of the application, you can select the most suitable frequency-voltage converter that offers reliable performance, compatibility, and cost-effectiveness.
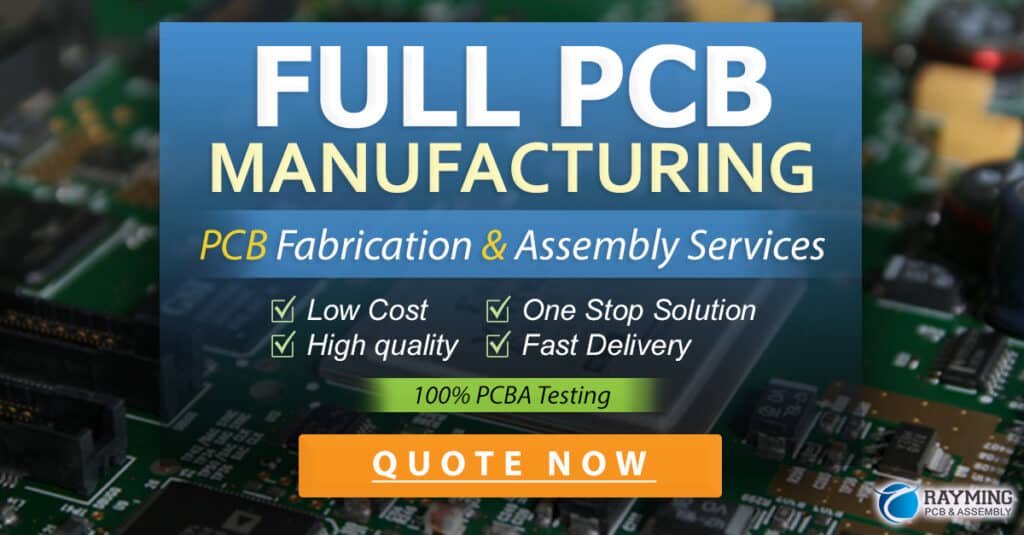
Frequency-Voltage Converter Installation and Configuration
Once you have selected the appropriate frequency-voltage converter for your application, the next step is to install and configure it correctly. Proper installation and configuration ensure optimal performance and reliable operation. Let’s go through the key steps involved in this process.
Mechanical Installation
The first step is to mechanically install the frequency-voltage converter in the desired location. Consider the following factors during mechanical installation:
-
Mounting: Choose a suitable mounting method based on the converter’s form factor and the available space in the application. Common mounting options include DIN rail mounting, panel mounting, or PCB mounting.
-
Orientation: Ensure that the converter is mounted in the correct orientation, following the manufacturer’s guidelines. Proper orientation helps prevent issues related to heat dissipation and signal integrity.
-
Vibration and Shock: If the application involves vibration or shock, use appropriate vibration-dampening techniques or shock-absorbing mounts to protect the converter from mechanical stress.
-
Clearance: Provide sufficient clearance around the converter for proper ventilation and ease of access for maintenance or troubleshooting.
Electrical Connections
After mechanical installation, proceed with the electrical connections of the frequency-voltage converter. Follow these steps:
-
Power Supply: Connect the converter to the appropriate power supply, ensuring that the voltage and current ratings match the converter’s requirements. Use the recommended wire gauge and follow the manufacturer’s wiring instructions.
-
Input Signal: Connect the input frequency signal to the designated input terminals of the converter. Ensure proper signal polarity and use shielded cables if necessary to minimize noise interference.
-
Output Signal: Connect the output voltage signal from the converter to the target measurement or control system. Use the appropriate connector type and ensure secure and reliable connections.
-
Grounding: Establish a proper grounding scheme for the converter, following the manufacturer’s recommendations. Proper grounding helps reduce noise and ensures a stable reference for the signals.
-
Cable Management: Organize and route the cables neatly, avoiding sharp bends or excessive strain on the connections. Use cable ties or conduits to keep the wiring tidy and protected.
Configuration and Calibration
With the mechanical and electrical installations complete, the next step is to configure and calibrate the frequency-voltage converter according to the application requirements. Follow these steps:
-
Scaling Adjustment: Use the scaling adjustment features of the converter to set the desired output voltage range. This typically involves adjusting gain or span potentiometers or configuring the scaling through software or DIP switches.
-
Offset Adjustment: If required, adjust the offset of the output voltage signal to match the desired zero-frequency voltage level. This can be done using offset adjustment potentiometers or software settings.
-
Calibration: Perform calibration of the converter to ensure accurate frequency-to-voltage conversion. Follow the manufacturer’s calibration procedure, which may involve applying known frequency inputs and verifying the corresponding output voltages.
-
Linearity Check: Verify the linearity of the conversion by applying different frequency inputs across the operating range and measuring the corresponding output voltages. Ensure that the converter maintains linearity within the specified tolerance.
-
Temperature Compensation: If the converter supports temperature compensation, enable and configure this feature according to the manufacturer’s guidelines. Temperature compensation helps maintain accuracy over the operating temperature range.
Testing and Verification
After configuration and calibration, perform thorough testing and verification to ensure that the frequency-voltage converter is functioning as expected. Consider the following steps:
-
Functional Testing: Apply various frequency inputs to the converter and verify that the output voltages are accurate and stable. Test the converter across the entire operating frequency range.
-
Noise and Interference Testing: Evaluate the converter’s performance in the presence of noise and interference sources present in the application environment. Ensure that the converter maintains accuracy and stability under these conditions.
-
System Integration Testing: Integrate the converter with the target measurement or control system and verify that the converted voltage signal is correctly received and processed by the system.
-
Long-term Reliability Testing: Conduct long-term reliability testing to assess the converter’s performance over extended periods of operation. Monitor for any drift, stability issues, or failures.
By following these installation and configuration steps, you can ensure that the frequency-voltage converter is set up correctly and ready to provide reliable and accurate frequency-to-voltage conversion in your application.
Troubleshooting Frequency-Voltage Converters
Despite proper installation and configuration, issues may arise with frequency-voltage converters during operation. Troubleshooting these issues promptly is crucial to maintain the reliability and accuracy of the converter. Let’s explore some common problems and their troubleshooting strategies.
No Output Voltage
If the frequency-voltage converter is not providing any output voltage, consider the following troubleshooting steps:
-
Power Supply: Verify that the converter is receiving the correct power supply voltage and current. Check the power connections and ensure that the supply meets the converter’s requirements.
-
Input Signal: Confirm that the input frequency signal is present and within the specified range. Use an oscilloscope or frequency counter to measure the input signal characteristics.
-
Output Connections: Check the output connections for any loose or damaged wires. Ensure that the output terminals are securely connected to the target
No responses yet